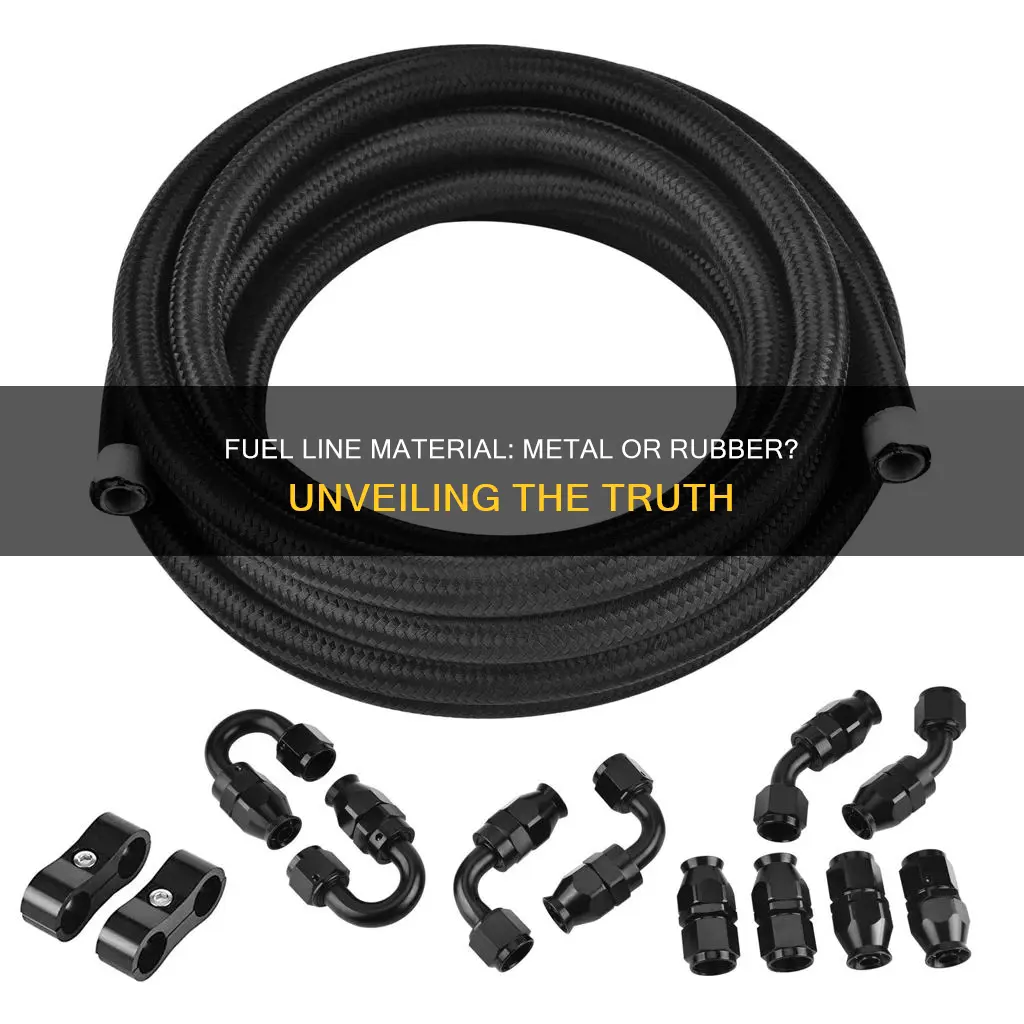
The fuel line, a crucial component in any vehicle's fuel system, is an often-overlooked yet vital part of the engine's performance and safety. It is the conduit that carries fuel from the tank to the engine, and the question of whether it is made of metal or rubber is an important one. Both materials have their advantages and disadvantages, and understanding these can help in making informed decisions about vehicle maintenance and upgrades.
Characteristics | Values |
---|---|
Material | Rubber |
Flexibility | High flexibility, allowing for movement with the engine and vibrations |
Durability | Resistant to heat, oil, and fuel, ensuring long-lasting performance |
Temperature Tolerance | Can withstand a wide range of temperatures, from cold starts to high engine operation |
Corrosion Resistance | Not susceptible to corrosion, maintaining structural integrity over time |
Cost | Generally more affordable compared to metal alternatives |
Installation | Easier to install due to its pliability and ability to conform to engine components |
Maintenance | Requires regular inspection for cracks or damage, but is less prone to leaks |
Weight | Lighter than metal, reducing overall engine weight |
Compatibility | Compatible with various fuel types, including gasoline and diesel |
What You'll Learn
- Material Composition: Understanding the materials used in fuel lines, focusing on metal and rubber options
- Durability Comparison: Analyzing the durability of metal vs. rubber fuel lines in various conditions
- Flexibility Analysis: Examining the flexibility of fuel lines, considering metal and rubber variations
- Corrosion Resistance: Investigating how metal and rubber fuel lines resist corrosion over time
- Cost-Effectiveness: Comparing the cost of metal and rubber fuel lines for different applications
Material Composition: Understanding the materials used in fuel lines, focusing on metal and rubber options
The composition of fuel lines is a critical aspect of vehicle maintenance, as it directly impacts the performance and longevity of the fuel system. When it comes to fuel lines, the materials used can vary, but the two primary options are metal and rubber. Understanding the characteristics and applications of these materials is essential for making informed decisions about fuel line replacements or upgrades.
Metal fuel lines, often made from materials like steel or aluminum, offer several advantages. Firstly, metal is known for its durability and strength. It can withstand high pressure and temperature changes, making it ideal for fuel lines that carry high-octane fuels or operate in extreme environments. Metal lines are less susceptible to corrosion and are less likely to degrade over time, ensuring a longer-lasting solution. Additionally, metal fuel lines provide excellent flexibility, allowing them to navigate through tight spaces and engine compartments without kinking or bending. This flexibility is crucial for maintaining a secure and efficient fuel supply.
On the other hand, rubber fuel lines have their own set of benefits. Rubber is a popular choice due to its flexibility and resistance to abrasion. It can accommodate slight movements and vibrations within the engine bay without compromising the fuel flow. Rubber lines are also known for their ability to absorb and dampen vibrations, reducing engine noise and improving overall performance. Furthermore, rubber is lightweight, making it easier to install and work with compared to metal. This material is often used for fuel lines in older vehicles or those with more limited engine spaces.
The choice between metal and rubber fuel lines depends on various factors, including the vehicle's age, engine requirements, and environmental conditions. Modern vehicles often utilize a combination of both materials. For instance, metal lines might be employed for critical high-pressure applications, while rubber lines handle the fuel supply to the engine. This hybrid approach ensures optimal performance and longevity.
In summary, understanding the material composition of fuel lines is vital for vehicle owners and mechanics alike. Metal and rubber each bring unique advantages to the table, and the decision should be based on specific vehicle needs. Whether it's the durability of metal or the flexibility and vibration absorption of rubber, choosing the right material ensures a reliable and efficient fuel system.
The Ultimate Guide to Thread Sealants for Fuel Lines
You may want to see also
Durability Comparison: Analyzing the durability of metal vs. rubber fuel lines in various conditions
The debate between metal and rubber fuel lines has long been a topic of discussion among vehicle enthusiasts and mechanics. When it comes to durability, both materials have their own advantages and disadvantages, and understanding these can help in making an informed decision for your vehicle's fuel system.
Metal fuel lines, often made of steel or aluminum, offer exceptional strength and rigidity. They are less susceptible to damage from external factors such as temperature changes, UV radiation, and chemical exposure. Metal lines can withstand high-pressure environments and are less prone to leaks or punctures. This makes them ideal for high-performance vehicles or those operating in extreme conditions. However, metal fuel lines can be more rigid and less flexible, which might lead to issues with installation and potential damage to the fuel tank or engine components during the process.
On the other hand, rubber fuel lines have been a traditional choice for many years due to their flexibility and ease of installation. They are more resistant to abrasion and can accommodate slight movements within the engine bay without cracking or breaking. Rubber lines are also more flexible, making them less likely to cause damage during installation. However, rubber is more susceptible to degradation over time, especially when exposed to sunlight, heat, and certain chemicals in fuel. This can lead to cracking, brittleness, and potential leaks, which may result in fuel loss and engine performance issues.
In terms of durability, metal fuel lines generally outperform rubber lines in most conditions. Metal's superior strength and resistance to environmental factors make it a reliable choice, especially for high-performance or modified vehicles. However, rubber fuel lines have their place in certain applications. For instance, in classic or vintage cars, where the engine bay might have limited space and flexibility is crucial, rubber lines can be a practical solution. Additionally, in environments with minimal exposure to harsh chemicals or extreme temperatures, rubber lines can provide a cost-effective and reliable option.
The choice between metal and rubber fuel lines ultimately depends on the specific requirements of your vehicle and the conditions it will operate in. For high-performance or modified vehicles, metal lines offer superior durability and peace of mind. Meanwhile, rubber lines are more versatile and can be a suitable choice for various applications, especially where flexibility and ease of installation are key considerations.
Pipe Thread Sealant: Essential for Fuel Line Maintenance?
You may want to see also
Flexibility Analysis: Examining the flexibility of fuel lines, considering metal and rubber variations
The flexibility of fuel lines is a critical aspect of vehicle performance and safety, especially in the context of fuel delivery systems. When considering the composition of fuel lines, two primary materials come into play: metal and rubber. Each material offers distinct advantages and characteristics that influence the overall flexibility of the fuel line.
Metal fuel lines, often made from materials like steel or aluminum, are known for their durability and strength. These lines are rigid and offer excellent resistance to pressure and external forces. While metal lines provide a robust connection, they may lack the flexibility required for certain vehicle applications. Metal's rigidity can make it challenging to navigate around tight spaces or accommodate slight movements within the engine compartment. This lack of flexibility might lead to potential issues during installation or over time as the vehicle ages.
On the other hand, rubber fuel lines offer a different set of advantages. Rubber is inherently flexible, allowing the fuel line to bend and adjust to the vehicle's contours. This flexibility is crucial for maintaining a secure connection between the fuel tank and the engine, especially in areas with limited space. Rubber's elasticity also helps absorb vibrations and shocks, reducing the risk of fuel line damage during the vehicle's operation. Additionally, rubber is resistant to corrosion and can withstand the chemical properties of fuel, ensuring a reliable and long-lasting connection.
The choice between metal and rubber fuel lines depends on various factors, including vehicle design, engine requirements, and environmental conditions. In high-performance vehicles or those operating in extreme temperatures, metal lines might be preferred for their ability to withstand intense conditions. However, for everyday use, especially in compact cars or older models, rubber fuel lines often provide the necessary flexibility and reliability.
In summary, the flexibility of fuel lines is a result of the material used, with rubber offering superior flexibility and adaptability. Metal lines, while durable, may not provide the same level of flexibility. Understanding these variations is essential for mechanics and vehicle owners to ensure optimal fuel delivery and overall vehicle performance. This analysis highlights the importance of considering material properties when selecting fuel lines for different automotive applications.
Locate the Fuel Injector Line on Your 2007 Impala SS
You may want to see also
Corrosion Resistance: Investigating how metal and rubber fuel lines resist corrosion over time
The choice between metal and rubber fuel lines is a critical consideration for vehicle owners and mechanics, especially when it comes to long-term performance and reliability. While both materials have their advantages, understanding their respective corrosion resistance properties is essential to ensure the longevity of the fuel system.
Metal fuel lines, often made from materials like steel or aluminum, offer several benefits. Firstly, they are known for their durability and strength. Metal lines can withstand high pressure and are less susceptible to damage from external factors such as road debris or temperature fluctuations. Additionally, metal is inherently resistant to corrosion due to its natural protective oxide layer. This layer forms on the surface of the metal, preventing further oxidation and corrosion. As a result, metal fuel lines can provide a reliable and long-lasting solution for fuel delivery, especially in harsh environments.
On the other hand, rubber fuel lines have their own set of advantages. Rubber is flexible and can accommodate slight movements within the engine bay, reducing the risk of damage from vibrations and impacts. It is also more resistant to abrasion compared to metal, making it suitable for areas with higher friction. However, rubber's susceptibility to corrosion is a significant concern. Over time, rubber can degrade due to exposure to fuel, UV radiation, and temperature changes, leading to cracking and deterioration. This degradation can result in fuel leaks and potential engine damage.
To enhance corrosion resistance in rubber fuel lines, manufacturers often incorporate additives and specialized compounds. These treatments can improve the material's ability to withstand fuel-related chemicals and environmental factors. Additionally, some rubber compounds are designed to be more resistant to UV radiation, ensuring that the fuel lines remain stable and flexible over a longer period.
In summary, both metal and rubber fuel lines have their unique characteristics and considerations. Metal lines offer superior corrosion resistance and durability, making them ideal for high-pressure applications and harsh conditions. Rubber, while more susceptible to corrosion, provides flexibility and abrasion resistance, which are crucial for certain engine bay environments. Understanding these properties allows vehicle owners and mechanics to make informed decisions when selecting fuel lines, ensuring optimal performance and longevity.
Freezing Fuel: The Impact of Water in Fuel Lines
You may want to see also
Cost-Effectiveness: Comparing the cost of metal and rubber fuel lines for different applications
When considering fuel lines for various applications, understanding the cost-effectiveness of different materials is crucial. Metal and rubber are the two primary materials used, each with its own advantages and disadvantages in terms of cost. Metal fuel lines, often made from stainless steel, offer durability and resistance to corrosion, making them ideal for high-performance vehicles or applications where fuel lines are exposed to harsh conditions. However, the initial cost of metal fuel lines can be significantly higher compared to rubber alternatives. The manufacturing process for metal lines involves intricate welding and precise engineering, contributing to the higher price tag.
On the other hand, rubber fuel lines are generally more affordable and widely used. Rubber is lightweight, flexible, and resistant to fuel degradation, making it a popular choice for everyday vehicles and applications where cost is a primary concern. The production of rubber fuel lines is relatively simpler, involving molding and extrusion processes, which can result in lower manufacturing costs. Additionally, rubber lines are often more readily available, making them a convenient and cost-effective option for quick replacements or repairs.
The cost-effectiveness of fuel lines becomes even more apparent when considering long-term maintenance and replacement expenses. Metal fuel lines, despite their higher initial cost, may offer longer-lasting performance, reducing the need for frequent replacements. This can be particularly beneficial for high-performance vehicles or industrial applications where reliability is critical. In contrast, rubber fuel lines might require more frequent replacements due to wear and tear, especially in harsh environments, but their lower cost per unit makes them a more economical choice for applications with lower performance demands.
In certain scenarios, a compromise between cost and performance can be made. For example, in classic car restoration, where maintaining the original look and feel is essential, metal fuel lines might be preferred despite their higher cost. Conversely, for high-volume production in the automotive industry, rubber fuel lines could be the more economical choice, ensuring cost-efficiency without compromising on essential performance factors.
In conclusion, the choice between metal and rubber fuel lines depends on the specific application and its requirements. While metal fuel lines offer superior durability and performance, they come at a higher cost. Rubber fuel lines, with their affordability and versatility, cater to a wide range of applications, especially those with budget constraints. Understanding the trade-offs between cost and performance is essential for making an informed decision when selecting fuel lines for different projects or vehicles.
Choosing the Right Fuel Line for E100 Gasoline
You may want to see also
Frequently asked questions
Fuel lines are typically made of rubber or a composite material, often a blend of rubber and plastic. Rubber is a common choice due to its flexibility, durability, and resistance to fuel degradation.
Metal fuel lines, usually made of steel or aluminum, offer some advantages. They are more rigid and less susceptible to expansion and contraction with temperature changes, which can be beneficial in extreme weather conditions. However, they are more prone to corrosion and can be more expensive. Rubber fuel lines are generally preferred for their cost-effectiveness and ease of installation.
You can inspect the fuel line for visual clues. Rubber fuel lines are often flexible and may have a slight give when bent. They might also show signs of wear and tear, such as cracks or brittleness over time. Metal fuel lines are stiffer and less flexible. They may have a metallic sheen and could be more challenging to bend without causing damage. It's best to consult a professional mechanic for an accurate assessment if you're unsure.