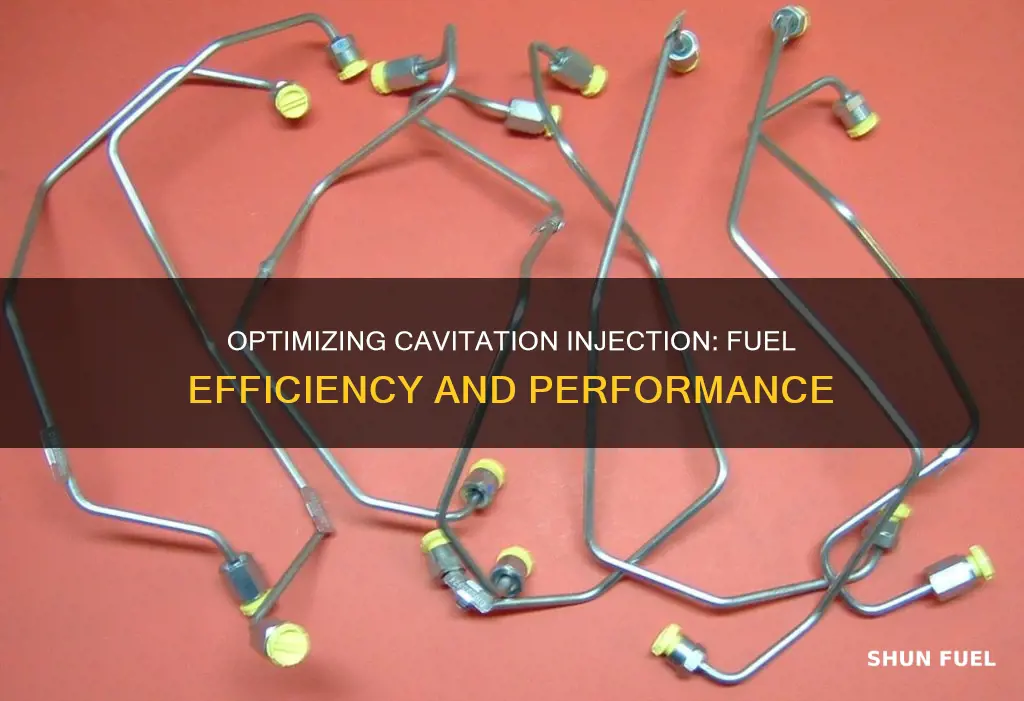
Understanding the optimal fuel flow rate from cavitation injection lines is crucial for optimizing engine performance and fuel efficiency. This paragraph introduces the topic by highlighting the importance of precise fuel management in engine systems, particularly focusing on the role of cavitation injectors. It emphasizes the need to determine the appropriate fuel output from these lines to ensure efficient combustion, minimize emissions, and maintain engine health. By exploring this subject, we can gain insights into the intricate relationship between fuel injection, engine operation, and the overall performance of internal combustion engines.
What You'll Learn
- Fuel Pressure Regulation: Adjusting pressure to ensure optimal fuel atomization and combustion
- Fuel Flow Control: Managing fuel flow rate to match engine demand and prevent over-fuelling
- Fuel Line Design: Optimizing line diameter and length for efficient fuel delivery
- Fuel Injector Nozzle Geometry: Designing nozzles to control fuel spray patterns and droplet size
- Fuel Return Systems: Implementing systems to manage excess fuel and prevent engine flooding
Fuel Pressure Regulation: Adjusting pressure to ensure optimal fuel atomization and combustion
Fuel pressure regulation is a critical aspect of engine performance, especially in systems utilizing cavitation-based fuel injection. The process involves precisely controlling the pressure of the fuel as it exits the injection lines to ensure optimal atomization and combustion. This is a complex task, as the fuel must be atomized to a specific size to achieve the desired air-fuel mixture for efficient combustion.
In cavitation-based injection systems, the fuel is injected at high pressure, often in the range of 300 to 500 bar, which is then reduced to a lower pressure as it exits the injectors. This pressure drop is crucial for proper atomization. If the pressure is too high, it can lead to fuel spray being too coarse, resulting in poor atomization and incomplete combustion. Conversely, if the pressure is too low, the fuel may not atomize effectively, leading to misfires and reduced engine performance.
The key to achieving optimal fuel atomization is to maintain a consistent pressure drop across the injectors. This can be challenging due to various factors such as fuel pump characteristics, line restrictions, and temperature variations. For instance, fuel temperature can significantly impact pressure; colder fuel is more viscous and may not atomize as well, requiring adjustments to the pressure settings.
Engineers and technicians use specialized tools and sensors to monitor fuel pressure and make real-time adjustments. These tools measure the pressure at different points in the system, allowing for fine-tuning to ensure the fuel exits the injectors at the correct pressure. This process is often automated, with electronic controls adjusting the pressure based on engine load, speed, and other operating conditions.
Proper fuel pressure regulation is essential for maintaining engine performance, fuel efficiency, and emissions compliance. It ensures that the fuel is atomized to the correct size, allowing for efficient combustion and minimizing the formation of harmful pollutants. Regular maintenance and calibration of the fuel injection system are necessary to guarantee optimal performance and longevity.
Essential Fittings for High-Pressure Fuel Lines: 60 PSI Requirements
You may want to see also
Fuel Flow Control: Managing fuel flow rate to match engine demand and prevent over-fuelling
The precise management of fuel flow is a critical aspect of engine performance and efficiency, especially in modern fuel injection systems. When it comes to cavitation injection lines, the challenge lies in ensuring that the fuel flow rate matches the engine's demand while avoiding over-fuelling, which can lead to inefficient combustion and potential engine damage.
In the context of cavitation injection, the fuel flow rate is controlled by a carefully designed system that regulates the pressure and volume of fuel entering the engine. This system typically includes a fuel pump, a fuel pressure regulator, and a precision fuel flow meter. The fuel pump is responsible for delivering the required fuel volume at the necessary pressure, ensuring that the fuel is atomized and mixed with air for optimal combustion. The pressure regulator maintains a consistent pressure, preventing excessive fuel pressure that could lead to fuel spray disruption and inefficient atomization.
The fuel flow meter is a critical component that measures and controls the exact amount of fuel entering the engine. It operates by monitoring the fuel flow rate and adjusting the fuel pressure or flow control valves accordingly. This ensures that the engine receives the precise amount of fuel required for the current operating conditions. For instance, during high-load conditions, the engine demands more fuel, and the flow control system increases the fuel flow rate to meet this demand while maintaining optimal combustion.
Over-fuelling can have detrimental effects on engine performance and longevity. When the fuel flow rate exceeds the engine's requirement, it can lead to excessive air-fuel mixture, causing misfires and reduced engine power. Moreover, over-fuelling can result in increased emissions of unburned hydrocarbons and carbon monoxide, violating environmental regulations. To prevent over-fuelling, the fuel flow control system employs various strategies, such as feedback control loops and real-time engine data analysis. These mechanisms allow the system to adjust the fuel flow rate dynamically, ensuring that the engine operates within the optimal fuel-air ratio at all times.
In summary, managing the fuel flow rate is essential for optimizing engine performance and preventing over-fuelling. By employing precise fuel flow control systems, engineers can ensure that the engine receives the right amount of fuel, promoting efficient combustion and reducing emissions. This level of control is particularly crucial in cavitation injection systems, where the fuel flow rate directly impacts engine operation and longevity.
Mastering Fuel Return Line Testing: A Comprehensive Guide
You may want to see also
Fuel Line Design: Optimizing line diameter and length for efficient fuel delivery
The design of fuel lines is a critical aspect of any fuel injection system, especially in high-performance engines where precise fuel delivery is essential for optimal performance and efficiency. When it comes to optimizing fuel line design for efficient fuel delivery, the diameter and length of the lines play a pivotal role. These factors directly influence the flow rate, pressure drop, and overall performance of the fuel injection system.
The diameter of the fuel line is a key consideration. A larger diameter allows for a higher flow rate, which is crucial for engines that require rapid and precise fuel injection. However, increasing the diameter also increases the line's resistance to pressure drop, which can lead to fuel pressure losses. The ideal diameter should balance these factors, ensuring that the fuel flows efficiently without excessive pressure drop. This balance is often achieved through careful calculations and simulations, taking into account the engine's specific requirements and operating conditions.
Line length is another critical factor. Longer fuel lines can introduce additional pressure drops due to friction and the energy required to move the fuel through the line. This pressure drop can be significant, especially in high-performance engines with high fuel flow rates. To mitigate this, engineers often use shorter lines or incorporate pressure regulators and boosters to maintain the required fuel pressure throughout the system. The length of the fuel lines should be optimized to minimize pressure losses while ensuring that the fuel reaches the injectors at the desired pressure and flow rate.
Optimizing fuel line design involves a comprehensive understanding of fluid dynamics and engine performance. Engineers use specialized software and simulations to model the fuel flow, pressure drops, and potential issues associated with different line diameters and lengths. These simulations help identify the optimal design that meets the engine's performance goals while ensuring efficient and reliable fuel delivery. By carefully selecting the line diameter and length, engineers can fine-tune the fuel injection system to deliver the precise amount of fuel required for optimal combustion.
In summary, fuel line design is a critical component of efficient fuel delivery in high-performance engines. The diameter and length of the fuel lines must be carefully optimized to balance flow rate, pressure drop, and engine requirements. Through detailed calculations, simulations, and a deep understanding of fluid dynamics, engineers can create fuel injection systems that deliver the right amount of fuel at the right time, resulting in improved engine performance and efficiency. This meticulous design process ensures that the fuel lines play a vital role in achieving the engine's full potential.
Is Aluminum Fuel Line Legal for NHRA Competition?
You may want to see also
Fuel Injector Nozzle Geometry: Designing nozzles to control fuel spray patterns and droplet size
The design of fuel nozzles plays a critical role in determining the spray pattern and droplet size of fuel, which directly impacts engine performance and efficiency. Nozzle geometry is a key factor in achieving the desired fuel atomization and spray characteristics. The primary goal is to create a spray pattern that ensures efficient mixing of fuel and air, leading to optimal combustion.
Nozzle design involves several parameters that influence the spray's behavior. One crucial aspect is the nozzle orifice diameter, which directly affects the fuel flow rate and spray velocity. A smaller orifice diameter results in a higher flow rate and a more concentrated spray, while a larger orifice produces a lower flow rate and a wider spray pattern. Engineers carefully select the orifice size based on the engine's requirements, ensuring that the fuel is atomized effectively without excessive pressure drop.
Another important consideration is the nozzle exit geometry, which includes the shape and contour of the exit orifice. The design of this region can influence the spray's angle and the distribution of fuel droplets. For instance, a conical or tapered exit can promote a more uniform spray, while a flat or slightly curved surface may result in a more directional spray, beneficial for specific engine operating conditions. The nozzle exit's design also impacts the spray's penetration and mixing quality within the combustion chamber.
Additionally, the nozzle's internal flow path and the presence of swirl or vortex generators are essential design elements. These features can manipulate the fuel's flow direction and create a swirling motion, leading to improved atomization and spray stability. Swirl generators are particularly useful in high-pressure fuel systems, where they help maintain droplet size and prevent fuel from being pushed back into the fuel rail.
Optimizing nozzle geometry requires a comprehensive understanding of fluid dynamics and engine performance. Engineers use computational fluid dynamics (CFD) simulations to model the fuel spray's behavior under various conditions. These simulations help predict spray patterns, droplet sizes, and fuel-air mixing, allowing for the fine-tuning of nozzle designs. By carefully adjusting the nozzle's geometry, engineers can achieve the desired fuel atomization, spray penetration, and overall engine performance.
Optimizing Fuel Delivery: Choosing the Right Size for Your Viva HC
You may want to see also
Fuel Return Systems: Implementing systems to manage excess fuel and prevent engine flooding
Implementing an efficient fuel return system is crucial for managing excess fuel and preventing engine flooding, especially in high-performance engines with direct fuel injection. The concept of fuel return lines is to ensure that any excess fuel that cannot be burned efficiently is safely returned to the fuel tank or reservoir, preventing it from entering the engine's intake system and causing potential issues. This is particularly important in engines with electronic fuel injection (EFI) and common rail systems, where precise fuel management is essential for optimal performance and emissions control.
The primary function of a fuel return system is to provide a path for excess fuel to be directed away from the engine. When an engine operates at low loads or during idling, it may not require the full amount of fuel injected, leaving excess fuel in the injection lines. This excess fuel can lead to several problems, including engine flooding, where the air-fuel mixture becomes too rich, leading to poor performance and potential engine damage.
To implement an effective fuel return system, engineers often design dedicated fuel return lines that are separate from the main fuel injection lines. These return lines are strategically positioned to allow excess fuel to flow back to the fuel tank or reservoir. The design and placement of these lines are critical to ensure that fuel is returned efficiently without causing any backpressure issues in the injection system.
One common approach is to use a small-bore return line with a restricted opening, creating a pressure differential that facilitates the return of excess fuel. This design ensures that the fuel flow rate is controlled, allowing for a gradual and smooth return of fuel to the tank. Additionally, some systems incorporate a check valve to prevent the backflow of fuel during high-pressure conditions, ensuring a one-way flow of excess fuel.
In high-performance applications, fuel return systems may also include pressure regulators and filters to manage the quality and flow rate of the returning fuel. These components help maintain the overall fuel system's integrity and ensure that the fuel returned to the tank is clean and free from contaminants. Proper implementation of fuel return systems is essential for engine longevity and optimal performance, especially in racing or high-demand applications where fuel management is critical.
Choosing the Right Fuel Line: Size Matters!
You may want to see also
Frequently asked questions
The amount of fuel injected through these lines can vary depending on the engine design and operating conditions. Generally, cavitation injectors are used to provide a precise and controlled fuel injection, often in the range of a few milligrams to a few grams per cycle. This is a small but crucial amount to ensure efficient combustion and performance.
Cavitation injectors are designed to improve engine performance and efficiency. They create a low-pressure zone, which draws fuel into the combustion chamber, enhancing the mixing process and promoting complete combustion. This results in better power output, improved fuel economy, and reduced emissions.
Yes, the fuel injection rate can be adjusted to optimize engine performance. This adjustment is often done through electronic controls that can vary the fuel pressure, injection timing, and duration. By fine-tuning these parameters, engineers can ensure the engine operates efficiently across different loads and speeds.
Injecting too much fuel can lead to excessive combustion, causing a rich mixture and potential engine knock. On the other hand, injecting too little fuel may result in a lean mixture, leading to reduced power, poor performance, and potential engine misfires. Therefore, precise control and calibration are essential to maintain optimal engine operation.