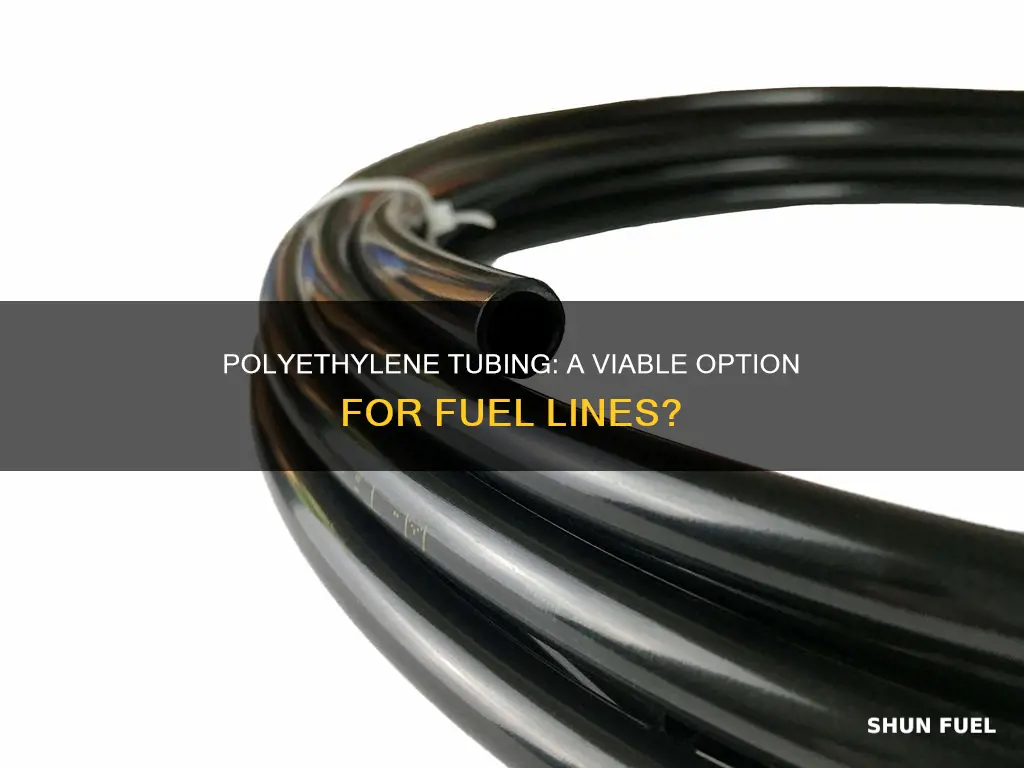
Polyethylene tubing is a versatile material commonly used in various applications, but its suitability for fuel lines is a topic of interest for many. This paragraph aims to explore whether polyethylene tubing can be effectively utilized for fuel lines, considering its properties and potential advantages or limitations in this specific context.
Characteristics | Values |
---|---|
Material | Polyethylene (PE) |
Flexibility | High flexibility, allowing for easy installation and bending around engine components |
Temperature Resistance | Typically suitable for temperatures ranging from -40°F to 140°F (-40°C to 60°C) |
Chemical Resistance | Resistant to most fuels, including gasoline, diesel, and ethanol blends |
Pressure Rating | Varies depending on the specific PE grade and wall thickness, but generally adequate for fuel lines |
Color | Often black or white, depending on the manufacturer |
Cost | Generally affordable compared to other fuel line materials |
Availability | Widely available in hardware stores and automotive supply stores |
Installation | Can be cut and spliced using standard tools, making installation relatively straightforward |
Maintenance | Requires minimal maintenance, with no need for regular lubrication |
Durability | Abrasion-resistant and can withstand the rigors of fuel transport |
Environmental Impact | Generally considered environmentally friendly due to its recyclability |
What You'll Learn
- Durability: Polyethylene tubing is durable and resistant to fuel line wear and tear
- Flexibility: It offers flexibility, making it easy to route and bend
- Temperature Tolerance: Suitable for a wide temperature range, ensuring fuel line integrity
- Chemical Resistance: Resistant to fuel chemicals, preventing degradation and leaks
- Cost-Effective: An affordable alternative to traditional fuel line materials
Durability: Polyethylene tubing is durable and resistant to fuel line wear and tear
Polyethylene tubing is an excellent choice for fuel lines due to its exceptional durability and resistance to wear and tear, making it a reliable and long-lasting solution for various applications. This type of tubing is specifically designed to withstand the demanding conditions often encountered in fuel systems. One of the key advantages of polyethylene is its ability to resist abrasion, which is crucial in fuel lines where the material is constantly exposed to the elements and potential hazards. The tubing's robust construction ensures that it can handle the physical stresses of fuel transportation without compromising its structural integrity.
The durability of polyethylene tubing is attributed to its chemical composition and manufacturing process. It is engineered to have a high degree of impact resistance, which means it can absorb and distribute the force of any potential collisions or impacts without breaking or deforming. This is particularly important in fuel lines, as it ensures that the tubing can withstand accidental bumps or damage during installation or maintenance without leaking or failing. Additionally, polyethylene's resistance to UV radiation and ozone degradation makes it suitable for outdoor use, providing long-term protection against environmental factors that could otherwise cause deterioration.
In fuel line applications, polyethylene tubing's durability is further enhanced by its flexibility and ease of installation. It can be easily bent and manipulated to fit various routes and contours, making it adaptable to different vehicle designs and layouts. This flexibility, combined with its strength, allows for efficient and secure fuel line routing, ensuring a reliable supply of fuel to the engine without the risk of damage or breakage. The tubing's ability to withstand temperature fluctuations is also a significant advantage, as it can maintain its structural integrity in both hot and cold environments, further contributing to its overall durability.
Furthermore, polyethylene's resistance to corrosion is a critical factor in its durability. Unlike some other materials, polyethylene does not react with fuels or other chemicals commonly found in fuel systems, making it an ideal choice for long-term use. This resistance to corrosion ensures that the tubing remains free from degradation, maintaining its structural integrity and functionality over extended periods. As a result, polyethylene fuel lines are less prone to leaks, cracks, or other forms of damage that could compromise the fuel supply, making it a highly reliable option for various vehicle and equipment applications.
In summary, polyethylene tubing's durability and resistance to wear and tear make it an excellent material for fuel lines. Its ability to withstand abrasion, impact, and environmental factors, coupled with its flexibility and corrosion resistance, ensures a reliable and long-lasting solution for fuel transportation. By choosing polyethylene, users can have confidence in the performance and longevity of their fuel lines, contributing to a safer and more efficient operation of vehicles and equipment.
Optimizing Fuel Delivery: Choosing the Right Line for Your 500HP EFI Engine
You may want to see also
Flexibility: It offers flexibility, making it easy to route and bend
Polyethylene tubing is an excellent choice for fuel lines due to its remarkable flexibility, which is a crucial factor in the design and installation of fuel systems. This material's inherent flexibility allows for easy routing and bending, making it highly adaptable to various vehicle architectures and engine configurations. When compared to traditional rigid metal or plastic fuel lines, polyethylene tubing provides a more versatile and user-friendly solution.
The flexibility of polyethylene tubing is particularly advantageous during the installation process. It can be easily manipulated to navigate around tight spaces, sharp corners, and complex engine compartments without the risk of damage or kinking. This characteristic ensures that fuel lines can be installed efficiently, reducing the time and effort required for the job. Additionally, the flexibility of the tubing allows for a more customized and tailored fit, ensuring optimal performance and minimizing the chances of fuel leaks or system failures.
In terms of practical application, polyethylene tubing's flexibility is evident in its ability to accommodate movement. Vehicles experience various vibrations and shocks during operation, and the tubing's pliability helps absorb these movements, reducing the stress on the fuel lines. This feature is especially important in high-performance or off-road vehicles, where fuel lines may be subjected to more extreme conditions. The flexibility of polyethylene tubing ensures that the fuel system remains intact and functional, even when the vehicle encounters challenging terrain or aggressive driving conditions.
Furthermore, the ease of routing and bending provided by polyethylene tubing simplifies the overall fuel system design. Engineers and mechanics can create more efficient and aesthetically pleasing layouts, optimizing the fuel delivery process. This flexibility in design can lead to improved engine performance and a more reliable fuel system, as the tubing can be strategically positioned to minimize resistance and ensure a smooth flow of fuel.
In summary, the flexibility of polyethylene tubing is a key advantage when considering its use for fuel lines. Its adaptability, ease of installation, and ability to withstand vehicle movement make it an ideal choice for fuel systems. By offering flexibility, polyethylene tubing ensures a reliable and efficient fuel delivery process, contributing to the overall performance and longevity of the vehicle's engine.
Mastering Fuel Line Maintenance: A Guide to Priming Bulb Replacement
You may want to see also
Temperature Tolerance: Suitable for a wide temperature range, ensuring fuel line integrity
Polyethylene tubing is an excellent choice for fuel lines due to its remarkable temperature tolerance, making it a reliable and versatile option for various applications. This material can withstand a wide range of temperatures, from extremely low to high, ensuring the integrity and performance of the fuel line.
The temperature tolerance of polyethylene is a critical factor in its suitability for fuel lines. It can handle the extreme cold temperatures often encountered in colder climates, preventing brittleness and cracking that could lead to fuel leaks. In contrast, it can also endure high temperatures, which is essential for applications where fuel lines are exposed to intense heat, such as in high-performance engines or industrial settings. This wide temperature range ensures that the fuel line remains flexible and maintains its structural integrity, even when subjected to varying environmental conditions.
One of the key advantages of using polyethylene tubing for fuel lines is its ability to resist thermal expansion and contraction. This property is crucial as it allows the fuel line to maintain its shape and fit without becoming brittle or losing its sealing capabilities. Unlike some other materials, polyethylene does not become brittle at low temperatures, ensuring that the fuel line remains pliable and functional even in freezing conditions.
Additionally, polyethylene's temperature tolerance contributes to its overall durability. It is resistant to UV radiation and ozone, which can cause degradation in other materials over time. This durability ensures that the fuel line can withstand long-term exposure to harsh environmental conditions, making it a reliable choice for outdoor or long-term installations.
In summary, polyethylene tubing's temperature tolerance is a significant advantage for fuel line applications. Its ability to withstand a wide range of temperatures, resist thermal expansion, and maintain durability ensures that the fuel line remains intact and functional, providing a safe and efficient fuel delivery system. This makes polyethylene an ideal material for various fuel line installations, offering peace of mind and reliable performance.
Troubleshooting Clogged Fuel Lines: A Guide for JD L 120 Owners
You may want to see also
Chemical Resistance: Resistant to fuel chemicals, preventing degradation and leaks
The use of polyethylene tubing for fuel lines is a practical and reliable solution for many applications, especially when considering its chemical resistance properties. Polyethylene, a type of thermoplastic polymer, offers a robust and durable option for fuel transportation and distribution systems. One of its key advantages is its inherent resistance to various chemicals commonly found in fuels.
In the context of fuel lines, chemicals such as gasoline, diesel, aviation fuel, and biofuels can be highly corrosive to other materials. However, polyethylene tubing is specifically engineered to withstand these fuel chemicals, ensuring the integrity of the fuel system. This chemical resistance is crucial as it prevents the degradation of the tubing over time, which could lead to fuel leaks, contamination, and potential safety hazards.
The resistance of polyethylene to fuel chemicals is attributed to its molecular structure. The polymer's long-chain molecules form a strong, flexible network that resists the penetration of fuel chemicals. This property is particularly important in fuel lines, where the tubing must endure constant exposure to varying fuel compositions and temperatures. By withstanding these harsh conditions, polyethylene ensures that the fuel remains contained and secure within the tubing.
Furthermore, the chemical resistance of polyethylene tubing contributes to the overall safety and reliability of fuel systems. It minimizes the risk of fuel leaks, which can cause environmental damage, equipment corrosion, and potential fires or explosions. This is especially critical in industrial settings, aviation, and marine applications where fuel handling and transportation are prevalent.
In summary, polyethylene tubing's chemical resistance to fuel chemicals is a vital feature that ensures the longevity and safety of fuel lines. Its ability to prevent degradation and leaks makes it an ideal choice for fuel transportation and distribution, providing a reliable and cost-effective solution for various industries. This property, combined with its flexibility and durability, positions polyethylene as a preferred material for fuel-related applications.
Unveiling the Causes: Why Fuel Line Leaks Happen
You may want to see also
Cost-Effective: An affordable alternative to traditional fuel line materials
The use of polyethylene tubing as a fuel line is an innovative and cost-effective solution for various applications, especially in the automotive and marine industries. This material offers a compelling alternative to traditional fuel lines, which can be expensive and prone to degradation over time. One of the primary advantages of polyethylene is its affordability, making it an attractive option for those seeking a budget-friendly solution without compromising on quality.
Polyethylene tubing is known for its flexibility, allowing it to navigate through tight spaces and complex engine layouts with ease. This characteristic is particularly useful when retrofitting or repairing older vehicles where space is limited. The material's flexibility also reduces the risk of damage during installation, further contributing to cost savings. Additionally, polyethylene's lightweight nature makes it easier to handle, reducing labor costs and installation time.
In terms of durability, polyethylene fuel lines can withstand the rigors of everyday use. They are resistant to fuel-related chemicals, ensuring that the material does not degrade or become brittle over time. This resistance is crucial for maintaining the integrity of the fuel system and preventing potential leaks or failures. Furthermore, polyethylene's ability to resist kinking and crushing makes it a reliable choice, especially in harsh environments or when exposed to vibrations.
Another cost-saving aspect is the ease of installation. Polyethylene tubing can be cut and fitted with various connectors and fittings, allowing for a straightforward and efficient installation process. This simplicity reduces the time and resources required for setup, making it a practical choice for both professionals and DIY enthusiasts. Moreover, the material's compatibility with a wide range of fuels, including gasoline, diesel, and even biofuels, further enhances its versatility and cost-effectiveness.
For those seeking an affordable and reliable fuel line solution, polyethylene tubing presents a compelling case. Its flexibility, durability, and ease of installation make it a practical choice, especially for applications where traditional fuel lines may be less suitable. By considering the long-term cost benefits and the material's performance, users can make an informed decision, ensuring a cost-effective and efficient fuel system.
Understanding the Fuel Tank Return Line: A Comprehensive Guide
You may want to see also
Frequently asked questions
Yes, polyethylene tubing can be used for fuel lines, but it's important to choose the right type and thickness to ensure it can withstand the pressure and temperature changes associated with fuel. High-density polyethylene (HDPE) is a popular choice for fuel lines due to its chemical resistance and flexibility.
Polyethylene tubing offers several benefits for fuel lines. It is lightweight, easy to install, and has good resistance to fuel-related chemicals. Additionally, it can absorb vibrations, reducing the risk of fuel leaks. However, it's crucial to select a grade that meets the specific requirements of the fuel type and operating conditions.
While polyethylene tubing is a reliable option, it may not be suitable for high-pressure applications. It can become brittle over time, especially at lower temperatures, which could lead to cracks and fuel leaks. Proper installation, including the use of appropriate fittings and regular inspections, is essential to ensure the system's integrity.