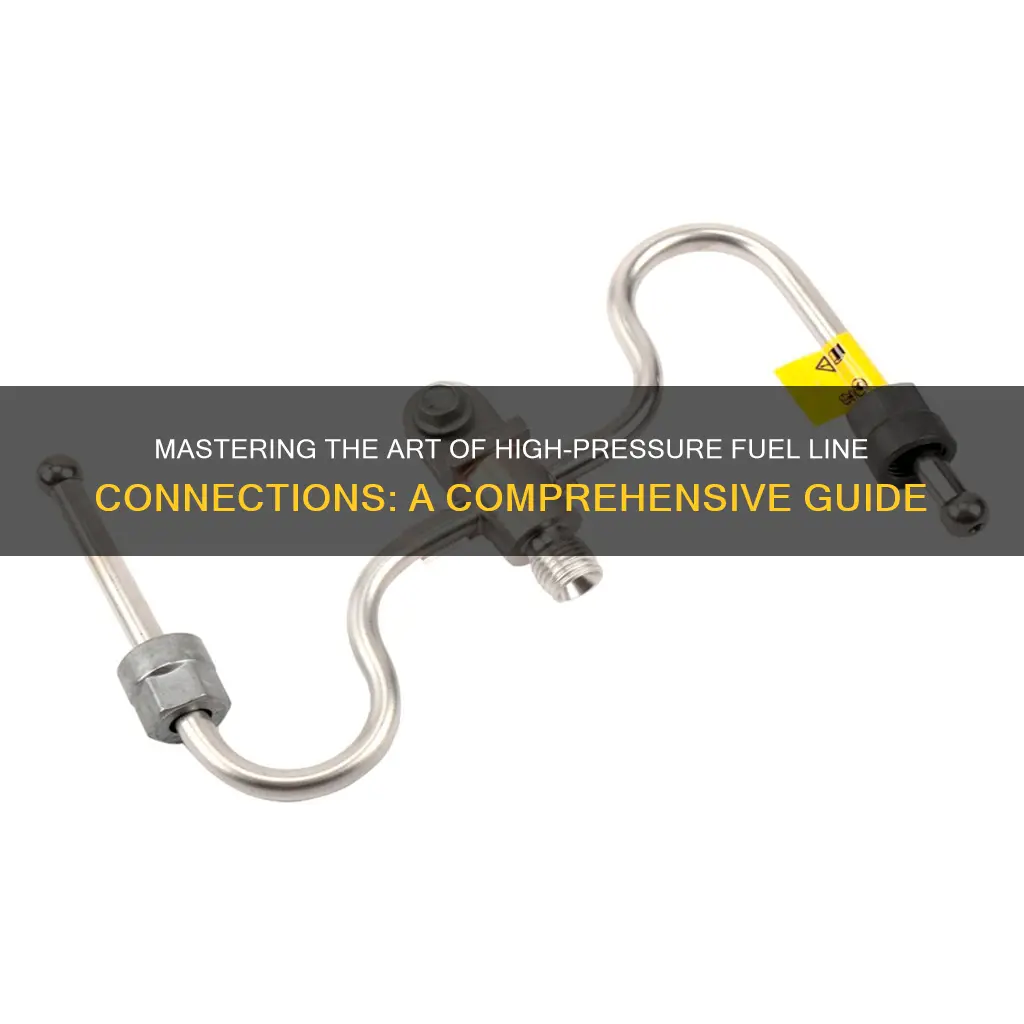
Connecting two high-pressure fuel lines requires careful attention to detail and adherence to safety protocols. This process involves ensuring that the lines are compatible, properly sized, and securely attached to prevent leaks and potential hazards. It is essential to understand the specific requirements of the fuel system and to use the correct tools and materials to ensure a successful and safe connection.
What You'll Learn
- Preparation: Ensure both lines are clean, dry, and free of debris
- Clamps: Use appropriate high-pressure clamps for a secure connection
- Alignment: Align lines properly to avoid kinks and ensure smooth flow
- Fitting Types: Choose the right fitting type for your specific application
- Testing: Verify the connection's integrity with a pressure test
Preparation: Ensure both lines are clean, dry, and free of debris
When preparing to connect two high-pressure fuel lines, it is crucial to ensure that both lines are in optimal condition to avoid any potential issues. Start by thoroughly cleaning each fuel line. This process involves removing any dirt, grime, or debris that may have accumulated over time. Use a suitable cleaning agent or solvent recommended for fuel lines to ensure effective cleaning. Rinse the lines thoroughly to eliminate any residue and allow them to dry completely. Moisture or dirt within the lines can lead to corrosion or blockages, so ensure they are entirely dry before proceeding.
Once the lines are clean, inspect them for any signs of damage or wear. Look for cracks, leaks, or any other visible defects. If any issues are found, it is essential to replace the affected lines to maintain the integrity of the fuel system. Ensure that the lines are straight and free of any kinks or bends that could restrict flow.
After cleaning and inspection, verify that both fuel lines are dry. Moisture can cause corrosion and lead to issues with the connection. Use a towel or a soft cloth to wipe down the lines and remove any excess moisture. Allow sufficient time for the lines to air dry completely, ensuring there is no residual dampness.
By taking the time to properly prepare the fuel lines, you can ensure a successful and secure connection. This preparation process is vital to maintaining the performance and safety of the fuel system, especially when dealing with high-pressure fuel lines. It is a critical step that should not be overlooked to avoid potential complications during the connection process.
A Step-by-Step Guide to Cleaning Your Boat's Fuel Lines
You may want to see also
Clamps: Use appropriate high-pressure clamps for a secure connection
When connecting two high-pressure fuel lines, using the right clamps is crucial to ensure a secure and reliable seal. High-pressure fuel lines require specialized clamps that can withstand the intense forces and pressures involved. Here's a detailed guide on how to choose and use the appropriate clamps for this task:
Understanding High-Pressure Clamps:
High-pressure fuel lines operate at elevated pressures, often exceeding 100 psi. Standard clamps may not provide the necessary grip and sealing capability under these conditions. Specialized high-pressure clamps are designed to offer a tight, leak-free connection. These clamps typically feature a robust construction with a wide clamping range to accommodate various fuel line diameters. Look for clamps made from durable materials like stainless steel or hardened steel to ensure longevity and resistance to corrosion.
Selecting the Right Clamp:
The key to a successful connection is choosing the right clamp for your specific fuel line dimensions. Measure the diameter of your fuel lines accurately and select a clamp with a corresponding inside diameter. Clamps are often available in different sizes, so refer to the manufacturer's specifications to find the best fit. For instance, if your fuel lines are 0.5 inches in diameter, opt for a clamp designed for that size. Ensure the clamp has a secure locking mechanism, such as a screw or a quick-release lever, to ensure it stays in place.
Installation Process:
- Prepare the Lines: Ensure both fuel lines are clean and free of any debris or contaminants. Cut the lines to the desired length, leaving a few extra inches for clamping.
- Position the Clamp: Slide the clamp onto one fuel line, positioning it near the end. Ensure the clamp's opening is facing the correct direction for assembly.
- Connect the Lines: Carefully insert the second fuel line into the clamp, aligning it with the first line. Use your hands or a tool to push the lines together, creating a tight fit within the clamp.
- Secure the Clamp: Tighten the clamp's locking mechanism securely. Apply firm pressure to ensure the clamp is snug against the fuel lines. Avoid over-tightening to prevent damage to the lines.
- Test for Leaks: After clamping, check for any leaks by applying pressure to the connection and inspecting for any seepage. If leaks occur, adjust the clamp's position or tighten it slightly, then retest.
Using high-pressure clamps designed for fuel lines ensures a secure connection, preventing fuel leaks and potential engine damage. Always refer to the manufacturer's guidelines for specific clamp recommendations and installation instructions for your fuel line system.
Mastering the Art of Fuel Line Priming: A Comprehensive Guide
You may want to see also
Alignment: Align lines properly to avoid kinks and ensure smooth flow
When connecting two high-pressure fuel lines, proper alignment is crucial to ensure a safe and efficient setup. The primary goal is to avoid any kinks or bends that could restrict fuel flow and potentially lead to dangerous situations. Here's a step-by-step guide on how to achieve this:
- Prepare the Components: Before you begin, ensure you have the correct fittings and adapters for your specific fuel lines. Check the specifications of your fuel lines and the engine to determine the appropriate connections. Having the right tools, such as fuel line cutters, crimping tools, and thread seal tape, will also make the process smoother.
- Measure and Mark: Measure the length of the new connection to ensure it is the correct size. Mark the spots where the fuel lines will be connected, taking into account the desired angle and orientation. This step is essential to ensure that the lines are aligned correctly from the start.
- Cut and Prepare the Lines: Using the marked spots as a guide, carefully cut the fuel lines to the desired length. Remove any excess material, ensuring a clean and precise cut. If the lines have threads, apply thread seal tape to prevent leaks. For smooth connections, consider using fuel line adapters or fittings that match the thread sizes.
- Align and Connect: Now, it's time to bring the lines together. Align the ends of the fuel lines, ensuring they are straight and parallel to each other. The key is to avoid any sharp bends or kinks, as these can restrict flow and cause pressure buildup. Use the fittings and adapters to securely connect the lines, tightening them by hand first to check for any leaks. Then, use the appropriate tools to tighten the connections further, being careful not to overtighten and damage the lines.
- Final Checks: After connecting the lines, perform a thorough inspection. Check for any signs of damage, leaks, or improper alignment. Ensure that the connections are tight and secure. If everything looks good, start the engine and monitor the fuel flow. Listen for any unusual noises and watch for any fuel leaks. If all is well, your high-pressure fuel lines are now properly aligned and connected, ready to deliver fuel efficiently to your engine.
Remember, when working with high-pressure fuel lines, safety should always be the top priority. Take your time, follow the manufacturer's guidelines, and seek professional assistance if needed to ensure a successful and safe installation.
Locate the JDX500 Fuel Line Shut-Off Valve: A Comprehensive Guide
You may want to see also
Fitting Types: Choose the right fitting type for your specific application
When connecting two high-pressure fuel lines, selecting the appropriate fitting type is crucial to ensure a secure and reliable connection. The right fitting will depend on various factors, including the specific application, the type of fuel, and the operating conditions. Here's a guide to help you choose the appropriate fitting:
- Compression Fittings: These are commonly used for high-pressure fuel line connections due to their ability to provide a tight seal. Compression fittings consist of a ferrule (a metal or rubber ring) that is compressed between the two fuel lines. The key advantage is their versatility; they can accommodate different fuel types and sizes. When using compression fittings, ensure you follow these steps: First, clean the fuel lines and fittings to remove any debris. Then, insert the fuel lines into the fittings, ensuring they are aligned properly. Apply the appropriate amount of force to compress the ferrule, creating a secure seal. Tighten the fittings securely, but be careful not to over-tighten, as it may damage the lines.
- Quick-Connect Fittings: For applications requiring frequent disconnections and connections, quick-connect fittings are ideal. These fittings use a barbed design with an O-ring or gasket to create a seal. They are easy to assemble and disassemble, making them convenient for maintenance and repairs. However, they may not be as secure as compression fittings for high-pressure applications. When using quick-connect fittings, ensure a tight connection by inserting the fuel lines into the barbs and applying the recommended torque. Always check for any leaks after assembly.
- Swivel Fittings: Swivel fittings are useful when you need flexibility and the ability to rotate the connection. They are commonly used in applications where the fuel lines need to move or adjust. These fittings typically have a threaded connection and a swivel joint, allowing for a full range of motion. When installing swivel fittings, thread the fuel lines onto the fitting and secure them with a nut. Ensure the swivel joint is free to rotate, and check for any leaks at the connection points.
- Hose Clamps: While not a fitting type in the traditional sense, hose clamps can be used to secure and seal fuel lines in specific scenarios. They are useful for temporary connections or when working with flexible hoses. Hose clamps apply pressure to the fuel lines, creating a seal. Choose the appropriate size and material for the fuel line diameter and pressure requirements. Tighten the hose clamp securely, ensuring it is neither too loose nor too tight.
Remember, when working with high-pressure fuel lines, it is essential to prioritize safety and follow manufacturer guidelines. Always wear appropriate personal protective equipment and ensure you are familiar with the specific requirements of your application. Regularly inspect and maintain the connections to prevent potential issues.
Fuel Filter's Role: Ensuring Supply Line Efficiency
You may want to see also
Testing: Verify the connection's integrity with a pressure test
When dealing with high-pressure fuel lines, ensuring their integrity is crucial to prevent potential hazards and maintain optimal engine performance. A pressure test is an essential step to verify the connections' strength and reliability. Here's a detailed guide on how to perform this test:
Preparation: Before initiating the pressure test, ensure you have the necessary tools and equipment. You'll need a pressure gauge, preferably a digital one for accurate readings, and a source of compressed air or nitrogen. It is recommended to use a specialized pressure testing kit designed for fuel lines to ensure compatibility. Additionally, have a supply of clean, filtered fuel ready for the test.
Procedure: Start by disconnecting the fuel lines from the engine and any associated components. This step ensures that the lines are isolated and the test can be conducted safely. Inspect the connections and fittings for any signs of damage or corrosion. Clean the surfaces if necessary to ensure a proper seal during the test. Now, connect one end of the fuel line to the pressure source and the other to a suitable test point, such as a specialized test port or a temporary connection made with quick-release fittings. Secure all connections tightly to avoid any leaks.
Next, slowly increase the pressure in the fuel line using the compressed air or nitrogen source. Start with a low pressure and gradually build it up to the specified operating pressure for your fuel system. The target pressure should be determined by consulting the engine's manual or manufacturer's guidelines. As you increase the pressure, closely monitor the pressure gauge for any fluctuations or drops. A stable reading indicates a secure connection. If you notice any pressure loss, it could be a sign of a leak or an improperly tightened connection.
Interpreting Results: After reaching the desired pressure, maintain it for a specified duration, typically several minutes. During this time, inspect the connections again for any signs of leakage. If no leaks are observed, and the pressure holds steady, the connections are considered secure and reliable. However, if leaks are detected, it is crucial to identify the source immediately. This may involve re-tightening connections, replacing damaged fittings, or addressing any other potential issues.
Safety Considerations: Throughout the testing process, prioritize safety. Always work in a well-ventilated area, and ensure proper ventilation when using compressed air. Wear appropriate personal protective equipment, such as safety goggles and gloves, to protect against potential fuel splashes. Additionally, be mindful of the fuel's temperature and ensure it remains within safe limits during the test.
By following these steps and conducting a thorough pressure test, you can effectively verify the integrity of high-pressure fuel line connections, ensuring a safe and efficient fuel system.
Optimizing Performance: Choosing the Right Fuel Line Size for Your 3/8 Inline Filter
You may want to see also
Frequently asked questions
Connecting two high-pressure fuel lines requires careful attention to detail and the use of the right tools and materials. Here's a step-by-step guide: First, ensure both lines are clean and free of any debris. Then, use a fuel line connector kit, which typically includes a ferrule and a crimping tool. Cut the lines to the desired length, leaving a few extra inches for the connector. Insert the fuel line into the connector, ensuring it's the correct size. Use the crimping tool to apply pressure and create a secure connection. Repeat this process for the second line. It's crucial to check for any leaks after the connection is made.
You'll need a few essential tools to connect high-pressure fuel lines. These include a fuel line cutter or a pair of sharp scissors, a fuel line connector kit with various sizes of ferrules and a crimping tool, a solvent cleaner or fuel line cleaner, and a rag or cloth for cleaning. Additionally, having a torque wrench and a fuel pressure gauge can be helpful for ensuring a proper connection and checking for leaks.
Absolutely! Working with high-pressure fuel lines can be dangerous if not done correctly. Always wear safety gear, including gloves and safety goggles, to protect your hands and eyes. Ensure you're in a well-ventilated area, and be cautious of any potential fire hazards. It's crucial to double-check your connections and test for leaks before starting the vehicle. Never smoke or use open flames near the fuel lines.
While it's possible to use alternative connectors, it's generally recommended to stick with the original equipment manufacturer (OEM) specifications. Using the correct connector from the fuel line connector kit ensures compatibility and a secure connection. If you need to adapt the lines to a different system, consult a professional mechanic or refer to the vehicle's manual for specific instructions and recommended connectors.