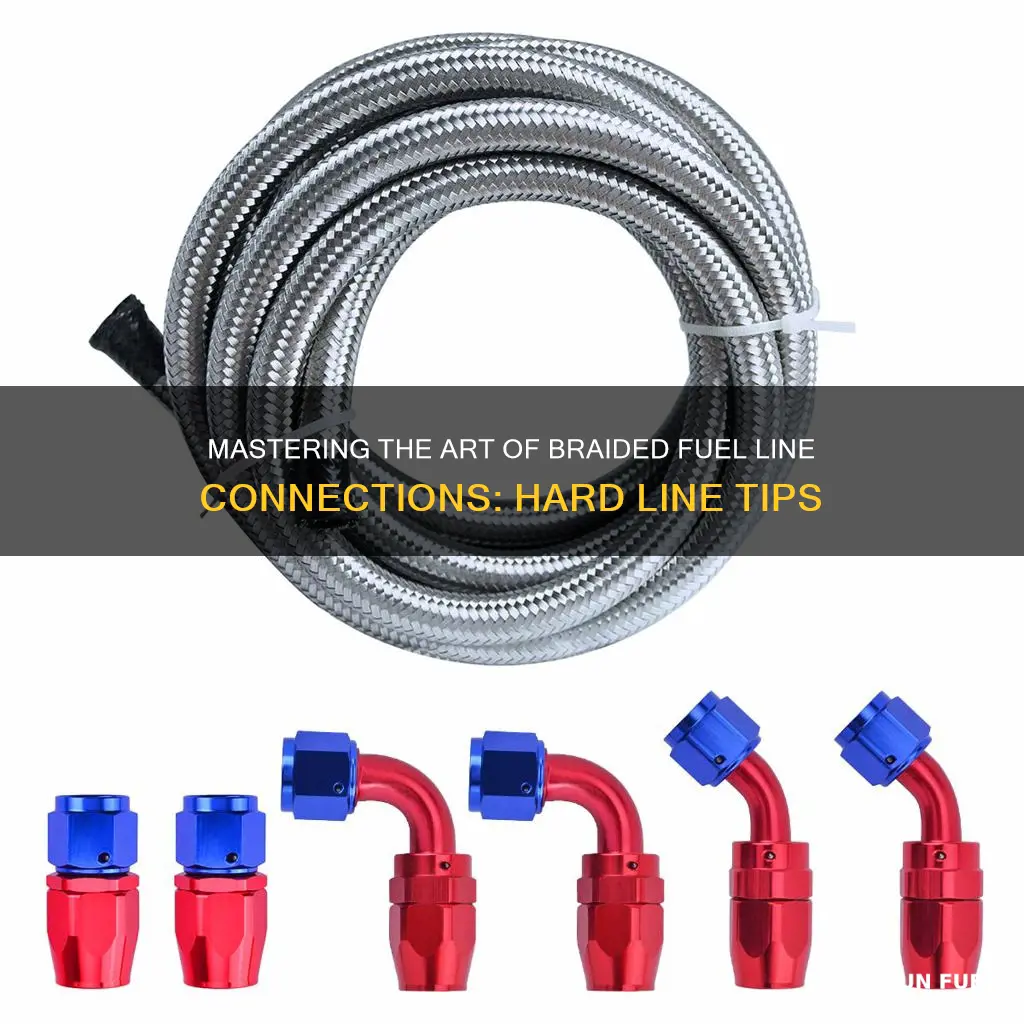
Connecting a braided fuel line to a hard line is a crucial step in ensuring the efficient and safe delivery of fuel in automotive applications. This process requires careful attention to detail and adherence to specific techniques to guarantee a secure and reliable connection. By following a step-by-step guide, you can ensure that the braided fuel line is properly attached to the hard line, maintaining the integrity of the fuel system and preventing potential leaks or damage. Understanding the proper methods for this connection is essential for anyone working on fuel systems, whether for maintenance, repairs, or modifications.
What You'll Learn
- Preparation: Ensure you have the right tools and materials, including fuel line and hard line connectors
- Clamping: Tighten the clamp securely, but avoid over-tightening to prevent damage
- Alignment: Align the fuel line and hard line at the connection point for a precise fit
- Sealing: Use a suitable sealant to create a tight, leak-free seal around the connection
- Testing: Verify the connection by checking for leaks and ensuring proper fuel flow
Preparation: Ensure you have the right tools and materials, including fuel line and hard line connectors
Before you begin the process of connecting a braided fuel line to a hard line, it's crucial to ensure you have the necessary tools and materials ready. This preparation step is often overlooked but is essential for a successful and secure connection. Here's a detailed guide on what you need:
Tools and Materials:
- Fuel Line and Hard Line Connectors: These are the primary components for your connection. You'll need a connector that is compatible with both the braided fuel line and the hard line. Common types include quick-connect fittings, which are widely available in automotive stores.
- Pliers: A good pair of pliers is essential for gripping and holding the connectors and fuel lines firmly during the connection process. Ensure they have a comfortable grip and are made of durable material.
- Rags or Cloths: Have some rags or old clothes nearby to protect your hands and work area from any potential fuel spills. This is important for safety and cleanliness.
- Fuel Line Cleaner: It's a good practice to clean the fuel lines before making connections. A fuel line cleaner will help remove any contaminants and ensure a proper seal.
- Towel or Paper Towel: Keep a towel or paper towel nearby to wipe your hands and tools, maintaining a clean and dry environment.
Having these items ready will make the connection process much smoother. It's always a good idea to double-check your tools and materials to ensure you have everything required before starting the task. This preparation will save you time and potential frustration during the actual connection process.
John Deere LX255 Fuel Line Location: A Comprehensive Guide
You may want to see also
Clamping: Tighten the clamp securely, but avoid over-tightening to prevent damage
When connecting a braided fuel line to a hard line, proper clamping is crucial to ensure a secure and reliable fuel system. The primary goal is to create a tight seal that prevents any fuel leakage while also allowing for flexibility to accommodate movement within the engine bay. Here's a step-by-step guide on how to achieve this:
Start by ensuring you have the right-sized clamp for your fuel lines. Clamps come in various sizes and materials, so it's essential to choose one that fits your specific fuel lines. A common choice is a stainless steel or aluminum clamp, which offers durability and resistance to corrosion. Place the clamp over the joined section of the braided and hard fuel lines, ensuring it covers the entire connection. The clamp should be positioned so that it can evenly distribute the pressure around the fuel lines.
Now, it's time to tighten the clamp. Use a wrench or a specialized clamp tool to apply firm pressure. The goal is to tighten the clamp securely, but it's important to avoid over-tightening. Over-tightening can lead to several issues, including damage to the fuel lines, reduced flexibility, and potential fuel leaks. As you tighten the clamp, you should feel resistance, but it should not feel forced or difficult. The ideal tightness is when the clamp is snug, and you can't easily move it along the fuel lines.
To ensure you haven't over-tightened, check the fuel lines for any signs of distress. Look for any visible damage, such as cracks or kinks, especially where the clamp is applied. Also, feel the fuel lines along the clamp's length; they should not feel overly stiff or rigid. If you notice any issues, loosen the clamp slightly and re-evaluate your tightening.
Remember, the key to successful clamping is finding the right balance between tightness and flexibility. By following these instructions and paying close attention to the feel and appearance of the fuel lines, you can ensure a secure and long-lasting connection between your braided and hard fuel lines.
Mastering Fuel Line Quick Connects: A Step-by-Step Guide
You may want to see also
Alignment: Align the fuel line and hard line at the connection point for a precise fit
When connecting a braided fuel line to a hard line, proper alignment is crucial to ensure a secure and leak-free connection. Here's a detailed guide on how to achieve this:
Start by preparing the connection point on both the fuel line and the hard line. Ensure that the ends of both lines are clean and free of any debris or contaminants. Use a suitable fuel line cleaner or a mild solvent to remove any old fuel residue, ensuring a fresh and clean surface for the connection.
Next, carefully inspect the connection point. Look for any existing damage or wear on the hard line, as this could affect the overall integrity of the connection. If there are any signs of damage, it's essential to replace the affected section of the hard line before proceeding.
Now, it's time to align the lines. Hold the braided fuel line and the hard line together, ensuring they are positioned correctly. The braided fuel line should be aligned with the hard line, with the braids running parallel to the hard line's surface. Take note of the direction of the braids; they should match the flow of the fuel line to maintain optimal performance.
Pay close attention to the connection point's geometry. The fuel line and hard line should be aligned in a way that the connection port or fitting is centered between the two lines. This alignment ensures an even distribution of pressure and prevents any potential strain on the lines.
Finally, secure the connection. Use the appropriate fuel line connectors or fittings designed for the specific lines you are working with. Tighten the connectors according to the manufacturer's instructions, being careful not to overtighten, as this can damage the lines. A secure connection will ensure the fuel line and hard line remain aligned and function optimally.
Keep Your Engine Healthy: Cleaning Fuel Lines Regularly
You may want to see also
Sealing: Use a suitable sealant to create a tight, leak-free seal around the connection
When connecting a braided fuel line to a hard line, ensuring a secure and leak-free seal is crucial to maintain the integrity of your fuel system. The process involves more than just physically attaching the two lines; it requires careful preparation and the use of an appropriate sealant. Here's a step-by-step guide to achieving a tight seal:
Start by ensuring both the braided fuel line and the hard line are clean and free of any debris or contaminants. Use a wire brush or a clean cloth to remove any dirt or old sealant residue from the connection points. This step is essential as any foreign matter can compromise the effectiveness of the sealant.
Next, prepare the ends of the lines. For the braided fuel line, you might need to cut back the protective covering to expose the inner fuel-resistant material. Similarly, the hard line should have a smooth, clean surface. If there are any sharp edges or burrs, gently file them down to create a smooth connection surface.
Now, it's time to apply the sealant. Choose a high-quality, fuel-resistant sealant that is compatible with the materials of both lines. A two-part epoxy sealant is often a good choice for this application. Follow the manufacturer's instructions for application, typically involving mixing the two parts together and then carefully applying the sealant to the connection area. Ensure you cover the entire interface, including any threads or fittings.
After applying the sealant, allow it to cure according to the manufacturer's guidelines. This process might take several hours or even overnight, depending on the product. During this time, avoid any pressure or force on the connection to ensure the sealant sets correctly. Once cured, the sealant will create a robust, leak-resistant bond between the braided fuel line and the hard line.
Remember, the key to a successful connection is proper preparation and the use of an appropriate sealant. Taking the time to clean the lines, prepare the ends, and apply the sealant correctly will result in a long-lasting, reliable fuel system. Always refer to the product instructions for specific details on sealant application and curing times.
Cold Weather Fuel Line Freezing: A Risk for Airplanes?
You may want to see also
Testing: Verify the connection by checking for leaks and ensuring proper fuel flow
After completing the connection between the braided fuel line and the hard line, it is crucial to verify the setup to ensure it is secure and functional. This testing phase is essential to prevent potential fuel leaks and ensure optimal engine performance. Here's a step-by-step guide to conducting this verification:
Leak Testing: Begin by applying a small amount of diesel fuel to the connection points. This can be done by using a syringe or a small fuel can. Pay close attention to the areas where the braided line and hard line are joined, as well as any fittings or connectors. Inspect the fuel line for any signs of leakage. If you notice any fuel seeping or dripping, it indicates a potential issue with the connection. Tighten the fittings or connectors if necessary, ensuring they are secure and free from any gaps that might allow fuel to escape.
Fuel Flow Inspection: Once the leak test is complete and all connections appear tight, it's time to check the fuel flow. Start the engine and allow it to run for a few minutes. Monitor the fuel gauge and ensure that the fuel level is steady and not fluctuating erratically. If the fuel flow is inconsistent or the gauge shows sudden drops, it suggests a possible restriction or blockage in the line. In such cases, inspect the line for any kinks or obstructions and ensure that the fuel pump is functioning correctly.
Pressure Check: To further ensure the integrity of the connection, perform a pressure check. You can use a fuel pressure gauge for this purpose. Connect the gauge to the fuel line and measure the pressure. The reading should be within the recommended range specified by the vehicle manufacturer. If the pressure is too low, it may indicate a restriction or a faulty pump. Conversely, excessive pressure could suggest a potential leak or over-tightening of connections.
Visual Inspection: While the engine is running, visually inspect the fuel lines for any signs of damage, such as cuts, punctures, or excessive wear. Also, check for any visible condensation or moisture accumulation inside the line, as this could indicate a potential issue with the fuel system.
By following these testing procedures, you can ensure that the braided fuel line is correctly connected to the hard line, providing a reliable and safe fuel supply to the engine. It is a critical step in maintaining the overall health and performance of the vehicle's fuel system.
Fixing Fuel Leaks: A Step-by-Step Guide to Repairing Fuel Lines
You may want to see also
Frequently asked questions
Braided fuel lines are an upgrade from traditional rubber hoses and are designed to handle high-pressure fuel systems. They offer improved flexibility, durability, and resistance to fuel degradation, making them ideal for high-performance engines.
Connecting a braided fuel line to a hard line requires a few steps. First, ensure both lines are clean and free of any debris. Then, use a fuel line adapter or a quick-connect fitting that matches the sizes of both lines. Tighten the fitting securely, but be careful not to overtighten, as it can damage the lines.
Yes, you'll need a fuel line tool or a fuel line cutter to ensure a clean and precise cut. This tool helps to create a smooth and even surface for the connection. Additionally, have a fuel line primer or adhesive to ensure a secure bond between the braided and hard lines.
Leaks can occur due to improper fitting, using the wrong size adapters, or not cleaning the lines before connection. Overtightening the fittings can also cause damage and lead to fuel leaks. Always double-check the connection and ensure all components are compatible.
Braided fuel lines are versatile and can be used with various engine types. However, it's essential to check the engine's specifications and requirements. Some high-performance engines may have specific fuel line materials and sizes, so consulting the vehicle's manual or a professional is advisable.