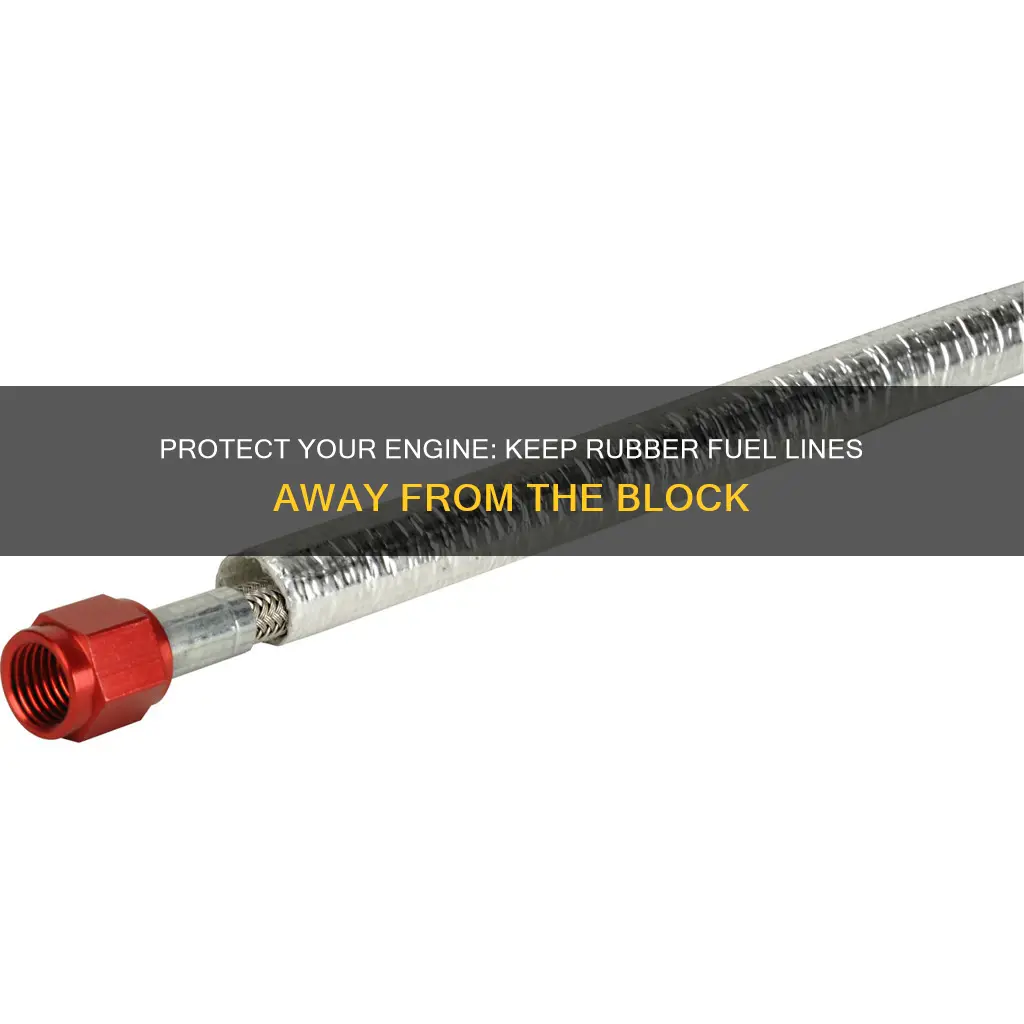
When working on a vehicle's fuel system, it's crucial to understand how to protect rubber fuel lines from potential damage, especially when they are in close proximity to the engine block. Rubber fuel lines are susceptible to heat and mechanical stress, which can lead to cracking, brittleness, and eventual failure. This guide will explore essential techniques and best practices to ensure the longevity and reliability of your fuel system by keeping the rubber fuel lines away from the engine block. By implementing these strategies, you can prevent costly repairs and ensure your vehicle's fuel system operates efficiently and safely.
What You'll Learn
- Insulation: Wrap rubber fuel lines with heat-resistant insulation to protect from engine block heat
- Clamps: Secure lines with tight, corrosion-resistant clamps to prevent leaks and damage
- Routing: Route lines away from engine block, using flexible hoses and brackets for support
- Coating: Apply a protective coating to lines to prevent abrasion and chemical damage
- Regular Inspection: Check lines for cracks, leaks, and damage, replacing as needed
Insulation: Wrap rubber fuel lines with heat-resistant insulation to protect from engine block heat
Insulating rubber fuel lines is a crucial step to prevent damage to your engine block and ensure the longevity of your vehicle's fuel system. When rubber fuel lines are exposed to the high temperatures generated by the engine, they can degrade over time, leading to cracks, leaks, and potential fuel contamination. Here's a detailed guide on how to effectively insulate these lines:
Materials Needed:
- Heat-resistant insulation tape or sleeves: Look for materials specifically designed for high-temperature applications, such as those used in automotive engine bay insulation. These can be made from materials like fiberglass, ceramic, or specialized synthetic fibers.
- Electrical tape (optional): Standard electrical tape can be used as a temporary solution, but it may not provide the same level of heat resistance as dedicated insulation.
- Utility knife or wire cutters.
- Clean cloth or rag.
Insulation Process:
- Inspect the Fuel Lines: Before beginning, carefully examine the rubber fuel lines for any existing damage or wear. Identify the sections that are most susceptible to heat exposure, typically those running alongside the engine block or near exhaust components.
- Clean the Lines: Ensure the fuel lines are clean and free of any debris or contaminants. A clean surface is essential for proper insulation adhesion. Use a clean cloth to wipe down the lines, removing any dirt or old insulation residue.
- Measure and Cut Insulation: Measure the length of the fuel lines that require insulation. Cut the heat-resistant insulation tape or sleeves to the appropriate length, allowing for a slight overlap to ensure a secure fit.
- Apply Insulation: Start at one end of the fuel line and carefully wrap the insulation around the line, ensuring complete coverage. Use the utility knife to trim any excess insulation as you go. Maintain tension to prevent wrinkles, and ensure the insulation is snug against the line. For a more professional finish, consider using insulation sleeves, which provide a smooth and continuous barrier.
- Secure and Protect: Once the insulation is applied, secure it in place using electrical tape or small clips, especially if the line is subject to movement. This extra step ensures the insulation stays in place, even under engine vibrations.
- Regular Maintenance: Insulation should be checked periodically, especially after any engine repairs or modifications. Reapply insulation if necessary, especially if the original insulation has deteriorated over time.
By following these steps, you can effectively protect your rubber fuel lines from the engine block's heat, reducing the risk of fuel leaks and potential engine damage. Proper insulation is a simple yet essential maintenance task for any vehicle owner.
Is the SSF Fuel Station Online? A Comprehensive Guide
You may want to see also
Clamps: Secure lines with tight, corrosion-resistant clamps to prevent leaks and damage
When it comes to maintaining a rubber fuel line, one of the most critical aspects is ensuring it remains securely in place and away from the engine block. This is crucial to prevent potential leaks, damage to the fuel line, and even more severe issues like engine overheating. One of the most effective methods to achieve this is by using the right type of clamps.
Clamps play a vital role in securing the fuel line to the frame or other structural components of the vehicle. They should be tight enough to hold the line in place without causing any damage or restricting its flexibility. The key is to find the perfect balance between a secure grip and allowing the line to move freely, especially when the vehicle is in motion. Over-tightening can lead to cracking or permanent deformation of the fuel line, while under-tightening can result in leaks and potential engine issues.
Corrosion-resistant clamps are essential for long-term reliability. Rubber fuel lines are susceptible to degradation over time due to exposure to fuel, heat, and other environmental factors. Clamps made from materials like stainless steel or brass with a protective coating can withstand these conditions, ensuring the fuel line remains secure and in optimal condition. This is particularly important in areas with harsh weather conditions or high humidity, where corrosion can accelerate.
When installing the clamps, it's important to follow a systematic approach. Start by cleaning the surface where the clamp will be attached to ensure a firm grip. Then, position the clamp securely around the fuel line, ensuring it is centered and aligned properly. Tighten the clamp using a wrench or a suitable tool, being careful not to overtighten. Regularly inspect the clamps for any signs of wear or damage, especially after periods of heavy use or extreme weather, and replace them if necessary.
In summary, using tight, corrosion-resistant clamps is a simple yet effective way to keep the rubber fuel line away from the engine block. This practice helps prevent leaks, maintains the integrity of the fuel system, and ensures the overall longevity of the vehicle's engine. By following these guidelines, vehicle owners can ensure their fuel lines remain in optimal condition, contributing to a more reliable and efficient vehicle performance.
Fuel Line Clogged? Fix Your Lawn Mower's Performance with These Steps
You may want to see also
Routing: Route lines away from engine block, using flexible hoses and brackets for support
When it comes to maintaining your vehicle's fuel system, proper routing of the rubber fuel line is crucial to prevent damage and ensure optimal performance. One of the key aspects of this process is keeping the fuel line away from the engine block, as direct contact can lead to potential issues. Here's a detailed guide on how to achieve this:
Routing the fuel line correctly is essential for several reasons. Firstly, it helps to prevent the line from being damaged by the engine's moving parts, which could lead to fuel leaks and potential engine issues. Secondly, it ensures that the fuel line maintains a safe distance from heat sources, such as exhaust manifolds or engine components, which can cause the rubber to degrade over time. By keeping the fuel line away from these areas, you can extend its lifespan and maintain the integrity of your fuel system.
To achieve this, start by carefully examining the existing routing of the fuel line. Identify any areas where it is too close to the engine block or other critical components. Once you've located these problem areas, it's time to implement some practical solutions. One effective method is to use flexible hoses and brackets for support. Flexible hoses allow for slight movement and adjustability, ensuring that the fuel line can accommodate the engine's vibrations without being pulled or stretched. These hoses are designed to bend and flex, providing a buffer between the fuel line and the engine block.
When installing the flexible hoses, ensure they are securely attached to the fuel line and the surrounding components. Use brackets or ties to keep the hoses in place, preventing them from moving or coming loose over time. Brackets provide a sturdy support system, holding the hoses in the desired position and maintaining the required distance from the engine block. It's important to route the hoses in a way that allows for easy access during maintenance and inspections.
Additionally, consider the use of protective sleeves or covers for the fuel line. These can be made of rubber or other durable materials and are designed to shield the line from potential impacts or abrasions. By adding these protective measures, you create an extra layer of defense against damage, especially in areas where the fuel line might come into contact with other components. Remember, the goal is to create a safe and efficient routing system that prioritizes the longevity of your fuel line and the overall performance of your vehicle.
Fuel Line Cleaning: Essential Tune-Up Component?
You may want to see also
Coating: Apply a protective coating to lines to prevent abrasion and chemical damage
When it comes to maintaining the integrity of your rubber fuel lines and ensuring they don't come into contact with the engine block, one of the most effective methods is to apply a protective coating. This simple yet crucial step can significantly extend the lifespan of your fuel lines and prevent potential damage. Here's a detailed guide on how to go about it:
Choosing the Right Coating: The first step is to select an appropriate protective coating. There are various options available, such as rubber-based coatings, silicone-based coatings, or even specialized fuel line coatings designed for automotive use. Look for coatings that offer excellent abrasion resistance and chemical stability. These properties are essential to ensure that the coating can withstand the harsh environment of your engine compartment, including exposure to fuel, oil, and other chemicals.
Preparation: Before applying the coating, ensure that the fuel lines are clean and free of any debris or old coatings. Use a mild detergent or a specialized cleaner to remove any dirt or grime. Rinse the lines thoroughly to eliminate any residue. This preparation step is crucial to ensure proper adhesion of the new coating. Additionally, inspect the fuel lines for any existing damage or wear. Repair or replace any sections that are beyond repair to ensure a comprehensive protection solution.
Application Process: Start by cutting the coating material to the appropriate length, ensuring it covers the entire length of the fuel line. Then, carefully wrap the coated material around the fuel line, ensuring complete coverage. Use a light hand to press the coating firmly against the line, creating a snug fit. For a more secure hold, you can use a small amount of adhesive or a specialized bonding agent, following the manufacturer's instructions. This step is vital to ensure the coating stays in place and provides effective protection.
Benefits of Coating: Applying a protective coating offers multiple advantages. Firstly, it acts as a barrier, preventing direct contact between the fuel lines and the engine block, which can cause damage over time. This is especially important in areas where the lines are close to moving parts or heat sources. Secondly, the coating provides abrasion resistance, protecting the lines from wear and tear caused by friction against other components. Lastly, it safeguards against chemical damage, ensuring that the fuel lines remain intact even when exposed to various engine fluids.
By following these steps and taking the time to properly coat your rubber fuel lines, you can significantly reduce the risk of damage and ensure the long-term reliability of your fuel system. This simple maintenance task can save you from potential headaches and costly repairs in the future.
YZ 78 Fuel Line: Choosing the Right Size for Optimal Performance
You may want to see also
Regular Inspection: Check lines for cracks, leaks, and damage, replacing as needed
Regular inspections are crucial for maintaining the health and longevity of your rubber fuel lines, especially when it comes to preventing them from coming into contact with the engine block. Here's a detailed guide on how to conduct these inspections and ensure your fuel lines remain in optimal condition:
Visual Inspection: Start by visually examining the fuel lines for any signs of wear and tear. Look for cracks, brittleness, or any visible damage along the length of the line. Rubber can degrade over time due to various factors, including heat, sunlight, and chemical exposure. Inspect areas where the lines connect to the fuel tank, pump, and injectors for any signs of deterioration. Even small cracks can lead to fuel leaks, which can cause engine misfires and other performance issues.
Leak Detection: A simple yet effective method to check for leaks is to spray a small amount of soapy water or a leak detection fluid along the length of the fuel line. If you notice any bubbles forming, it indicates a potential leak. Leaks can occur at connections, fittings, or where the lines are routed near hot engine components. Addressing these leaks promptly is essential to prevent fuel from contaminating the engine oil and causing internal engine damage.
Pressure Testing: Consider using a fuel line pressure tester to check the integrity of the lines. This test can help identify weak spots or areas of potential failure. Connect the tester to the fuel line and apply pressure to simulate real-world conditions. If the pressure drops or the line fails the test, it may indicate internal damage or a compromised seal.
Routing and Support: During your inspection, pay attention to how the fuel lines are routed. Ensure they are not rubbing against the engine block or other hard surfaces, as this can cause wear and damage over time. Properly secure the lines with clips or ties to maintain their position and prevent accidental damage.
Replacement and Maintenance: If you notice any cracks, leaks, or significant wear during your inspections, it's best to replace the affected fuel lines promptly. Keep a record of the mileage and condition of the lines to ensure timely replacements. Regular maintenance and inspections will help you identify issues early on, preventing potential engine damage and costly repairs.
Brake Fluid: A Potential Fuel Line Enemy?
You may want to see also
Frequently asked questions
Rubber fuel lines can be susceptible to heat damage from the engine block, which can lead to cracks, leaks, and potential fuel system failures. Prolonged exposure to high temperatures can cause the rubber to degrade, reducing its flexibility and sealing properties.
If the fuel line is in direct contact with the hot engine block, it can result in rapid heating of the rubber material. This can cause the fuel line to become brittle and potentially crack, leading to fuel leaks. In severe cases, the fuel line may even melt or deform, causing significant damage to the fuel system and potentially leading to engine misfires or stalls.
To prevent the fuel line from coming into contact with the engine block, it is essential to follow proper installation procedures. Use appropriate insulation materials, such as heat-resistant sleeves or protective tubing, to cover the fuel line where it passes near the engine block. Ensure that the fuel line is securely fastened and does not rub against any moving parts. Regularly inspect the fuel line for any signs of damage or wear, especially in areas where it is in close proximity to the engine block, and replace it if necessary.