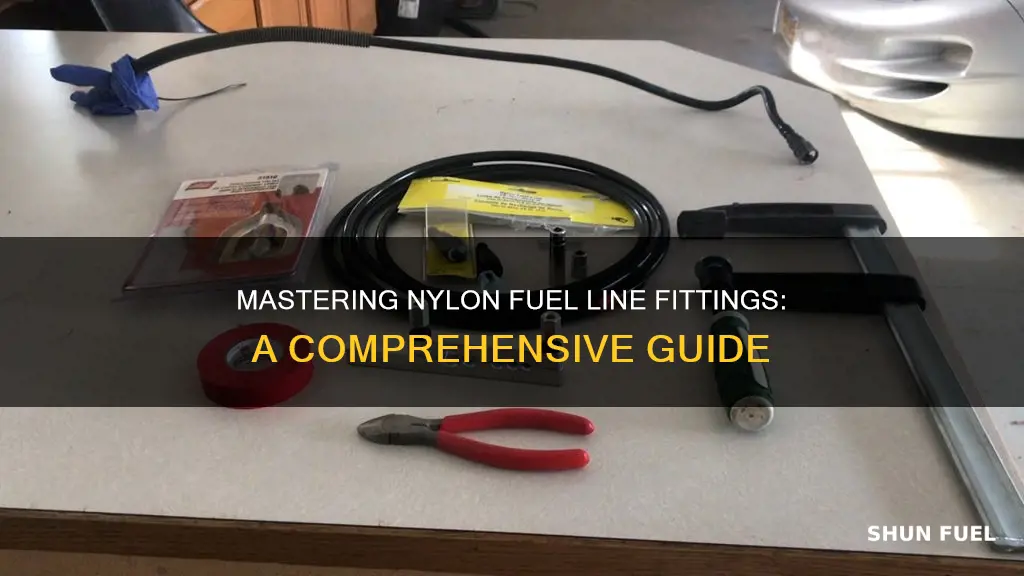
Installing nylon fuel line fittings is a straightforward process that can be accomplished with a few simple tools and some basic knowledge. Nylon fuel lines are a popular choice for their flexibility, durability, and resistance to heat and chemicals, making them ideal for fuel delivery systems. This guide will walk you through the steps to ensure a secure and reliable installation, providing tips on preparing the fittings and lines, using the right tools, and ensuring a tight seal to prevent leaks. By following these instructions, you can confidently install nylon fuel line fittings, ensuring your vehicle's fuel system operates efficiently and safely.
Characteristics | Values |
---|---|
Material | Nylon |
Compatibility | Fuel lines |
Installation Method | Clamping |
Temperature Range | -40°F to 250°F (-40°C to 121°C) |
Pressure Rating | Up to 150 psi (10.3 bar) |
Flexibility | High flexibility for easy installation |
Corrosion Resistance | Resistant to fuel-related chemicals |
Color | Typically black or white |
Availability | Widely available in hardware stores and online |
Cost | Generally affordable compared to metal fittings |
Maintenance | Low maintenance required |
Installation Tools | Required tools may vary but often include pliers and fuel line cutters |
Safety | Can provide a secure connection without the need for welding or soldering |
What You'll Learn
- Prepare Tools: Gather necessary tools like wrenches, pliers, and fuel line cleaner
- Clean Lines: Ensure fuel lines are clean and free of debris before installation
- Cut Lines: Measure and cut fuel lines to the appropriate length for fittings
- Slide Fittings: Slide fittings onto fuel lines, ensuring a snug fit
- Secure Connections: Tighten connections securely, checking for leaks
Prepare Tools: Gather necessary tools like wrenches, pliers, and fuel line cleaner
Before you begin the installation process of nylon fuel line fittings, it's crucial to ensure you have the right tools ready to make the task efficient and effective. Here's a detailed guide on preparing the necessary tools:
Wrenches and Pliers: These are essential tools for any fuel line installation. You'll need a set of adjustable wrenches to accommodate various sizes of fittings and pipes. Look for wrenches with a good grip and consider the size range suitable for your project. Additionally, a pair of adjustable pliers will be invaluable for gripping and turning fittings, especially in tight spaces. Ensure the pliers have a comfortable handle and a secure jaw to prevent slipping.
Fuel Line Cleaner: Cleaning is a critical step often overlooked. Before installing any fuel line, it's imperative to clean the existing lines to remove any contaminants, old fuel, or debris. Gather a reliable fuel line cleaner that is compatible with your fuel type. This cleaner will help ensure a proper seal and prevent potential leaks. Follow the manufacturer's instructions for application and rinsing to guarantee a thorough clean.
Other Useful Tools: Consider having a few extra items on hand to make the job smoother. A utility knife or a sharp blade will be handy for cutting the fuel lines to the desired length. Additionally, a small wire brush or a cleaning brush can help remove any stubborn dirt or corrosion from the fuel lines. Don't forget safety gear like gloves and safety goggles to protect yourself during the process.
By gathering these tools, you'll be well-prepared to tackle the installation of nylon fuel line fittings. It's always a good practice to double-check your tool collection before starting any project to avoid any last-minute hassles. With the right tools in hand, you'll be able to complete the installation efficiently and ensure a secure and reliable fuel line system.
Mastering Fuel Line Bleed: A Guide for Cummins Owners
You may want to see also
Clean Lines: Ensure fuel lines are clean and free of debris before installation
Before you begin the installation process of nylon fuel line fittings, it is crucial to ensure that the fuel lines are clean and free of any debris or contaminants. This step is often overlooked but plays a vital role in the overall performance and longevity of your fuel system. Here's a detailed guide on how to achieve clean lines:
Preparation and Cleaning: Start by removing the fuel lines from the vehicle or equipment they were previously connected to. This process might require some disassembly, especially if the lines are part of an existing system. Once separated, inspect the lines for any signs of damage, cracks, or debris accumulation. Use a soft-bristled brush or a small wire brush to gently clean the interior surface of the fuel lines. Remove any built-up dirt, rust, or old fuel residue. It is essential to be thorough during this step to ensure no contaminants remain.
Debris Removal: Focus on removing any debris or foreign objects that might have entered the fuel lines during their previous use. This could include small particles of dirt, metal shavings, or even insects. Use a magnifying glass or a small flashlight to inspect the lines closely and identify any foreign matter. Carefully remove these particles using a soft brush or a small vacuum cleaner with a narrow nozzle. Ensure that you do not damage the inner walls of the fuel lines during this process.
Cleaning Solutions: If the fuel lines are heavily contaminated, you may need to use a suitable cleaning solution. A mild detergent or a specialized fuel line cleaner can be applied to the interior of the lines. Follow the instructions on the cleaning product carefully and rinse thoroughly with clean water to remove any residue. Allow the lines to dry completely before proceeding with the installation.
Pre-Installation Inspection: After cleaning, perform a final inspection to ensure the fuel lines are free from any debris or contaminants. Check for any remaining dirt or residue and re-clean if necessary. This step is crucial to guarantee a smooth and successful installation of the nylon fuel line fittings.
By following these cleaning procedures, you will ensure that the nylon fittings are installed in a pristine environment, promoting optimal performance and reliability. Remember, proper preparation is key to a successful fuel line installation.
Understanding Aluminum Fuel Line Ratings: A Comprehensive Guide
You may want to see also
Cut Lines: Measure and cut fuel lines to the appropriate length for fittings
When installing nylon fuel line fittings, precise measurements and careful cutting are essential to ensure a secure and leak-free connection. Here's a step-by-step guide on how to measure and cut fuel lines to the appropriate length:
Step 1: Assess the Required Length: Begin by carefully examining the fuel line and identifying the desired length. Consider the distance between the existing fittings and the point where you want to install the new fittings. Measure twice to ensure accuracy, as this will be the basis for your cuts.
Step 2: Mark the Measurements: Using a permanent marker or a piece of chalk, mark the measured length on the fuel line. Make two marks, one at each end of the desired length. This will serve as a visual guide during the cutting process.
Step 3: Choose the Cutting Tool: For cutting fuel lines, a sharp utility knife or a dedicated fuel line cutter is recommended. These tools provide a clean and precise cut. Ensure the knife is sharp to make a clean cut without damaging the line.
Step 4: Make the Cut: Position the fuel line on a stable surface. Align the marks made in Step 2 with the cutting tool. Apply firm pressure and make a straight cut through the line. Take your time to ensure accuracy, as a precise cut is crucial for a proper fit.
Step 5: Verify the Length: After cutting, measure the length of the fuel line again to confirm it matches your initial assessment. This double-check ensures that you have achieved the correct length for the fittings.
By following these steps, you can accurately measure and cut fuel lines, allowing for a seamless installation of nylon fuel line fittings. Precision in this process is key to maintaining the integrity of the fuel system and preventing potential leaks.
Fuel Line to Fitting: A Step-by-Step Guide to Success
You may want to see also
Slide Fittings: Slide fittings onto fuel lines, ensuring a snug fit
Slide fittings are an essential component when working with fuel lines, especially in automotive applications. These fittings are designed to securely attach to the fuel lines, ensuring a tight seal to prevent any leaks. The process of installing slide fittings onto fuel lines is straightforward and can be accomplished with the right tools and a bit of patience.
To begin, you'll need to gather the necessary tools and materials. You should have the slide fittings, fuel lines, and a suitable solvent cleaner. It is crucial to ensure that the fittings are the correct size and type for your specific fuel line. Measure the inside diameter of your fuel line and compare it to the specifications of the fittings to make an accurate selection.
Start by cleaning the fuel line and the fitting's interior. Use the solvent cleaner to remove any dirt, debris, or old fuel residue. This step is vital to ensure a proper seal and prevent contamination. Make sure the line is dry before proceeding.
Now, slide the fitting onto the fuel line. Start at one end and carefully push the fitting onto the line until it is fully inserted. Ensure that the fitting is centered and aligned with the line. You should feel a slight resistance when the fitting is fully seated, indicating a snug fit. If you encounter any difficulty, double-check the alignment and try again.
For an extra secure connection, consider using a small amount of thread seal tape or pipe compound on the threads of the fitting. Wrap the tape or compound around the threads, ensuring an even coating. This additional step provides an extra layer of protection against leaks. Once the fitting is in place, test the system for any leaks by applying pressure and checking for any signs of seepage. If everything is secure, your fuel line is now ready for use.
Can You Pinch Fuel Line Hose with Hemostats? A Guide
You may want to see also
Secure Connections: Tighten connections securely, checking for leaks
When working with nylon fuel line fittings, ensuring tight and secure connections is crucial to prevent leaks and maintain the integrity of your fuel system. Here's a step-by-step guide to achieving secure connections:
Start by preparing the components. Ensure that the nylon fuel lines and fittings are clean and free from any debris or contaminants. Use a suitable solvent or cleaner to remove any old fuel residue or grease, especially if you're replacing existing fittings. This step is essential to ensure a proper bond and prevent any potential leaks.
Next, apply a thin layer of thread seal tape or pipe compound to the threads of the fittings. This additional layer of protection will provide extra security and help prevent leaks. Wrap the tape or compound clockwise around the threads, ensuring an even and consistent coating. Take care not to over-apply, as this can lead to excess material entering the fuel line.
Now, it's time to tighten the connections. Use the appropriate wrench or tool for the specific fitting type. Apply firm and consistent pressure, ensuring that the threads are fully engaged. The goal is to achieve a tight seal without overtightening, as this can damage the fittings or cause internal damage. A general rule of thumb is to tighten the connections until they are snug, but always refer to the manufacturer's guidelines for specific torque requirements.
After tightening, perform a leak test. This is a critical step to ensure the integrity of your fuel system. Apply a small amount of fuel or a suitable test fluid to the connections and observe for any signs of leakage. Check all joints, including the connections between the fuel lines and the fittings. If any leaks are detected, immediately tighten the affected areas further and retest. This process may require multiple attempts until a secure, leak-free connection is achieved.
Finally, once all connections are tight and leak-free, consider using a fuel line sealer or tape as an additional safety measure. This extra layer of protection can provide long-term security, especially in high-temperature environments. Always remember that proper installation and regular maintenance are key to keeping your fuel system reliable and efficient.
O-Ring Mystery: Trailblazer Fuel Line Diagram Decoded
You may want to see also
Frequently asked questions
You will need a set of wrenches or pliers to tighten the fittings securely. Additionally, a fuel line cutting tool or a sharp knife can be used to make precise cuts on the fuel lines.
Before connecting, ensure the surfaces are clean and free of any debris. Apply a thin layer of fuel line adhesive or tape to the ends of the lines, then insert the fittings over the lines, ensuring a snug fit. Use a primer or solvent to clean the threads if necessary, and then tighten the fittings firmly.
Yes, you can reuse old lines, but it's essential to inspect them for any signs of damage or wear. Cut off any damaged sections and ensure the remaining line is in good condition. You might also consider replacing the fittings to ensure a reliable connection.