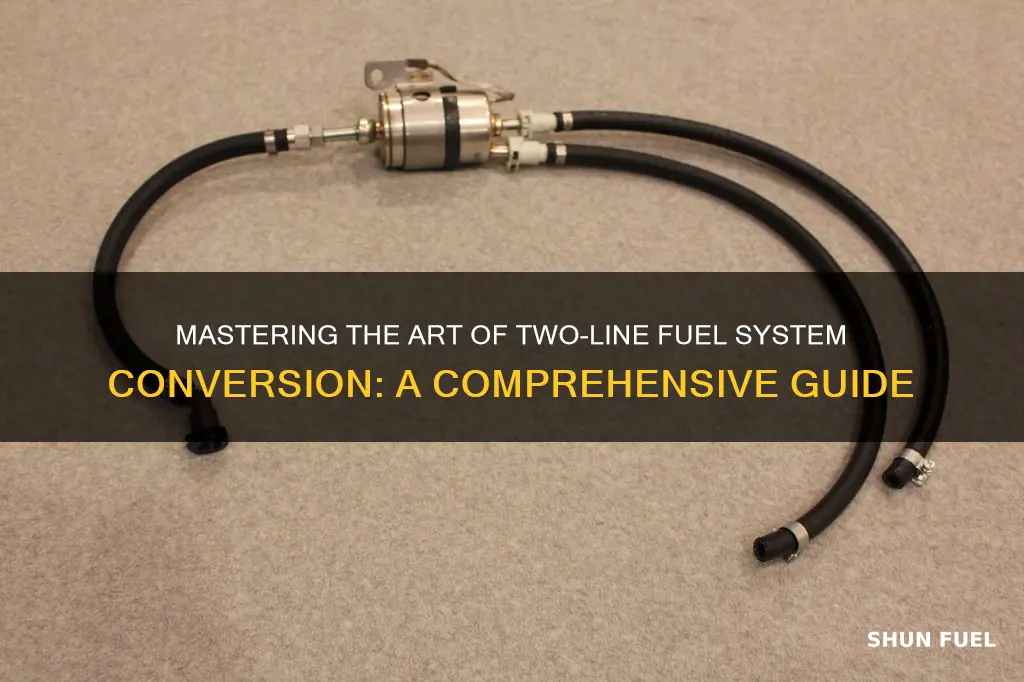
Converting a two-line fuel system is a process that involves transforming the fuel delivery mechanism in an engine or vehicle. This conversion is often necessary to improve fuel efficiency, enhance performance, or adapt to specific engine requirements. The process typically includes replacing the existing fuel lines with new, compatible lines, ensuring proper fuel pressure regulation, and optimizing the fuel injection system for optimal combustion. This guide will provide a step-by-step approach to successfully converting a two-line fuel system, covering essential considerations and techniques to ensure a smooth and efficient transition.
What You'll Learn
- Fuel Injector Removal: Carefully remove the fuel injectors from the engine block
- Line Routing: Plan and route the new lines to ensure proper placement
- Fittings and Adapters: Select appropriate fittings and adapters for a secure connection
- Fuel Pump Installation: Install the fuel pump and ensure it functions correctly
- Testing and Verification: Thoroughly test the system to ensure proper fuel flow and pressure
Fuel Injector Removal: Carefully remove the fuel injectors from the engine block
Fuel injector removal is a crucial step in converting a two-line fuel system, and it requires precision and care to ensure the process is done correctly. Here's a detailed guide on how to carefully extract the fuel injectors from the engine block:
Preparation: Before you begin, ensure you have the necessary tools, including a fuel pressure gauge, a set of socket wrenches or fuel injector pullers, and a clean workspace. It is essential to release any fuel pressure in the system to prevent accidents. Locate the fuel pressure regulator and disconnect the fuel lines, allowing the pressure to bleed off. This step is critical to avoid damage to the fuel injectors and the engine during removal.
Accessing the Injectors: Identify the fuel injectors you intend to remove. These are typically located near the engine's intake manifold or directly in the cylinder head. Carefully inspect the wiring harnesses and fuel lines connected to each injector. Take note of the positions and connections to ensure an accurate reinstallation later. You might need to remove some engine components or panels to gain full access to the injectors, so have the appropriate tools ready for this step.
Removing the Injectors: Start by loosening the mounting bolts or clips that secure the fuel injectors to the engine block. Use the appropriate socket or fuel injector puller to carefully extract each injector. Some injectors may have a retaining clip or pin that needs to be released before they can be pulled out. Take your time with this process, as forcing the injectors can damage them. Once removed, inspect each injector for any signs of damage or wear, especially the spray tips, which are delicate components.
Handling Delicate Components: When removing the fuel injectors, be mindful of the small parts that can easily fall out. You might need to use a magnifying glass or a small brush to clean any debris or contaminants from the injector body and spray tips. Ensure that no foreign objects enter the injector during removal. Properly store any removed components, preferably in a clean, dry environment, to prevent contamination.
Post-Removal Checks: After successfully removing all the fuel injectors, double-check the engine block for any signs of damage or excessive wear. Clean the engine block's surface where the injectors were mounted to ensure a smooth installation of the new system. This careful approach to fuel injector removal is essential to guarantee a successful conversion and maintain the engine's performance.
Mastering Quick Connect Fuel Lines: A Comprehensive Guide
You may want to see also
Line Routing: Plan and route the new lines to ensure proper placement
When converting a two-line fuel system, proper line routing is crucial to ensure optimal performance and safety. Here's a detailed guide on how to plan and route the new lines effectively:
- Understand the System: Begin by thoroughly understanding the existing two-line fuel system. Identify the locations of the fuel tanks, pumps, injectors, and any other relevant components. Familiarize yourself with the system's layout, including the lengths and angles of the lines. This knowledge will be essential for making informed decisions during the conversion process.
- Assess Space and Route Constraints: Evaluate the available space within the engine bay and surrounding areas. Consider the placement of other components, such as the engine, transmission, and existing wiring harnesses. Determine the optimal routes for the new lines, ensuring they have sufficient clearance and do not interfere with other parts. Proper spacing will prevent damage and ensure easy access for maintenance.
- Plan Line Lengths and Angles: Calculate the required lengths of the new lines based on the system's design and your measurements. Accurate calculations will ensure that the lines are neither too short nor too long. Additionally, consider the angles at which the lines need to be routed. This might involve creating bends or using specific fittings to achieve the desired orientation.
- Use Appropriate Fittings and Supports: Select the right fittings, such as elbows, tees, and unions, to connect the lines. Ensure these fittings are compatible with the fuel system's materials and pressure requirements. Implement proper line supports to prevent sagging or excessive movement. This can be achieved using rubber or plastic line retainers, clips, or brackets. Secure the lines at regular intervals to maintain tension and stability.
- Consider Fuel Flow and Pressure: As you route the lines, keep in mind the direction of fuel flow and pressure differentials. Ensure that the lines are sloped correctly to allow gravity-assisted fuel return when necessary. Avoid sharp bends or kinks that could restrict flow or cause pressure drops. Proper routing will maintain efficient fuel delivery and system performance.
- Document and Verify: Throughout the routing process, document your decisions and measurements. Create a visual representation or diagram of the planned line layout for future reference. Verify the accuracy of your routing by comparing it with the system's design specifications. This documentation will be valuable if any adjustments or troubleshooting are required during or after the conversion.
Fuel Line Swap: Can You Use It for Coolant?
You may want to see also
Fittings and Adapters: Select appropriate fittings and adapters for a secure connection
When converting a two-line fuel system, selecting the right fittings and adapters is crucial for ensuring a secure and efficient connection. Here's a detailed guide on how to approach this task:
Understanding the System: Begin by thoroughly understanding the existing two-line fuel system you're working with. Identify the types of fittings and adapters currently in use, their sizes, and the materials they are made from. This knowledge will help you make informed decisions when choosing replacements or upgrades.
Material Compatibility: Different materials have varying compatibility with fuels and require specific fittings. For instance, aluminum fittings might not be suitable for ethanol-blended fuels due to potential corrosion. Ensure that the new fittings and adapters you select are compatible with the fuel type and any additives present.
Size and Thread Compatibility: Fittings and adapters must match the size and thread of the existing lines to ensure a proper seal and prevent leaks. Check the internal diameter and thread pitch of the lines to find matching fittings. Standardized thread types like NPT (National Pipe Thread) or BSP (British Standard Pipe) are commonly used, so identifying the correct thread type is essential.
Consideration of Pressure and Temperature: The fittings and adapters should be able to withstand the pressure and temperature fluctuations within the fuel system. High-pressure systems, for example, require robust fittings that can handle increased stress without leaking. Similarly, if the fuel system operates at extreme temperatures, choose materials that can endure those conditions without degradation.
High-Quality Fittings: Invest in high-quality fittings and adapters made from durable materials like stainless steel or brass. These materials offer excellent corrosion resistance and longevity, ensuring your fuel system remains reliable over time. Well-made fittings will also provide a tighter seal, minimizing the risk of fuel leaks.
Welding and Bonding: If you need to join two different diameter lines or adapt to a specific fitting, consider welding or bonding techniques. These methods allow for a secure connection between dissimilar materials. However, ensure that you follow proper procedures and use compatible welding rods or adhesives to create a strong and leak-free bond.
By carefully selecting fittings and adapters that match the system's requirements, you can ensure a seamless conversion, maximizing the efficiency and safety of your two-line fuel system.
Nitro Fuel Line Length: Does It Really Matter?
You may want to see also
Fuel Pump Installation: Install the fuel pump and ensure it functions correctly
Fuel pump installation is a crucial step in converting a two-line fuel system, ensuring optimal performance and reliability. Here's a detailed guide on how to install the fuel pump and verify its functionality:
Preparation: Before you begin, ensure you have the necessary tools and components, including the new fuel pump, wiring harnesses, and any required adapters. Familiarize yourself with the vehicle's fuel system layout to identify the appropriate mounting points and connections. It's essential to work in a well-ventilated area and wear protective gear, such as gloves and safety goggles, to prevent any fuel-related hazards.
Installation Process:
- Locate the fuel tank and identify the mounting points for the fuel pump. Typically, it is positioned near the tank's bottom to ensure efficient fuel delivery.
- Carefully lift the fuel tank and set it aside, ensuring it is supported securely.
- Remove the old fuel pump (if applicable) by disconnecting the wiring harness and fuel lines. Take note of the connections to ensure a smooth reinstallation.
- Position the new fuel pump in the designated mounting location. Secure it using the provided mounting hardware, ensuring it is tightly fastened to prevent vibrations during operation.
- Connect the wiring harness to the fuel pump's electrical terminals. Double-check the polarity to avoid any electrical issues.
- Reattach the fuel lines, ensuring a secure and tight connection. Use fuel line connectors or clamps to prevent leaks.
Testing and Functionality Check:
- With the fuel pump installed, it's time to test its operation. Start the vehicle's engine and listen for any unusual noises.
- Check for fuel flow by placing a dipstick in the fuel tank and observing the rate at which the fuel level drops. The pump should deliver fuel efficiently.
- Monitor the engine's performance during this test. The engine should start smoothly and run without any stalling or hesitation, indicating proper fuel delivery.
- If the fuel pump functions correctly, you can proceed with the remaining fuel system conversions, ensuring a seamless integration.
Remember, proper installation and testing are critical to the success of your two-line fuel system conversion. Always refer to the manufacturer's guidelines and seek professional assistance if needed to ensure a safe and efficient fuel system upgrade.
Unleash the Power: NICOPP Lines for Fuel Efficiency
You may want to see also
Testing and Verification: Thoroughly test the system to ensure proper fuel flow and pressure
When converting a two-line fuel system, thorough testing and verification are essential to ensure optimal performance and safety. This process involves a series of steps to validate the system's functionality and identify any potential issues. Here's a detailed guide on how to approach this critical phase:
Fuel Flow Testing: Begin by setting up a test rig that simulates the actual engine environment. This setup should include a fuel pump, pressure gauge, and flow meter to measure the fuel's movement. Start by checking the fuel flow rate at different operating conditions. Gradually increase the engine speed and load to observe how the fuel system responds. The goal is to ensure a consistent and adequate fuel supply to the engine, meeting or exceeding the manufacturer's specifications. Note any deviations in flow rates and pressure drops, as these could indicate potential blockages or restrictions in the fuel lines.
Pressure Regulation: Fuel pressure is another critical aspect of the testing process. Use a pressure gauge to measure the system's pressure at various engine speeds and loads. The pressure should remain stable and within the recommended range to ensure efficient combustion. If the pressure fluctuates or drops significantly, it may indicate issues with the fuel pump, filter, or injectors. Adjustments or replacements might be necessary to restore optimal pressure.
Leakage and Tightness: A comprehensive leak test is vital to identify any potential fuel leaks. Apply a soapy water solution to all fuel lines, connections, and fittings. Observe for any bubbles or foam, indicating a leak. Even small leaks can lead to significant issues over time. Ensure all connections are tight and secure, as loose fittings can cause fuel loss and potential safety hazards.
Engine Performance Evaluation: Once the fuel system is thoroughly tested, it's time to assess its impact on engine performance. Start the engine and monitor its behavior. Check for any unusual noises, vibrations, or changes in idling quality. The engine should respond promptly to throttle inputs, indicating proper fuel-air mixture delivery. Any anomalies during this phase may require further investigation and adjustments.
Documentation and Calibration: Document all test results, including fuel flow rates, pressure readings, and engine performance metrics. This data will be crucial for fine-tuning and calibrating the system. Use this information to adjust fuel injection timing, spray angles, and other parameters to optimize performance. Proper calibration ensures the system operates efficiently and safely.
By following these testing and verification procedures, you can confidently convert a two-line fuel system, knowing that it meets the required standards and will perform reliably in real-world conditions. This meticulous approach is essential to avoid potential issues and ensure a smooth transition during the conversion process.
Fuel Line Proximity to Exhaust: Safety Limits Explained
You may want to see also
Frequently asked questions
A 2-line fuel system is a type of fuel delivery system commonly used in marine and small engine applications. It consists of two separate lines, one for the main fuel supply and another for the return of excess fuel, ensuring efficient and reliable fuel management.
Converting to a 2-line fuel system offers several advantages. It provides better fuel management, reduces the risk of fuel starvation, and improves overall engine performance. This setup is especially beneficial for applications where fuel efficiency and stability are crucial, such as in marine vessels or small aircraft.
The conversion process involves several steps. First, you'll need to purchase the necessary components, including a 2-line fuel filter, a fuel pump, and appropriate fittings. Then, you'll disconnect the existing fuel lines and install the new lines, ensuring proper connections and secure fittings. It is recommended to consult a professional or refer to detailed instructions specific to your engine model.
Yes, there are a few important factors to consider. Ensure that the new fuel pump can handle the required flow rate and pressure for your engine. Proper ventilation of the fuel tank is essential to prevent vacuum issues. Additionally, you might need to adjust the fuel mixture settings on your engine to accommodate the changes in the fuel system. It's always advisable to seek expert advice or consult the manufacturer's guidelines for a successful conversion.