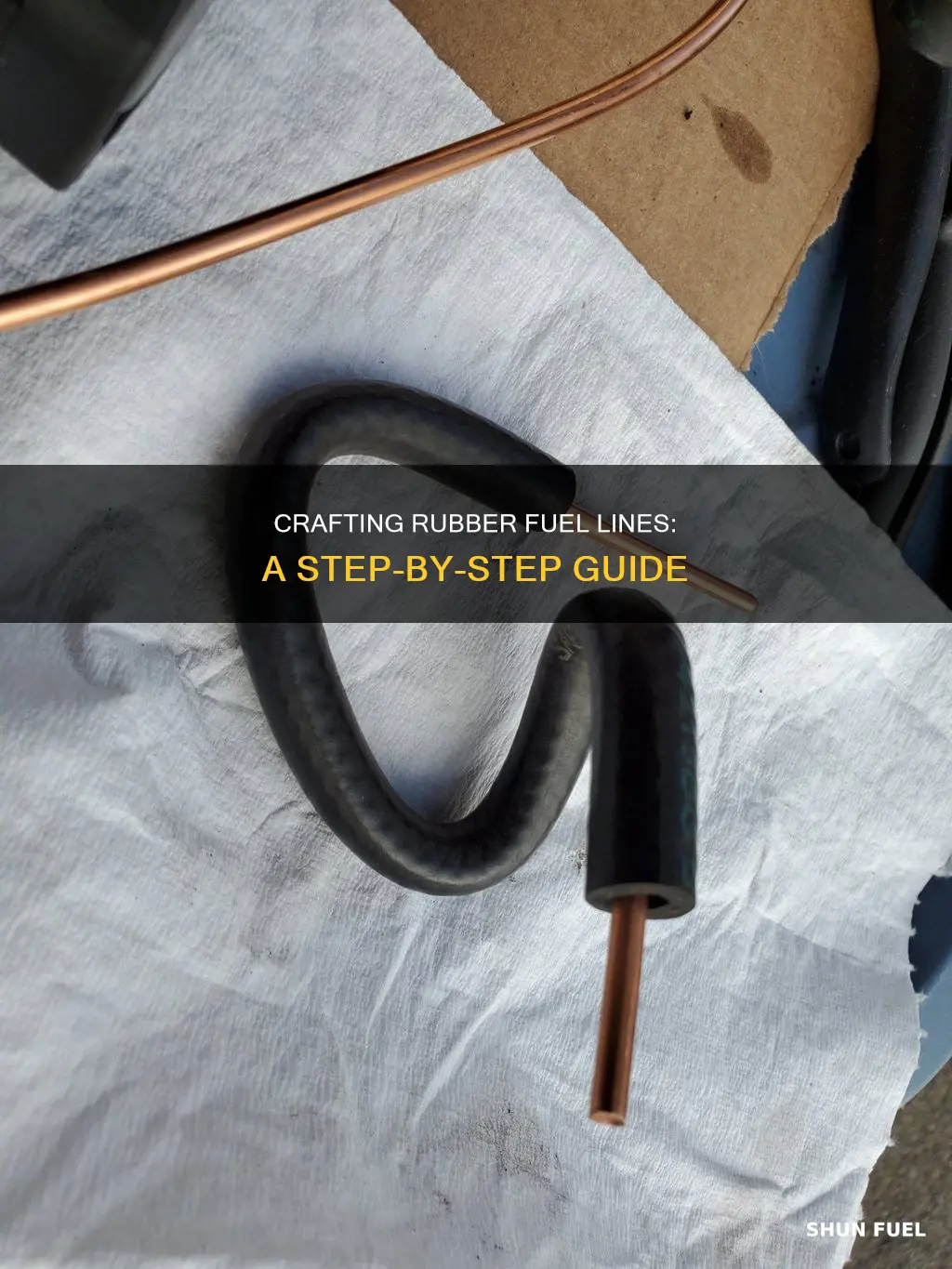
Forming a rubber fuel line is a crucial process in the construction of fuel systems for vehicles and machinery. It involves shaping and joining rubber tubing to create a flexible and durable pathway for fuel transport. This process requires careful consideration of the material's properties, including its elasticity, resistance to fuel degradation, and ability to withstand temperature fluctuations. The manufacturing process typically involves extrusion, where rubber is heated and pushed through a die to form the desired shape, followed by curing to ensure the material's integrity. Proper formation ensures a reliable and safe fuel supply, preventing leaks and potential engine damage.
What You'll Learn
- Material Selection: Choose the right rubber compound for fuel resistance and durability
- Design Considerations: Ensure the line's diameter, length, and bend radius meet specifications
- Manufacturing Process: Utilize techniques like extrusion or molding for precise construction
- Testing and Inspection: Perform pressure tests and visual inspections to ensure quality
- Installation Guidelines: Provide clear instructions for proper connection and routing
Material Selection: Choose the right rubber compound for fuel resistance and durability
When it comes to creating a rubber fuel line, material selection is a critical aspect that ensures the line's longevity and performance. The primary goal is to choose a rubber compound that can withstand the corrosive nature of fuel while maintaining its structural integrity over time. This involves considering several factors, including the type of fuel, operating temperatures, and the overall environment in which the fuel line will be used.
One of the most common materials used for fuel lines is natural rubber. Natural rubber has excellent flexibility and resilience, making it ideal for withstanding the constant flexing and movement that fuel lines experience. However, it is important to note that natural rubber is not inherently resistant to fuel. To address this, manufacturers often add specialized additives to the rubber compound. These additives can include antioxidants, stabilizers, and reinforcing agents, which help to enhance the rubber's resistance to fuel degradation. For instance, antioxidants prevent the oxidation of the rubber, which can lead to cracking and deterioration, while stabilizers improve the material's overall durability.
Another option for fuel lines is synthetic rubber, such as neoprene or butyl rubber. These materials offer superior fuel resistance compared to natural rubber. Neoprene, for example, is known for its excellent resistance to oils and fuels, making it a popular choice for fuel line applications. Butyl rubber, on the other hand, provides exceptional resistance to fuel evaporation and is less susceptible to swelling when exposed to fuels. The choice between natural and synthetic rubber often depends on the specific requirements of the project, including cost, temperature range, and the desired level of fuel resistance.
In addition to the type of rubber, the compounding process is crucial. The compounding process involves mixing various additives with the rubber to tailor its properties. For fuel lines, the compound should be designed to resist fuel-related degradation, such as cracking, swelling, and loss of flexibility. Manufacturers often use a combination of softeners, accelerators, and fillers to achieve the desired characteristics. Softeners, for instance, improve the rubber's flexibility, while accelerators enhance its curing properties, ensuring a strong and durable bond.
Furthermore, the choice of rubber compound should consider the operating conditions. If the fuel line is expected to operate at high temperatures, a compound with a higher heat resistance is necessary. Some rubbers, like silicone or fluororubber, offer excellent temperature stability and can withstand extreme conditions. The environmental factors, such as exposure to sunlight or chemicals, should also be taken into account to ensure the rubber compound is suitable for the specific application.
In summary, selecting the right rubber compound for fuel lines involves a careful consideration of various factors. Natural rubber can be used with additives, while synthetic rubbers like neoprene and butyl provide superior fuel resistance. The compounding process and the choice of additives play a vital role in tailoring the material's properties. By understanding the specific requirements and operating conditions, engineers can make informed decisions to ensure the fuel line's durability and performance.
2007 Hyundai Accent Fuel Lines: Location Guide
You may want to see also
Design Considerations: Ensure the line's diameter, length, and bend radius meet specifications
When designing a rubber fuel line, it is crucial to consider the specifications for diameter, length, and bend radius to ensure optimal performance and safety. These parameters play a significant role in determining the line's ability to transmit fuel efficiently and securely.
The diameter of the fuel line is a critical factor. It should be chosen based on the required flow rate and pressure considerations. A larger diameter allows for higher flow capacity, which is essential for applications demanding increased fuel supply. However, it's important to balance this with the available space within the vehicle's engine bay. Smaller diameters might be more suitable for compact designs, ensuring the line fits without causing interference with other components.
Length is another critical aspect. The fuel line's length should be determined by the distance between the fuel tank and the engine. Longer lines may introduce additional challenges, such as increased pressure drop and potential fuel vaporization. Designers must carefully calculate the required length to minimize these issues while ensuring the line's flexibility and ease of installation.
Bend radius is a critical consideration for the line's flexibility and durability. Rubber fuel lines need to navigate through the engine bay's intricate layout, often encountering sharp bends and tight spaces. A smaller bend radius allows for better maneuverability, ensuring the line can follow the available routes without causing damage or interference. Designers should aim for a bend radius that accommodates the line's path while maintaining its structural integrity.
Meeting these specifications is essential for the overall performance and longevity of the rubber fuel line. By carefully selecting the diameter, length, and bend radius, designers can create a fuel line that efficiently transmits fuel while withstanding the mechanical stresses encountered in a vehicle's operating environment. This attention to detail ensures a reliable and safe fuel supply system.
Pro-Tec Fuel Line Cleaner: Where to Find It
You may want to see also
Manufacturing Process: Utilize techniques like extrusion or molding for precise construction
The manufacturing process of rubber fuel lines involves several key techniques to ensure precision and reliability. One of the primary methods is extrusion, which is a process where raw rubber material is forced through a die to create a continuous shape. This technique is highly effective for producing fuel lines with consistent diameters and wall thicknesses, ensuring structural integrity and minimizing the risk of leaks. The extrusion process begins with the selection of high-quality rubber compounds, which are carefully formulated to meet the specific requirements of fuel lines, including resistance to fuel degradation and flexibility. The rubber is then heated and softened, making it easier to feed through the extrusion machinery.
Once the rubber is prepared, it is fed into the extrusion machine, which consists of a feed system, a barrel, and an extrusion head. The feed system ensures a consistent supply of rubber, while the barrel provides the necessary heat and pressure to melt the rubber. The extrusion head then shapes the rubber into the desired fuel line profile. This process requires precise control over temperature, pressure, and speed to achieve the required dimensions and properties. After extrusion, the fuel lines may undergo additional processes such as cooling, curing, and surface treatment to enhance their performance and durability.
Molding is another crucial technique in the construction of rubber fuel lines. This process involves shaping the rubber material using a mold, allowing for more complex geometries and intricate designs. The molding process can be performed using various methods, such as compression molding, transfer molding, or injection molding, each offering unique advantages. In compression molding, the rubber compound is placed in a mold and heated, then compressed to form the desired shape. This method is suitable for producing fuel lines with multiple components or intricate patterns. Transfer molding involves a similar process but uses a transfer cylinder to position the rubber in the mold, ensuring precise placement.
Injection molding is often employed for high-volume production, where the rubber compound is injected into a mold under high pressure, creating a strong bond between the mold and the rubber. This technique enables the creation of fuel lines with fine details and complex structures. After molding, the fuel lines may undergo additional operations like trimming, bonding, and testing to meet the required specifications. Both extrusion and molding techniques allow for the precise construction of rubber fuel lines, ensuring they can withstand the demanding conditions of fuel transport and engine operation.
In summary, the manufacturing process of rubber fuel lines involves extrusion and molding techniques to achieve precision and reliability. Extrusion provides consistent dimensions and structural integrity, while molding enables complex designs and intricate patterns. By utilizing these processes, manufacturers can produce high-quality fuel lines that meet the necessary performance standards and ensure safe and efficient fuel delivery in various applications.
Mastering the Dorman Fuel Line Fitting: A Comprehensive Guide
You may want to see also
Testing and Inspection: Perform pressure tests and visual inspections to ensure quality
When it comes to forming rubber fuel lines, testing and inspection are crucial steps to ensure the quality and reliability of the final product. These processes help identify any potential issues or defects before the fuel line is installed, preventing costly and dangerous failures down the line. Here's a detailed guide on how to perform these essential checks:
Pressure Testing:
- Start by preparing the fuel line for the pressure test. Ensure it is properly assembled and connected to the relevant components, such as the fuel tank and engine.
- Use a calibrated pressure gauge to apply a specific amount of pressure to the fuel line. The pressure value should be determined based on the fuel line's intended application and the manufacturer's specifications.
- Observe the fuel line for any signs of leakage or damage. Check for bubbles or drops in pressure, which could indicate a weak spot or crack in the rubber material.
- If any issues are detected, the fuel line may require further examination or replacement. Pressure testing helps identify potential weaknesses, ensuring that the final product can withstand the expected fuel pressure and temperature variations.
Visual Inspections:
- Visual inspections are a critical aspect of quality control. Begin by examining the fuel line for any visible defects or irregularities. Look for cuts, tears, or any signs of damage caused by sharp objects or manufacturing imperfections.
- Check the flexibility and pliability of the rubber material. Ensure it can bend and stretch without permanent deformation, which is essential for its ability to adapt to engine vibrations and movements.
- Inspect the connections and fittings for tightness and corrosion. Loose fittings may lead to fuel leaks, while corrosion can weaken the overall structure of the fuel line.
- Pay attention to the color and texture of the rubber. Discoloration or an unusual texture could indicate the presence of contaminants or degradation, which may affect the fuel line's performance and longevity.
During the inspection process, it is essential to document any issues or defects found. Create a detailed report, noting the specific location, type, and severity of each problem. This documentation will assist in troubleshooting and determining the necessary corrective actions.
Additionally, consider performing multiple visual inspections at different stages of the manufacturing process. This proactive approach can help identify and rectify issues early on, ensuring that the final product meets the required quality standards.
By combining pressure testing and thorough visual inspections, you can effectively evaluate the integrity and performance of rubber fuel lines. This meticulous approach to testing and inspection is vital for producing high-quality fuel lines that can safely and reliably deliver fuel to an engine.
Saturn Ion Fuel Line Removal: A Step-by-Step Guide
You may want to see also
Installation Guidelines: Provide clear instructions for proper connection and routing
When installing a rubber fuel line, it's crucial to follow a systematic approach to ensure a secure and reliable connection. Here's a step-by-step guide to help you through the process:
Preparation: Begin by gathering the necessary tools and materials. You'll need the rubber fuel line, a suitable primer or adhesive, a fuel line connector kit, and a cleaning agent. Ensure the work area is clean and well-lit to facilitate a precise installation.
Cleaning and Preparation: Start by cleaning the surfaces where the fuel line will be connected. Use the cleaning agent to remove any dirt, grease, or contaminants. This step is essential to ensure a strong bond between the fuel line and the connection points. Allow the surfaces to dry completely before proceeding.
Priming and Adhesion: Apply a thin layer of primer or adhesive to the fuel line and the connection surfaces. Follow the manufacturer's instructions for the specific product you are using. Allow the primer to dry as per the recommended time. This step enhances the bond between the rubber and the metal components, ensuring a leak-free connection.
Connection and Routing: Now, you can begin the actual connection process. Start by inserting the fuel line into the connector, ensuring it is aligned correctly. Use the provided tools to secure the line in place. Route the fuel line along the desired path, considering the vehicle's design and available space. Ensure the line is not twisted or kinked, as this can affect performance and durability.
Final Adjustments: After the initial connection, make any necessary adjustments to ensure a smooth and secure fit. Check for any sharp bends or areas where the line might rub against other components. Use a suitable protective covering or sleeve if needed to safeguard the fuel line during the installation process.
Remember, proper preparation and attention to detail are key to a successful installation. Take your time, follow the manufacturer's guidelines, and seek assistance if needed to ensure a professional-grade finish.
Fuel Line Routing: Husqvarna 128L Engine Guide
You may want to see also
Frequently asked questions
A rubber fuel line is used to transport fuel from the tank to the engine in vehicles, ensuring a secure and flexible connection. It is designed to withstand the pressure and temperature variations associated with fuel flow.
The size of the fuel line should be determined by the engine's requirements and the flow rate of fuel. It is crucial to select a line with an appropriate inner diameter to handle the desired fuel volume. Common sizes range from 3/8" to 1/2" ID (inside diameter).
Yes, rubber fuel lines are available in various pressure-rated grades. For high-pressure applications, it is essential to choose a line with a suitable durometer (hardness) and reinforcement to withstand the pressure without compromising flexibility.
Installation involves several steps. First, ensure the fuel system is drained and the line is clean. Then, cut the line to the desired length and use fuel-resistant adhesive or tape to secure connections. It is recommended to use fuel line clips or brackets to attach the line to the vehicle's frame for a secure fit.
Rubber fuel lines can fail due to several factors, including age, exposure to fuel contaminants, extreme temperatures, and mechanical damage. Cracks, leaks, and reduced flexibility are signs of deterioration. Regular inspection and replacement are necessary to prevent fuel leaks and ensure engine performance.