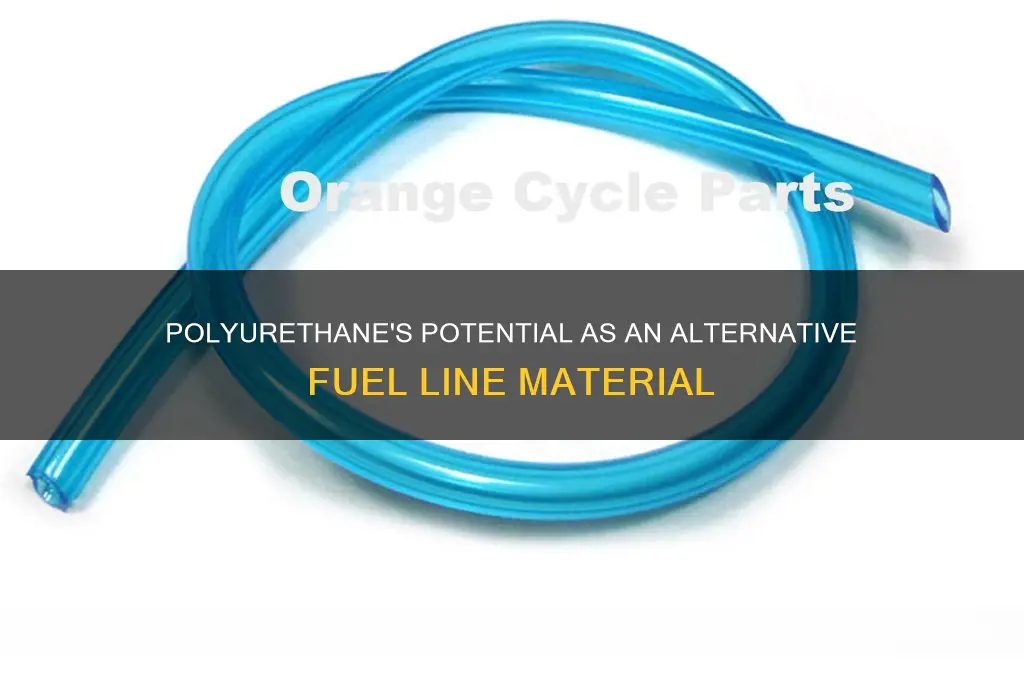
Polyurethane, a versatile synthetic material, has found numerous applications in various industries due to its unique properties. One area of interest is its potential use as a fuel line material. Fuel lines are crucial components in vehicles, responsible for transporting fuel from the tank to the engine. Traditionally, rubber or plastic materials have been used, but there is a growing need for alternatives that offer improved durability, flexibility, and resistance to fuel degradation. This has led to the exploration of polyurethane as a promising candidate for fuel line applications, as it can provide enhanced performance and longevity in harsh fuel environments.
What You'll Learn
- Chemical Composition: Polyurethane's chemical structure makes it resistant to fuel degradation
- Temperature Tolerance: It can withstand extreme temperatures, making it suitable for fuel lines
- Flexibility: Polyurethane's flexibility ensures it can withstand engine vibrations and movement
- Durability: It is resistant to wear and tear, ensuring long-lasting performance in fuel lines
- Compatibility: Polyurethane is compatible with most fuels, including gasoline, diesel, and biofuels
Chemical Composition: Polyurethane's chemical structure makes it resistant to fuel degradation
The chemical composition of polyurethane is a key factor in its ability to withstand the harsh conditions of fuel lines. Polyurethane is a polymer, a large molecule made up of repeating structural units, and its unique structure contributes to its remarkable resistance to fuel degradation.
At the heart of polyurethane's strength lies its molecular backbone, which is composed of organic isocyanates and polyols. These components form a long-chain polymeric structure, creating a robust and flexible material. The isocyanate groups in polyurethane are highly reactive and can form covalent bonds with the polyol molecules, resulting in a strong and durable polymer network. This network is highly resistant to the breakdown caused by fuel components, such as gasoline, diesel, and aviation fuels.
The resistance to fuel degradation is further enhanced by the presence of various additives in polyurethane formulations. These additives can include antioxidants, stabilizers, and UV inhibitors, which work together to protect the polymer from the damaging effects of fuel. Antioxidants, for instance, scavenge free radicals generated by fuel oxidation, preventing the initiation of degradation reactions. Stabilizers improve the thermal stability of polyurethane, ensuring it can withstand the high temperatures encountered in fuel lines. UV inhibitors, on the other hand, protect the material from the harmful effects of sunlight, which can accelerate degradation in outdoor applications.
The chemical structure of polyurethane also contributes to its flexibility and durability. The polymer's long-chain structure allows it to bend and stretch without breaking, making it ideal for fuel lines that experience vibrations and temperature fluctuations. Additionally, polyurethane's resistance to abrasion and chemical corrosion ensures its longevity in harsh environments.
In summary, the chemical composition of polyurethane, with its isocyanate-polyol backbone and carefully selected additives, provides an effective barrier against fuel degradation. This resistance, combined with its flexibility and durability, makes polyurethane an excellent choice for fuel line applications, ensuring reliable performance and longevity in various fuel systems.
Mastering the Art of Fuel Line Hose Clamp Removal: A Step-by-Step Guide
You may want to see also
Temperature Tolerance: It can withstand extreme temperatures, making it suitable for fuel lines
Polyurethane is an excellent material for fuel lines due to its remarkable temperature tolerance. It can withstand a wide range of temperatures, from extremely low to high, making it a reliable choice for fuel systems in various applications. This temperature resistance is a critical factor in ensuring the safety and efficiency of fuel lines, especially in environments where temperature fluctuations are common.
The ability of polyurethane to handle extreme temperatures is attributed to its unique chemical structure. It is a polymer with a long-chain structure, which provides excellent flexibility and durability. This flexibility allows polyurethane to maintain its shape and integrity even when exposed to rapid temperature changes. In fuel lines, this is crucial as it ensures that the material can withstand the expansion and contraction caused by temperature variations without compromising its structural integrity.
In low-temperature environments, polyurethane's temperature tolerance becomes especially valuable. It can resist freezing temperatures without becoming brittle or losing its flexibility. This property is essential for fuel lines used in cold climates or during winter months, ensuring that the material remains pliable and functional even when temperatures drop significantly.
On the other hand, polyurethane's resistance to high temperatures is equally impressive. It can withstand temperatures well above the boiling point of fuel, making it suitable for hot environments. This feature is particularly important in high-performance vehicles or industrial settings where fuel lines may be exposed to intense heat. The material's ability to maintain its shape and prevent fuel leakage under such conditions is a significant advantage.
Furthermore, the temperature tolerance of polyurethane contributes to its overall reliability and longevity. It can resist thermal degradation, ensuring that the fuel lines remain effective over an extended period. This durability is a result of polyurethane's chemical stability and its ability to resist oxidation and other forms of degradation caused by heat. As a result, polyurethane fuel lines offer a long-lasting solution, reducing the need for frequent replacements and minimizing maintenance issues.
Toyota Corolla Fuel Line Location: 1989 Model Guide
You may want to see also
Flexibility: Polyurethane's flexibility ensures it can withstand engine vibrations and movement
The flexibility of polyurethane is a key advantage when considering its use as a material for fuel lines in vehicles. This property allows the material to adapt and move with the engine, ensuring a reliable and secure connection. Engine vibrations and movement are common occurrences, especially during acceleration, deceleration, and high-speed driving. Without the necessary flexibility, fuel lines could become damaged or disconnected, leading to potential performance issues and safety hazards.
Polyurethane's ability to withstand these mechanical stresses is attributed to its unique molecular structure. The material is composed of long chains of polyurethane polymers, which can easily bend and stretch without breaking. This flexibility is particularly important in fuel lines, as it allows the material to accommodate the natural expansion and contraction of the engine components over time. As the engine operates, the fuel lines need to move with the engine block, and polyurethane's flexibility ensures that the lines remain intact and functional.
In contrast, traditional fuel lines made from materials like rubber or vinyl may not offer the same level of flexibility. These materials can become brittle and crack over time, especially when exposed to the harsh conditions inside an engine compartment. The constant vibrations and temperature fluctuations can cause the material to degrade, leading to leaks or even complete failure of the fuel line.
The flexibility of polyurethane also contributes to its durability. It can resist wear and tear, ensuring that the fuel lines remain intact even in the presence of engine contaminants. The material's resistance to abrasion and chemical degradation makes it an ideal choice for fuel lines, as it can withstand the corrosive effects of fuel and engine fluids.
Furthermore, polyurethane's flexibility allows for easier installation and maintenance. The material can be easily manipulated into the desired shape and size, making it simpler to route the fuel lines through the engine compartment. This ease of installation can save time and effort during the manufacturing process and also simplifies any necessary repairs or replacements in the future.
Mastering the Art of Painting Rubber Fuel Line Hose
You may want to see also
Durability: It is resistant to wear and tear, ensuring long-lasting performance in fuel lines
Polyurethane is an excellent material for fuel lines due to its exceptional durability and resistance to wear and tear. This property is crucial for ensuring the long-lasting performance of fuel lines, which are subjected to various environmental stresses and mechanical strains. The durability of polyurethane is attributed to its robust molecular structure, which provides excellent resistance to abrasion, impact, and chemical degradation.
One of the key advantages of polyurethane in fuel lines is its ability to withstand the constant flexing and movement that occurs during vehicle operation. Unlike traditional materials like rubber or vinyl, polyurethane is highly flexible and can retain its shape even under repeated bending and stretching. This flexibility is essential for maintaining a secure connection between the fuel tank and the engine, preventing leaks and ensuring optimal fuel delivery.
The wear and tear resistance of polyurethane is further enhanced by its ability to resist aging and degradation over time. Polyurethane fuel lines can withstand exposure to harsh chemicals, oils, and fuels, which are common in automotive environments. This resistance to chemical degradation ensures that the fuel lines remain intact and functional even in the presence of contaminants, preventing potential fuel leaks and engine damage.
Additionally, polyurethane's durability is evident in its ability to resist temperature fluctuations. It can withstand extreme temperatures, from the intense heat generated by the engine to the cold temperatures of winter. This temperature resistance ensures that the fuel lines maintain their structural integrity and flexibility, even in varying environmental conditions.
In summary, polyurethane's durability is a critical factor in its suitability as a fuel line material. Its resistance to wear and tear, combined with its flexibility and chemical resistance, ensures that fuel lines remain reliable and long-lasting. This makes polyurethane an ideal choice for fuel lines, providing a safe and efficient solution for fuel delivery in vehicles.
Catalyst Fuel Line Removal: A Step-by-Step Guide for 2006 Jeep Liberty Owners
You may want to see also
Compatibility: Polyurethane is compatible with most fuels, including gasoline, diesel, and biofuels
Polyurethane is an incredibly versatile material that has found its way into numerous applications, and its compatibility with various fuels is one of its most notable attributes. When it comes to fuel lines, the material's ability to withstand the corrosive effects of different fuels is a significant advantage. This compatibility is particularly important in the automotive and aviation industries, where fuel lines are exposed to a variety of fuels, from traditional gasoline and diesel to the emerging biofuels.
The compatibility of polyurethane with these fuels is a result of its chemical structure. Polyurethane is a polymer, and its resistance to degradation from fuel exposure is due to the strength and stability of its polymer chains. These chains are resistant to the breakdown caused by the various hydrocarbons and oxygenates present in different fuel types. This means that polyurethane fuel lines can maintain their structural integrity and performance over time, even when exposed to the varying chemical compositions of different fuels.
In the context of gasoline, polyurethane's compatibility is especially relevant. Gasoline contains a range of volatile hydrocarbons, and its exposure to these components can lead to degradation in other materials. However, polyurethane's resistance to hydrocarbon dissolution and its ability to maintain flexibility and tensile strength make it an ideal choice for fuel lines. This is crucial for ensuring the safe and efficient operation of fuel systems, as it prevents leaks and maintains the integrity of the fuel supply.
Similarly, diesel fuel, with its higher cetane number and different chemical composition compared to gasoline, also poses unique challenges. Polyurethane's compatibility with diesel is equally important, as it ensures that the fuel lines can withstand the higher pressure and temperature conditions associated with diesel engines. This compatibility is further enhanced by polyurethane's ability to resist oxidation, which is a common issue with fuels containing higher levels of oxygenates.
The versatility of polyurethane extends to biofuels as well. As the world shifts towards more sustainable energy sources, biofuels are becoming increasingly common. These fuels, derived from organic materials, can vary widely in composition. Polyurethane's compatibility with biofuels is a significant advantage, as it allows for the use of these alternative fuels without compromising the performance and longevity of fuel lines. This is particularly important in the development of more sustainable transportation systems.
Brake Line vs. Fuel Line: Understanding the Differences
You may want to see also
Frequently asked questions
Yes, polyurethane is commonly used for fuel lines in the automotive industry due to its excellent resistance to fuel-related chemicals and its ability to withstand high temperatures and pressures.
Polyurethane fuel lines offer several benefits, including superior flexibility, which allows for easier installation and reduced risk of damage during vehicle operations. They also have a longer lifespan compared to traditional rubber fuel lines, providing better long-term reliability.
Absolutely! Polyurethane is an ideal choice for high-performance applications as it can handle the increased stress and demands of such vehicles. Its durability and resistance to fuel degradation make it a preferred material for racing and modified cars.
While polyurethane fuel lines might have a slightly higher initial cost compared to some alternatives, their longevity and performance advantages often make them a cost-effective solution in the long run. Additionally, their ability to prevent fuel leaks can save money on potential repairs and maintenance.