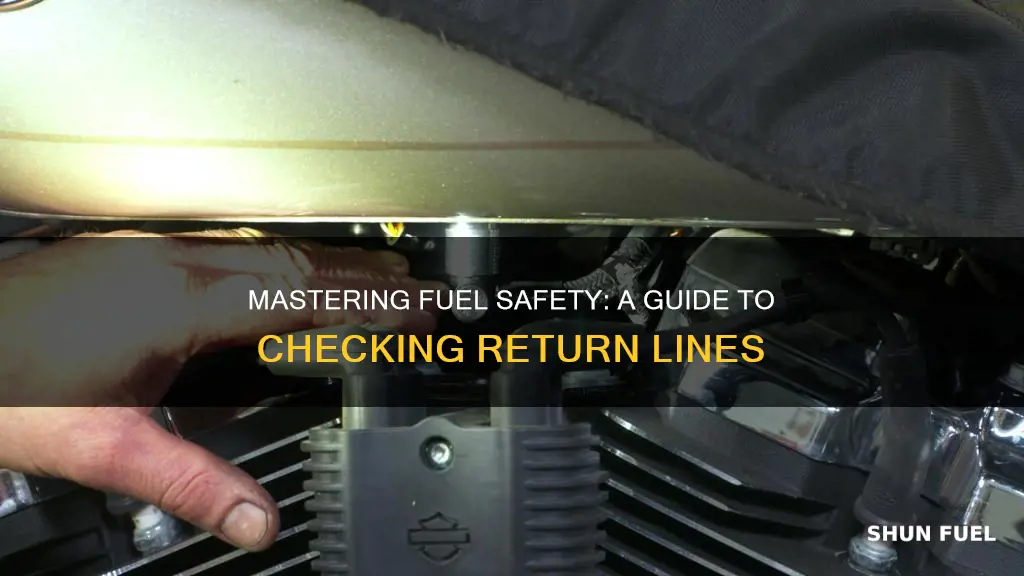
Checking the fuel return line is an important maintenance task for ensuring your vehicle's engine operates efficiently and safely. This guide will provide a step-by-step process to inspect the fuel return line, which connects the fuel tank to the engine, to identify any potential issues such as leaks, blockages, or damage. By following these instructions, you can maintain your vehicle's performance and prevent costly repairs.
What You'll Learn
- Visual Inspection: Check for cracks, leaks, and damage with the naked eye
- Pressure Testing: Use a gauge to test for leaks and proper pressure
- Fluid Analysis: Examine fuel for contamination and water content
- Flow Measurement: Measure fuel flow rate to ensure proper operation
- Ultrasonic Testing: Use sound waves to detect internal damage and blockages
Visual Inspection: Check for cracks, leaks, and damage with the naked eye
A visual inspection is a crucial step in checking the fuel return line for any issues. This method allows you to identify potential problems without the need for specialized tools or equipment. Here's a detailed guide on how to perform this inspection:
Start by locating the fuel return line, which is typically a hose or pipe that connects the fuel tank to the engine. It is usually positioned near the fuel tank and runs along the bottom of the vehicle. Inspect the line for any visible signs of damage or deterioration. Look for cracks, cuts, punctures, or any other form of physical damage. These issues could be caused by wear and tear, impact damage, or previous repairs. Pay close attention to the connections and fittings, as these areas are prone to leaking or becoming loose over time. Check for any signs of corrosion or rust, especially if the line is exposed to the elements. Corrosion can weaken the material and lead to leaks.
During the visual inspection, look for any signs of fuel leakage. Even a small amount of fuel dripping or pooling around the line could indicate a serious problem. Check the ground beneath the vehicle for any fuel stains, which might suggest a leaking return line. Inspect the surrounding area for any fuel-related odors, as these can be an early warning sign of a potential issue. Additionally, look for any visible signs of fuel accumulation or pooling near the line, as this could indicate a blockage or malfunction.
The naked eye can also detect changes in the line's appearance. Check for any discoloration or swelling along the length of the fuel return line. These changes might indicate internal damage or the presence of contaminants. If you notice any unusual patterns or variations in the line's color or texture, it could be a sign of deterioration or damage.
Remember, the goal of this visual inspection is to identify any visible defects or issues that could compromise the fuel return line's functionality. By carefully examining the line for cracks, leaks, damage, and other abnormalities, you can take the necessary steps to address any problems and ensure the safe operation of your vehicle's fuel system.
Echo PB 200 Fuel Line Size: A Comprehensive Guide
You may want to see also
Pressure Testing: Use a gauge to test for leaks and proper pressure
Pressure testing is a crucial step in ensuring the integrity of your fuel return line system. It helps identify any potential leaks or pressure-related issues that might compromise the system's performance and safety. Here's a detailed guide on how to perform this test effectively:
Gather the Necessary Tools: Before you begin, ensure you have the required equipment. You'll need a fuel pressure gauge, which is specifically designed to measure the pressure within the fuel system. It should be compatible with your vehicle's fuel type (gasoline or diesel). Additionally, have a supply of fuel additive or a fuel system cleaner to flush out any contaminants if needed.
Preparation and Safety: Start by locating the fuel return line, which is typically a small-diameter hose or tube that connects the fuel tank to the engine. Park your vehicle on a level surface and allow the engine to cool down if it has been running. This step is essential for safety, as working on a hot engine can be dangerous. Ensure you have a clear workspace and wear appropriate personal protective equipment (PPE), such as gloves and safety goggles.
Initial Inspection: Visually inspect the fuel return line for any signs of damage, cracks, or leaks. Look for any discolored or contaminated areas, as this could indicate a breach in the line. Also, check for any loose connections or fittings that might cause pressure loss. This initial inspection will help you identify potential problem areas before proceeding with the pressure test.
Pressure Testing Procedure: Attach the fuel pressure gauge to the fuel return line, ensuring a secure connection. Start the engine and allow it to idle for a few minutes to reach a stable operating temperature. Then, slowly increase the engine speed while monitoring the gauge. The pressure should stabilize at a specific value, depending on your vehicle's specifications. If the pressure drops or fluctuates, it indicates a potential leak or issue with the fuel pump or return line.
Leak Detection: After the initial pressure reading, release the pressure by slowly turning the engine off and disconnecting the gauge. Inspect the connection points and the fuel return line for any signs of fuel leakage. Even a small amount of fuel escaping can be a critical issue. If you notice any leaks, you may need to flush the system and retest.
Record and Analyze: Document the pressure reading and any observations during the test. Compare the results with the manufacturer's specifications to determine if the fuel return line is functioning correctly. If the pressure is significantly lower or higher than the expected range, further investigation is required. This process ensures that any issues are identified and addressed promptly.
Remember, pressure testing is a critical maintenance task to keep your fuel system in optimal condition. Regularly checking for leaks and proper pressure can prevent potential engine damage and ensure efficient fuel delivery.
Powerful Engine, Right Fuel Line? Size Matters!
You may want to see also
Fluid Analysis: Examine fuel for contamination and water content
Fluid analysis is a critical process in maintaining the health and performance of fuel systems, especially when it comes to identifying contamination and water content. This procedure is essential for ensuring that fuel is clean, dry, and free from any substances that could cause engine issues. Here's a step-by-step guide to examining fuel for these potential problems:
Fuel Sample Collection: Begin by carefully collecting a fuel sample from the return line, ensuring it is representative of the overall fuel quality. This might require specialized equipment or techniques, such as using a fuel sampling pump to extract a precise volume of fuel without introducing air or contaminants. Proper sampling techniques are crucial to accurate analysis.
Visual Inspection: Start with a basic visual check. Look for any visible signs of contamination, such as discoloration, sediment, or the presence of water droplets. Contaminants like water, dirt, or debris can often be seen to the naked eye, especially if they have settled at the bottom of the fuel tank or return line. This initial inspection provides a quick assessment of the fuel's condition.
Water Content Measurement: Measuring water content is a critical aspect of fluid analysis. Use a water content meter or a similar device specifically designed for this purpose. These tools can accurately determine the percentage of water present in the fuel. If the water content exceeds acceptable limits, it may indicate a breach in the fuel system's integrity or potential issues with the fuel's source.
Contaminant Analysis: To identify specific contaminants, you can employ various testing methods. One common approach is to use a fuel contamination test kit, which often includes multiple tests for different types of contaminants. These tests might involve color-changing reagents, chemical indicators, or even electronic sensors. For instance, a test for water content could use a hydrometer, while a test for sediment might involve filtering the fuel and examining the filter for particles.
Laboratory Testing: For more comprehensive analysis, send the fuel sample to a laboratory for detailed testing. Labs can provide in-depth reports on fuel quality, including the presence of various contaminants, water content, acid number, and oxidation stability. These tests are essential for a thorough understanding of the fuel's condition and can help identify any underlying issues.
By following these steps, you can effectively examine fuel for contamination and water content, ensuring that your fuel system operates optimally and minimizing the risk of engine problems caused by poor fuel quality. Regular fluid analysis is a proactive approach to maintenance, helping to extend the life of your equipment and vehicles.
Understanding Fuel Line Sizes for Tahoe Ti 9000 Lxu Models
You may want to see also
Flow Measurement: Measure fuel flow rate to ensure proper operation
To ensure the proper operation of your fuel system, it is crucial to measure the fuel flow rate, especially when checking the fuel return line. This process involves assessing the rate at which fuel flows back to the tank after it has been used by the engine. Here's a step-by-step guide to help you with this task:
Step 1: Gather the Necessary Tools
Before you begin, ensure you have the required tools for the job. You will need a fuel flow meter, which is a specialized device designed to measure the volume of fuel flowing through a line. It should be compatible with the fuel type in your system. Additionally, have a fuel gauge, a pressure gauge, and a method to temporarily block the fuel line to isolate the return line for testing.
Step 2: Locate the Fuel Return Line
Identify the fuel return line, which is typically a smaller diameter line that brings fuel from the engine back to the fuel tank. This line is crucial as it ensures that excess fuel is returned, preventing accumulation and potential engine issues. Locate the line where it connects to the fuel pump and the tank.
Step 3: Set Up the Flow Meter
Securely attach the fuel flow meter to the fuel return line. Ensure it is positioned straight and secure to get accurate readings. Turn on the flow meter and allow it to stabilize. This process might take a few minutes, and the meter will display the initial flow rate.
Step 4: Measure the Flow Rate
With the flow meter set up, start the engine and allow it to run for a period recommended by the flow meter's instructions. Typically, this is around 10-15 minutes. During this time, the flow meter will continuously display the fuel flow rate. Record this rate, as it should be within a specific range for optimal engine performance.
Step 5: Compare and Analyze
Compare the measured flow rate with the expected or recommended range for your vehicle's make and model. If the flow rate is significantly higher or lower than the specified value, it may indicate a problem with the fuel return line or the overall fuel system. This measurement is vital in diagnosing potential issues and ensuring the engine receives the correct amount of fuel.
Remember, accurate flow measurement is essential for maintaining engine health and performance. It allows for early detection of potential fuel system problems, ensuring your vehicle operates efficiently and reliably.
Mastering Fuel Line Bleeding: A Step-by-Step Guide for New Holland Tractors
You may want to see also
Ultrasonic Testing: Use sound waves to detect internal damage and blockages
Ultrasonic testing is a non-destructive method that utilizes high-frequency sound waves to inspect and evaluate the internal condition of various components, including fuel return lines. This technique is particularly useful for identifying hidden damage, blockages, or defects that might not be visible through traditional visual inspections. By employing sound waves, ultrasonic testing can provide valuable insights into the structural integrity and functionality of fuel return lines, ensuring optimal performance and safety.
The process begins with the application of a coupling medium, typically a gel or a special ultrasonic couplant, between the ultrasonic transducer and the surface of the fuel return line. This coupling agent ensures efficient energy transfer and helps to eliminate air gaps, which can interfere with the sound wave propagation. The transducer, a small device with a piezoelectric crystal, is then placed on the surface, emitting high-frequency sound waves into the material. These sound waves travel through the fuel return line, reflecting off any internal structures or defects.
As the sound waves encounter different materials or defects within the fuel return line, they create echoes, which are detected by the transducer. The time it takes for the sound waves to travel through the material and back to the transducer is measured, allowing for the calculation of the distance to the defect. This information is crucial in identifying the location and severity of any internal damage or blockages. Advanced ultrasonic testing systems can also analyze the shape and characteristics of the echoes, providing detailed information about the nature of the defect.
One of the key advantages of ultrasonic testing is its ability to detect internal defects without causing any damage to the fuel return line. Unlike some other inspection methods, ultrasonic testing does not involve physical contact or the use of chemicals, making it a safe and non-invasive technique. This is particularly important in fuel systems, where any damage or blockage could lead to performance issues or safety hazards. By identifying and addressing these problems early on, ultrasonic testing plays a vital role in maintaining the efficiency and reliability of fuel return lines.
Ultrasonic testing can be performed in various environments, including both laboratory and in-field settings. In-field testing is especially useful for immediate inspections during maintenance or troubleshooting, allowing for quick identification of issues. The technique is highly versatile and can be adapted to different fuel return line materials and geometries, making it a valuable tool for a wide range of applications. With its ability to provide detailed internal information, ultrasonic testing ensures that fuel return lines are thoroughly examined, contributing to the overall safety and performance of the vehicle or system.
Auto Body Repair: Can Shops Fix Fuel Lines?
You may want to see also