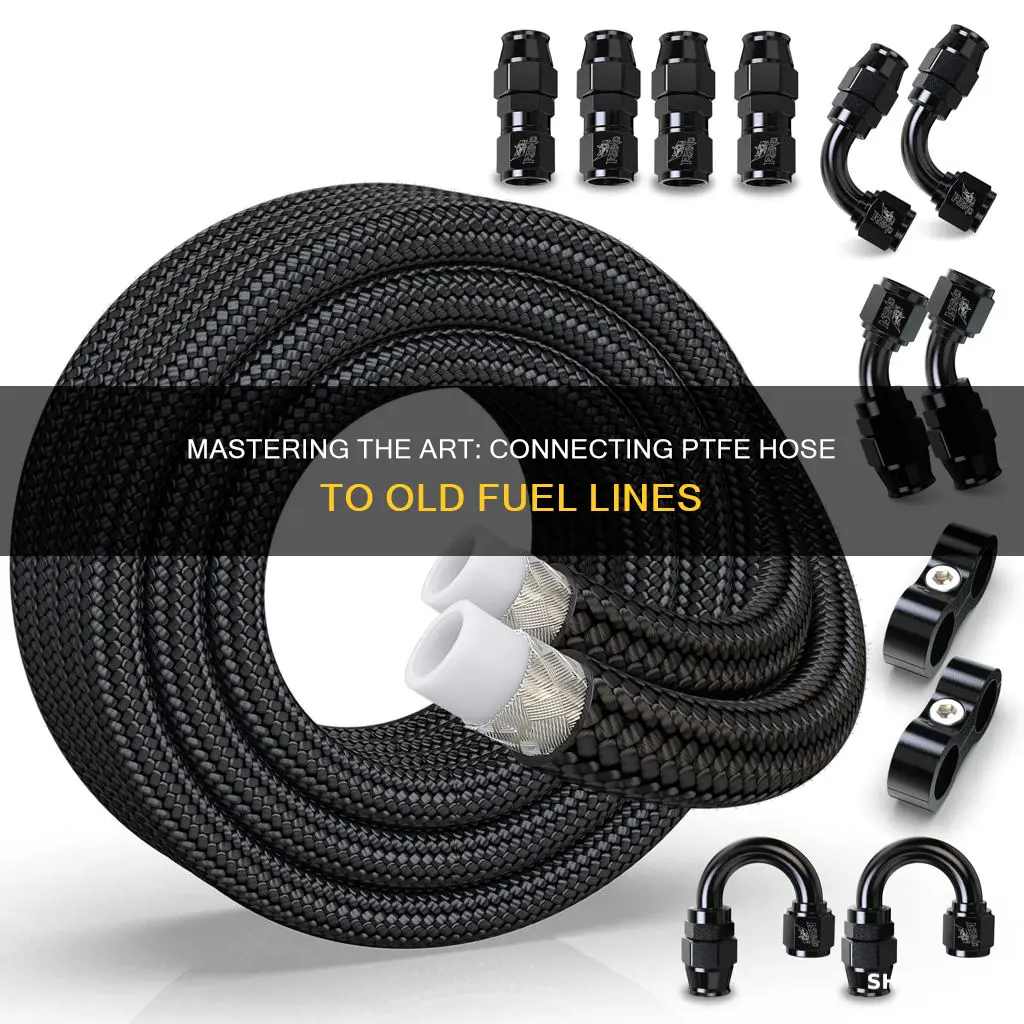
Connecting a PTFE (polytetrafluoroethylene) hose to an old fuel line can be a useful method for retrofitting or upgrading fuel systems in older vehicles. This process involves ensuring a secure and leak-free connection between the two components, which can be challenging due to the age and condition of the existing fuel line. The following steps will guide you through the process, ensuring a reliable and safe fuel delivery system.
What You'll Learn
- Preparation: Clean and inspect both hoses and fuel line for damage
- Fitting Selection: Choose a suitable fitting for a secure connection
- Clamping: Securely clamp the PTFE hose to the fuel line
- Testing: Perform pressure tests to ensure a tight seal
- Maintenance: Regularly inspect and maintain the connection for longevity
Preparation: Clean and inspect both hoses and fuel line for damage
Before attempting to connect the PTFE (polytetrafluoroethylene) hose to the old fuel line, it is crucial to ensure a proper and safe installation. The preparation process involves a thorough inspection and cleaning of both components to guarantee a reliable connection.
Start by removing the old fuel line from the vehicle's system. This step requires careful disassembly to avoid any damage to the surrounding components. Once the old fuel line is removed, inspect it for any signs of wear, cracks, or damage. Look for any areas where the fuel line has been compromised, as these sections will need to be replaced or repaired. Cleaning the fuel line is essential; use a suitable solvent to remove any debris, contaminants, or old fuel residue. Ensure that the fuel line is completely dry before proceeding.
Now, turn your attention to the PTFE hose. Inspect it for any visible defects, such as tears, cracks, or discolored areas. Check for any sharp bends or kinks that might affect its flexibility and durability. If the hose shows any signs of damage, it should be replaced to ensure a secure connection. Cleaning the PTFE hose is also important; use a mild detergent and water solution to remove any dirt or contaminants. Rinse thoroughly and allow the hose to air dry completely.
The inspection and cleaning process is vital to ensure a successful connection. By removing any debris or contaminants, you create a clean surface for the PTFE hose and fuel line to make a secure bond. Additionally, identifying and replacing any damaged components ensures the overall integrity of the fuel system. Take your time during this step, as a thorough inspection will contribute to a more reliable and long-lasting installation.
Fixing a Broken Fuel Line: Can You Trick a Truck?
You may want to see also
Fitting Selection: Choose a suitable fitting for a secure connection
When connecting a PTFE (polytetrafluoroethylene) hose to an old fuel line, selecting the right fitting is crucial for a secure and reliable connection. The goal is to ensure a tight seal that can withstand the pressure and temperature variations associated with fuel systems. Here's a detailed guide on how to choose the appropriate fitting:
Understanding the System: Begin by understanding the existing fuel line setup. Identify the diameter and material of the old fuel line. PTFE hoses typically come in various diameters, so matching the hose's inner diameter to the fuel line's size is essential for a proper fit. Common diameters for fuel lines range from 3/8" to 1/2" in North America, but always check the specific dimensions of your system.
Fitting Types: There are several types of fittings available for connecting hoses to fuel lines. The most common options include barbed fittings, compression fittings, and quick-connect fittings. Each type has its advantages and is suited to different scenarios:
- Barbed Fittings: These are simple and cost-effective but may not provide the tightest seal. They are best for temporary connections or when the fuel line is not under significant pressure.
- Compression Fittings: Compression fittings offer a more secure connection by compressing a ferrule around the fuel line, creating a tight seal. They are durable and suitable for permanent installations.
- Quick-Connect Fittings: As the name suggests, these fittings allow for quick and easy connections and disconnections. They are convenient for frequent access, such as when topping up the fuel tank.
Material Compatibility: Ensure that the chosen fitting is made from a material that is compatible with both the fuel line and the PTFE hose. PTFE is known for its chemical resistance, but it's still important to avoid fittings with metals that might corrode or react with the fuel over time. Stainless steel or brass fittings are often suitable choices.
Pressure and Temperature Considerations: Fuel systems can experience varying temperatures and pressures. Select a fitting that can handle these conditions without compromising the seal. High-pressure fittings or those with reinforced construction might be necessary for high-performance applications.
Installation and Maintenance: Consider the ease of installation and future maintenance. Compression fittings, for example, require careful assembly to ensure a proper seal. Quick-connect fittings offer convenience but may need regular inspection and replacement due to wear.
By carefully selecting the right fitting based on these factors, you can ensure a secure and long-lasting connection between your PTFE hose and the old fuel line, minimizing the risk of leaks and ensuring optimal performance.
Snow Blower Fuel Lines: Size Guide for Optimal Performance
You may want to see also
Clamping: Securely clamp the PTFE hose to the fuel line
When connecting a PTFE (polytetrafluoroethylene) hose to an old fuel line, clamping is a crucial step to ensure a secure and leak-free connection. Here's a detailed guide on how to achieve this:
Choose the Right Clamp: Select a clamp specifically designed for fuel lines and compatible with the diameter of your PTFE hose and the fuel line. Common types include metal or plastic clamping bands. Ensure the clamp has a smooth interior surface to avoid damaging the PTFE hose.
Prepare the Hose and Line: Clean the fuel line and hose thoroughly to remove any dirt, debris, or old fuel residue. This step is essential for a tight seal. Ensure the surfaces are dry before proceeding.
Position the Clamp: Place the chosen clamp over the PTFE hose and fuel line, positioning it where the hose connects to the line. The clamp should be centered and aligned properly.
Secure the Clamp: Tighten the clamp securely by turning it clockwise with a wrench or spanner. Apply firm pressure to ensure a snug fit. Avoid over-tightening, as it can damage the hose or line. The goal is to create a tight seal without causing any damage.
Test for Leaks: After clamping, inspect the connection for any signs of leakage. You can use a soapy water solution and gently apply it around the clamp. If no bubbles appear, the connection is secure. If leaks occur, carefully adjust the clamp and try again.
Remember, proper clamping is vital to the longevity of the connection and the safety of your fuel system. Take your time to ensure a precise fit, and always refer to manufacturer guidelines for specific instructions related to your hose and fuel line materials.
Understanding the Role of AV in Fuel Lines
You may want to see also
Testing: Perform pressure tests to ensure a tight seal
When connecting a PTFE (polytetrafluoroethylene) hose to an old fuel line, it's crucial to ensure a tight and secure seal to prevent any potential leaks. Pressure testing is an essential step in this process, as it allows you to verify the integrity of the connection and identify any potential issues before putting the system into operation. Here's a detailed guide on how to perform these tests:
Preparation: Before initiating the pressure test, ensure that the fuel line and the PTFE hose are properly prepared. Clean both surfaces to remove any dirt, debris, or contaminants that could interfere with the seal. This can be done using a suitable solvent or a mild detergent, ensuring that the surfaces are dry before proceeding.
Test Setup: Securely attach the PTFE hose to the fuel line using the appropriate fittings or clamps. It is essential to use the correct hardware designed for the specific materials to ensure a reliable connection. Set up a pressure gauge or a test gauge system that can measure the pressure within the system. The gauge should be calibrated and capable of reading the expected pressure range.
Pressure Application: Gradually increase the pressure in the system while monitoring the gauge. Start with a low pressure and slowly build up to the recommended operating pressure for the fuel line. This gradual increase allows you to identify any potential issues early on. The pressure should be maintained for a specified duration, typically a few minutes, to ensure a thorough test.
Leak Detection: During and after the pressure application, closely observe the connection for any signs of leakage. Even a small leak can indicate an improper seal. Check for any visible moisture, fuel accumulation, or pressure drops on the gauge. If any leaks are detected, immediately release the pressure and inspect the connection. Tighten or adjust the fittings as necessary to ensure a secure seal.
Documentation: Record the pressure values and any observations during the test. This documentation will help in troubleshooting and ensuring compliance with the system's specifications. It also provides valuable data for future reference, especially if similar connections need to be made.
By following these steps and conducting thorough pressure tests, you can confidently establish a reliable connection between the PTFE hose and the old fuel line, minimizing the risk of fuel leaks and ensuring the safety and efficiency of your fuel system.
Unleash Your Engine's Potential: HP 5-16 Fuel Line Power
You may want to see also
Maintenance: Regularly inspect and maintain the connection for longevity
When it comes to maintaining the connection between a PTFE (polytetrafluoroethylene) hose and an old fuel line, regular inspection and maintenance are crucial to ensure longevity and prevent potential issues. Here's a detailed guide on how to approach this task:
Visual Inspection: Begin by visually examining the connection area. Look for any signs of damage, cracks, or deterioration in both the PTFE hose and the fuel line. Check for any visible wear and tear, especially around the fittings and joints. Over time, fuel lines can develop cracks due to age, heat, or chemical exposure, which may compromise their integrity. Similarly, the PTFE hose should be inspected for any signs of softening, brittleness, or discoloration, as these could indicate material degradation.
Tightness Check: Ensure that the connection is secure and tight. Loosen the fittings slightly and then retighten them by hand. This process helps to ensure that the connection is not too tight, which could lead to damage over time, or too loose, which may result in fuel leaks. Use a wrench or socket to tighten the fittings, but be cautious not to overtighten, as this can cause the hose or fuel line to crack. Regularly checking and tightening the connections will help maintain a reliable seal.
Leak Detection: Perform leak tests to verify the integrity of the connection. After tightening the fittings, apply a small amount of soapy water or a non-toxic leak detection fluid around the connection points. If a leak is present, bubbles will form, indicating the location of the leak. Address any leaks promptly to prevent fuel wastage and potential engine issues. Regular leak checks are essential, especially if the system has been exposed to extreme temperatures or harsh conditions.
Regular Cleaning: Keep the connection area clean and free from debris. Over time, dirt, grime, and fuel contaminants can accumulate, leading to reduced performance and potential blockages. Use a soft brush or cloth to gently clean the area, ensuring that no damage is caused to the hose or fuel line. Regular cleaning will also make it easier to identify any existing issues, allowing for prompt maintenance.
Temperature Considerations: Take note of the operating temperature of your fuel system. Extreme temperatures can affect the performance and longevity of both the PTFE hose and the fuel line. If your vehicle operates in high-temperature environments, consider using a heat shield to protect the connections. Similarly, in cold climates, ensure that the fuel system is properly insulated to prevent freezing. Regularly monitoring and managing temperature-related factors will contribute to the overall maintenance of the connection.
By following these maintenance steps, you can ensure that the connection between the PTFE hose and the old fuel line remains secure, leak-free, and functional over an extended period. Regular inspections and prompt attention to any issues will help extend the lifespan of your fuel system and maintain optimal performance.
Unveiling the Secrets: Corvette Fuel Line Sizing, 1969 Edition
You may want to see also
Frequently asked questions
PTFE hoses are commonly used for fuel line connections due to their excellent chemical resistance and ability to withstand high temperatures. They provide a reliable and durable solution, especially when dealing with older fuel lines that may have degraded over time.
It is generally not recommended to directly connect a PTFE hose to an old fuel line without proper preparation. Old fuel lines might have rust, corrosion, or damage that can compromise the integrity of the connection. It's best to clean and prepare the fuel line before making the connection.
Start by thoroughly cleaning the fuel line to remove any dirt, rust, or debris. You can use a fuel line cleaner or a mixture of vinegar and water. Ensure the line is dry before proceeding. Consider replacing any damaged sections of the fuel line to ensure a secure connection.
You will need a PTFE hose with compatible fittings, a fuel line cleaner or solvent, a cloth or rag for cleaning, and possibly a fuel line repair kit or tape for additional reinforcement. It's essential to use the correct size and type of hose and fittings for a proper seal.
Yes, it's crucial to follow these steps: First, ensure the hose and fuel line are properly aligned. Then, use a suitable adhesive or sealant specifically designed for fuel line connections. Apply the adhesive or sealant according to the manufacturer's instructions, and finally, connect the hose securely, ensuring no gaps or misalignments.