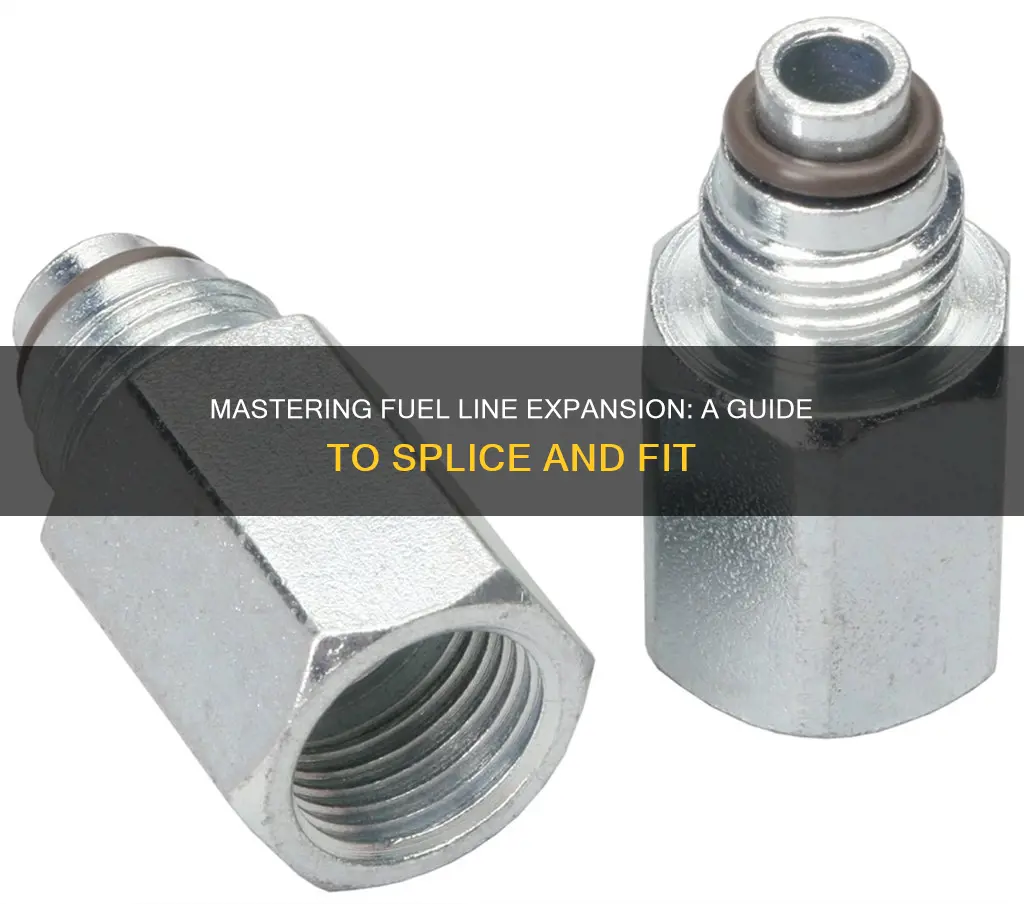
Expanding a fuel line to fit a splice can be a challenging task, but with the right tools and techniques, it can be accomplished efficiently. This process involves carefully measuring and cutting the fuel line to the desired length, then using a special tool to expand the end of the line to create a secure connection for the splice. It's crucial to ensure a tight fit to prevent any fuel leaks, so taking the time to prepare the line properly and using high-quality materials is essential. Understanding the specific requirements of your fuel system and following a step-by-step guide will help you achieve a successful and safe expansion.
What You'll Learn
- Fuel Line Materials: Choose compatible materials for expansion and splicing
- Line Cleaning: Ensure the fuel line is clean and free of debris
- Splicing Techniques: Employ various methods like crimping, soldering, or welding
- Pressure Testing: Test the expanded line for leaks and pressure integrity
- Safety Precautions: Wear protective gear and follow safety protocols during the process
Fuel Line Materials: Choose compatible materials for expansion and splicing
When expanding a fuel line to accommodate a splice, it is crucial to select materials that are compatible with the fuel type and the existing system. The primary goal is to ensure the new connection is robust, leak-free, and safe. Here's a detailed guide on choosing the right materials for this task:
- Understanding Compatibility: Different fuels have unique chemical compositions, and some materials may react with or degrade over time when exposed to certain fuels. For instance, rubber hoses might not be suitable for fuel lines carrying gasoline due to the solvent-like properties of this fuel, which can cause the hose to deteriorate over time. Similarly, certain plastics may not withstand the heat generated by diesel engines. Always refer to the fuel manufacturer's guidelines and the material's data sheets to ensure compatibility.
- Hose and Tube Materials: The most common materials for fuel lines are rubber, vinyl, and various types of synthetic rubber compounds. For example, natural rubber is often used for its flexibility and resistance to fuel degradation. However, for high-temperature applications, such as those involving diesel, a synthetic rubber like butyl or neoprene might be more appropriate. These materials offer improved heat resistance and longevity. Additionally, consider the wall thickness of the hose or tube; thicker walls provide better flexibility and durability, especially when the line needs to expand and contract with temperature changes.
- Fittings and Connectors: The choice of fittings and connectors should complement the chosen hose or tube material. Metal fittings, such as those made from brass or stainless steel, are commonly used for their strength and corrosion resistance. These materials can withstand the pressure and temperature fluctuations in a fuel system. However, for a splice, you might opt for quick-connect fittings, which are easier to install and provide a secure, leak-free connection without the need for extensive welding or crimping.
- Adhesives and Sealants: When splicing two fuel lines together, an adhesive or sealant is essential to ensure a tight, leak-free bond. For rubber hoses, a fuel-resistant adhesive is ideal, as it will not degrade when exposed to the fuel. Silicone-based sealants are also excellent choices, as they offer flexibility and can accommodate minor movements within the splice. Always test the adhesive or sealant in a controlled environment before applying it to the fuel line to ensure it meets the required specifications.
- Safety Considerations: Always prioritize safety when working with fuel lines. Ensure that all materials used are approved for fuel applications and comply with relevant industry standards. Avoid using materials that may compromise the integrity of the fuel system, as this could lead to dangerous leaks or system failures. Regularly inspect the expanded and spliced fuel lines for any signs of damage or wear, especially in areas where the lines are under stress or exposed to harsh conditions.
Mastering the Art of Two-Line Fuel System Conversion: A Comprehensive Guide
You may want to see also
Line Cleaning: Ensure the fuel line is clean and free of debris
When preparing to expand a fuel line to accommodate a splice, it's crucial to prioritize line cleaning as a fundamental step. This process ensures that the fuel line is free from any debris, contaminants, or obstructions that could compromise the integrity of the connection. Start by identifying the section of the fuel line that requires the splice. Inspect the line for any visible signs of damage, corrosion, or blockages. If you notice any issues, address them before proceeding with the expansion.
The cleaning process begins with removing the fuel line from the vehicle's fuel system. This step requires careful handling to avoid any damage to the line. Use a suitable cleaning agent recommended for fuel lines. Common choices include fuel line cleaners, which are typically applied directly to the line and left to work for a specified duration. These cleaners dissolve and remove any accumulated contaminants. Alternatively, you can use a compressed air or nitrogen gun to blow out any debris from the line. Ensure that the cleaning process is thorough, as even small particles can affect the performance of the splice.
After cleaning, it's essential to rinse the fuel line to remove any residual cleaning agents. Use a clear, clean solvent to flush the line, ensuring that no cleaning chemicals remain. Rinsing helps to prevent any potential corrosion or adverse reactions when the line is reinstalled. During the rinsing process, inspect the line for any signs of damage or wear. Replace the line if necessary to ensure optimal performance.
Once the line is clean and rinsed, allow it to dry completely. Moisture can lead to corrosion and other issues, so ensure the line is thoroughly dried. You can use a heat gun or a hairdryer on a low setting to accelerate the drying process. After drying, carefully reattach the fuel line to the vehicle's fuel system, ensuring all connections are secure and properly aligned.
By following these cleaning procedures, you create a clean and healthy environment for the splice, ensuring a reliable and efficient connection. This step is often overlooked but is critical to the success of the expansion and splice, as it prevents potential issues related to contamination and debris.
Fuel Line Removal: A Guide for 1990 Harley Sportster 883 Owners
You may want to see also
Splicing Techniques: Employ various methods like crimping, soldering, or welding
When it comes to expanding a fuel line to accommodate a splice, there are several splicing techniques you can employ to ensure a secure and reliable connection. These methods include crimping, soldering, and welding, each offering unique advantages and applications. Understanding these techniques will enable you to make the right choice for your specific fuel line splicing needs.
Crimping is a popular and relatively simple method for splicing fuel lines. It involves using a specialized tool to apply pressure to the ends of the fuel lines, creating a mechanical connection. This technique is ideal for creating a quick and temporary splice, especially when you need to make adjustments or modifications on-site. Crimping provides a strong and reliable bond, ensuring that the fuel lines remain securely connected. It is a cost-effective solution and can be easily reversed if needed, making it a versatile choice for various fuel line splicing scenarios.
Soldering is another effective splicing technique, offering a more permanent and robust connection. This method involves melting a solder material, typically a metal alloy, onto the fuel line ends to create a joint. Soldering provides an excellent bond due to the chemical reaction between the solder and the fuel line material. It is crucial to use the correct type of solder and flux to ensure a strong and reliable connection. Soldering is particularly useful when dealing with thinner fuel lines or when a more discreet splice is required, as it creates a clean and seamless appearance.
Welding, often associated with heavy-duty applications, can also be employed for splicing fuel lines. This technique involves using a welding torch or similar heat source to melt and fuse the fuel line ends together. Welding provides an incredibly strong and durable connection, making it suitable for high-pressure or high-temperature environments. It offers a permanent solution and ensures that the splice will withstand the rigors of the fuel system. However, welding requires specialized equipment and skills, making it a more advanced splicing method compared to crimping or soldering.
In summary, when expanding a fuel line to fit a splice, you have the option to choose from crimping, soldering, or welding techniques. Each method has its advantages and is suited to different scenarios. Crimping offers a quick and temporary solution, soldering provides a more permanent bond, and welding ensures the strongest and most durable connection. Understanding these splicing techniques will enable you to make an informed decision and ensure a successful and reliable fuel line splice.
Fuel Line Placement: Carb Dirtbike Guide
You may want to see also
Pressure Testing: Test the expanded line for leaks and pressure integrity
Pressure testing is a critical step in ensuring the safety and functionality of any fuel line system, especially when making modifications like expanding a line to fit a splice. This process involves applying pressure to the expanded section of the fuel line to check for any potential leaks or weaknesses in the system. Here's a detailed guide on how to perform this essential test:
Preparation: Before initiating the pressure test, ensure you have the necessary tools and equipment. You'll need a pressure gauge, a source of compressed air or a pump, and a container to collect any potential fuel leaks. It is also advisable to wear protective gear, including gloves and safety goggles, to safeguard against any fuel splashes or spills.
Procedure: Start by securely attaching the pressure gauge to the expanded fuel line section. The gauge should be positioned to measure the pressure at the point where the splice will be made. Gradually increase the pressure in the system using the compressed air or pump, ensuring a steady and controlled rate. As you apply pressure, closely observe the gauge and the fuel line for any signs of leaks. Pay attention to any hissing sounds, which could indicate a leak, or look for any fuel accumulation around the connection points.
Leak Detection: If a leak is detected, it is crucial to identify its source. Carefully inspect the expanded section of the fuel line for any visible damage, cracks, or improper connections. Leaks can occur at the splice site, where the new section is joined to the original line, or at other points along the expanded length. Use a soapy water solution to perform a visual inspection, as soapy bubbles will indicate areas of potential leakage.
Pressure Integrity: Besides leak detection, pressure testing also assesses the overall integrity of the fuel line. The pressure should be maintained at a level that simulates the system's normal operating conditions. For most fuel systems, this typically involves reaching a specific pressure threshold, often recommended by the manufacturer. If the pressure holds steady without any drops, it indicates that the expanded line can withstand the required pressure and is likely to function correctly.
Documentation and Safety: After the pressure test, document the results, including the pressure levels reached and any observations made during the test. This documentation is essential for future reference and can help identify any recurring issues. Always prioritize safety during this process, ensuring that the fuel system is properly secured and that any potential hazards are mitigated.
By following these steps, you can effectively pressure-test the expanded fuel line, ensuring that it is leak-free and capable of withstanding the necessary pressure for safe operation. This process is a vital part of modifying fuel lines and should not be overlooked to maintain the overall integrity of the vehicle's fuel system.
Unveiling the Tvr Tasmin's Fuel Line Mystery: Size Matters!
You may want to see also
Safety Precautions: Wear protective gear and follow safety protocols during the process
When working on expanding a fuel line to accommodate a splice, it is crucial to prioritize safety to prevent accidents and injuries. Here are some essential safety precautions to keep in mind:
Personal Protective Equipment (PPE): Before beginning any work, ensure you are equipped with the necessary PPE. This includes safety goggles or glasses to protect your eyes from potential fuel splashes or debris. Gloves are essential to maintain a secure grip and prevent cuts or burns. Consider wearing a respirator or dust mask if you'll be working in an enclosed space to avoid inhaling harmful fumes. Additionally, a full-face respirator can offer enhanced protection during this process.
Work Environment: Choose a well-ventilated area for your work to minimize the risk of inhaling fuel vapors. If working outdoors, be mindful of the weather conditions. Avoid windy areas to prevent fuel from being blown back into the system. Keep the work area clean and organized to reduce tripping hazards and potential accidents.
Fuel Line Inspection: Before expanding the fuel line, inspect it for any signs of damage, cracks, or corrosion. If you notice any issues, address them promptly to ensure the integrity of the fuel system. It is also crucial to check for any existing splices or connections and ensure they are secure and in good condition.
Safety Protocols: Follow the manufacturer's guidelines and safety protocols specific to your vehicle's fuel system. These protocols often include recommendations for the correct tools and techniques to use. Adhere to the suggested torque specifications for any fasteners to avoid over-tightening, which can lead to damage. Be cautious when using heat sources, such as torch or heat guns, to expand the fuel line, and always maintain a safe distance to prevent burns.
Training and Expertise: If you are not familiar with the process, consider seeking guidance from a professional mechanic or referring to detailed online tutorials. Proper training ensures you understand the potential risks and know how to handle the tools and equipment safely. It is also advisable to work on a level surface to maintain stability and avoid accidents.
Remember, safety should always be the top priority when working on any automotive repairs or modifications. By following these precautions, you can ensure a safer working environment and minimize the risks associated with fuel line expansion and splicing.
Braided Fuel Lines: Insulation Against Vapor Lock Explained
You may want to see also
Frequently asked questions
To ensure a proper fit, measure the existing fuel line and the desired length for expansion. Consider the diameter and material of the original line, as these factors influence the new size. Typically, a slight increase in diameter is recommended for a splice, allowing for a secure connection.
Expanding a fuel line requires a few essential tools. You'll need a fuel line expander, which comes in various sizes to match different diameters. Additionally, have a fuel line cutter, a hose clamp, and a cleaning solution ready for preparation.
Yes, splice kits are designed for this purpose. These kits include the necessary components to create a secure connection. They often consist of a sleeve, a ferrule, and a crimping tool. By following the manufacturer's instructions, you can ensure a reliable splice.