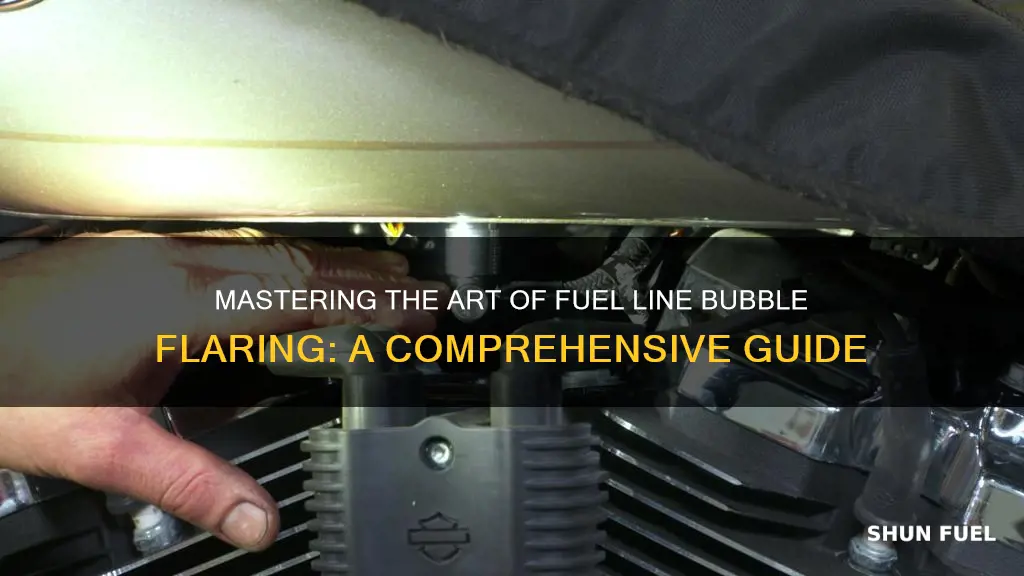
Bubble flare is a technique used to clear fuel lines of air bubbles, ensuring a smooth and efficient flow of fuel to the engine. This process involves a specific method to remove any trapped air, which can cause performance issues and even engine damage. By following a step-by-step guide, you can effectively bubble flare a fuel line, ensuring optimal engine performance and longevity.
What You'll Learn
- Prepare Tools: Gather necessary tools: fuel line cleaner, compressed air, and a flare gun
- Clean Line: Remove dirt and debris from the fuel line using a fuel line cleaner
- Inspect Flare: Check flare for damage, ensuring it's straight and free of obstructions
- Attach Flare: Securely attach the flare to the fuel line using the appropriate fittings
- Test Bubble: Blow compressed air through the flare to ensure a tight seal and no bubbles
Prepare Tools: Gather necessary tools: fuel line cleaner, compressed air, and a flare gun
To begin the process of bubble flaring a fuel line, it is crucial to have the right tools and materials ready. The first step is to gather the necessary equipment, which includes a fuel line cleaner, compressed air, and a flare gun. These tools are essential for ensuring a successful and safe flare operation.
Fuel line cleaner is a critical component in this process. It is used to remove any contaminants or debris that may be present in the fuel line. This cleaner helps to ensure that the fuel line is free of any obstructions, allowing for a smooth and efficient flare. When selecting a fuel line cleaner, opt for a product specifically designed for this purpose, as it will have the necessary properties to dissolve and remove any built-up residue.
Compressed air is another vital tool in this setup. It is used to blow air through the fuel line, creating a controlled burst of air that helps to clear any remaining contaminants. The air pressure should be sufficient to create a strong, controlled blast, ensuring that the fuel line is thoroughly cleaned. It is important to use compressed air carefully, as excessive pressure can damage the fuel line or other components.
Lastly, a flare gun is an indispensable tool for the bubble flare process. This gun is designed to create a controlled flame at the end of the fuel line, allowing for the flaring operation. The flare gun should be compatible with the fuel line's diameter and material to ensure a secure connection. It is essential to handle the flare gun with care, as it generates high temperatures and flames, which can be dangerous if not used properly.
By having these tools prepared and readily available, you are setting the foundation for a successful bubble flare operation. Each of these items plays a specific role in ensuring the fuel line is cleaned, prepared, and ready for the flaring process, which is a critical step in maintaining the integrity of the fuel system.
Fixing Auto Hot Rod Fuel Leaks: A Step-by-Step Guide
You may want to see also
Clean Line: Remove dirt and debris from the fuel line using a fuel line cleaner
To ensure optimal performance and longevity of your fuel system, it's crucial to keep the fuel lines clean and free from contaminants. One effective method to achieve this is by using a fuel line cleaner, which can help remove dirt, debris, and other impurities that may accumulate over time. Here's a step-by-step guide on how to clean your fuel line using a cleaner:
Step 1: Prepare the Materials
Before you begin, gather the necessary tools and materials. You will need a fuel line cleaner, preferably a specialized cleaner designed for fuel systems. These cleaners are typically available at auto parts stores or online. Additionally, you'll require a fuel line brush, which is a flexible brush with bristles designed to navigate the twists and turns of the fuel line. It's also a good idea to have a container for the cleaner and some rags or paper towels for wiping.
Step 2: Locate the Fuel Line
Identify the fuel line that you want to clean. This is typically the line that runs from the fuel tank to the engine. Locate the fuel line's starting point at the fuel tank and its endpoint at the engine's fuel injection system or carburetor. Make a mental note of any connections or fittings along the way, as you'll need to access these areas during the cleaning process.
Step 3: Disconnect the Fuel Line (Optional)
Depending on your vehicle's design, you might need to disconnect the fuel line from the fuel tank or other components to gain better access. Carefully disconnect the fuel line, ensuring you label or mark the connections to remember their positions. This step is optional but can make the cleaning process easier, especially if the fuel line is difficult to reach.
Step 4: Apply the Fuel Line Cleaner
Pour a small amount of the fuel line cleaner into the container. Follow the instructions on the cleaner's packaging to determine the appropriate amount. Slowly pour the cleaner into the fuel line, starting from the engine end and working your way back towards the fuel tank. Ensure that the cleaner is evenly distributed throughout the line.
Step 5: Use the Fuel Line Brush
Insert the fuel line brush into the cleaner-filled line. Start at the engine end and gently push the brush through the line, removing any built-up dirt and debris. Work your way back towards the fuel tank, ensuring that you clean the entire length of the fuel line. The brush will help dislodge and capture contaminants, leaving the line clean.
Step 6: Rinse and Reassemble
Once you've cleaned the entire fuel line, remove the brush and rinse it with clean fuel or a mild solvent to remove any remaining cleaner. If you disconnected the fuel line, carefully reconnect it, ensuring all connections are secure. Reattach any fittings or components that you had removed earlier.
Step 7: Start the Engine
With the fuel line now clean, start your engine and let it run for a few minutes. Check for any unusual noises or vibrations, and ensure that the engine is running smoothly. This step helps verify that the cleaning process has been successful and that the fuel system is functioning optimally.
Remember, regular maintenance and cleaning of the fuel line can prevent issues such as fuel contamination, reduced engine performance, and potential damage to the fuel system. By following these steps, you can ensure that your fuel lines remain clean and contribute to the overall health of your vehicle's engine.
Mastering Fuel Line Threading: A Step-by-Step Guide to Connector Success
You may want to see also
Inspect Flare: Check flare for damage, ensuring it's straight and free of obstructions
When inspecting the flare for a fuel line, it's crucial to ensure that the flare is in optimal condition to prevent any potential issues with fuel flow and safety. Here's a step-by-step guide on how to inspect the flare:
- Visual Inspection: Begin by carefully examining the flare for any visible signs of damage or wear. Look for cracks, bends, or any distortion in the flare's shape. Even minor damage can lead to fuel leaks or reduced performance, so it's essential to be thorough. Check the flare's connection points, especially where it joins the fuel line. Ensure that the connections are tight and secure, as loose fittings can cause fuel leaks over time.
- Straightness and Alignment: Verify that the flare is straight and aligned correctly. Fuel lines should have a slight angle to allow for slight movement and expansion, but they must not be kinked or bent excessively. A bent flare can restrict fuel flow and may lead to fuel pressure issues. Use a straightedge or a ruler to check the flare's alignment, ensuring it forms a smooth, continuous curve without any sharp bends.
- Obstructions and Debris: Inspect the flare for any obstructions or debris that might interfere with its functionality. Over time, dirt, rust, or other contaminants can accumulate in the flare, leading to reduced performance. Carefully remove any debris or contaminants you find. If the flare has a protective cover, ensure it is securely in place to prevent foreign objects from entering.
- Pressure Testing (Optional): For a more comprehensive inspection, consider performing a pressure test. This step is especially important if the fuel line is under high pressure. Attach a pressure gauge to the flare and slowly increase the pressure. Monitor the gauge to ensure the flare can withstand the pressure without leaking. If any issues are detected, further investigation and potential repairs may be necessary.
Remember, regular maintenance and inspections are vital to ensuring the safety and efficiency of your fuel system. By following these steps, you can identify potential problems with the flare and take appropriate action, whether it's making adjustments, replacing damaged components, or seeking professional assistance.
Understanding Fuel Line Flare: A Comprehensive Guide
You may want to see also
Attach Flare: Securely attach the flare to the fuel line using the appropriate fittings
When it comes to securing the flare to the fuel line, it's crucial to use the right fittings to ensure a tight and reliable connection. Here's a step-by-step guide to help you through this process:
Step 1: Prepare the Fittings
Start by gathering the necessary fittings. You'll typically need a flare fitting, which is specifically designed to connect to the fuel line. These fittings come in various sizes and types, so ensure you have the correct one that matches the diameter of your fuel line. Additionally, get a suitable hose or tube to connect the flare fitting to the fuel line.
Step 2: Clean and Inspect
Before attaching, make sure both the flare fitting and the fuel line are clean and free from any debris or contaminants. Use a cloth or brush to wipe down the surfaces, ensuring a smooth and clean connection. Inspect the fittings for any signs of damage or wear, and replace them if necessary.
Step 3: Apply Thread Seal Tape or Compound
To ensure a tight seal, apply a thin layer of thread seal tape or compound around the threads of the flare fitting. This step is essential to prevent leaks and ensure a secure connection. Wrap the tape or compound clockwise around the threads, covering at least one full turn.
Step 4: Connect the Fittings
Now, carefully connect the flare fitting to the fuel line. Start by inserting the fuel line into the flare fitting, ensuring it is aligned correctly. Use your hands or a tool to tighten the fitting by turning it clockwise. Apply firm pressure to create a secure bond. Check for any leaks by gently pressing around the connection and observing if any fuel escapes. If there are any leaks, tighten the fitting further or reapply thread seal material.
Step 5: Final Adjustments
Once the flare is attached, make any necessary adjustments to ensure optimal performance. Check the connection for tightness and make sure there are no kinks or obstructions in the fuel line. You may need to adjust the flare's position or orientation to achieve the desired bubble flare effect.
Remember, taking the time to properly secure the flare fitting will result in a more efficient and reliable fuel line setup. Always refer to the manufacturer's guidelines for specific instructions and recommendations for your particular fuel line and flare system.
Mastering the Art of Bedding Fuel Lines: A Comprehensive Guide
You may want to see also
Test Bubble: Blow compressed air through the flare to ensure a tight seal and no bubbles
To ensure a proper and safe fuel line installation, it is crucial to test the flare connection for any potential issues, especially bubbles. Here's a detailed guide on how to perform the 'Test Bubble' step:
Step 1: Prepare the Tools and Materials
Before you begin, gather the necessary tools and materials. You will need a compressed air source, such as an air compressor or a portable air tank, with an output pressure of at least 100 psi. Additionally, have a flare tool or a similar device that can be used to apply force and create a seal. It is also recommended to wear protective gear, including safety goggles and gloves, to ensure personal safety during the process.
Step 2: Connect the Fuel Line and Flare
Carefully connect the fuel line to the flare, ensuring a proper and tight connection. Check for any leaks or gaps that might allow air to enter the system. If you notice any issues, tighten the connections or use sealing compounds to address the problem. The goal is to create a secure and airtight bond between the fuel line and the flare.
Step 3: Apply Compressed Air
Now, it's time to test the seal by blowing compressed air through the flare. Turn on the compressed air source and direct the airflow towards the flare connection. The air should be applied at a steady and controlled rate to avoid any sudden pressure spikes. As you blow air, pay close attention to the flare connection. If you hear any hissing sounds or see air escaping from the connection, it indicates the presence of bubbles or an improper seal.
Step 4: Ensure a Tight Seal
The primary objective of this test is to verify that there are no bubbles or air pockets within the flare connection. Bubbles can lead to fuel contamination, reduced performance, and potential safety hazards. If you detect any bubbles, it means the seal is not tight, and you need to re-evaluate the connection. Tighten the flare further or consider using a different sealing technique to ensure a secure bond.
Step 5: Repeat and Verify
Repeat the process of blowing compressed air through the flare connection multiple times to ensure consistency. Each test should yield the same results, confirming a tight and bubble-free seal. If you consistently find no bubbles, you can proceed with the fuel line installation, confident that the connection is secure and reliable. However, if bubbles persist, further investigation and adjustments are necessary to achieve a proper seal.
Remember, this test is a critical step in the process of bubble flaring a fuel line, ensuring the safety and efficiency of your fuel system. Always follow safety guidelines and consult relevant resources for specific instructions tailored to your equipment and fuel line type.
Fuel Injector Cars: The Return Line Mystery
You may want to see also
Frequently asked questions
Bubbling a fuel line, also known as fuel line bubbling, is a process used to ensure the proper flow and pressure of fuel in a vehicle's engine. It involves introducing air into the fuel line to create a bubbly mixture, which helps to prevent fuel accumulation and ensures optimal fuel atomization during combustion.
If you notice any of the following symptoms, it may indicate that your fuel line requires bubbling: engine misfires, poor fuel efficiency, hard starting, or a noticeable drop in engine performance. These issues can often be attributed to fuel-related problems, and bubbling the fuel line can help diagnose and resolve these concerns.
To bubble a fuel line, you will typically need a fuel line bubbler kit, which includes a bubbler device, a fuel line connector, and a source of compressed air. It is recommended to use a kit specifically designed for your vehicle's fuel system to ensure compatibility and proper functionality.
Yes, it is crucial to exercise caution when bubbling a fuel line. Always ensure the engine is off and the vehicle is in a secure position to avoid any accidents. Additionally, be mindful of fuel line pressure and follow the manufacturer's guidelines to prevent damage to the fuel system. It is advisable to consult a professional mechanic if you are unsure about any step of the process.