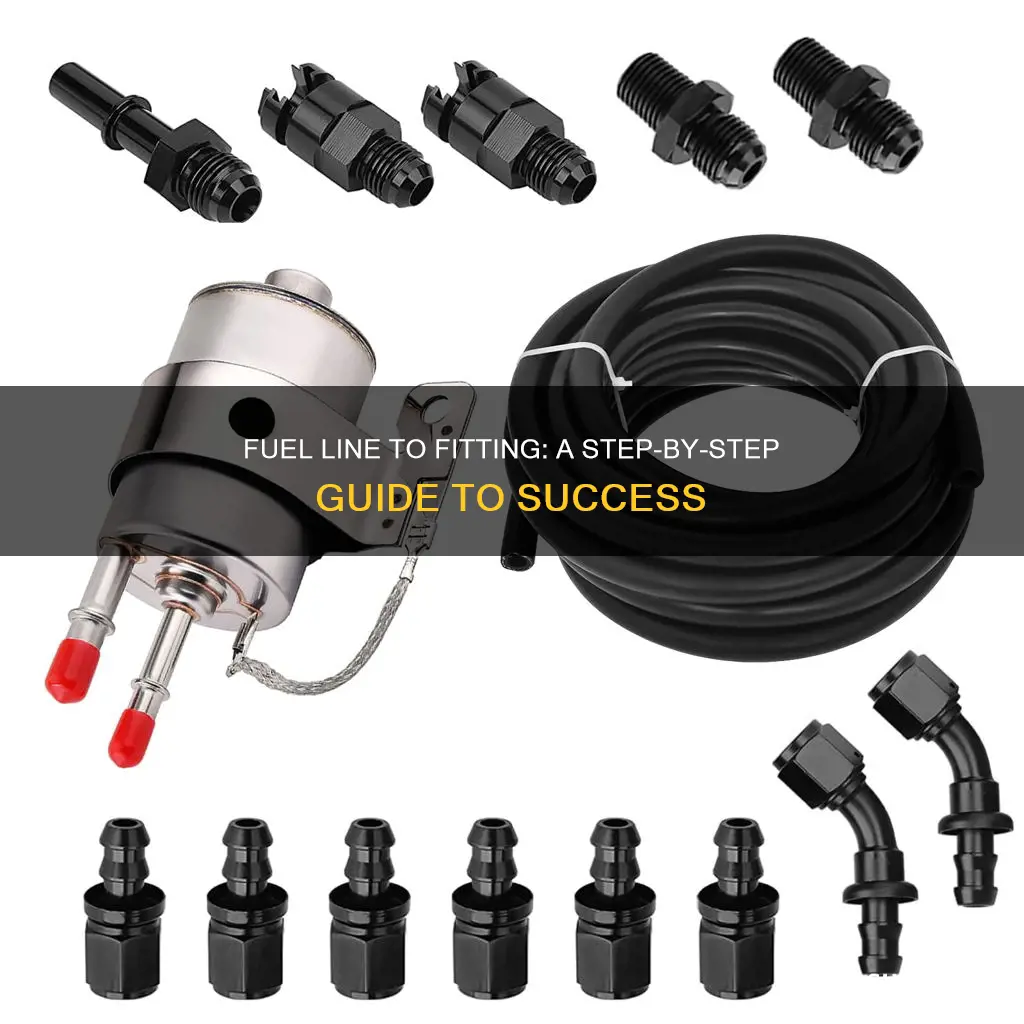
Turning a fuel line into a fitting is a common task for those working on vehicles or equipment that require fuel delivery systems. This process involves modifying a fuel line to connect it securely to a fuel tank, pump, or other components. It requires careful preparation, including cleaning the fuel line and ensuring it is free of debris, and then using the appropriate fitting and tools to create a tight, leak-free connection. This guide will provide a step-by-step process to achieve a professional-grade installation, ensuring the system's reliability and safety.
What You'll Learn
- Cutting the Line: Use a sharp, clean tool to carefully cut the fuel line to the desired length
- Deburring: Smooth the edges of the cut line to prevent damage to the fitting
- Cleaning: Ensure the line and fitting are free of dirt, debris, and old fuel
- Fitting Selection: Choose a fitting that matches the fuel line diameter and material
- Assembly: Tighten the fitting securely, using the appropriate tools and torque specifications
Cutting the Line: Use a sharp, clean tool to carefully cut the fuel line to the desired length
When working with fuel lines, precision and care are essential to ensure a safe and effective installation. One crucial step in this process is cutting the fuel line to the appropriate length. This task requires a sharp and clean tool to make a clean cut, ensuring a professional finish and preventing any potential leaks or damage. Here's a step-by-step guide to help you through this process:
Prepare Your Tools and Materials: Before you begin, ensure you have a high-quality, sharp utility knife or a fuel line cutter. These tools are designed to make clean, precise cuts. Additionally, have a pair of clean gloves to protect your hands and a cloth or rag to wipe away any fuel residue. It's important to work in a well-ventilated area and to take necessary safety precautions, such as wearing safety goggles, to protect your eyes from any potential splashes.
Measure and Mark: Carefully measure the length of the fuel line you need to cut. Double-check your measurements to ensure accuracy. Then, use a marker or a piece of chalk to make a clear mark on the fuel line at the desired cut point. This step is crucial to ensure you cut the line to the correct length, especially if you're working with a fuel line that needs to be connected to a specific fitting.
Make the Cut: Now, it's time to use your sharp tool. Position the knife or cutter at the marked spot and apply steady pressure. Cut slowly and carefully, following the natural curve of the fuel line to ensure a clean, straight cut. Avoid applying excessive force, as this can lead to a jagged edge. If you're using a utility knife, make sure to use a steady hand and a gentle touch to achieve a precise cut. For fuel line cutters, follow the manufacturer's instructions for the best results.
Examine the Cut: Once you've made the cut, take a moment to inspect the edge. A clean cut should have a smooth, straight edge without any burrs or sharp points. If the cut is not clean, you may need to re-cut the line, ensuring you use the same technique for a precise fit. This step is vital to guarantee a secure connection and to prevent any potential issues with fuel leakage.
Wipe and Prepare: After cutting, wipe the fuel line and the cut end with a clean cloth to remove any fuel residue. This step ensures that the fuel line is clean and ready for installation. It's also a good practice to wipe the fitting or connector you will be attaching to the cut end to ensure a proper seal.
By following these steps, you can ensure that your fuel line is cut accurately and safely, allowing for a seamless installation and minimizing the risk of any fuel-related issues. Remember, taking the time to do this right can save you from potential headaches and ensure the longevity of your vehicle's fuel system.
Chevy HHR Fuel Line Location: A Comprehensive Guide
You may want to see also
Deburring: Smooth the edges of the cut line to prevent damage to the fitting
When working with fuel lines, it's crucial to ensure that the edges of the cut line are smooth and free from sharp burrs. Deburring is a critical step in the process of turning a fuel line into a fitting, as it helps prevent damage to the fitting and ensures a secure and leak-free connection. Here's a detailed guide on how to deburr the edges effectively:
Start by identifying the cut line where the fuel line has been severed. Look for any rough or jagged edges that may have formed during the cutting process. These sharp edges can cause friction and wear on the fitting, leading to potential leaks or damage over time. Use a fine-grit sandpaper or a similar abrasive material to gently smooth out these edges. Start with a coarse-grit sandpaper to remove any large burrs and then progress to a finer grit for a more refined finish. Work the sandpaper along the length of the cut line, ensuring you cover the entire area. The goal is to create a smooth, even surface without leaving any sharp projections.
For a more precise and controlled deburring process, consider using a deburring tool or a specialized deburring machine. These tools are designed to remove small burrs and create a consistent, smooth finish. Apply gentle pressure and move the tool along the cut line, following the natural curve of the fuel line. This method is especially useful for intricate fittings or those with complex shapes. If you're working with a machine, ensure it is set to the appropriate speed and pressure to avoid damaging the fuel line material.
Another effective technique is to use a file to carefully remove the burrs. Select a file with a fine, smooth surface, such as a diamond-coated file, which is ideal for this purpose. File the cut line in a gentle, continuous motion, always moving in the direction of the material's grain. Take your time and be meticulous, as rushing this step may lead to uneven results. Remember, the goal is to create a seamless transition between the fuel line and the fitting.
After deburring, inspect the cut line closely to ensure the edges are smooth and free from any remaining burrs. You can use a magnifying glass or a bright light to aid in this inspection. If any sharp edges are still present, repeat the deburring process until you achieve the desired level of smoothness. This attention to detail will contribute to the overall quality and longevity of your fuel line fitting.
Fitech Go EFI-8 Fuel Line Sizing: Expert Guide
You may want to see also
Cleaning: Ensure the line and fitting are free of dirt, debris, and old fuel
When preparing a fuel line for installation or repair, it is crucial to ensure that it is clean and free of any contaminants. This process involves thoroughly cleaning the fuel line and fitting to remove dirt, debris, and any residual fuel that may have accumulated over time. Here's a step-by-step guide to achieving this:
Start by disconnecting the fuel line from its current source or the vehicle's fuel system. This step ensures that you can work on the line without any fuel pressure or potential hazards. Use appropriate tools to carefully detach the line, taking note of the connection points and any fittings or adapters involved. Once disconnected, you can begin the cleaning process.
The next step is to remove any visible dirt or debris from the fuel line. You can use a small brush or a cleaning tool specifically designed for fuel lines to gently scrub the interior surface. Pay close attention to any bends or kinks in the line, as these areas may accumulate more contaminants. For stubborn deposits or old fuel residue, consider using a fuel line cleaner or a mild solvent, but always exercise caution and follow the product instructions. Rinse the line thoroughly with clean water to remove any cleaning agents and ensure no residue remains.
After cleaning the fuel line, it's essential to inspect the fitting as well. Remove any old fuel or debris from the fitting's interior by using a similar cleaning process as before. Check for any signs of corrosion or damage and ensure the fitting is in good condition. If necessary, use a small brush or a compressed air tool to blow out any remaining particles.
Once the cleaning process is complete, allow the fuel line and fitting to air dry completely. Ensure there are no obstructions or moisture remaining inside the line, as this could lead to future issues. After drying, you can reassemble the fuel line and fitting, ensuring a secure and leak-free connection. Proper cleaning is a critical step to guarantee the longevity and efficiency of your fuel system.
Hose Clamps for 5/16 Fuel Lines: Size Matters
You may want to see also
Fitting Selection: Choose a fitting that matches the fuel line diameter and material
When transforming a fuel line into a fitting, the selection of the appropriate fitting is a critical step to ensure a secure and reliable connection. The first and most important consideration is the diameter of the fuel line. Different fuel lines have varying diameters, and it is essential to choose a fitting that matches this dimension. For example, if you have a 3/8-inch fuel line, you need a fitting designed for this specific diameter. Using a fitting that is too small or too large can lead to issues such as reduced flow, potential leaks, or even damage to the fuel line.
The material of the fuel line is another crucial factor. Fuel lines are typically made from materials like rubber, vinyl, or synthetic compounds, each with its own unique properties. The chosen fitting should be compatible with the material of the fuel line to ensure a proper seal and prevent any potential leaks. For instance, rubber fuel lines might require a fitting made from a flexible material that can accommodate slight movements, while vinyl lines could benefit from a more rigid fitting.
To ensure a proper fit, it is advisable to consult the manufacturer's specifications or seek guidance from automotive experts. They can provide information on the specific requirements for your vehicle's fuel line and recommend suitable fittings. Additionally, consider the type of fitting needed, such as a compression, quick-connect, or barbed fitting, each serving different purposes and applications.
When selecting a fitting, look for high-quality options made from durable materials to ensure longevity. Check for any additional features like gaskets or seals that enhance the connection's integrity. Properly aligning the fitting with the fuel line and using the appropriate tools for installation will further contribute to a successful and leak-free connection.
Remember, taking the time to choose the right fitting for your fuel line will result in a more efficient and safer fuel system, reducing the risk of fuel leaks and potential engine damage. It is a crucial step in the process of modifying or repairing a fuel line, ensuring a reliable and long-lasting solution.
Rubber vs. Steel Fuel Lines: When to Choose Each
You may want to see also
Assembly: Tighten the fitting securely, using the appropriate tools and torque specifications
When assembling a fuel line fitting, it's crucial to ensure a tight and secure connection to prevent any leaks or potential hazards. Here's a step-by-step guide on how to tighten the fitting securely:
Gather the Right Tools: Before you begin, make sure you have the necessary tools for the job. You'll typically need a wrench or a fitting spanner specifically designed for the type of fitting you're working with. The size and type of wrench should match the fitting's threads. Additionally, have a torque wrench or a socket set with various sizes to ensure accurate tightening.
Prepare the Fuel Line and Fitting: Ensure the fuel line is clean and free of any debris or contaminants. If necessary, cut the fuel line to the desired length and deburr the ends to create a smooth surface for the fitting. Slide the fitting onto the fuel line, ensuring it is aligned correctly. The fitting should have a secure grip on the fuel line, but not be too tight, as this can cause damage.
Tighten the Fitting: Now, it's time to tighten the fitting securely. Locate the wrench or fitting spanner and position it around the fitting. Apply firm pressure and rotate the fitting counterclockwise to tighten it. Use your hand or a torque wrench to apply the specified torque value, which can vary depending on the fitting type and manufacturer's recommendations. As a general rule, tighten the fitting until it is snug, but be careful not to over-tighten, as this can strip the threads or damage the fuel line.
Check for Leaks: After tightening, inspect the fitting for any signs of leakage. Apply a small amount of diesel or fuel to the fitting and observe if any fuel drips out. If there are any leaks, it may indicate an improper fit or an issue with the fuel line. In such cases, carefully inspect the connection and ensure the fuel line is properly seated within the fitting.
Final Adjustments: If the fitting is still not tight enough or leaks persist, you may need to make final adjustments. Loosen the fitting slightly and re-tighten it with the appropriate torque. This process ensures a secure and leak-free connection. Remember, the goal is to achieve a tight fit without causing damage to the fuel line or fitting.
By following these steps and using the correct tools, you can ensure a professional-grade assembly, providing a reliable and safe fuel system for your vehicle or equipment. Always refer to the manufacturer's guidelines for specific torque specifications and recommendations for your particular fitting type.
Unclogging the Fuel Line: A Step-by-Step Guide for 96 Jeep Cherokee Owners
You may want to see also
Frequently asked questions
Converting a fuel line into a fitting involves a few steps. First, you'll need to cut the fuel line to the desired length using a fuel line cutter or a sharp, clean blade. Ensure the cut is clean and straight. Then, you can use a fuel line fitting adapter or a fitting kit specific to your fuel line type. These kits often include a fitting, a ferrule, and a crimping tool. Insert the fuel line into the fitting, align the threads, and tighten securely using a wrench. Finally, inspect the connection for any leaks and ensure it is properly sealed.
Yes, you'll need a few essential tools for this conversion. A fuel line cutter or a sharp knife will help you make a clean cut. A fuel line fitting adapter or a fitting kit is crucial, as it provides the necessary components for the conversion. You'll also need a crimping tool to secure the fitting, and a wrench to tighten the connection. Additionally, have some fuel line sealant or tape ready to ensure a leak-free connection.
It's important to choose the right fitting for your fuel line. Different fuel lines have specific diameters and fitting requirements. Ensure you select a fitting that matches the fuel line's inner diameter and thread type. Using the correct fitting ensures a proper seal and prevents fuel leaks. It's recommended to consult a vehicle's manual or seek advice from a professional to identify the appropriate fitting for your specific fuel line.
To guarantee a secure and leak-free connection, follow these steps. Start by cleaning the fuel line and the fitting threads to remove any debris. Insert the fuel line into the fitting, ensuring it is straight and properly aligned. Use the crimping tool to apply the ferrule (a metal or plastic ring) onto the fuel line, following the manufacturer's instructions. Then, tighten the fitting securely with the wrench, being careful not to overtighten. Finally, inspect the connection for any signs of leakage and test the fuel system to ensure there are no issues.