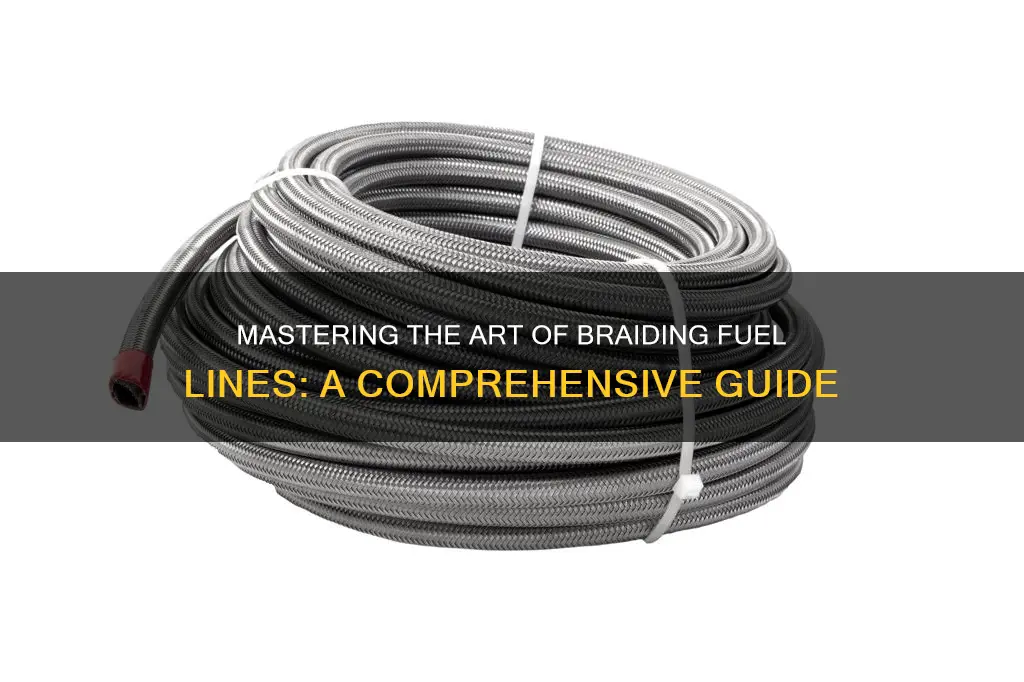
Fabricating a braided fuel line is a crucial process in ensuring the safety and efficiency of fuel delivery systems in vehicles. This method involves creating a flexible and durable fuel line by braiding multiple layers of materials together. The process begins with selecting the appropriate materials, such as high-temperature-resistant fibers, which are then carefully woven or braided to form a strong and lightweight structure. The braided design provides excellent flexibility, making it ideal for routing through tight spaces in engines. Proper fabrication techniques, including precise measurements and secure connections, are essential to prevent fuel leaks and ensure optimal performance. This guide will provide a step-by-step overview of the fabrication process, highlighting the importance of attention to detail and the use of specialized tools to achieve a reliable and long-lasting braided fuel line.
What You'll Learn
- Design Considerations: Determine line length, diameter, and material based on engine requirements
- Braiding Process: Use specialized braiding machine to create a strong, flexible fuel line
- Crimping Technique: Apply pressure to connect fittings securely without damaging the line
- Testing Methods: Perform pressure and leak tests to ensure the line's integrity
- Finishing Steps: Inspect and clean the braided fuel line for final installation
Design Considerations: Determine line length, diameter, and material based on engine requirements
When designing a braided fuel line, several key considerations come into play to ensure optimal performance and longevity. Firstly, the length of the line is a critical factor. It should be carefully calculated based on the specific engine requirements and the layout of the vehicle. The goal is to provide a direct and efficient path for the fuel to travel from the tank to the engine while minimizing unnecessary length, which can lead to increased pressure drop and potential fuel degradation. Measure the distance between the fuel tank and the engine, taking into account any bends, turns, or obstacles along the route. This will help determine the required length of the braided line.
The diameter of the fuel line is another important design aspect. The choice of diameter depends on the engine's fuel flow rate and pressure requirements. A larger diameter line can handle higher volumes of fuel, which is crucial for high-performance engines or those with increased displacement. However, a larger diameter may also result in increased pressure drop, especially over longer distances. On the other hand, a smaller diameter line might be more suitable for applications with lower fuel demands, ensuring efficient fuel delivery without excessive pressure loss. It is essential to consider the engine's specifications and consult the manufacturer's guidelines to select the appropriate diameter that balances performance and efficiency.
Material selection is a critical decision in the design process. Braided fuel lines are typically made from various materials, each offering unique advantages. Common choices include stainless steel, aluminum, or high-temperature plastics. Stainless steel provides excellent durability and corrosion resistance, making it ideal for high-pressure applications. Aluminum offers lightweight properties, reducing overall system weight. High-temperature plastics, such as nylon or polyetheretherketone (PEEK), are suitable for fuel lines that operate at elevated temperatures. The material should be chosen based on the engine's operating conditions, considering factors like temperature range, chemical compatibility with the fuel, and environmental exposure.
In addition to these considerations, it is essential to account for the flexibility and bend radius of the braided line. The line should be flexible enough to navigate through the vehicle's chassis and engine compartment without kinking or causing damage. The bend radius should be sufficient to accommodate the tightest possible turns without compromising the line's integrity. Proper flexibility ensures easy installation and reduces the risk of fuel contamination due to kinking.
Lastly, when determining the design specifications, it is crucial to consider the overall system layout and any potential interference. The braided fuel line should be routed away from heat sources, sharp edges, or moving components that could cause damage or restriction. Proper routing ensures a smooth and efficient fuel delivery system, contributing to the engine's performance and longevity.
Jacob's Fuel Line Break: A Potential Catastrophe Unveiled
You may want to see also
Braiding Process: Use specialized braiding machine to create a strong, flexible fuel line
The braiding process is a crucial step in fabricating a braided fuel line, ensuring it is both strong and flexible. This technique involves using a specialized braiding machine to intertwine multiple strands of material, typically a high-strength synthetic fiber, in a specific pattern. The machine's precision and control are essential to creating a consistent and durable fuel line.
Specialized braiding machines are designed to handle the unique requirements of fuel line production. These machines can accommodate various fiber types and sizes, allowing for customization based on the desired fuel line's performance. The braiding process begins with the selection of the appropriate fibers, considering factors such as strength, flexibility, and resistance to fuel-related chemicals. Once the fibers are prepared, they are fed into the braiding machine, where the magic happens.
The braiding machine's mechanism involves a series of rotating bobbins or cones that guide the fibers. These fibers are then intertwined in a specific pattern, often a braided or tubular structure, depending on the design requirements. The machine's speed and tension control are critical to achieving the desired braid density and tightness. A tighter braid provides increased strength and flexibility, ensuring the fuel line can withstand the rigors of the automotive environment.
During the braiding process, the fibers are twisted and woven together, creating a continuous strand. This strand is then wound onto a spool or core, forming the initial structure of the fuel line. The machine's precision ensures that the braid is uniform and consistent along the entire length of the fuel line. After braiding, the fuel line may undergo additional processes like heat setting or coating to enhance its performance and durability.
Braiding offers several advantages for fuel lines. The resulting structure is highly flexible, allowing for easy routing and installation in tight spaces. Additionally, the braided design provides excellent strength, resisting abrasion and maintaining its integrity even under pressure. This process is particularly useful for fuel lines in high-performance vehicles or those requiring precise fuel delivery, ensuring a reliable and efficient fuel supply.
Understanding the Fuel Line T Connector: A Comprehensive Guide
You may want to see also
Crimping Technique: Apply pressure to connect fittings securely without damaging the line
When it comes to fabricating a braided fuel line, the crimping technique is a crucial step to ensure a secure and reliable connection between fittings. This method involves applying pressure to the fittings to create a tight seal, preventing fuel leaks and ensuring the line's integrity. Here's a detailed guide on how to master this technique:
Start by gathering the necessary tools and materials. You'll need a crimping tool specifically designed for fuel line connections, as well as the appropriate size and type of crimp rings or sleeves. The crimping tool should be capable of exerting the required force to secure the fitting without causing damage to the braided fuel line. Ensure that the crimp rings or sleeves are compatible with the fuel line's diameter and material.
Preparation is key to a successful crimp. Clean the fitting and fuel line thoroughly to remove any dirt, corrosion, or debris. This ensures a tight connection and prevents contaminants from affecting the seal. Use a wire brush or a specialized cleaner to ensure a smooth and clean surface. Take note of the orientation of the fuel line and fitting to ensure proper alignment during the crimping process.
Now, it's time to crimp. Position the fitting onto the fuel line, ensuring it is centered and aligned with the crimp ring or sleeve. Apply the crimping tool, using steady pressure, and move it along the length of the fitting. The goal is to create a uniform and consistent crimp, applying enough force to deform the metal of the fitting and crimp ring without causing any damage to the braided fuel line. The crimp should be tight enough to prevent any movement between the fitting and the line but not so forceful that it distorts the line's shape.
After crimping, inspect the connection. Check for any signs of damage to the fuel line, such as kinks or cuts, and ensure that the fitting is securely attached. A successful crimp will result in a smooth, continuous curve along the length of the fitting, indicating a proper connection. If the crimp is too tight, you may need to carefully adjust the pressure and try again.
Practice and precision are essential when mastering the crimping technique. It requires a steady hand and an understanding of the required force to achieve a secure connection without compromising the fuel line's integrity. With time and experience, you'll develop a feel for the right amount of pressure needed for each specific fitting and fuel line combination.
Troubleshooting: Ford Explorer Fuel Pump Issues and Fuel Line Removal
You may want to see also
Testing Methods: Perform pressure and leak tests to ensure the line's integrity
When it comes to ensuring the integrity of a braided fuel line, pressure and leak tests are essential components of the testing process. These tests are designed to verify the line's ability to withstand various operating conditions and to identify any potential weaknesses or defects. Here's a detailed breakdown of the testing methods:
Pressure Testing:
Pressure testing is a critical step to assess the fuel line's ability to handle different pressure levels. This test involves applying a controlled amount of pressure to the line and monitoring its response. The process typically starts with filling the fuel line with a suitable fluid, such as water or a specialized test fluid, to a predetermined pressure. The line is then clamped or secured in place to ensure it remains stable during the test. As the pressure is gradually increased, the braided fuel line should maintain its structural integrity without showing any signs of distortion, cracking, or failure. The test should be conducted at various pressure levels to simulate different operating scenarios. For example, starting with a low pressure and gradually increasing it to the maximum expected pressure in the system. This method helps identify any potential weaknesses in the braided structure, such as areas where the fibers might bunch up or separate, which could lead to reduced pressure resistance.
Leak Testing:
Leak testing is an equally important procedure to ensure the fuel line's tightness and prevent fuel leakage. This test involves applying a vacuum or pressure to the fuel line and observing for any signs of leakage. The process begins by connecting the fuel line to the test equipment, which can include a vacuum pump or a pressure gauge. The line is then subjected to a controlled vacuum or pressure, and the system is monitored for any leaks. A common method is the use of a soap solution or a specialized dye to detect leaks. If a leak is detected, it indicates a potential issue with the fabrication process, such as improper sealing, damaged insulation, or faulty connections. The leak test should be conducted at different points along the fuel line to ensure comprehensive coverage. This includes testing at the connections, bends, and any fittings to identify any weak points that might allow fuel to escape.
Combined Pressure and Leak Testing:
In some cases, it is beneficial to perform both pressure and leak tests simultaneously to gain a more comprehensive understanding of the fuel line's performance. This combined approach allows for a more efficient testing process, especially when multiple fuel lines or components are involved. By applying pressure and monitoring for leaks at the same time, any issues related to pressure resistance and sealing can be identified and addressed. This method is particularly useful in complex fuel systems where multiple components are interconnected.
Test Results and Analysis:
After completing the pressure and leak tests, a thorough analysis of the results is necessary. This involves documenting the pressure levels and vacuum/pressure differentials used during the tests, along with any observed leaks or anomalies. The data should be compared against the expected performance standards and specifications to determine if the braided fuel line meets the required criteria. If any issues are identified, the fabrication process should be reviewed, and necessary adjustments or repairs should be made to ensure the line's integrity.
By following these testing methods, fabricators can ensure that the braided fuel lines are reliable, safe, and capable of withstanding the demands of their intended applications. It is a crucial step in the fabrication process to guarantee the long-term performance and safety of fuel systems.
Signs of a Clogged Fuel Line: What to Look For
You may want to see also
Finishing Steps: Inspect and clean the braided fuel line for final installation
Once you've completed the fabrication process and assembled the braided fuel line, it's crucial to inspect and clean it thoroughly before final installation. This step ensures the fuel line is in optimal condition and ready for use, minimizing the risk of any issues down the line.
Start by examining the braided fuel line for any visible defects or damage. Look for cuts, tears, or any signs of wear and tear that could compromise its integrity. Inspect the braiding pattern for any inconsistencies or areas where the strands may be loose or misaligned. Pay close attention to the connections and fittings, ensuring they are securely attached and free from any debris or contaminants.
Cleaning the fuel line is an essential part of the process. Use a mild detergent or a specialized fuel line cleaner to remove any dirt, grease, or oil residue that may have accumulated during fabrication. Apply the cleaner generously along the length of the line, ensuring it reaches all areas, including the connections and fittings. Allow sufficient time for the cleaner to work its way through the material, breaking down any stubborn deposits.
After cleaning, rinse the fuel line thoroughly with water to remove any remaining detergent and contaminants. Ensure that all traces of cleaner are washed away, as any residue could attract dirt and debris over time. Use a gentle stream of water to avoid causing any damage to the braided structure.
Finally, inspect the fuel line once more to ensure it is free from any contaminants and appears clean and ready for installation. This meticulous approach to finishing the braided fuel line will contribute to its longevity and performance, ensuring a reliable fuel supply for your vehicle.
John Deere LX255 Fuel Line Location: A Comprehensive Guide
You may want to see also
Frequently asked questions
Fabricating a braided fuel line involves several steps. First, you need to measure and cut the fuel line to the desired length, ensuring it's long enough to accommodate the necessary connections and allow for some extra length. Then, you'll need to prepare the ends by deburring and cleaning them to ensure a smooth connection. The next step is to insert the fuel line into the braided sleeve, which is typically made of a flexible material like rubber or plastic. The sleeve is then heat-shrunk or crimped onto the line to secure it in place. Finally, you'll need to connect the braided fuel line to the fuel source and the engine, following the manufacturer's instructions for proper installation.
To achieve a secure connection, it's crucial to use the appropriate fittings and connectors designed for braided fuel lines. These fittings should be made of compatible materials to prevent any damage or degradation over time. When connecting the line, ensure a tight fit by using the right amount of force, but be careful not to over-tighten, as it may damage the line. It's also essential to inspect the connections regularly for any signs of wear or damage, especially in areas with high vibration or temperature fluctuations.
Yes, you can reuse the braided fuel line after removing it from the vehicle, but it's essential to inspect it for any signs of damage or wear. Check for cracks, brittleness, or any signs of fuel degradation. If the line appears to be in good condition, you can clean and lubricate the connections to ensure a proper seal. However, if the line shows significant signs of damage, it's best to replace it to avoid potential fuel leaks and ensure optimal engine performance.