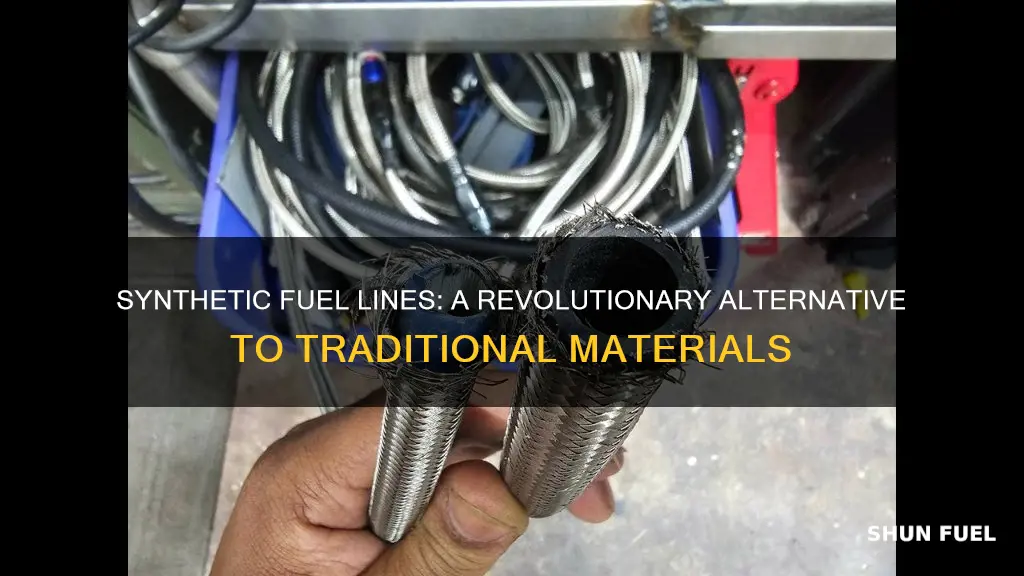
Fuel lines, which are crucial components in the transportation of fuel from the tank to the engine, can indeed be crafted from synthetic materials. These synthetic fuel lines offer a range of advantages over traditional rubber or steel options. Synthetic materials are known for their superior flexibility, durability, and resistance to extreme temperatures and chemicals, making them ideal for use in harsh automotive environments. This introduction sets the stage for a discussion on the benefits and considerations of using synthetic fuel lines in vehicles.
What You'll Learn
- Synthetic Materials: Polyethylene, polyurethane, and nylon are common synthetic materials used for fuel lines
- Flexibility: Synthetic fuel lines offer superior flexibility, making them ideal for engine vibrations and temperature changes
- Durability: Synthetic lines are resistant to fuel degradation, ensuring long-lasting performance and reduced maintenance
- Chemical Resistance: They can withstand various fuel types, including ethanol blends, without compromising integrity
- Cost-Effectiveness: Synthetic fuel lines are often more affordable than traditional rubber, making them an attractive option
Synthetic Materials: Polyethylene, polyurethane, and nylon are common synthetic materials used for fuel lines
Synthetic materials have revolutionized the automotive industry, offering innovative solutions for various components, including fuel lines. When it comes to fuel lines, several synthetic materials have gained popularity due to their unique properties and advantages over traditional materials like rubber. Among these, polyethylene, polyurethane, and nylon stand out as the most commonly used synthetic materials for this purpose.
Polyethylene, a versatile polymer, is widely utilized in the manufacturing of fuel lines. It offers excellent chemical resistance, ensuring that the fuel lines can withstand various fuels, including gasoline, diesel, and even biofuels. This material is known for its flexibility, making it easy to route and install, especially in tight spaces within the engine compartment. Additionally, polyethylene's durability and resistance to abrasion contribute to the long-term reliability of fuel lines, reducing the risk of leaks and ensuring a safe and efficient fuel supply.
Polyurethane, another synthetic material, is highly regarded for its superior flexibility and resistance to heat and chemicals. These properties make it an ideal choice for fuel lines, as it can withstand the demanding conditions of fuel transport. Polyurethane fuel lines are known for their ability to absorb vibrations, reducing the risk of damage and ensuring a smooth and continuous fuel flow. Its flexibility also allows for easy installation and customization to fit various vehicle models and engine configurations.
Nylon, a strong and lightweight synthetic fiber, is also employed in fuel line manufacturing. It offers excellent resistance to wear and tear, making it highly durable. Nylon fuel lines are known for their ability to resist kinking and bending, ensuring a reliable and consistent fuel supply. This material's lightweight nature also contributes to the overall weight reduction of the vehicle, which is a significant advantage in the automotive industry.
The use of these synthetic materials in fuel lines has brought about significant improvements in vehicle performance and safety. Their ability to withstand harsh conditions, resist chemicals, and provide flexibility ensures a reliable and efficient fuel system. As technology advances, further innovations in synthetic materials will likely lead to even more advanced and sustainable fuel line solutions, contributing to the overall advancement of the automotive industry.
Fuel Line Cut: Understanding Gas Flow and Pressure
You may want to see also
Flexibility: Synthetic fuel lines offer superior flexibility, making them ideal for engine vibrations and temperature changes
Synthetic fuel lines have revolutionized the automotive industry with their exceptional properties, particularly in terms of flexibility. This feature is crucial for ensuring the longevity and performance of fuel systems in vehicles, especially those subjected to rigorous conditions. The inherent flexibility of synthetic materials allows them to withstand the extreme forces and movements that engines encounter during operation.
Engine vibrations are a significant concern in automotive engineering. As engines run, they experience constant vibrations that can cause traditional fuel lines to become rigid and potentially crack or break over time. Synthetic fuel lines, however, are designed to absorb and distribute these vibrations more effectively. Their flexible nature enables them to move and bend with the engine, reducing the risk of damage and ensuring a consistent fuel supply. This flexibility is especially beneficial in high-performance vehicles or those with powerful engines, where vibrations can be more intense.
Temperature changes are another critical factor in fuel line performance. Engines operate in various environments, from cold starts in winter to high-temperature conditions during extended use. Synthetic fuel lines excel in this regard due to their ability to maintain flexibility across a wide temperature range. Unlike traditional rubber lines, which can become brittle in cold weather and prone to cracking in hot conditions, synthetic lines remain pliable. This flexibility prevents fuel leaks and ensures a reliable fuel supply, even in extreme temperatures, making it an essential feature for all-weather vehicle performance.
The superior flexibility of synthetic fuel lines also contributes to their overall durability. Over time, fuel lines may experience constant flexing and movement, especially in vehicles with high mileage. Synthetic materials are known for their resistance to wear and tear, ensuring that the fuel lines remain intact and functional. This durability is particularly important in preventing fuel leaks, which can lead to costly repairs and potential safety hazards.
In summary, synthetic fuel lines offer a unique advantage in terms of flexibility, making them an excellent choice for modern engines. Their ability to withstand engine vibrations and temperature changes ensures a reliable fuel supply, contributing to the overall performance and longevity of the vehicle. As technology advances, the use of synthetic materials in fuel lines will likely become even more prevalent, offering drivers a more robust and efficient fuel system.
Winter Fuel Line Freeze: Prevention Tips for Cold Climates
You may want to see also
Durability: Synthetic lines are resistant to fuel degradation, ensuring long-lasting performance and reduced maintenance
Synthetic fuel lines have emerged as a game-changer in the automotive industry, offering a range of benefits that traditional rubber or vinyl lines simply cannot match. One of the most significant advantages of synthetic lines is their exceptional durability, particularly in the context of fuel degradation.
Fuel degradation is a natural process that occurs over time, where the components of gasoline or diesel break down, leading to reduced performance and potential issues. This degradation can cause fuel lines to become brittle, crack, or even rupture, resulting in fuel leaks and potential engine damage. However, synthetic lines are engineered to be highly resistant to this degradation process. They are typically made from advanced materials that can withstand the harsh chemicals present in fuel, ensuring that the lines remain flexible, pliable, and intact over an extended period. This resistance to fuel degradation means that synthetic lines can maintain their structural integrity, providing long-lasting performance and reliability.
The durability of synthetic fuel lines translates to reduced maintenance for vehicle owners. Traditional fuel lines often require periodic replacement due to wear and tear, especially in high-temperature environments or areas with extreme weather conditions. With synthetic lines, the risk of leaks and failures is significantly lower, as they can endure the same environmental stresses without compromising their structure. This not only saves vehicle owners from the inconvenience and cost of frequent replacements but also ensures that the fuel system remains efficient and reliable, contributing to overall engine performance and longevity.
Furthermore, the resistance to fuel degradation in synthetic lines is particularly important in applications where fuel quality is a concern. In regions with poor fuel standards or where fuel contains higher levels of contaminants, synthetic lines can provide an extra layer of protection. They can help prevent fuel-related issues, such as engine misfires, reduced power, and even catastrophic failures, ensuring that the vehicle operates optimally even in less-than-ideal fuel conditions.
In summary, synthetic fuel lines offer a superior solution for maintaining the integrity of the fuel system. Their resistance to fuel degradation ensures that they remain durable and functional over time, reducing the need for frequent replacements and minimizing the risk of fuel-related issues. This makes synthetic lines an attractive choice for vehicle owners seeking long-term reliability and performance from their fuel delivery systems.
Fuel Line: Can It Run by Transmission?
You may want to see also
Chemical Resistance: They can withstand various fuel types, including ethanol blends, without compromising integrity
The use of synthetic materials for fuel lines is an innovative approach to vehicle maintenance, offering a range of benefits that traditional rubber or plastic lines cannot match. One of the most significant advantages is their chemical resistance, which is crucial for the longevity and reliability of fuel systems. Synthetic fuel lines are designed to withstand a wide variety of fuel types, including modern ethanol blends, which have become increasingly common in many regions. Ethanol, a renewable biofuel, is often mixed with gasoline to reduce emissions and improve engine performance. However, its use can pose challenges to fuel system components, as it can cause degradation and brittleness in conventional materials over time.
Synthetic fuel lines are engineered to resist the corrosive effects of ethanol, ensuring that they remain flexible and intact even when exposed to this fuel type. This resistance is particularly important in regions where ethanol-blended fuels are prevalent, as it helps prevent fuel leaks and maintains the overall integrity of the fuel system. By withstanding the chemical properties of ethanol, synthetic lines can ensure that fuel is delivered efficiently and safely to the engine, without compromising performance or reliability.
The chemical resistance of synthetic fuel lines is a result of their advanced composition and manufacturing processes. These materials are typically made from high-performance polymers that have been specifically formulated to resist a broad spectrum of chemicals, including those found in various fuel types. This resistance is not just limited to ethanol but also extends to other common fuel additives and impurities, ensuring that the fuel lines remain robust and reliable over the long term.
In addition to ethanol resistance, synthetic fuel lines also excel in their ability to handle other fuel types, such as diesel and gasoline. This versatility is a significant advantage, as it allows vehicle owners to use different fuel types without worrying about the integrity of their fuel lines. Synthetic materials can adapt to the unique properties of each fuel, ensuring optimal performance and safety.
Furthermore, the chemical resistance of synthetic fuel lines contributes to their overall durability and longevity. By resisting fuel degradation, these lines can maintain their structural integrity, flexibility, and resistance to cracking or leaking over extended periods. This durability is particularly important in harsh environmental conditions or for vehicles that are frequently used for long-distance travel, where fuel lines are exposed to varying temperatures and fuel compositions.
Brake Line vs. Fuel Line: Understanding the Differences
You may want to see also
Cost-Effectiveness: Synthetic fuel lines are often more affordable than traditional rubber, making them an attractive option
Synthetic fuel lines have emerged as a cost-effective alternative to traditional rubber fuel lines, offering a range of benefits that make them an attractive option for both manufacturers and consumers. One of the primary advantages of synthetic fuel lines is their affordability. Traditional rubber fuel lines have been the standard for decades, but their production and maintenance costs can be relatively high. Rubber is a natural material that is susceptible to degradation over time, leading to potential leaks and failures, especially in harsh environments. In contrast, synthetic fuel lines are engineered to be more durable and resistant to wear and tear. They are often made from advanced polymers and compounds that can withstand extreme temperatures, UV radiation, and chemical exposure, ensuring a longer lifespan and reduced maintenance requirements.
The cost-effectiveness of synthetic fuel lines becomes even more apparent when considering their long-term benefits. While the initial purchase price of synthetic lines might be slightly higher than that of rubber, their extended service life significantly reduces overall costs. Synthetic fuel lines are less prone to cracking, splitting, and deterioration, which means they require fewer replacements and repairs over time. This is particularly advantageous for vehicle owners and fleet operators who want to minimize maintenance expenses and ensure reliable fuel delivery systems.
Furthermore, the affordability of synthetic fuel lines extends beyond their initial cost. These synthetic materials often have a lower environmental impact compared to traditional rubber. Synthetic fuel lines can be produced using recycled materials and are more easily recyclable at the end of their life cycle, contributing to a more sustainable approach to manufacturing. This eco-friendly aspect can be a significant selling point for environmentally conscious consumers and businesses.
In addition to cost savings, synthetic fuel lines offer improved performance and reliability. They provide better flexibility and resistance to temperature changes, ensuring a consistent and secure fuel supply. This is crucial for high-performance vehicles and applications where fuel lines need to withstand rapid acceleration and deceleration without compromising integrity. The enhanced performance of synthetic fuel lines can lead to better fuel efficiency and reduced emissions, further contributing to their cost-effectiveness.
In summary, synthetic fuel lines present a compelling case for cost-effectiveness. Their affordability, durability, and long-term benefits make them a wise choice for various industries, including automotive, aviation, and marine. As technology advances, synthetic materials continue to improve, offering even more competitive advantages over traditional rubber fuel lines, making them an increasingly attractive option for those seeking reliable and cost-efficient fuel delivery systems.
Is Your Car's Fuel Line Clogged? Signs and Solutions
You may want to see also
Frequently asked questions
Synthetic fuel lines are an alternative to traditional rubber or vinyl fuel lines. They are made from synthetic materials, often a blend of polymers and plastics, specifically designed for use in fuel systems.
Yes, synthetic fuel lines can be a great choice for many vehicles. They offer several advantages, including improved flexibility, resistance to fuel degradation, and enhanced durability compared to traditional rubber lines. This can lead to a longer lifespan and better performance for your fuel system.
Synthetic fuel lines are engineered to provide superior performance and longevity. They are more flexible, which allows for easier installation and better accommodation of engine movement. Additionally, synthetic lines are less susceptible to fuel-related degradation, ensuring a longer-lasting and more reliable fuel delivery system.
Absolutely! Synthetic fuel lines are often preferred in high-performance applications due to their ability to withstand extreme temperatures and pressure. They can handle the demands of powerful engines, providing a reliable and efficient fuel supply.
While synthetic fuel lines are durable, regular inspections are still recommended. Check for any signs of damage, cracks, or leaks. It's also a good practice to use the correct fuel additives to maintain the health of the fuel system, which can indirectly benefit the synthetic lines.