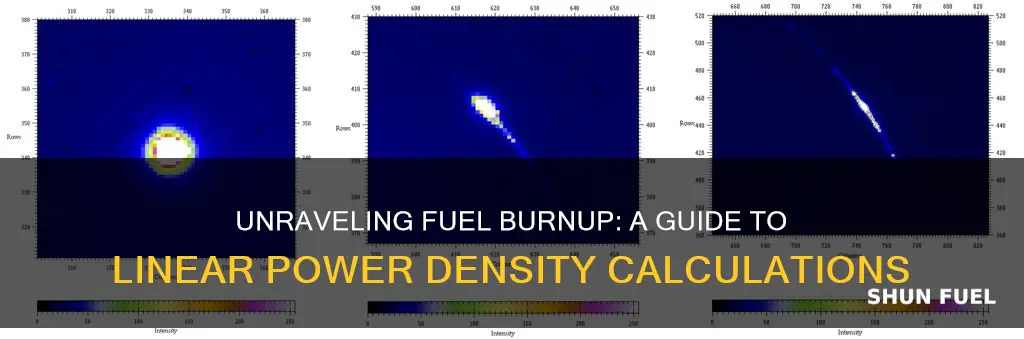
Calculating fuel burnup from linear power density is a crucial aspect of nuclear reactor design and operation. This process involves determining the rate at which fuel is consumed and converted into energy within the reactor core. By understanding the relationship between power density and fuel burnup, engineers can optimize reactor performance, ensure fuel efficiency, and enhance safety measures. This paragraph will delve into the methods and considerations involved in calculating fuel burnup, providing a comprehensive guide for professionals in the nuclear energy field.
What You'll Learn
- Power Density Definition: Understand power density as power per unit area, a key concept for fuel burnup calculations
- Fuel Geometry: Shape and size of fuel pellets and rods directly impact linear power density and burnup
- Fuel Material: Different fuel materials have varying thermal conductivity and specific heat, affecting power density
- Coolant Flow: Efficient coolant flow is crucial for heat removal, influencing power density and burnup
- Burnup Calculation Models: Use empirical or computational models to estimate fuel burnup based on power density
Power Density Definition: Understand power density as power per unit area, a key concept for fuel burnup calculations
Power density is a fundamental concept in understanding the performance and efficiency of systems, especially in the context of energy production and utilization. It is defined as the power output per unit area and is typically measured in watts per square meter (W/m²). This metric is crucial when analyzing and designing systems that involve energy conversion, such as power plants, solar panels, or even nuclear reactors.
In the context of fuel burnup calculations, power density plays a pivotal role. Fuel burnup refers to the process of converting nuclear fuel into energy through fission reactions, and it is a critical parameter in nuclear reactor design and operation. Linear power density, which is the power output per unit length, is directly related to the fuel's burnup rate. Higher power density in a fuel element means a more rapid conversion of fuel into energy, leading to increased burnup.
To calculate fuel burnup from linear power density, one must consider the geometry and arrangement of the fuel elements within the reactor core. The power density distribution along the length of the fuel element is essential. By integrating the power density over the length of the fuel element, you can determine the total power output and, subsequently, the burnup rate. This calculation is vital for reactor operators to ensure that the fuel is utilized efficiently and to predict when refueling or replacement is necessary.
Understanding power density is key to optimizing the performance of nuclear reactors. It allows engineers to design fuel elements with specific power densities to meet desired burnup rates. This optimization ensures that the reactor operates within safe limits while maximizing energy output. Moreover, it helps in managing the fuel cycle, as it provides insights into the fuel's usage and remaining life.
In summary, power density, as the power output per unit area, is a critical concept for fuel burnup calculations. It enables engineers and scientists to design and operate nuclear systems efficiently, ensuring optimal energy production while managing fuel resources effectively. By applying power density calculations, professionals can make informed decisions regarding reactor design, fuel utilization, and overall system performance.
Fuel Line Material: Metal or Rubber? Unveiling the Truth
You may want to see also
Fuel Geometry: Shape and size of fuel pellets and rods directly impact linear power density and burnup
The shape and size of fuel pellets and rods play a crucial role in determining the linear power density and overall burnup of a fuel assembly. Linear power density, often referred to as power per unit length, is a critical parameter in nuclear reactor design and operation. It represents the power generated per unit length of the fuel, and it directly influences the fuel's performance and efficiency. When considering fuel geometry, engineers aim to optimize the arrangement of fuel pellets and rods to maximize power output while ensuring safe and efficient operation.
One key aspect of fuel geometry is the pellet shape. Fuel pellets, which are typically cylindrical or spherical, can be designed with specific dimensions to achieve desired power density. For instance, a more compact pellet shape with a higher surface-to-volume ratio can result in a higher linear power density. This is because a smaller pellet can accommodate a higher power output per unit volume, allowing for a more efficient use of space within the fuel assembly. However, it's important to note that the choice of pellet shape also depends on the specific nuclear fuel material and its mechanical properties.
The size of fuel pellets and rods is another critical factor. Larger pellets or rods can provide a higher surface area, which can be beneficial for heat transfer and cooling. This is particularly important in maintaining the fuel's temperature and preventing overheating. By increasing the size, the fuel can accommodate a higher power output without compromising its structural integrity. However, larger pellets may also lead to increased fuel volume, which could impact the overall fuel assembly design and packing efficiency.
Furthermore, the arrangement of fuel pellets and rods within the assembly is essential. The packing density, or the ratio of fuel volume to the total assembly volume, influences the linear power density. A higher packing density can result in a more compact and efficient fuel assembly, allowing for a higher power output per unit length. However, it's crucial to maintain a balance between packing density and fuel integrity to ensure the stability and safety of the reactor.
In summary, the fuel geometry, including the shape and size of pellets and rods, significantly impacts linear power density and burnup. Engineers must carefully consider these factors to optimize fuel performance, maximize power output, and ensure the safe operation of nuclear reactors. Understanding the relationship between fuel geometry and power density is essential for designing efficient and reliable fuel assemblies.
Locate the Fuel Line on Your Deere X500
You may want to see also
Fuel Material: Different fuel materials have varying thermal conductivity and specific heat, affecting power density
The thermal properties of fuel materials play a critical role in determining their performance within a reactor environment. Thermal conductivity and specific heat capacity are two key factors that significantly influence power density, which in turn affects the overall fuel burnup. These properties are essential to understand as they directly impact how efficiently heat is transferred from the fuel to the surrounding coolant or containment structure.
Thermal conductivity is a measure of a material's ability to conduct heat. Materials with high thermal conductivity, such as uranium dioxide (UO2), efficiently transfer heat, allowing for higher power densities. This is particularly important in reactor design as it enables the fuel to operate at higher temperatures without excessive heat buildup. On the other hand, materials with lower thermal conductivity, like some types of uranium-plutonium oxides, may require more complex cooling systems to maintain optimal operating conditions.
Specific heat capacity, another crucial property, represents the amount of heat energy required to raise the temperature of a unit mass of a substance by one degree Celsius. Materials with higher specific heat capacities can absorb and store more heat, which is beneficial for moderating temperature fluctuations within the reactor. This property is especially relevant in reactor designs where maintaining a stable temperature is essential for safety and efficiency. For instance, fuels with higher specific heat capacities might be preferred in fast breeder reactors, where rapid temperature changes could occur.
The variation in thermal conductivity and specific heat capacity among different fuel materials directly translates to differences in power density. Power density is a measure of the energy output per unit volume of fuel. Materials with higher thermal conductivity and specific heat capacity can support higher power densities, allowing for more efficient energy production. This is a critical consideration in reactor design, as it influences the overall size and complexity of the reactor system.
In summary, the choice of fuel material is a critical aspect of reactor design, as it directly impacts power density and, consequently, fuel burnup. Understanding the thermal properties of various fuel materials enables engineers to select the most suitable options for specific reactor applications, ensuring optimal performance, safety, and efficiency. This knowledge is essential for the development of advanced reactor technologies and the optimization of existing nuclear power systems.
Spraying Fuel Lines: A Protective Coating Solution
You may want to see also
Coolant Flow: Efficient coolant flow is crucial for heat removal, influencing power density and burnup
Efficient coolant flow is a critical aspect of nuclear reactor design and operation, especially when considering the relationship between coolant flow rate, heat removal, and the performance of fuel rods. In the context of calculating fuel burnup from linear power density, understanding the coolant's role is essential. Coolant, typically water or a liquid metal, serves as a medium to absorb heat generated by the fission process and subsequently transfer it away from the fuel rods to prevent overheating and potential damage.
The efficiency of coolant flow directly impacts the overall heat removal capacity of the reactor. When coolant flows optimally, it can effectively carry away the generated heat, allowing for a higher power output without compromising the integrity of the fuel. This is particularly important in high-power-density applications, where the fuel experiences intense thermal stresses. Efficient coolant flow ensures that the fuel's surface temperature remains within safe limits, thereby extending its operational life and maximizing burnup.
The relationship between coolant flow and burnup can be understood through the concept of heat transfer coefficients. These coefficients describe the rate at which heat is transferred from the fuel to the coolant. Higher heat transfer coefficients indicate more efficient heat removal, which, in turn, allows for higher power densities and, consequently, increased fuel burnup. Engineers and scientists use these coefficients to design reactor systems that optimize coolant flow, ensuring the fuel's performance meets the desired specifications.
In practice, achieving efficient coolant flow involves several considerations. One crucial factor is the design of the coolant channels and passages within the reactor core. These channels must be optimized to provide a smooth and consistent flow path for the coolant, minimizing any potential flow disruptions or dead zones. Additionally, the coolant's inlet and outlet temperatures play a significant role, as temperature differentials drive the heat transfer process. Maintaining an appropriate temperature gradient ensures that the coolant absorbs heat effectively without overheating itself.
Furthermore, the pressure and velocity of the coolant flow are critical parameters. Proper flow rate management ensures that the coolant's kinetic energy is sufficient to carry away the generated heat without causing excessive wear and tear on the fuel and reactor components. Advanced control systems and monitoring equipment are employed to maintain optimal coolant flow conditions, adapting to variations in power density and other operating parameters. By optimizing coolant flow, nuclear engineers can enhance the overall efficiency of the reactor, enabling higher fuel burnup rates while ensuring the safety and longevity of the system.
Understanding Impulse Fuel Lines: Powering Chainsaws Efficiently
You may want to see also
Burnup Calculation Models: Use empirical or computational models to estimate fuel burnup based on power density
The calculation of fuel burnup is a critical aspect of nuclear reactor design and operation, and it can be estimated using various models, both empirical and computational. These models provide a way to predict the rate at which nuclear fuel undergoes fission, which is directly related to the power density of the reactor. Power density, often expressed as power per unit area, is a key parameter in these calculations as it influences the fuel's performance and longevity.
Empirical models are derived from experimental data and historical fuel performance data. These models establish correlations between power density and fuel burnup, allowing for the estimation of burnup based on known power density values. For instance, researchers might collect data from multiple reactor designs and operating conditions, plotting power density against burnup to identify trends. This empirical approach can be useful when specific reactor parameters are known, providing a direct relationship between power density and fuel consumption.
One common empirical model is the 'Power-Burnup Relationship', which assumes a linear correlation between power density and burnup. This model is relatively simple and can be expressed as a mathematical equation: Burnup = m * Power Density + b, where 'm' is the slope and 'b' is the y-intercept. By adjusting these parameters based on experimental data, engineers can estimate fuel burnup for different power density scenarios. However, it's important to note that this linear relationship may not hold true for all reactor types and fuel materials, requiring careful calibration and validation.
Computational models, on the other hand, are based on physical principles and mathematical equations that simulate the complex processes within the reactor. These models can account for various factors influencing fuel burnup, such as fuel composition, reactor geometry, and thermal-hydraulic conditions. Computational fluid dynamics (CFD) simulations, for example, can predict the heat transfer and fluid flow within the reactor, which is crucial for understanding fuel behavior under different power density conditions. By solving sets of governing equations, these models provide detailed insights into fuel performance, allowing for more accurate burnup predictions.
When using computational models, engineers often employ finite element analysis (FEA) to discretize the reactor into smaller elements, enabling the simulation of heat transfer and fuel behavior at a microscopic level. This approach requires detailed knowledge of the reactor's design and material properties. The output of these simulations can be used to validate empirical models or to directly estimate fuel burnup, especially when empirical data is scarce or unavailable for specific reactor configurations.
In summary, both empirical and computational models play essential roles in estimating fuel burnup based on power density. Empirical models provide a direct correlation, while computational models offer a more comprehensive understanding by considering multiple factors. The choice of model depends on the available data, reactor specifics, and the level of accuracy required for a particular application.
Fuel Line Degradation: A Hidden Threat in Transmission Fluids
You may want to see also
Frequently asked questions
Fuel burnup refers to the process of consuming nuclear fuel in a reactor, resulting in the production of fission products and the release of energy. Linear power density is a measure of the power output per unit length of the fuel, and it directly influences the fuel burnup rate.
To calculate fuel burnup, you can use the following formula: Burnup (B) = Linear Power Density (P) * Time (t) / Fuel Cross-Section (σ). This equation represents the amount of fuel consumed per unit area over time, considering the power output and the fuel's cross-sectional area.
The fuel cross-section (σ) is a crucial factor as it represents the probability of a neutron interaction with the fuel. It depends on the fuel composition and its microscopic structure. A higher cross-section means more interactions, affecting the fuel burnup rate.
Higher linear power density results in a more rapid fuel burnup. This is because a higher power output per unit length means more energy is deposited in the fuel, leading to increased neutron interactions and faster fuel consumption.
Yes, it's important to consider the reactor's design and operating conditions. Factors like fuel enrichment, moderator temperature, and reactor geometry can influence the linear power density and, consequently, the fuel burnup. These factors should be accounted for in practical applications to ensure accurate calculations.