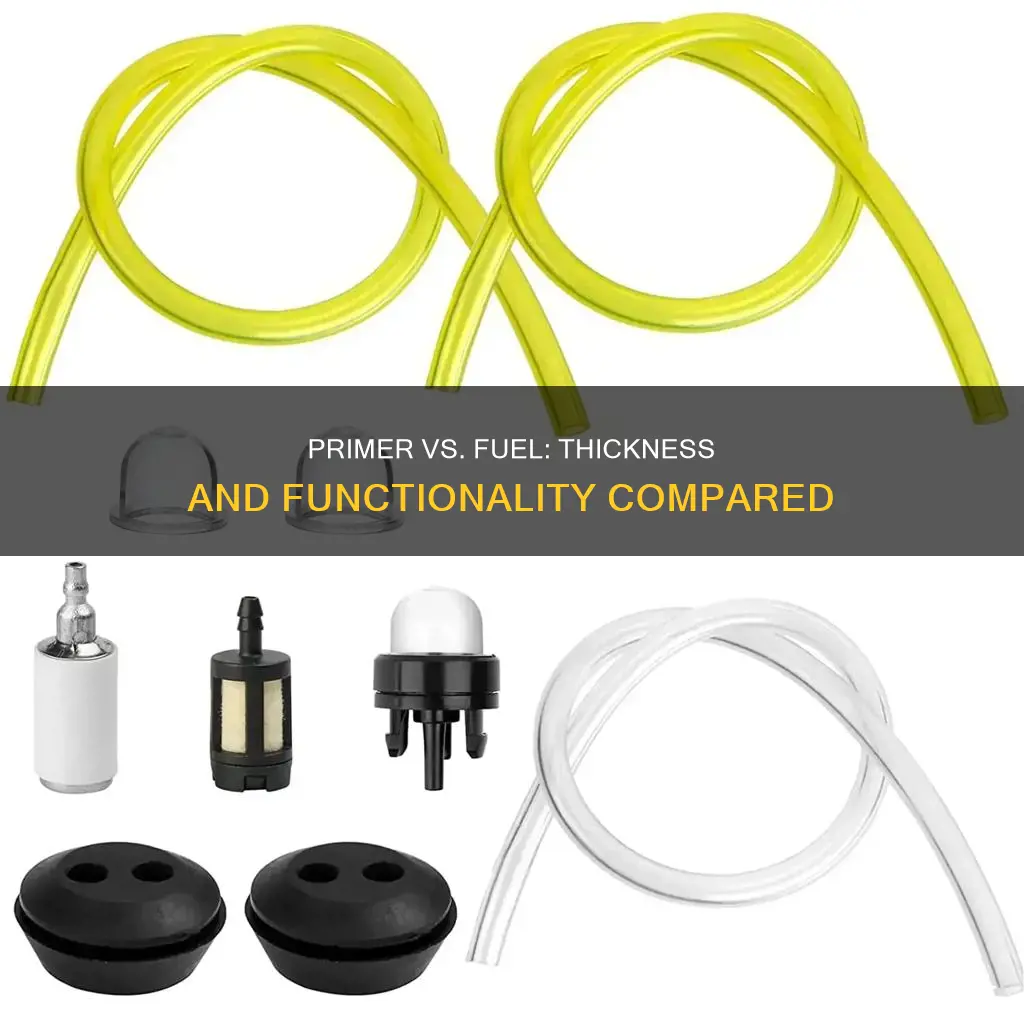
The question of whether a primer line is thicker than a fuel line is an important consideration for anyone working with automotive or industrial systems. Primer lines are typically used to prepare surfaces for painting, while fuel lines are used to transport fuel in engines and other machinery. Understanding the differences in thickness and material composition between these lines is crucial for ensuring proper functionality and safety in various applications. This paragraph aims to explore the variations in thickness and their implications, providing insights into the design choices made for these essential components.
Characteristics | Values |
---|---|
Thickness | Primer lines are typically thicker than fuel lines. |
Material | Both are made of plastic or rubber, but primer lines often have a higher density and thicker walls. |
Diameter | Primer lines usually have a larger diameter compared to fuel lines. |
Pressure Rating | Primer lines are designed to withstand higher pressure, which is crucial for efficient priming. |
Flexibility | While both are flexible, primer lines might offer more flexibility due to their thicker construction. |
Application | Primer lines are used for priming and starting engines, while fuel lines are for transporting fuel. |
Cost | Thicker primer lines might be more expensive due to the higher material and manufacturing costs. |
Compatibility | Ensure compatibility with the engine and fuel system to avoid issues. |
What You'll Learn
- Primer Line Material: Primer lines are often made of a thicker, more durable material than fuel lines
- Pressure Requirements: Thicker primer lines can handle higher pressure, a key difference
- Flow Rate: Primer lines typically have a higher flow rate, which affects their thickness
- Compatibility: Compatibility with the fuel type influences the thickness of both lines
- Safety Considerations: Thicker primer lines enhance safety by preventing fuel leaks
Primer Line Material: Primer lines are often made of a thicker, more durable material than fuel lines
Primer lines, an essential component in the automotive and marine industries, are specifically designed to withstand the rigorous demands of their applications. One of the key factors that set primer lines apart from fuel lines is the material composition. Primer lines are often crafted from a thicker and more robust material, ensuring they can handle the unique challenges posed by their role. This thicker construction is a deliberate choice to provide enhanced durability and longevity, especially in environments where primer lines are exposed to varying levels of pressure, temperature fluctuations, and chemical exposure.
The material used for primer lines is typically a high-density, high-strength plastic, such as polypropylene or polyethylene. These plastics offer excellent resistance to abrasion, impact, and chemical degradation, making them ideal for the demanding conditions found in engines, marine vessels, and other industrial settings. The thicker walls of primer lines provide structural integrity, enabling them to resist the forces exerted by fuel flow, engine vibrations, and environmental factors.
In contrast, fuel lines are generally thinner and made from materials like rubber or flexible plastic. While these materials are suitable for containing fuel, they are not designed to withstand the same level of mechanical stress and environmental exposure as primer lines. Fuel lines are more susceptible to damage from engine vibrations, temperature changes, and the corrosive effects of fuel over time.
The difference in material thickness and composition is crucial to understanding the roles and limitations of each type of line. Primer lines, with their thicker and more durable construction, are better equipped to handle the challenges of transferring primer, a highly concentrated and often corrosive substance, from the supply tank to the spray gun or other application points. This ensures that the primer is delivered efficiently and effectively, contributing to the overall success of the painting or coating process.
In summary, the material choice for primer lines is a critical aspect of their design, ensuring they can meet the specific requirements of their application. The thicker, more durable nature of primer lines, often made from high-strength plastics, sets them apart from fuel lines, which are thinner and made from materials more suited to fuel containment. This distinction highlights the importance of understanding the unique needs of different fluid transfer systems in various industries.
Signs of Frozen Fuel Lines: A Winter Checklist
You may want to see also
Pressure Requirements: Thicker primer lines can handle higher pressure, a key difference
When it comes to the automotive world, understanding the differences between various fuel and primer lines is crucial for ensuring optimal performance and safety. One of the most significant distinctions lies in their pressure requirements, which directly impact their thickness and functionality. Thicker primer lines are specifically designed to withstand higher pressure, making them a critical component in certain engine systems.
In the context of pressure requirements, the thickness of a line plays a pivotal role. Primer lines, often thicker than fuel lines, are engineered to handle the increased pressure generated during the priming process. This is particularly important in applications where engines require a robust priming system, such as in high-performance vehicles or those with unique starting mechanisms. The thicker primer line acts as a buffer, preventing pressure spikes that could potentially damage the engine or fuel system.
The pressure-handling capability of these thicker lines is a result of their construction and material composition. Typically, primer lines are made from high-quality materials that offer superior strength and flexibility. This ensures that the line can withstand the force exerted by the engine during priming without compromising its structural integrity. As a result, thicker primer lines provide a reliable and consistent priming action, which is essential for efficient engine operation.
In contrast, fuel lines, while also crucial, generally have thinner walls due to the lower pressure they need to manage. Thinner fuel lines are designed to allow for easier bending and routing, making them more adaptable to various engine configurations. However, this thinner design means they cannot handle the same level of pressure as primer lines, which is why they are typically used for fuel delivery rather than priming.
Understanding the pressure requirements and the resulting thickness of primer lines is essential for mechanics and enthusiasts alike. It ensures that the right components are used, optimizing engine performance and longevity. By recognizing the key difference in pressure handling, one can make informed decisions when selecting or modifying engine lines, ultimately contributing to a more reliable and efficient powerplant.
Chevy Silverado Fuel Line Location: A Comprehensive Guide
You may want to see also
Flow Rate: Primer lines typically have a higher flow rate, which affects their thickness
The flow rate of a line is a critical factor in determining its thickness, especially when comparing primer lines and fuel lines. Primer lines are designed to deliver a high volume of fuel to the engine's carburetor or fuel injection system, ensuring efficient and effective operation. This high flow rate requires a specific design and construction that can influence the overall thickness of the line.
In the context of flow rate, primer lines are engineered to handle a greater volume of fuel per unit of time compared to fuel lines. This is achieved through various design considerations, such as the inner diameter of the line, the material used, and the overall construction. The higher flow rate is essential for priming the engine, especially during the initial start-up process, where a rapid and consistent fuel supply is required.
The thickness of a line is directly related to its flow rate capacity. Primer lines, with their higher flow rates, often feature a thicker wall or diameter compared to fuel lines. This increased thickness allows for a larger cross-sectional area, enabling the line to accommodate a higher volume of fuel flow. As a result, the primer line can efficiently transport the required amount of fuel to the engine, ensuring optimal performance during start-up and operation.
The design of primer lines takes into account the specific requirements of the engine and the fuel system. Engineers aim to create a line that can handle the increased pressure and flow rate associated with priming. This often involves using materials with higher tensile strength and durability to withstand the demands of the high-flow environment. The construction process may also include reinforcing techniques to ensure the structural integrity of the line.
Understanding the relationship between flow rate and thickness is crucial for selecting the appropriate primer line for a particular engine. It ensures that the line can effectively deliver the required fuel volume, especially during critical engine start-up scenarios. By considering the flow rate requirements, engineers and mechanics can choose primer lines that meet the specific needs of the engine, optimizing performance and reliability.
Mastering Motorcycle Fuel Line Removal: A Step-by-Step Guide
You may want to see also
Compatibility: Compatibility with the fuel type influences the thickness of both lines
The compatibility of a fuel system with the type of fuel it is designed to use is a critical factor that determines the thickness of both the primer and fuel lines. Different fuels have varying properties, including their chemical composition, volatility, and combustion characteristics. These properties directly impact the design and construction of the fuel lines to ensure optimal performance and safety.
For instance, gasoline, a commonly used fuel, requires fuel lines that can withstand its volatile nature and high-pressure conditions. The fuel lines must be designed to resist evaporation and ensure a tight seal to prevent fuel leakage. As a result, gasoline fuel lines are typically thicker and made from materials with excellent chemical resistance. In contrast, diesel fuel lines are often thinner due to the fuel's higher density and lower volatility, requiring less robust construction.
The primer line, which is responsible for delivering fuel to the carburetor or fuel injection system, also needs to be compatible with the fuel type. For gasoline engines, the primer line must be able to handle the fuel's volatility and provide a consistent flow. Thicker primer lines are often used to accommodate the higher flow rates and ensure efficient priming. In diesel applications, the primer line may be thinner, as diesel fuel's properties allow for a more relaxed design.
In summary, the compatibility of the fuel system with the specific fuel type is a key consideration in determining the thickness of both primer and fuel lines. Engineers and designers must carefully select materials and construction methods that align with the fuel's characteristics to ensure reliable performance and prevent potential issues related to fuel incompatibility. This attention to detail is essential for maintaining the efficiency and safety of the fuel system in various automotive and industrial applications.
Dodge Charger Fuel Line Maintenance: Tips for Long-Term Reliability
You may want to see also
Safety Considerations: Thicker primer lines enhance safety by preventing fuel leaks
When it comes to fuel systems, safety is paramount, and the thickness of primer lines plays a crucial role in ensuring secure and leak-free operations. Thicker primer lines are designed to provide an extra layer of protection, especially in critical areas where fuel lines are exposed to potential hazards. This additional thickness acts as a robust barrier, preventing fuel from leaking and minimizing the risk of fires or explosions.
The primary concern with fuel lines is the potential for leaks, which can lead to dangerous situations. Thicker primer lines are engineered to withstand higher pressure and maintain their structural integrity. This is particularly important in high-performance vehicles or applications where fuel is under increased stress. By using thicker lines, the risk of fuel escaping and causing damage or igniting is significantly reduced.
In the event of a collision or impact, thinner fuel lines might not be able to withstand the force, leading to potential leaks. Thicker primer lines offer enhanced protection, ensuring that the fuel system remains intact. This is especially critical in racing or high-performance driving scenarios, where the risk of accidents is higher. The added thickness provides a safety net, allowing drivers to push their vehicles to the limit without compromising safety.
Furthermore, thicker primer lines are often used in industrial settings where fuel handling is common. These environments pose unique challenges, such as extreme temperatures and mechanical hazards. The extra thickness helps to safeguard against potential fuel leaks, ensuring that operations remain safe and efficient. It is a simple yet effective measure to prevent costly and dangerous fuel-related incidents.
In summary, thicker primer lines are a vital safety consideration in fuel systems. They provide an additional layer of protection, preventing fuel leaks and minimizing risks associated with fires or explosions. Whether in high-performance vehicles, racing, or industrial applications, the use of thicker lines is a proactive approach to maintaining safety standards and ensuring the well-being of both personnel and equipment.
Fuel Line Removal: A Guide to YJ Fuel Rail Maintenance
You may want to see also
Frequently asked questions
Yes, typically the primer line is thicker than the fuel line. Primer lines are usually made of a thicker material to ensure a strong bond and proper adhesion to the surface, especially when used in painting or coating applications.
The thickness of the primer line is essential for achieving a smooth and even finish. Thicker primer provides better coverage, allowing for a more uniform base layer. This is crucial for creating a solid foundation for the final paint or coating, ensuring a professional-looking result.
It is not recommended to use a thinner fuel line as a substitute for a primer line. Fuel lines are designed for specific purposes and may not provide the necessary adhesion and coverage. Using a thinner primer line might result in an uneven surface and compromise the quality of the final finish.