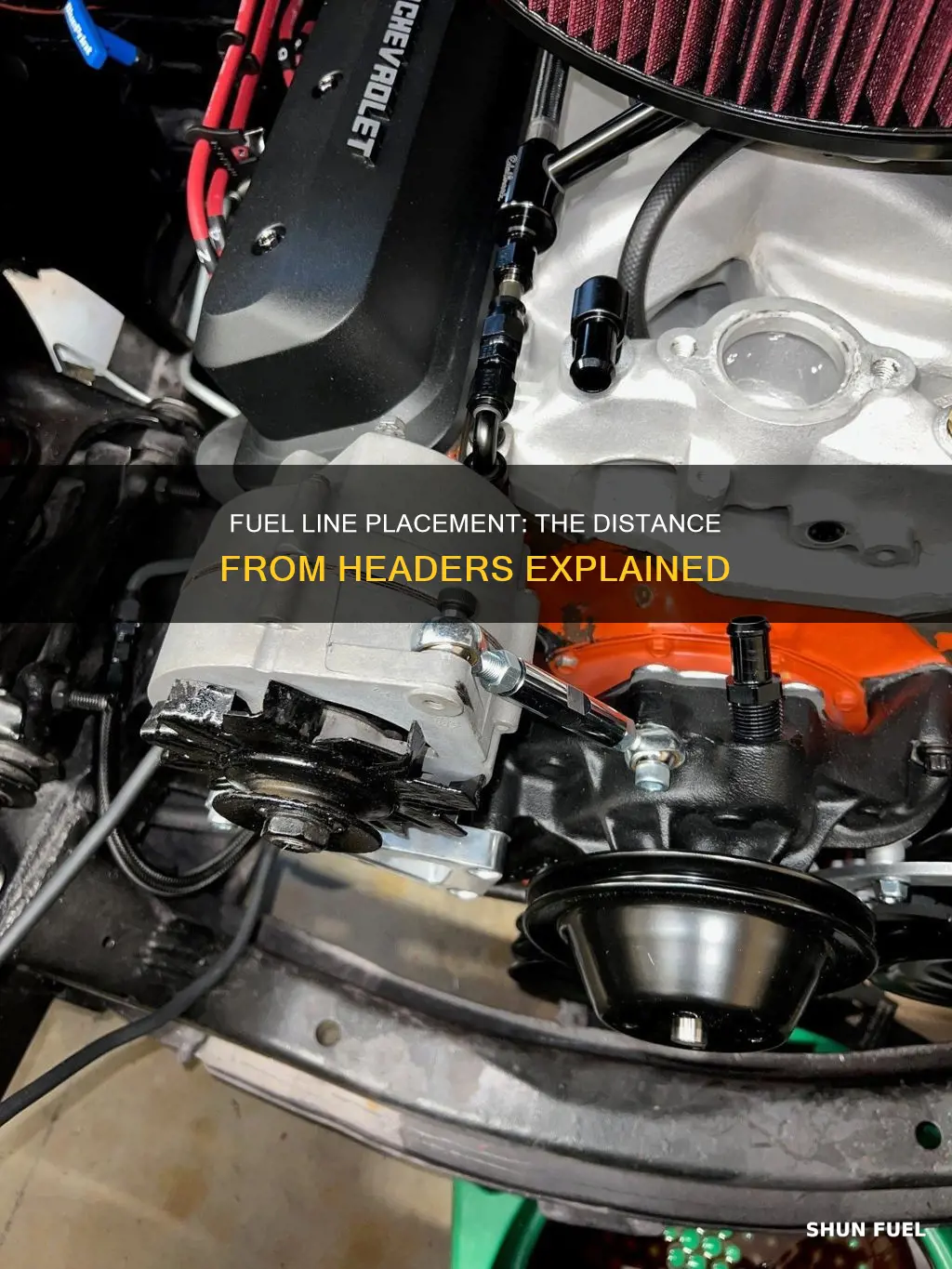
When installing a fuel system in a vehicle, it's crucial to maintain a safe distance between the fuel lines and the headers to prevent potential hazards. The distance required can vary depending on factors such as the type of fuel, the vehicle's design, and local regulations. This guide will explore the recommended spacing to ensure optimal safety and performance, providing valuable insights for mechanics and enthusiasts alike.
Characteristics | Values |
---|---|
Distance from Headers | Typically, fuel lines should be kept at least 2 inches away from the engine's headers to prevent overheating and potential fuel line damage. |
Material Considerations | The material of the fuel line is crucial. Some materials, like aluminum, may require more distance due to their thermal conductivity. |
Engine Type | The specific engine type and its cooling system can influence the required distance. For high-performance engines, a greater distance might be necessary. |
Fuel Line Diameter | Thicker fuel lines might need more space to accommodate the flow rate and ensure proper cooling. |
Environmental Factors | External factors like ambient temperature and engine operating conditions can impact the fuel line placement. |
Safety Regulations | Adhering to local safety regulations and standards is essential to ensure the fuel system's integrity. |
What You'll Learn
- Distance Requirements: Fuel lines must be at least 2 inches away from exhaust headers to prevent overheating and potential fire hazards
- Material Considerations: Choose fuel lines made from heat-resistant materials to ensure durability near the headers
- Clamping Techniques: Proper clamping is crucial to maintain the required distance and prevent fuel line movement
- Routing Strategies: Route fuel lines away from headers, avoiding sharp bends and tight spaces to prevent damage
- Regular Inspections: Inspect fuel lines periodically for wear and tear, especially near the headers, to ensure safety
Distance Requirements: Fuel lines must be at least 2 inches away from exhaust headers to prevent overheating and potential fire hazards
When it comes to vehicle maintenance, ensuring the safety and functionality of your car's fuel system is of utmost importance. One critical aspect often overlooked is the proper spacing between fuel lines and exhaust headers. This seemingly small detail can have significant implications for your vehicle's performance and safety.
The primary concern is the potential for overheating and subsequent fire hazards. Exhaust headers, being in close proximity to the engine, generate intense heat. If fuel lines are not adequately spaced from these headers, the fuel could overheat, leading to potential evaporation and the release of volatile gases. These gases, when ignited, can result in dangerous fires or explosions.
To mitigate this risk, it is essential to maintain a safe distance between the fuel lines and exhaust headers. The recommended distance is a minimum of 2 inches. This spacing ensures that the fuel lines are not exposed to excessive heat, reducing the chances of overheating and potential fire incidents.
Maintaining this distance is a relatively simple task during vehicle assembly or maintenance. It involves careful routing of the fuel lines to avoid close contact with the exhaust headers. Proper insulation and protective measures can also be employed to further safeguard the fuel lines from heat exposure.
In summary, adhering to the 2-inch distance requirement between fuel lines and exhaust headers is a crucial safety measure. It ensures the efficient operation of your vehicle while minimizing the risk of overheating and fire-related accidents. Regular inspection and maintenance of this spacing can contribute to a safer and more reliable driving experience.
E85 Gas: Corrosive or Harmless to Your Fuel System?
You may want to see also
Material Considerations: Choose fuel lines made from heat-resistant materials to ensure durability near the headers
When it comes to installing fuel lines, one of the critical aspects is ensuring they are positioned correctly to avoid potential hazards. Specifically, maintaining a safe distance from the vehicle's headers is essential, as these components can reach extremely high temperatures during operation. This is where material considerations play a vital role in the overall safety and longevity of the fuel system.
The primary goal is to choose fuel lines that can withstand the intense heat generated by the headers. Heat-resistant materials are specifically designed to maintain their structural integrity under high-temperature conditions. These materials are typically made from specialized polymers or synthetic compounds that offer excellent thermal stability. By selecting such materials, you ensure that the fuel lines remain flexible and durable, even when exposed to the intense heat emitted by the vehicle's headers.
Heat-resistant fuel lines are engineered to handle the extreme temperatures that can vary depending on the vehicle's operating conditions. For instance, in high-performance engines, the headers may reach temperatures of over 1000 degrees Fahrenheit. Using standard fuel lines in such an environment would lead to rapid degradation, cracking, or even melting. Therefore, it is crucial to invest in high-quality, heat-resistant lines to ensure the system's reliability and safety.
The choice of material is particularly important in high-performance or racing vehicles, where engine temperatures are often pushed to their limits. In these cases, using heat-resistant fuel lines becomes a necessity rather than a recommendation. These specialized lines are designed to withstand the harsh conditions, ensuring that the fuel remains stable and the system operates efficiently without the risk of fuel line failure or damage to other engine components.
In summary, when dealing with fuel lines near vehicle headers, material selection is a critical factor. Opting for heat-resistant materials ensures that the fuel lines can endure the intense heat, providing a reliable and safe fuel supply to the engine. This consideration is essential for maintaining the overall health and performance of the vehicle, especially in high-performance applications where engine temperatures are a significant concern.
Fixing a Fuel Line Leak: A Step-by-Step Guide
You may want to see also
Clamping Techniques: Proper clamping is crucial to maintain the required distance and prevent fuel line movement
When it comes to fuel line installation, proper clamping techniques are essential to ensure the fuel line maintains the required distance from the headers and operates efficiently without any movement or interference. Clamps play a critical role in securing the fuel line, preventing it from coming into contact with hot engine components, and maintaining the necessary clearance. Here's an overview of the clamping process and its importance:
Clamps are designed to provide a secure and tight fit around the fuel line, holding it in place. The primary goal is to eliminate any potential movement or vibration that could lead to the fuel line touching the headers or other engine parts. Over time, such contact can cause damage to the fuel line and potentially lead to fuel leaks or engine performance issues. Therefore, proper clamping is a preventative measure to ensure the longevity and reliability of the fuel system.
The clamping process involves using specialized fuel line clamps, which are typically made of durable materials like stainless steel or heat-resistant rubber. These clamps are designed to fit snugly around the fuel line, providing a secure hold. It is crucial to choose the right size and type of clamp for the specific fuel line diameter to ensure a proper fit. Clamps that are too loose may not effectively secure the line, while overly tight clamps can restrict flow and cause damage.
To ensure proper clamping, it is recommended to follow these steps: First, identify the correct clamp size by measuring the fuel line's diameter. Then, carefully slide the clamp onto the fuel line, ensuring it covers the entire length where the line needs support. The clamp should be tightened securely but gently to avoid damaging the fuel line. It is essential to check the clamp's position regularly, especially during the initial stages of engine operation, to ensure it remains in place.
In addition to the initial clamping, periodic inspections are vital. Over time, clamps can loosen due to heat, vibration, or fuel line expansion. Regularly checking the clamps and tightening them if necessary will help maintain the required distance between the fuel line and headers. This practice is particularly important in high-performance engines or vehicles operating in extreme conditions.
By employing proper clamping techniques, you can ensure that the fuel line remains at a safe distance from the headers, preventing potential damage and maintaining optimal engine performance. This simple yet critical step in fuel line installation contributes to the overall reliability and efficiency of the vehicle's fuel system.
Transmission Oil vs. Fuel: Exploring the Feasibility of a Swap
You may want to see also
Routing Strategies: Route fuel lines away from headers, avoiding sharp bends and tight spaces to prevent damage
When designing the fuel system for an engine, proper routing of the fuel lines is crucial to ensure optimal performance and longevity. One critical aspect of this routing is keeping the fuel lines away from the engine headers. Headers, also known as exhaust manifolds, are components that direct exhaust gases from the cylinders to the exhaust system. They are typically located close to the engine block and can pose a significant risk to fuel lines if not routed correctly.
The primary concern with placing fuel lines near headers is the potential for damage. Headers operate at high temperatures, and any fuel line that comes into contact with them can be exposed to extreme heat, leading to potential degradation of the fuel line material. Over time, this can result in fuel leaks, which are not only dangerous but can also cause engine misfires and reduced performance. Additionally, the sharp bends and tight spaces around headers can cause mechanical stress on the fuel lines, leading to potential cracks or even ruptures.
To mitigate these risks, it is essential to follow specific routing strategies. Firstly, fuel lines should be routed as far away from the headers as possible. This can be achieved by running the lines along the top of the engine bay, where temperatures are generally lower, or by using longer lines that extend further away from the headers. The goal is to create a safe distance between the fuel lines and the heat source.
Secondly, when routing fuel lines, it is crucial to avoid sharp bends and tight spaces. Fuel lines should be allowed to follow a smooth, gentle curve to reduce the risk of damage. Sharp bends can cause stress concentrations, making the lines more susceptible to cracking or breaking. It is recommended to use flexible fuel lines with a suitable diameter to accommodate the necessary bends without causing excessive strain.
Furthermore, proper support and insulation of the fuel lines can help prevent damage. Using fuel line brackets or clips to secure the lines in place can reduce the risk of movement and potential impact with other engine components. Additionally, applying heat shielding or insulation materials around the fuel lines can provide an extra layer of protection against the high temperatures emitted by the headers.
In summary, routing fuel lines away from headers, avoiding sharp bends, and providing adequate support and insulation are essential strategies to prevent damage and ensure the longevity of the fuel system. By following these guidelines, engine builders and mechanics can create a robust and reliable fuel system that meets the demands of the engine's performance while maintaining safety.
Brake Flush: Choosing the Right Fuel Line Size
You may want to see also
Regular Inspections: Inspect fuel lines periodically for wear and tear, especially near the headers, to ensure safety
Regular inspections of fuel lines are an essential safety measure that should not be overlooked. Fuel lines are critical components in any vehicle's engine, and their condition directly impacts the vehicle's performance and safety. Over time, fuel lines can experience wear and tear, especially in areas where they are more susceptible to damage, such as near the engine headers. These headers are a vital part of the engine's exhaust system, and their proximity to the fuel lines means that any damage or deterioration can have serious consequences.
The primary goal of these inspections is to identify and address potential issues before they escalate into more significant problems. Fuel lines that are too close to the headers may be at risk of damage from heat, vibration, or even direct impact during engine operation. This can lead to fuel leaks, which pose a significant fire hazard and can also cause engine misfires or complete failure. Therefore, it is crucial to maintain a safe distance between the fuel lines and the headers.
During the inspection, look for any signs of damage, such as cracks, brittleness, or corrosion. Fuel lines should be checked for any bends or kinks that might have occurred due to engine movement or previous repairs. It is recommended to use a flexible measuring tape to ensure the fuel lines are not too close to the headers, maintaining a safe clearance distance. The exact distance may vary depending on the vehicle make and model, but generally, a gap of at least 2 inches (5 cm) is considered a good practice.
Regular maintenance and inspections can help extend the lifespan of the fuel lines and ensure the vehicle's overall reliability. By keeping a close eye on these critical components, you can prevent potential disasters and save on costly repairs. It is always better to be proactive and address minor issues before they become major problems.
In summary, periodic inspections of fuel lines, especially those near the headers, are vital for vehicle safety. These inspections help identify wear and tear, potential damage, or any deviations from the recommended clearance distance. By following this simple maintenance routine, vehicle owners can ensure their engines run smoothly and safely, reducing the risk of fuel-related accidents and costly repairs.
Unraveling the Mystery: Suction Fuel Line for Your Poulan Wild Thing Chainsaw
You may want to see also
Frequently asked questions
The general rule of thumb is to maintain a safe distance of at least 2 inches (5.1 cm) between the fuel line and the exhaust headers. This spacing helps prevent potential fuel line damage caused by heat from the headers.
Exhaust headers are designed to efficiently route exhaust gases away from the engine. However, they can reach extremely high temperatures, which can pose a risk to nearby components. If the fuel line is too close to the headers, it may be exposed to excessive heat, leading to potential fuel line degradation, cracking, or even fuel leaks.
Yes, several factors influence the recommended distance. The type of fuel line material is crucial; some materials are more heat-resistant than others. Additionally, the operating temperature of the headers and the ambient temperature of the surrounding area play a role. In high-performance applications or environments with elevated temperatures, a greater distance might be advised.
If the fuel line is too close to the exhaust headers, it can result in fuel line damage, including melting, warping, or cracking. This can lead to fuel leaks, reduced engine performance, and potential safety hazards. Proper spacing ensures the longevity and reliability of the fuel system, contributing to overall engine health and safety.