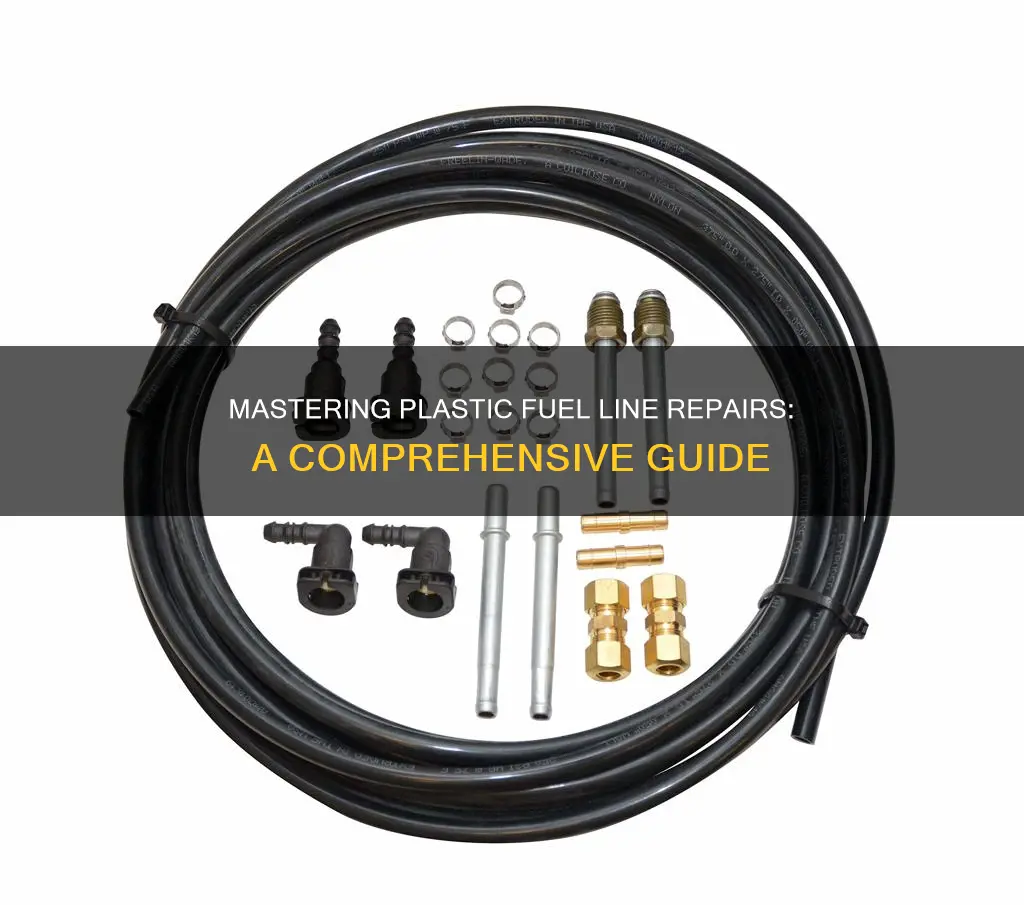
Fixing a plastic fuel line can be a straightforward process if you follow the right steps. Whether you're dealing with a small tear or a more significant damage, it's important to address the issue promptly to prevent fuel leaks and potential engine problems. In this guide, we'll walk you through the necessary tools, materials, and techniques to effectively repair a plastic fuel line, ensuring it's safe and reliable once again.
What You'll Learn
- Identify the Problem: Inspect for cracks, brittleness, or fuel leaks
- Prepare the Line: Clean and dry the fuel line before replacement
- Choose the Right Material: Select a compatible replacement material for the fuel line
- Cut and Install: Carefully cut and install the new fuel line
- Test and Secure: Test for leaks and ensure proper connection and routing
Identify the Problem: Inspect for cracks, brittleness, or fuel leaks
When dealing with a plastic fuel line, the first step in identifying any issues is a thorough visual inspection. This process is crucial to ensure the safety and efficiency of your vehicle's fuel system. Start by examining the fuel line for any visible signs of damage or deterioration. Look for cracks, which could be a result of age, heat exposure, or physical impact. Even small cracks can lead to fuel leaks, which can cause environmental contamination and potentially dangerous situations. Check for brittleness, especially in areas where the fuel line is exposed to extreme temperatures or vibrations. Plastic fuel lines can become brittle over time, and this can lead to a higher risk of breakage.
Pay close attention to the connections and fittings. These are common points of failure due to the stress they endure. Inspect the fittings for any signs of corrosion or damage that might compromise their ability to hold the fuel line securely. If you notice any cracks or brittleness, it's essential to take action immediately. Even a small crack can expand over time, leading to more significant issues. Additionally, check for any signs of fuel leakage around the connections. A fuel leak is a serious problem and can lead to engine misfires, reduced performance, and potential safety hazards.
During your inspection, consider the overall condition of the fuel line. Look for any signs of swelling, softening, or discoloration, as these could indicate internal damage or degradation. If you find any of these issues, it's best to replace the fuel line to prevent further complications. Remember, regular maintenance and timely inspections can help avoid costly repairs and ensure the longevity of your vehicle's fuel system.
Understanding Fuel Impulse Lines: Their Role in Engine Performance
You may want to see also
Prepare the Line: Clean and dry the fuel line before replacement
Before you begin the process of replacing a damaged plastic fuel line, it is crucial to ensure that the old line is thoroughly prepared. Start by disconnecting the fuel line from the engine and the fuel tank. This step is essential to prevent any accidental fuel spillage during the cleaning process. Once disconnected, locate the fuel line and inspect it for any signs of damage, cracks, or blockages. If there are any visible issues, it is best to replace the entire line to avoid potential leaks.
Cleaning the fuel line is a critical step to ensure a proper repair. Use a fuel line cleaner, which can be purchased from automotive stores. This cleaner is specifically designed to dissolve and remove any built-up fuel, varnish, or debris that may have accumulated inside the line. Follow the instructions on the cleaner's packaging for the correct application method. Typically, you will need to spray or pour the cleaner into the fuel line and allow it to sit for a specified duration, which can range from a few minutes to a few hours, depending on the product.
After the cleaning process, it is vital to rinse the fuel line to remove any remaining cleaner and debris. Use a garden hose with a gentle spray setting to flush out the line. Start at the fuel tank end and work your way towards the engine, ensuring that you rinse thoroughly. This step helps to eliminate any residue and prepares the line for its new installation.
Drying the fuel line is an often-overlooked but crucial step. Moisture can lead to corrosion and further damage, so it is essential to ensure the line is completely dry before proceeding. Use a clean cloth or towel to wipe down the fuel line, removing any visible moisture. You can also use a hairdryer on a low setting to speed up the drying process, being careful not to apply excessive heat that could damage the plastic.
Once the fuel line is clean, dry, and free of any debris or moisture, it is ready for replacement. This preparation process ensures that the new fuel line will have a clean and dry interior, reducing the risk of future issues and providing a more reliable fuel supply to the engine. Proper preparation is key to a successful repair, so take the time to follow these steps carefully.
Quick Steel Pudy Removal: Fuel Line Rescue Tips
You may want to see also
Choose the Right Material: Select a compatible replacement material for the fuel line
When dealing with a damaged or old plastic fuel line, choosing the right replacement material is crucial to ensure the system's longevity and reliability. The primary goal is to select a material that can withstand the harsh conditions of the fuel environment, including temperature fluctuations, fuel type, and chemical resistance. Here's a guide to help you make the right choice:
Identify the Original Material: Start by examining the existing fuel line to identify the type of plastic used. Common materials include polyvinyl chloride (PVC), high-density polyethylene (HDPE), and cross-linked polyethylene (PEX). Each material has unique properties, and knowing the original type will help you find a compatible replacement. For instance, PVC is known for its flexibility and chemical resistance, while HDPE is more rigid and suitable for high-pressure applications.
Consider Fuel Compatibility: Different fuels have varying chemical compositions, and some can degrade certain plastics over time. For example, ethanol-blended fuels can be more corrosive to certain plastics. If your vehicle uses ethanol, opt for a fuel line material that is specifically designed to withstand these blends, such as certain types of HDPE or PEX. Always check the manufacturer's recommendations or consult a professional to ensure compatibility.
Temperature and Flexibility: Plastic fuel lines must endure a wide range of temperatures, from cold starts in winter to hot engine operation. Choose a replacement material that can handle these temperature extremes without becoming brittle or soft. For instance, flexible fuels lines often use materials like HDPE or PEX, which offer good flexibility and resistance to temperature changes. Avoid materials that may become brittle or crack under extreme conditions.
Chemical Resistance: Fuel lines are exposed to various chemicals, including fuel, engine oil, and coolant. Select a replacement material that exhibits excellent chemical resistance to ensure it doesn't degrade or become permeable over time. Some plastics, like certain grades of PVC and PEX, are known for their ability to resist fuel and oil solvents. Always verify the compatibility of the new material with the fuel and fluids in your vehicle.
Research and Consult Experts: With numerous plastic types and brands available, it's essential to research and consult experts or manufacturers. They can provide specific recommendations based on your vehicle's make and model. Online forums and automotive communities can also offer valuable insights and experiences from other vehicle owners, helping you make an informed decision.
Optimizing Performance: Choosing the Right Fuel Line for Your 2005 Johnson 90 HP
You may want to see also
Cut and Install: Carefully cut and install the new fuel line
Before you begin the installation process, it's crucial to gather the necessary tools and materials. You'll need a new fuel line that is compatible with your vehicle's specifications, a pair of sharp scissors or a utility knife, a fuel line cutter (if required), a fuel line clamp or ferrule, and a fuel line primer and solvent (if needed for a seamless connection). Ensure you have a clean workspace and wear protective gloves to avoid any potential hazards.
Start by locating the old fuel line that needs to be replaced. Carefully inspect the line for any signs of damage, cracks, or leaks. Mark the position of the old line where it connects to the fuel tank and the engine. This will help you align the new line correctly during installation.
Using the sharp scissors or utility knife, carefully cut the new fuel line to the desired length. Measure twice to ensure accuracy, as cutting the line too short can lead to installation issues. Consider the route the fuel line will take and leave enough length to allow for bends and connections. If your vehicle requires a specific type of fuel line cutter, ensure you have the appropriate tool to make a clean cut.
Now, it's time to install the new fuel line. Begin by feeding the line through the designated route, following the path of the old line. Take note of any bends or turns in the line and ensure the new line mimics these paths to avoid strain or damage. Once the line is in place, locate the fuel line clamp or ferrule and secure it tightly around the new line. Make sure the clamp is positioned correctly, providing a snug fit without causing any kinks or bends in the line.
If your vehicle requires a fuel line primer and solvent, apply them according to the manufacturer's instructions. This step ensures a secure and leak-free connection. Prime the connection points and allow the solvent to work as per the product guidelines. Finally, double-check your work by testing the fuel line for any leaks. If everything is secure, your vehicle should now be running smoothly with the new fuel line in place.
Mastering the Art of Fuel Line Maintenance: Removing Connectors with Ease
You may want to see also
Test and Secure: Test for leaks and ensure proper connection and routing
When dealing with a plastic fuel line, it's crucial to test for leaks and ensure that the connections and routing are secure to prevent any potential issues. Here's a step-by-step guide to help you through this process:
Leak Testing: Start by identifying the fuel line sections that need to be tested. Use a soapy water solution as a leak detection method. Mix a few drops of dish soap with water and carefully apply this mixture to the fuel line, focusing on the connections and any potential problem areas. If you notice any bubbles forming on the surface, it indicates a leak. Bubbles signify that fuel is escaping, and you should address this issue immediately. Leaks can lead to fuel wastage, potential engine damage, and safety hazards.
Connection Inspection: Carefully examine all connections along the fuel line. Ensure that each fitting is tight and secure. Over time, connections can loosen due to vibration or temperature changes. Use a wrench or the appropriate tool to check the tightness of each connection. If you find any loose fittings, tighten them securely, ensuring they are snug. Properly secured connections will prevent fuel leaks and maintain the integrity of the fuel system.
Routing Assessment: Evaluate the routing of the fuel line to ensure it is free from any sharp bends or kinks. Plastic fuel lines can be flexible, but excessive bending can lead to cracks or damage over time. Check for any sharp turns or areas where the line might be pinched or compressed. Adjust the routing to create smoother curves, ensuring the line is not subjected to unnecessary stress. Proper routing will not only prevent damage but also allow for easier maintenance and access in the future.
Pressure Testing (Optional): For added assurance, you can perform a pressure test. This method involves using a fuel pressure gauge to measure the pressure in the fuel system. If the pressure drops significantly when the engine is off, it may indicate a leak. However, this test should be conducted by a professional or with specialized equipment to ensure accuracy.
By following these steps, you can effectively test and secure your plastic fuel line, ensuring it functions reliably and safely. Regular maintenance and leak testing are essential to prevent potential issues and maintain the overall health of your vehicle's fuel system.
Mastering Fuel Line Disconnect Pliers: A Comprehensive Guide
You may want to see also
Frequently asked questions
Visual inspection is the first step. Look for any cracks, brittleness, or visible damage along the fuel line. Also, check for any leaks or spills around the fuel line connections. If you notice any issues, it's best to replace the damaged section.
Small cracks can sometimes be temporarily sealed using a fuel line repair kit. These kits typically include a specialized adhesive or sealant that can be applied to the crack. However, for a more permanent solution, it's recommended to replace the entire fuel line to ensure safety and prevent further damage.
Plastic fuel lines can crack due to several factors. Age, exposure to sunlight, and chemicals in fuel can degrade the material over time. Additionally, physical damage from accidents, road debris, or improper installation can also lead to cracks. Regular maintenance and using fuel stabilizers can help prevent such issues.
Replacing a damaged fuel line section involves a few steps. First, locate the damaged area and cut out the affected portion carefully. Ensure you have the correct replacement section with the same specifications. Then, clean the surfaces, apply a suitable primer, and use fuel line connectors or clamps to secure the new section. Always refer to the vehicle's manual for specific instructions.
In emergency situations, you can use a temporary fix like a fuel line plug or a piece of rubber hose to stop the leak. However, this is a short-term solution and should not be considered a permanent repair. It's crucial to address the issue promptly and replace the fuel line to ensure the safety of your vehicle and prevent potential fires.