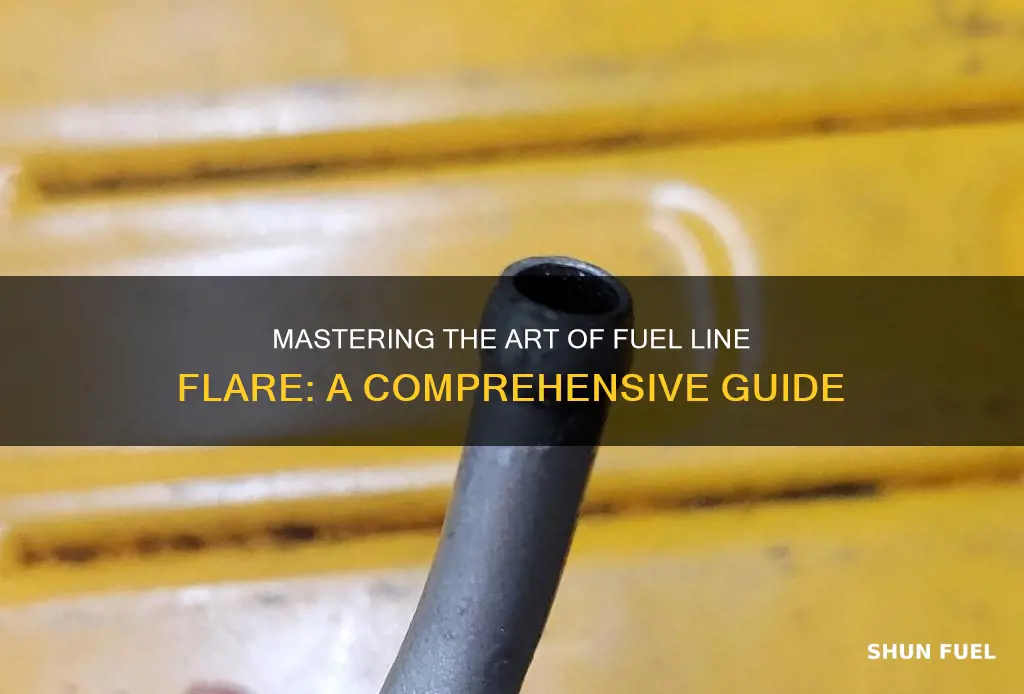
Flaring a fuel line is a crucial step in the process of safely and effectively managing fuel systems. This technique involves the controlled burning of excess fuel to prevent spills and ensure the safe operation of engines. It is a critical procedure for mechanics and technicians working with fuel systems, as it helps to mitigate the risks associated with fuel leaks and potential fires. By understanding the proper techniques and safety measures, one can effectively flare fuel lines, contributing to the overall safety and efficiency of fuel management systems.
What You'll Learn
- Location: Identify the fuel line's position under the vehicle
- Tools: Gather necessary tools: wrench, pliers, fuel line flare kit
- Preparation: Clean the fuel line and ensure a dry environment
- Flare Process: Tighten the flare nut and apply heat to create a seal
- Testing: Verify the connection by checking for leaks and functionality
Location: Identify the fuel line's position under the vehicle
To locate the fuel lines under your vehicle, you'll need to inspect the engine bay and the area directly below it. Here's a step-by-step guide to help you identify their positions:
- Access the Engine Bay: Start by opening the hood of your vehicle. Ensure you are wearing protective gear, such as gloves and safety goggles, to prevent any potential injuries. Locate the fuel tank, which is typically a rectangular or cylindrical component. It might be located on the driver's side or passenger's side of the engine bay, depending on the vehicle's design.
- Identify the Fuel Tank: The fuel tank will have a fuel filler port, often with a small cap or cover. This is the primary access point for refueling. Look for any visible fuel lines connected to the tank. These lines will typically run from the tank to the engine compartment.
- Trace the Fuel Lines: Carefully trace the path of the fuel lines from the tank towards the engine. They might be attached to various components, such as the fuel pump, fuel filter, or the engine itself. Look for any fittings, valves, or connectors along the way. These are crucial points to identify as they may require specialized tools for flaring.
- Locate the Engine's Fuel System: In the engine bay, identify the fuel injectors or carburetor (if applicable). The fuel lines will connect to these components, delivering fuel to the engine's combustion chambers. Carefully inspect the connections between the fuel lines and the engine to ensure they are secure and in good condition.
- Check for Additional Lines: Some vehicles may have additional fuel lines for auxiliary systems, such as the fuel pump sending unit or the fuel pressure regulator. These lines might be less visible but are essential to the overall fuel system. Take note of their positions and any unique characteristics that can help you identify them.
Remember, the key to successfully flaring a fuel line is accurate identification of its position and connections. Take your time to inspect the vehicle thoroughly, and if you're unsure, consult the vehicle's service manual or seek professional assistance.
Diagnosing Fuel Issues: A Guide to Checking the Return Line on Your Kubota Diesel Engine
You may want to see also
Tools: Gather necessary tools: wrench, pliers, fuel line flare kit
To successfully flare a fuel line, it's crucial to have the right tools at hand. The primary tools required for this task are a wrench, pliers, and a fuel line flare kit. Each of these tools plays a specific role in ensuring a secure and leak-free connection.
A wrench is an essential tool for any plumbing or fuel line work. It provides the necessary leverage to tighten or loosen fittings and connections. When flaring a fuel line, you'll use the wrench to apply the right amount of force to the flare nut, ensuring it is neither too tight nor too loose. Opt for a wrench with a comfortable grip and a good range of sizes to accommodate various flare nuts.
Pliers are another indispensable tool for this process. They are particularly useful for gripping and manipulating small components, such as the fuel line itself. When flaring, you'll use pliers to hold the fuel line in place while applying the flare nut. This ensures that the fuel line is positioned correctly and remains stable during the flaring process. Look for pliers with a smooth jaw surface to avoid damaging the fuel line.
The fuel line flare kit is the star of the show when it comes to flaring. This kit contains all the necessary components to create a secure flare connection. It typically includes a variety of flare nuts, sleeves, and dies, each designed to fit specific fuel line sizes. The kit provides the precision and consistency required to create a tight seal. When gathering your tools, ensure that the flare kit is in good condition and includes the appropriate sizes for your fuel line.
Having these tools ready will significantly contribute to the success of your fuel line flaring project. It's essential to inspect each tool for any signs of wear or damage before beginning the work, ensuring they are in optimal condition for the task at hand.
Fixing a Fuel Line: A Step-by-Step Guide to Getting Your Car Back on the Road
You may want to see also
Preparation: Clean the fuel line and ensure a dry environment
Before you begin the process of flaring a fuel line, it is crucial to ensure that the work area is clean and dry. This step is often overlooked but is essential for a successful and safe repair. Start by removing any debris or contaminants from the area where the fuel line will be flared. Use a soft brush or a compressed air tool to blow away any dust, dirt, or small particles that might interfere with the flaring process. Pay close attention to the area around the fuel line, as any residue or contamination can affect the flare's integrity.
Cleaning the fuel line itself is the next critical step. Over time, fuel lines can accumulate dirt, rust, and other debris, which can lead to blockages and reduced performance. Use a fuel line cleaner or a mild detergent mixed with water to thoroughly clean the line. Apply the cleaner to the entire length of the fuel line, ensuring that you cover all areas, including the fittings and connectors. Allow the cleaner to sit for a few minutes to loosen any built-up contaminants. Then, use a flexible brush or a high-pressure water jet (if available) to scrub the fuel line, removing any residue. Rinse the line thoroughly with clean water to eliminate any cleaning agent residue.
Ensuring a dry environment is equally important. Moisture in the fuel line can lead to corrosion and potential fuel leaks. After cleaning, allow the fuel line to air dry completely. You can use a hairdryer on a low setting to speed up the drying process, but be cautious not to apply excessive heat, as it may damage the fuel line. Once dry, inspect the fuel line for any signs of damage or wear. If any issues are found, address them before proceeding with the flaring process.
Additionally, check the surrounding area for any potential sources of moisture. Condensation or dampness in the air can affect the flare's effectiveness. If the environment is particularly humid, consider using a dehumidifier or working in a well-ventilated area to maintain a dry atmosphere. By taking these preparation steps, you'll create an optimal environment for flaring the fuel line, ensuring a clean and dry surface for the upcoming process.
Mastering Yamaha 50 Fuel Line Connection: A Step-by-Step Guide
You may want to see also
Flare Process: Tighten the flare nut and apply heat to create a seal
The flare process is a crucial step in creating a secure and leak-free connection between two fuel lines. Once the flare nut is in place, the next step is to ensure a tight and reliable seal. Here's a detailed guide on how to achieve this:
Tightening the flare nut is an essential part of the process. Use a wrench to apply firm pressure and tighten the nut securely. The goal is to create a snug fit, ensuring that the flare connection is tight against the fuel line. Over-tightening should be avoided as it can damage the fuel line or cause internal damage to the flare fitting. The ideal tightness is when the flare nut is hand-tightened, and you can feel a slight resistance, indicating a secure connection.
After tightening, the flare connection needs to be heated to facilitate the sealing process. Heat is applied to the flare nut and the surrounding area using a flame torch or a heat gun. The heat softens the metal, allowing it to conform to the shape of the fuel line. It's important to apply the heat evenly and not to overheat the connection, as this can lead to melting or damage. Focus the heat on the flare nut and the adjacent section of the fuel line, ensuring a consistent temperature.
As the metal cools, it will contract, creating a tight seal. This process is known as 'cold-welding' or 'flare welding'. The heat causes the metal surfaces to interlock, forming a strong bond. The flare nut should now be firmly attached, and the connection should be leak-tight.
Remember, practice and precision are key when flaring fuel lines. Take your time, ensure a tight fit, and apply heat carefully to achieve a professional-grade connection. This method ensures a reliable and safe fuel line connection, minimizing the risk of leaks and potential hazards.
Amoutlander Fuel Line Diagram: A Comprehensive Guide
You may want to see also
Testing: Verify the connection by checking for leaks and functionality
Before you can ensure the integrity of your fuel line connection, you must first understand the importance of testing. Flare connections, while strong, can still be susceptible to leaks if not properly assembled and tested. This step is crucial to prevent fuel leaks, which can lead to dangerous situations and costly repairs. Here's a detailed guide on how to verify the connection:
- Prepare the Tools and Materials: You'll need a few essential tools for this process. These include a soapy water solution, a spray bottle, a clean cloth, and a torch (optional). The soapy water is the key to identifying potential leaks, as it will create a visible foam if there's a breach in the connection.
- Spray and Inspect: Start by spraying the soapy water solution onto the flared connection. Pay close attention to the area where the two pipes meet. If there's a leak, you should see bubbles forming and expanding, indicating a break in the seal. Ensure you cover all surfaces, including the threads and the flare itself.
- Check for Visual Signs: After spraying, inspect the connection thoroughly. Look for any signs of moisture or soap residue around the connection. If you notice any, it's a good sign that there might be a leak. Also, check for any visible damage or deformation in the flare, as this could be a result of an improper connection.
- Test Functionality: Once you've confirmed the connection is leak-free, it's time to test its functionality. This involves ensuring that the fuel flows smoothly through the line without any blockages. Start by turning on the fuel supply and observing the flow. Check for any unusual noises or pressure drops, which could indicate a problem. If everything seems normal, you can proceed with the next steps.
- Final Inspection: After testing functionality, give the connection a final visual inspection. Look for any signs of wear and tear, corrosion, or damage that might have occurred during the testing process. This step ensures that the connection is not only leak-free but also in optimal condition.
Remember, proper testing is essential to guarantee the longevity and safety of your fuel line. By following these steps, you can identify and address any potential issues before they become major problems. Always take your time during this process to ensure a thorough inspection.
Solid Fuel Safety: Can It Be Used in Fuel Lines?
You may want to see also
Frequently asked questions
Flaring a fuel line is a process used in plumbing and automotive applications to create a controlled burn-off of excess fuel or gas. It helps to prevent fuel leaks, improve combustion efficiency, and ensure a safe and controlled environment.
Fuel lines can develop leaks or become damaged over time, leading to potential hazards. Flaring the ends of the fuel line helps to eliminate these leaks by creating a controlled flame that burns off any excess fuel, ensuring a tight seal and preventing dangerous gas accumulation.
The process typically involves a flare tool or kit, which includes a torch, a heat shield, and various sizes of flare nuts and sleeves. It is essential to have the appropriate safety gear, such as heat-resistant gloves and eye protection, to ensure a safe working environment.
Absolutely! Working with flammable substances like fuel requires extreme caution. Ensure the work area is well-ventilated and clear of any ignition sources. Always follow safety protocols, wear protective gear, and have a fire extinguisher nearby. It is crucial to have proper training or guidance from an experienced professional to avoid accidents.