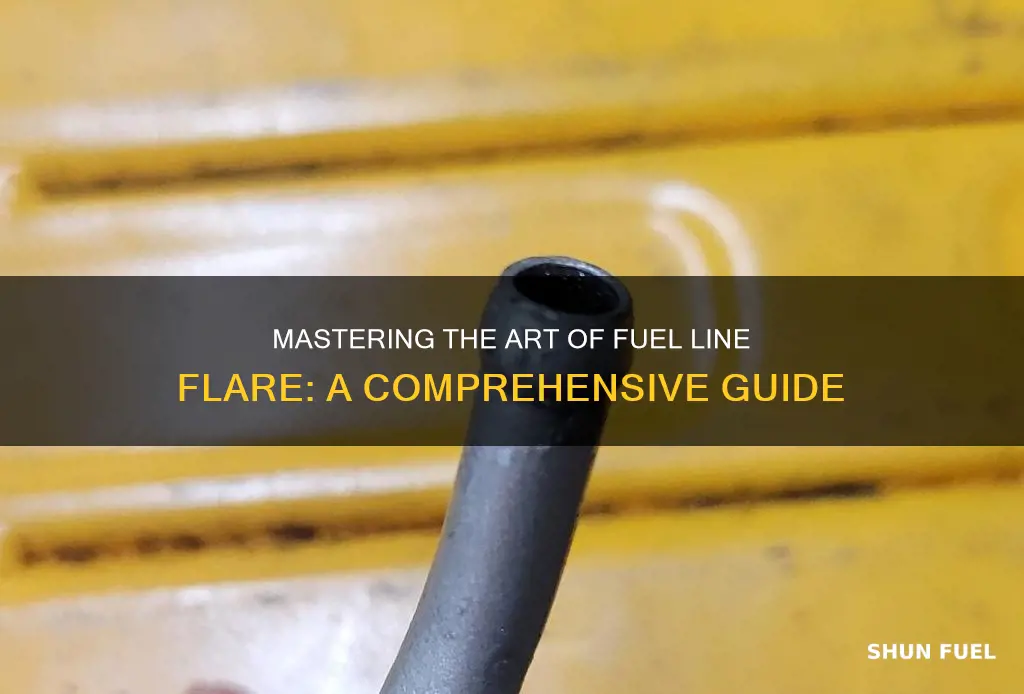
Flaring a 3/8 fuel line is a crucial step in ensuring the proper functioning of your fuel system. This process involves shaping the fuel line to create a smooth, tight bend that prevents fuel leaks and ensures optimal fuel flow. Whether you're a mechanic or a DIY enthusiast, knowing how to flare a 3/8 fuel line is essential for maintaining the integrity of your vehicle's fuel system. In this guide, we'll provide a step-by-step tutorial on how to flare a 3/8 fuel line, including the necessary tools and techniques to achieve a professional-quality finish.
What You'll Learn
- Tools and Materials: Gather necessary tools like fuel line cutters, crimping pliers, and fuel line tape
- Safety Precautions: Wear safety gear, ensure engine is off, and work in a well-ventilated area
- Fuel Line Inspection: Check for damage, kinks, or leaks before flaring
- Flaring Technique: Use a flaring tool to create a smooth, tight bend in the fuel line
- Crimping and Sealing: Crimp connections securely and seal with fuel line tape
Tools and Materials: Gather necessary tools like fuel line cutters, crimping pliers, and fuel line tape
To successfully flare a 3/8 fuel line, it's crucial to have the right tools and materials at hand. Here's a detailed breakdown of what you'll need:
Fuel Line Cutters: These specialized tools are designed to cut fuel lines cleanly and precisely. Look for cutters that can handle the thickness of your 3/8 fuel line. Opt for a set that includes different sizes to accommodate various diameters.
Crimping Pliers: Crimping pliers are essential for creating secure and leak-tight connections. Choose a pair with a comfortable grip and adjustable jaws to accommodate different fuel line sizes. Make sure they have a good range of crimping dies, including those for 3/8 fuel lines.
Fuel Line Tape: This is a specialized adhesive tape designed for sealing fuel line connections. It's crucial to use the right type of tape for your fuel line material. Look for tape specifically labeled for fuel lines, as it will provide the best bonding and resistance to fuel leaks.
Safety Gear: While not strictly a tool, safety gear is essential. Wear gloves to protect your hands from sharp edges and potential fuel spills. Safety goggles are also recommended to shield your eyes from any debris or splashes.
Work Surface: A clean, flat work surface is essential for accurate and safe flaring. A dedicated workbench or a sturdy table will provide the stability needed for the process.
Having these tools and materials ready will significantly contribute to the success of your fuel line flaring project. Remember to inspect each tool for any damage before use and replace any that are worn out to ensure a safe and effective repair.
Air in Fuel Line: Throttle Lag or Performance Boost?
You may want to see also
Safety Precautions: Wear safety gear, ensure engine is off, and work in a well-ventilated area
Before you begin any work on flaring a 3/8 fuel line, it is crucial to prioritize safety. This process involves working with fuel, which can be hazardous if not handled properly. Here are some essential safety precautions to follow:
Personal Protective Equipment (PPE): Always wear appropriate safety gear to protect yourself. This includes heat-resistant gloves, safety goggles, and a respirator mask to guard against inhaling fuel vapors. Additionally, consider wearing long sleeves and pants to minimize skin contact with hot surfaces. Ensure that your PPE is in good condition and suitable for the task at hand.
Engine Safety: Start by ensuring that the engine is turned off and the vehicle is in a secure position. Working on a running engine can be extremely dangerous due to the risk of fuel explosions and fires. Allow sufficient time for the engine to cool down before proceeding. It is also advisable to disconnect the battery to eliminate any electrical hazards.
Work Environment: Choose a suitable work area that is well-ventilated and free from potential hazards. Fuel lines should be worked on in a well-ventilated garage or workshop to minimize the risk of fuel inhalation. Ensure there are no open flames or sparks nearby, as these can ignite fuel vapors. Keep flammable materials and substances away from the work area.
Ventilation and Respiratory Protection: Proper ventilation is critical when working with fuel. If you are working in a confined space, use a fan to increase air circulation. Consider setting up a temporary ventilation system if necessary. Always wear a respirator mask to protect your lungs from inhaling fuel fumes, especially when cutting or welding fuel lines.
Tool and Equipment Safety: Inspect all tools and equipment you will be using. Ensure they are in good working condition and suitable for the task. Keep your workspace organized to avoid accidents caused by tripping or falling objects. Have a fire extinguisher nearby, and familiarize yourself with its use in case of emergencies.
Remember, safety should always be the top priority when working with fuel lines or any automotive repairs. By following these precautions, you can minimize the risks associated with the task and ensure a safer working environment.
Mastering the Art of Fuel Line Disconnection: A Step-by-Step Guide
You may want to see also
Fuel Line Inspection: Check for damage, kinks, or leaks before flaring
Before attempting to flare a 3/8 fuel line, it is crucial to conduct a thorough inspection to ensure the process is done safely and effectively. This initial step is often overlooked but is essential to prevent potential issues and ensure the longevity of the fuel system. Here's a comprehensive guide to inspecting the fuel line:
Visual Inspection: Start by examining the fuel line for any visible signs of damage, cracks, or corrosion. Look for any discolored areas, especially if the fuel line has been exposed to harsh chemicals or extreme temperatures. Check for any bends or kinks in the line, as these can cause reduced flow or even blockages. Ensure that the fuel line is not pinched or compressed in any area, as this can lead to potential leaks. Pay close attention to the connections and fittings, ensuring they are secure and free from any signs of deterioration.
Leak Detection: A critical part of the inspection is to identify potential leak points. Start by applying a small amount of diesel fuel or a suitable leak detection fluid along the length of the fuel line. Allow it to sit for a few minutes, then inspect the area carefully. Any areas where the fluid has formed droplets or pooled indicate a potential leak site. Also, check for any signs of fuel vapor escaping, which could be a sign of a damaged or compromised line.
Pressure Testing: To further ensure the integrity of the fuel line, consider performing a pressure test. This can be done using a fuel line pressure gauge and a compressed air source. Inflate the line to a specified pressure and observe for any leaks or drops in pressure. This test helps identify weak points or damaged areas that might not be visible during a visual inspection.
Kink and Flexibility Check: Fuel lines need to be flexible to accommodate engine movement, so it's essential to check their flexibility. Try to bend the line gently at various points to ensure it doesn't kink or break. A kinked fuel line can restrict flow and potentially cause engine performance issues. Also, ensure that the line is not twisted or coiled in a way that might cause damage during the flaring process.
By following these inspection steps, you can identify and address any potential issues with the fuel line before proceeding with the flaring process. This proactive approach ensures a safer and more efficient fuel system, reducing the risk of leaks, engine problems, and costly repairs. Remember, proper inspection is the foundation for successful and safe fuel line work.
Optimizing Cavitation Injection: Fuel Efficiency and Performance
You may want to see also
Flaring Technique: Use a flaring tool to create a smooth, tight bend in the fuel line
Flaring is a crucial technique used in plumbing and automotive repair to create a smooth, tight bend in a fuel line, ensuring a secure and leak-free connection. When dealing with a 3/8-inch fuel line, the flaring process involves using a specialized tool to shape the end of the line, creating a precise and durable joint. This method is particularly important in fuel systems, where even a small leak can lead to engine performance issues or safety hazards.
The flaring tool is designed to apply controlled force to the fuel line, forcing it into a specific shape. This process requires precision and skill to ensure the bend is tight and uniform. Start by positioning the fuel line securely in the flaring tool, ensuring it is centered and aligned with the tool's jaws. The tool's jaws should be adjusted to match the diameter of the fuel line, providing a snug fit. Apply steady pressure and rotate the tool in a clockwise direction, creating a gradual bend. The goal is to form a smooth, 90-degree angle without any sharp creases or kinks.
As you work, maintain a consistent force and avoid applying too much pressure, which could damage the fuel line. The flaring tool should guide the line, ensuring the bend is consistent and free from any sharp edges. This technique is crucial to prevent fuel leaks and maintain the integrity of the fuel system. Once the desired bend is achieved, carefully remove the fuel line from the tool, inspecting the flare for any imperfections.
Practice and patience are key when mastering the art of flaring. It may take a few attempts to get the hang of it, but with time, you'll be able to create professional-quality flares. Remember, the goal is to create a tight, smooth bend that can withstand the pressure and movement within the fuel system. Always ensure you have the correct tools and follow the manufacturer's guidelines for the best results.
In summary, flaring a 3/8-inch fuel line using a specialized tool is an essential skill for any mechanic or DIY enthusiast. It allows for a secure connection, preventing potential fuel leaks and ensuring optimal engine performance. With practice and attention to detail, you can master this technique and tackle fuel line repairs with confidence.
Poulan Pro's Unique Fuel Line: Unlocking the Mystery
You may want to see also
Crimping and Sealing: Crimp connections securely and seal with fuel line tape
When working with fuel lines, ensuring a secure and reliable connection is crucial to prevent leaks and maintain the integrity of your vehicle's fuel system. Crimping and sealing are essential steps in the process of connecting fuel lines, and they require precision and attention to detail. Here's a step-by-step guide to mastering these techniques:
Crimping Connections:
Start by gathering the necessary tools, including a crimping tool designed for 3/8-inch fuel lines. Measure and cut the fuel line to the desired length, ensuring it is slightly longer than the required length for the connection. Prepare the fitting by cleaning it and ensuring it is free of any debris or contaminants. Slide the fitting onto the fuel line, positioning it where you intend to make the connection. Use the crimping tool to apply pressure to the fitting, following the manufacturer's instructions for the specific crimping technique. Apply consistent force and ensure the crimp is complete by checking the fit with your fingers or a tool. A secure crimp will create a tight, reliable connection.
Sealing with Fuel Line Tape:
After crimping the connection, it's essential to seal it to prevent fuel leaks. Clean the crimped area to remove any excess fuel line material. Wrap a layer of fuel line tape around the crimped connection, ensuring it covers the entire crimp. Apply firm pressure as you wrap the tape to create a tight seal. Continue wrapping the tape in a clockwise direction, overlapping each layer slightly. The tape should be snug and free of any wrinkles or creases. Finish by securing the tape with a small amount of fuel line cement, following the product's instructions. This additional step provides an extra layer of protection against fuel leaks.
Practice and precision are key when crimping and sealing fuel line connections. Take your time, use the right tools, and follow the manufacturer's guidelines for the best results. Properly crimped and sealed connections will ensure a reliable fuel supply, contributing to the overall performance and safety of your vehicle. Remember, in the world of automotive repairs, a secure connection is a happy connection!
Butyl's Role in Fuel Line Safety: A Comprehensive Guide
You may want to see also
Frequently asked questions
Flaring a fuel line is a process used to create a smooth, bent transition at the end of the line, which helps to prevent leaks and ensures a secure connection. It is an essential step in plumbing and automotive applications to maintain the integrity of the fuel system.
First, ensure you have the correct flaring tool for the size of the fuel line. Place the line into the tool, aligning the end with the flaring die. Apply force and rotate the tool to create the flare. The process involves bending the metal to form a cone-shaped flare, which should be smooth and free of any sharp edges.
Yes, it's crucial to follow these techniques: use the right amount of force, apply consistent pressure, and rotate the tool in a controlled manner. Take your time and make precise bends to achieve a tight, secure flare. Avoid over-bending, as it can lead to damage or cracking.
Common issues include using excessive force, improper alignment, or not following the manufacturer's instructions. Over-bending can cause the flare to become too tight, leading to cracking. Insufficient force or incorrect rotation may result in an incomplete or uneven flare.
It is recommended to use flaring tools specifically designed for the size of the fuel line you are working with. Different sizes require different amounts of force and precision. Reusing tools for various sizes may lead to inaccurate flares and potential fuel leaks. It's best to invest in tools tailored to your specific fuel line requirements.