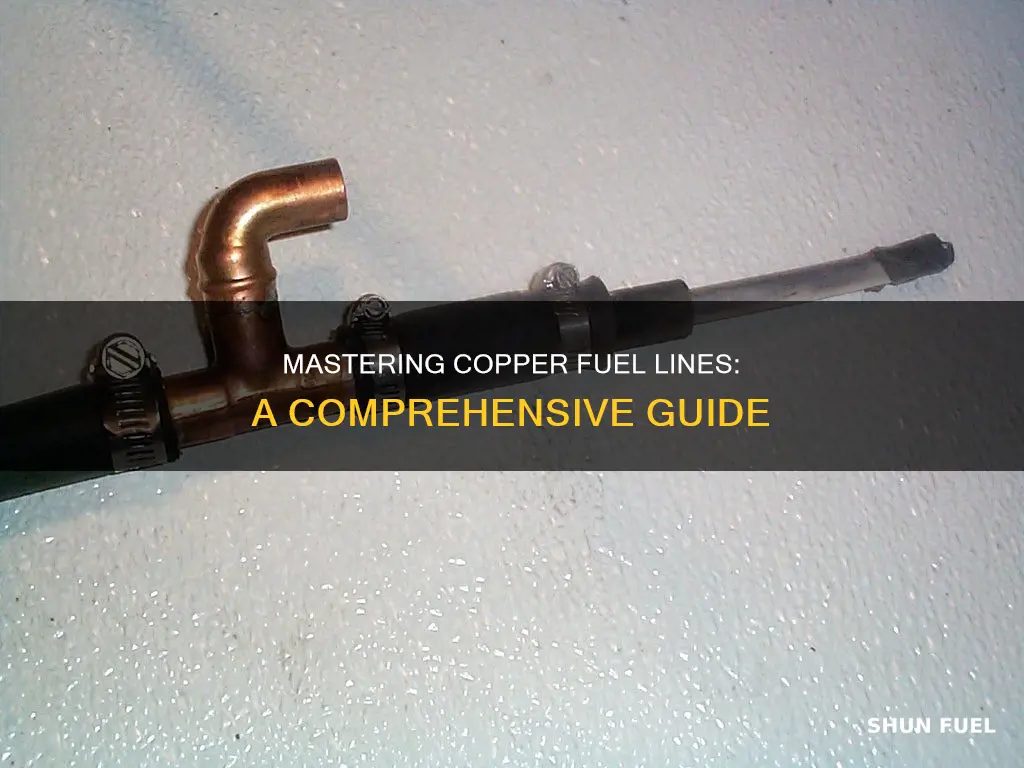
Copper fuel lines are a popular choice for many car enthusiasts and DIY mechanics due to their durability and ability to withstand high temperatures. Copper fuel lines offer an upgrade over traditional rubber or plastic lines, providing a more reliable and efficient fuel delivery system. This guide will provide a step-by-step process on how to install and maintain copper fuel lines, ensuring your vehicle's engine receives the clean and precise fuel it needs for optimal performance. Whether you're a seasoned mechanic or a hobbyist, understanding the process of working with copper fuel lines can be a valuable skill for any car enthusiast.
What You'll Learn
- Materials and Tools: Gather copper tubing, fuel line connectors, and necessary tools like a tube cutter
- Preparation: Clean and deburr the ends of the copper tubing for a secure connection
- Fitting Installation: Slide fittings onto the tubing, ensuring a tight and leak-free seal
- Bending and Routing: Carefully bend the tubing to the desired shape, considering fuel flow and vehicle layout
- Testing and Inspection: Check for leaks and ensure proper fuel flow before finalizing the installation
Materials and Tools: Gather copper tubing, fuel line connectors, and necessary tools like a tube cutter
When embarking on the task of copper fuel line installation, it's crucial to start with the right materials and tools. Copper tubing is a popular choice for fuel lines due to its durability and resistance to corrosion. It's essential to select the appropriate size and thickness of copper tubing to ensure a secure and reliable connection. The tubing should be free of any bends or kinks that could compromise its integrity.
Along with the tubing, you'll need a variety of fuel line connectors. These connectors come in different types, such as compression fittings, crimp fittings, and clamp-style connectors. Compression fittings are commonly used for their ease of installation and reliability. They consist of a fitting with a compression ring that tightens around the copper tubing, creating a secure seal. Crimp fittings are another option, where a special tool is used to crimp the connector onto the tubing, forming a tight bond. Clamp-style connectors are also available, which use a clamp to secure the tubing in place. It's important to choose the right type of connector based on your specific fuel line requirements.
Gathering the necessary tools is just as vital. A tube cutter is an essential tool for this project. It allows you to precisely cut the copper tubing to the desired length, ensuring a clean and accurate fit. Make sure to get a tube cutter that can handle the thickness of your copper tubing. Additionally, consider having a tubing bender on hand, especially if you need to bend the tubing to fit around certain engine components. Other tools you might find useful include a wrench or pliers for tightening connections, a fuel line inspection mirror to check for any blockages or damage, and safety gear such as gloves and safety goggles to protect yourself during the installation process.
Having all these materials and tools ready will ensure that you have a well-prepared and organized workspace, making the copper fuel line installation process smoother and more efficient. It's always a good idea to double-check your inventory before starting the project to avoid any last-minute surprises.
Oregon vs. Tygon: Choosing the Best Fuel Line for Your Needs
You may want to see also
Preparation: Clean and deburr the ends of the copper tubing for a secure connection
When preparing to connect copper fuel lines, ensuring a clean and smooth surface is crucial for a secure and leak-free joint. The process begins with meticulous cleaning to remove any contaminants that could compromise the integrity of the connection. Start by using a wire brush or a specialized cleaning tool to scrub the ends of the copper tubing. This step is essential to eliminate oxidation, which can create a rough surface and hinder the bonding process. Pay close attention to the edges, as any debris or oxidation left here can lead to a weak connection.
After thorough brushing, rinse the tubing with a clear, degreasing solvent to remove any remaining dirt or residue. This step ensures that the surface is not only clean but also free from any oily or greasy substances that might interfere with the bonding process. Once rinsed, allow the tubing to dry completely. You can use a soft cloth or a low-heat hairdryer on a cool setting to speed up the drying process while maintaining the integrity of the copper.
Deburring is the next critical step in the preparation process. This technique involves carefully smoothing the edges of the tubing to create a consistent and rounded surface. You can use a fine-grit sandpaper or a deburring tool specifically designed for copper. Gently file or sand the edges, ensuring that you remove any sharp points or burrs. The goal is to create a smooth, continuous surface that allows for a tight and secure connection without any protruding edges that could cause leaks.
For an even more precise and professional finish, consider using a specialized deburring tool or a small file designed for working with copper. These tools provide better control and accuracy, ensuring that the deburring process is thorough and consistent. Take your time with this step, as a well-deburred surface will significantly contribute to the overall quality of the fuel line connection.
In summary, the preparation of copper fuel lines involves a meticulous cleaning process to remove oxidation and contaminants, followed by thorough drying to ensure a clean surface. Deburring the ends of the tubing is then essential to create a smooth and rounded connection point, ensuring a secure and leak-free joint. These steps are fundamental to the success of any copper fuel line installation or repair.
Mastering Chainsaw Maintenance: A Guide to Replacing Fuel Lines
You may want to see also
Fitting Installation: Slide fittings onto the tubing, ensuring a tight and leak-free seal
When installing copper fuel lines, ensuring a secure and leak-free connection is crucial for the safety and performance of your vehicle. One effective method for achieving this is by using slide fittings, which provide a reliable and efficient way to join the tubing. Here's a step-by-step guide on how to properly install these fittings:
Start by preparing the tubing. Ensure that the copper fuel lines are clean and free from any debris or contaminants. Use a suitable solvent or cleaner to remove any old adhesive or residue from previous fittings. This step is essential to ensure a strong bond between the new fitting and the tubing.
Next, slide the fitting onto the tubing. Carefully align the fitting over the end of the tube, ensuring that the threads or locking mechanism of the fitting are properly positioned. The key to a successful installation is a tight fit, so apply firm pressure as you slide the fitting into place. Make sure the fitting is centered and secure, with no gaps or misalignments.
To ensure a leak-free seal, use a high-quality pipe compound or thread seal tape. Apply a generous amount of the compound to the threads of the fitting and the tubing. For slide fittings, you can also use a thread-locking adhesive or a specialized fitting compound. These products create a strong bond between the fitting and the tubing, preventing any potential leaks.
After applying the compound or adhesive, twist the fitting onto the tubing until it is fully engaged. Ensure that the threads are properly aligned and that the fitting is tightened securely. Check for any leaks by applying pressure to the connection and inspecting for any signs of leakage. If everything is tight and secure, your fitting installation is complete.
Remember, taking the time to properly prepare the tubing and use the right sealing materials will result in a robust and reliable fuel line system. Regularly inspect your connections and replace any worn-out fittings to maintain the safety and efficiency of your vehicle's fuel delivery system.
Braided Fuel Line Installation: A Step-by-Step Guide
You may want to see also
Bending and Routing: Carefully bend the tubing to the desired shape, considering fuel flow and vehicle layout
Bending and routing copper fuel lines is a crucial step in the installation process, requiring precision and careful consideration of the vehicle's layout and fuel flow. This process ensures that the fuel lines are not only functional but also aesthetically pleasing and safe. Here's a detailed guide on how to approach this task:
Understanding the Layout: Before you begin bending, it's essential to have a clear understanding of the vehicle's design and the desired placement of the fuel lines. Visualize the route the fuel will take from the tank to the engine. Consider the engine's position, the location of the fuel pump, and any existing components that might affect the line's path. This planning phase is critical to ensure the fuel lines are not only functional but also easily accessible for maintenance.
Gathering the Tools: You'll need a few essential tools for bending copper tubing. A tubing bender is a must-have; it allows you to create smooth, precise bends. Additionally, a pair of pliers or a tubing cutter will be useful for making adjustments and ensuring a clean cut. Consider using a tubing file or a similar tool to smooth out the inside of the bend, which helps prevent fuel leaks.
Bending Techniques: When bending the copper tubing, start by marking the desired bend points. Use a straight edge or a ruler to ensure accuracy. Apply firm pressure to the bender, following the manufacturer's instructions, and bend the tubing to the required angle. For tighter bends, you might need to apply more force, but always be cautious not to over-bend, as this can damage the tubing. Remember, the goal is to create a smooth, continuous curve that follows the natural flow of the vehicle's layout.
Considering Fuel Flow: As you bend the tubing, keep in mind the direction of fuel flow. Ensure that the bends do not restrict the flow or create unnecessary pressure points. The fuel lines should be able to accommodate the volume and pressure of the fuel without any bottlenecks or kinks. Proper bending techniques will help maintain the integrity of the fuel system.
Routing and Support: After bending, carefully route the fuel lines through the vehicle's interior, ensuring they are not pinched or damaged by sharp edges. Secure the lines with ties or clips to keep them in place and prevent tangling. Proper routing also involves considering the vehicle's movement during operation; fuel lines should not be able to come loose or rub against moving parts.
Mastering the art of bending and routing copper fuel lines is essential for a successful installation. It requires a combination of technical skill, spatial awareness, and attention to detail. By carefully planning, using the right tools, and considering the vehicle's layout and fuel flow, you can ensure a reliable and safe fuel system.
Mastering Quad Fuel Line Hose Attachment: A Step-by-Step Guide
You may want to see also
Testing and Inspection: Check for leaks and ensure proper fuel flow before finalizing the installation
Before finalizing the installation of copper fuel lines, it is crucial to conduct thorough testing and inspection to ensure the system's integrity and functionality. This process involves several key steps to verify that the fuel lines are leak-free and that the fuel is flowing correctly.
The first step is to check for leaks. Start by visually inspecting the fuel lines for any signs of damage, cracks, or bends that could lead to potential leaks. Look for any visible signs of corrosion or deterioration, especially at the connections and bends. Use a bright flashlight to illuminate the lines and inspect for any moisture or discolored areas, which could indicate a leak. Additionally, check the fittings and clamps for tightness; loose connections can lead to fuel escaping into the engine bay. If any issues are found, repair or replace the affected parts before proceeding.
Next, perform a pressure test to ensure the lines can withstand the fuel pressure. This can be done using a fuel pressure gauge and a small amount of compressed air or nitrogen. Connect the gauge to the fuel line and apply the pressure, ensuring it meets the manufacturer's specifications. Observe the gauge for any drops in pressure, which could indicate a leak. If the pressure holds steady, the lines are likely secure. However, if there are any leaks, address them immediately by tightening connections or replacing damaged lines.
To ensure proper fuel flow, start the engine and monitor its performance. Check for any unusual noises, such as hissing or roaring, which could indicate a fuel leak. Observe the engine's behavior; if it runs roughly or stalls, it may be due to insufficient fuel supply. Adjust the fuel flow rate by using a fuel pressure regulator or adjusting the fuel pump if necessary. Ensure that the fuel pump is functioning correctly and delivering the required volume and pressure to the engine.
Furthermore, consider using a fuel system diagnostic tool to verify the fuel flow and pressure. These tools can provide detailed readings of fuel pressure, flow rate, and volume, allowing for precise adjustments. By using such tools, you can fine-tune the system to ensure optimal performance.
In summary, testing and inspection are vital steps in the installation process. By checking for leaks, performing pressure tests, monitoring engine performance, and utilizing diagnostic tools, you can ensure that the copper fuel lines are installed correctly and will provide reliable fuel delivery to the engine. This meticulous approach helps prevent potential issues and ensures the longevity of the fuel system.
Dodge Truck Fuel Line Sizes: A Comprehensive Guide
You may want to see also
Frequently asked questions
Copper fuel lines are often used in high-performance or classic car applications due to their superior flexibility and corrosion resistance compared to traditional steel or aluminum lines. They offer improved fuel flow and can enhance the overall performance and longevity of the fuel system.
Installing copper fuel lines requires careful preparation and the right tools. Start by cleaning the fuel lines and ensuring they are free of any debris. Use a fuel line cutter to ensure precise lengths. Then, apply a suitable primer or adhesive to the ends of the lines and connect them to the fuel pump and tank. Tighten the connections securely but avoid over-tightening to prevent damage.
Copper is generally compatible with most fuel types, including gasoline, diesel, and ethanol blends. However, it's essential to check for any specific compatibility issues with your vehicle's fuel system and the type of fuel you use. Some fuel systems may require additional precautions or modifications to ensure optimal performance and safety.
To minimize the risk of leaks, it's crucial to follow proper installation procedures and use high-quality fittings and connectors. Ensure that all connections are tight and secure. Regularly inspect the fuel lines for any signs of damage, corrosion, or wear, especially in areas prone to vibration or impact. Promptly address any issues to maintain the integrity of the fuel system.