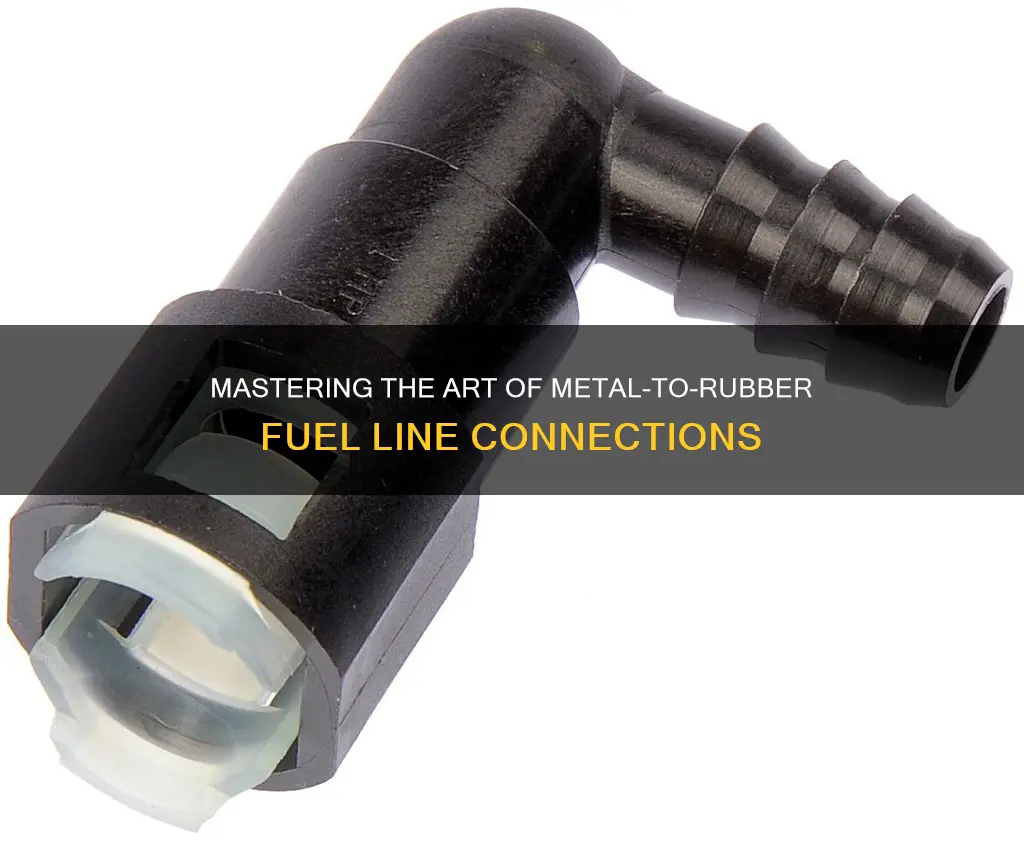
Connecting a metal fuel line to a rubber component requires careful preparation and the right tools to ensure a secure and leak-free joint. This process involves cleaning the surfaces, applying an appropriate adhesive or sealant, and using the correct connection method, such as crimping or clamping, to create a strong bond between the metal and rubber materials. Proper alignment and tightening of the connection are essential to prevent fuel leaks and ensure the system's reliability. Understanding the specific requirements and techniques for this task is crucial for anyone working on fuel systems in vehicles or machinery.
What You'll Learn
- Preparation: Ensure metal and rubber are clean, dry, and free of debris
- Fitting Selection: Choose a fitting that matches the fuel line's diameter and material
- Assembly: Tighten the fitting securely, but avoid over-tightening to prevent damage
- Sealing: Use fuel-resistant tape or sealant to create a tight seal
- Testing: Check for leaks by applying pressure and observing for any fuel escaping
Preparation: Ensure metal and rubber are clean, dry, and free of debris
When preparing to connect a metal fuel line to a rubber component, it is crucial to follow a meticulous process to ensure a secure and reliable bond. The initial step in this process is to guarantee that both the metal and rubber surfaces are in optimal condition. Start by thoroughly cleaning the metal fuel line. Use a mild detergent or soap and warm water to remove any dirt, grease, or grime that may be present. Rinse the metal line thoroughly to eliminate any residue and ensure it is completely dry before proceeding.
For the rubber component, a similar cleaning process is required. Remove any visible dirt or debris using a soft-bristled brush or a clean cloth. Pay close attention to the areas where the metal and rubber will be connected, as these spots should be free of any contaminants. After cleaning, ensure that both surfaces are completely dry. Moisture can interfere with the bonding process, so it is essential to use a clean, dry cloth to wipe away any remaining water or dirt.
The next step is to inspect the surfaces for any signs of damage or wear. Look for any cracks, tears, or imperfections in the rubber that could compromise its integrity. Similarly, check the metal fuel line for any bends, kinks, or corrosion that might affect its performance. If any issues are identified, address them before proceeding with the connection. For example, if there are small cracks in the rubber, consider using a suitable rubber repair compound to reinforce the area.
Additionally, ensure that the metal and rubber surfaces are free of any debris or contaminants that could hinder the bonding process. This includes removing any loose particles, rust, or oxidation that may have formed on the metal. Use a fine-grit sandpaper or a wire brush to gently clean the metal surface, taking care not to damage the underlying material. Once both surfaces are clean, dry, and free of debris, you are ready to proceed with the connection process, ensuring a strong and durable bond between the metal fuel line and the rubber component.
Mastering Fuel Line and Steering Repairs: A Comprehensive Guide
You may want to see also
Fitting Selection: Choose a fitting that matches the fuel line's diameter and material
When connecting metal fuel lines to rubber components, selecting the right fitting is crucial for a secure and reliable connection. The primary goal is to ensure a tight seal that prevents fuel leaks and maintains the integrity of the fuel system. Here's a detailed guide on how to choose the appropriate fitting:
Understanding the Components: Begin by familiarizing yourself with the fuel lines and the rubber components they will connect to. Metal fuel lines are typically rigid and made of materials like steel or aluminum, while rubber hoses or tubes are flexible and often used to accommodate bends and vibrations. The key is to match the fitting's dimensions to the fuel lines' diameter and material.
Fitting Selection: The market offers various types of fittings, including compression, quick-connect, and clamp-style fittings. For metal fuel lines and rubber hoses, compression fittings are commonly used. These fittings consist of a male thread on the metal line and a corresponding female thread or compression nut on the fitting. The compression nut is tightened, creating a secure grip around the rubber hose, ensuring a leak-free connection. When choosing a fitting, ensure it is specifically designed for the fuel line's diameter. Different diameters require different fitting sizes to ensure a proper seal.
Material Compatibility: Consider the material of the fuel lines and the rubber components. For metal fuel lines, stainless steel or aluminum fittings are often used due to their durability and resistance to corrosion. Ensure that the chosen fitting is compatible with the fuel line material to prevent any adverse reactions or degradation over time.
Precision and Fit: Pay close attention to the fitting's dimensions and ensure it matches the fuel line's diameter precisely. A poor fit can lead to fuel leaks and system inefficiencies. Measure the fuel line's inside diameter accurately and select a fitting with a corresponding size. This precision ensures a snug connection without causing damage to the rubber hose.
Installation and Maintenance: Proper installation is essential. Follow the manufacturer's instructions for the chosen fitting type. After installation, regularly inspect the connections for any signs of wear or damage, especially in high-vibration environments. Tighten connections periodically to maintain their integrity.
Find the Perfect Fuel Line Size for Your Husqvarna 128LD
You may want to see also
Assembly: Tighten the fitting securely, but avoid over-tightening to prevent damage
When connecting a metal fuel line to a rubber hose, it's crucial to ensure a secure and reliable assembly to prevent any potential leaks or damage. The process involves using a fitting that allows the metal line to be attached to the rubber hose, providing a strong and flexible connection. Here's a step-by-step guide on how to achieve this:
Start by preparing the components. Ensure the metal fuel line and rubber hose are clean and free of any debris or contaminants. Inspect the fitting you will be using; it should be the appropriate size and type for your specific application. Common fittings include compression-style or quick-connect fittings, each with unique methods for attachment.
Now, it's time to assemble the parts. Insert the metal fuel line into the fitting, ensuring it is aligned correctly. For compression fittings, you'll typically wrap an O-ring or gasket around the hose and then insert the line. Tighten the fitting using a wrench or spanner, but be cautious not to over-tighten. The goal is to achieve a secure connection without applying excessive force, as this can damage the rubber hose or cause the fitting to crack.
The key to a successful assembly is finding the right balance between tightness and gentleness. You want to ensure the fitting is snug, creating a reliable seal, but avoid forcing it, as this can lead to issues. Over-tightening can cause the rubber to compress unevenly, potentially leading to cracks or permanent deformation. Instead, use a gentle, steady hand to tighten the fitting until it is secure.
After tightening, inspect the connection for any signs of damage or leaks. Check for any visible cracks in the rubber hose and ensure the metal line is not pinched or kinked. If everything looks good, your assembly is complete, and you can now proceed with using the fuel line with confidence. Remember, a well-executed connection will provide a long-lasting and reliable fuel supply while minimizing the risk of any issues.
Primer vs. Fuel: Thickness and Functionality Compared
You may want to see also
Sealing: Use fuel-resistant tape or sealant to create a tight seal
When connecting a metal fuel line to a rubber component, ensuring a tight and secure seal is crucial to prevent fuel leaks and potential hazards. One effective method to achieve this is by using fuel-resistant tape or sealant. Here's a step-by-step guide on how to create a reliable seal:
Start by ensuring that the surfaces of both the metal fuel line and the rubber component are clean and free of any debris or contaminants. Use a mild detergent or isopropyl alcohol to wipe down the areas where they will be connected. This step is essential for proper adhesion. Once the surfaces are clean, apply a thin layer of fuel-resistant tape or sealant. You can use specialized products designed for fuel lines, which are typically available in tape or tube forms. These products are formulated to withstand the corrosive nature of fuels and provide excellent sealing properties.
For the tape, carefully wrap it around the metal fuel line and the rubber connection, ensuring complete coverage. Start from one end and work your way around, applying gentle pressure as you go to create a tight seal. Make sure the tape is smooth and free of any wrinkles or creases, as these can compromise the seal. If using a sealant, apply it generously to the interface between the metal and rubber. Use a small brush or your finger (after cleaning) to spread the sealant evenly, ensuring full contact between the surfaces. Allow the sealant to cure according to the manufacturer's instructions, which may involve waiting for a specified time before handling the connection.
The key to a successful seal is using the right materials and ensuring proper application. Fuel-resistant tape provides a physical barrier and mechanical grip, while sealants offer a chemical bond that can be more resistant to fuel penetration. Choose the method that best suits your specific application and the type of fuel you are dealing with. Regularly inspect the connection to ensure the seal remains intact, especially in environments where vibrations or temperature fluctuations are present.
Remember, a well-sealed connection is vital for the safe and efficient operation of your fuel system. By following these steps and using the appropriate sealing methods, you can create a reliable bond between metal and rubber components, minimizing the risk of fuel leaks and ensuring the longevity of your system.
Mastering the Art of Sealing Fuel Lines in Plastic Tanks
You may want to see also
Testing: Check for leaks by applying pressure and observing for any fuel escaping
When connecting a metal fuel line to a rubber component, ensuring a secure and leak-free joint is crucial to prevent fuel leaks and potential hazards. After completing the connection, it is essential to perform a thorough leak test to verify the integrity of the assembly. Here's a step-by-step guide on how to test for leaks:
Preparation: Before initiating the test, ensure you have the necessary tools and materials, including a pressure gauge, a source of compressed air or a pump, and a clean, dry area to work in. It is also recommended to wear protective gear, such as gloves and safety goggles, to safeguard against any potential fuel spills.
Applying Pressure: Start by applying pressure to the fuel line connection. You can use a hand pump or a compressed air source to generate a controlled amount of pressure. The pressure should be sufficient to simulate real-world conditions but should not exceed the fuel line's specified pressure rating. Gradually increase the pressure in increments, allowing time to observe for any signs of leakage between the metal and rubber components.
Observing for Leaks: During the pressure test, carefully observe the connection area for any fuel escaping. Leaks can occur at the interface between the metal and rubber, so pay close attention to this region. Look for any fuel seeping out, forming droplets, or creating a visible mist around the connection. Additionally, check for any unusual sounds, such as hissing or bubbling, which could indicate a leak. If you notice any fuel escaping, it is crucial to address the issue promptly.
Troubleshooting and Repair: If a leak is detected, you have a few options. Firstly, ensure that the connection is tight and secure. Double-check the installation and make any necessary adjustments. If the leak persists, consider using a high-quality fuel line sealant or adhesive specifically designed for metal-to-rubber connections. Apply the sealant according to the manufacturer's instructions, allowing sufficient time for it to cure before retesting.
Re-testing: After making any necessary repairs or adjustments, re-apply pressure to the connection and observe for any further leaks. This step ensures that the issue has been resolved effectively. If no leaks are detected, your connection is likely secure, and you can proceed with the fuel system's further assembly or installation. However, if leaks persist, it may indicate a more complex issue, and further investigation or professional assistance might be required.
E-Tech Fuel Line Size: 2007 Model Guide
You may want to see also
Frequently asked questions
To create a reliable bond, start by cleaning the surfaces of both the metal line and the rubber hose. Use a wire brush or sandpaper to remove any dirt, corrosion, or debris. Then, apply a suitable adhesive specifically designed for fuel line installations. Wrap the metal line around the hose, ensuring it is tightly secured, and let the adhesive cure according to the manufacturer's instructions.
Leaks can be a common issue when joining different materials. To minimize this risk, consider using a flexible metal adapter that is designed to fit over the metal fuel line and into the rubber hose. Ensure a tight fit by using a wrench, and then secure it with a ferrule or clamp. Alternatively, you can braze the connection by applying a suitable brazing alloy and heating the joint to create a strong, leak-resistant bond.
Yes, having the right tools can make the job easier. You will need a wire brush or sandpaper for surface preparation, an adhesive or sealant suitable for fuel line applications, and a heat source if you plan to braze the connection. Additionally, a wrench or pliers will be useful for tightening the metal adapter or clamp. It's also a good idea to have a fuel line cutter and a hose cutter to ensure precise and clean connections.