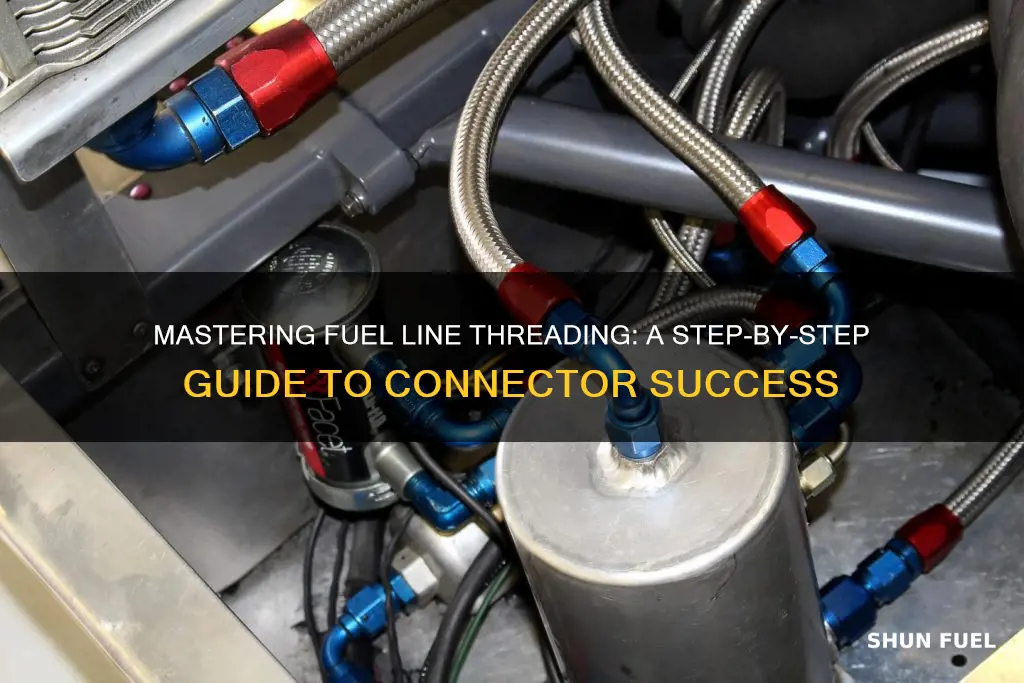
Threading a fuel line for a connector is a crucial step in ensuring a secure and leak-free fuel supply system. This process involves carefully inserting the fuel line into the connector, ensuring a tight and precise fit. It requires attention to detail and the right tools to avoid damage to the fuel line or the connector. This guide will provide a step-by-step approach to threading the fuel line, covering preparation, installation, and troubleshooting common issues to ensure a successful and reliable fuel system.
What You'll Learn
- Prepare the Fuel Line: Clean and inspect the fuel line for any damage or debris
- Cut the Line: Measure and mark the desired length, then cut with a sharp blade
- Prepare the Connector: Ensure the connector is clean and free of any obstructions
- Slide the Line: Carefully slide the fuel line into the connector, ensuring a snug fit
- Secure with Clamps: Tighten the clamps securely to prevent any leaks
Prepare the Fuel Line: Clean and inspect the fuel line for any damage or debris
Before you begin threading the fuel line, it's crucial to ensure that the line is in optimal condition. Start by thoroughly cleaning the fuel line to remove any dirt, grime, or debris that may have accumulated over time. This step is essential as it ensures a smooth and secure connection. Use a soft-bristled brush or a specialized fuel line cleaning tool to gently scrub the interior of the line, paying extra attention to any bends or kinks. Rinse the line with a clean, degreased solvent to eliminate any remaining contaminants. Allow the line to air dry completely before proceeding.
Once the fuel line is clean, perform a visual inspection to check for any signs of damage or wear. Look for cracks, punctures, or any other visible defects along the length of the line. Inspect the fittings and connectors as well, ensuring they are intact and securely attached. If you notice any damage, it's crucial to replace the affected section of the fuel line to prevent potential leaks or system failures. Take note of the length and type of fuel line you need to replace so you can source the appropriate replacement parts.
In addition to visual inspection, you can use a flexible metal probe or a fuel line inspection camera to thoroughly examine the interior of the line. These tools can help you identify hidden damage or blockages that may not be visible to the naked eye. If you find any issues, such as internal corrosion or debris buildup, address them accordingly before proceeding with the threading process.
Remember, a well-prepared fuel line is essential for a successful connection and the overall performance of your fuel system. By taking the time to clean and inspect the line, you can ensure a reliable and safe fuel supply to your engine.
Troubleshooting Evaporation: Fixing Mazda's Fuel Line Issues
You may want to see also
Cut the Line: Measure and mark the desired length, then cut with a sharp blade
Before you begin cutting the fuel line, it's crucial to measure and mark the desired length accurately. This step is essential to ensure a proper fit and prevent any unnecessary waste of material. Start by laying out the fuel line on a flat surface and measuring it with a tape measure or ruler. Identify the exact length required, taking into account any bends or connections that need to be made. Mark this length on the fuel line using a permanent marker or a piece of chalk. Make sure the mark is clear and visible, as it will guide your cutting process.
Once you have the length marked, it's time to cut the fuel line. Use a sharp blade, such as a utility knife or a pair of scissors, to make a clean and precise cut. Hold the fuel line steady with one hand and the blade with the other. Carefully slice through the material, following the marked line. Take your time and apply steady pressure to ensure a straight cut. Avoid applying excessive force, as it may lead to a jagged edge. If you're using scissors, ensure they are sharp to get a clean cut.
When cutting, it's important to consider the type of connector you are working with. Different connectors may require specific lengths or angles for optimal connection. Refer to the manufacturer's guidelines or diagrams if available to ensure you are cutting the fuel line to the correct specifications. A precise cut will result in a seamless connection and prevent any potential leaks or damage.
After cutting, inspect the edge of the fuel line. If it's not already smooth, use a file or sandpaper to gently smooth the cut surface. This step is crucial to ensure a tight seal when connecting the fuel line. Take your time with this process to avoid any rough edges that could cause issues during assembly.
Remember, accuracy and precision are key when measuring and cutting the fuel line. Take your time, double-check your measurements, and use sharp tools to ensure a professional finish. Properly measured and cut fuel lines will make the threading process much easier and more efficient.
Volvo Loader Fuel Line Testing: A Comprehensive Guide
You may want to see also
Prepare the Connector: Ensure the connector is clean and free of any obstructions
When preparing the connector for threading the fuel line, it is crucial to ensure that the connector is in optimal condition. Start by inspecting the connector for any signs of damage, corrosion, or debris. If you notice any issues, address them before proceeding. For example, if the connector has rust or corrosion, carefully clean it using a suitable solvent or a mild acid solution. Ensure that all traces of corrosion are removed to prevent any interference during the threading process.
Next, check for any obstructions or blockages within the connector. Over time, fuel lines can accumulate dirt, debris, or even small clogs. Use a thin wire brush or a small tool to carefully clear any obstructions. Make sure to remove any foreign matter to ensure a smooth and accurate fit for the fuel line. This step is essential to guarantee a proper connection and prevent potential leaks.
Additionally, inspect the threads of the connector. Threads should be smooth, straight, and free of any damage. If the threads are damaged or worn, consider replacing the connector to ensure a secure connection. Smooth and intact threads will make it easier to thread the fuel line and reduce the risk of stripping or damaging the threads during the process.
It is also beneficial to lubricate the connector threads with a thin layer of thread seal tape or pipe compound. This simple step can help prevent the threads from sticking together and make threading the fuel line smoother. Just ensure that the lubricant is compatible with the materials used in the connector to avoid any adverse reactions.
By thoroughly preparing the connector, you create a solid foundation for a successful fuel line installation. This process ensures that the connector is ready to accept the fuel line without any complications, promoting a reliable and safe fuel system. Remember, taking the time to clean and prepare the connector is an essential step that should not be overlooked.
Unclogging Fuel Lines: Why a Flush is Necessary
You may want to see also
Slide the Line: Carefully slide the fuel line into the connector, ensuring a snug fit
Before you begin, it's crucial to ensure you have the correct tools and materials. You'll need the fuel line, the connector, and a pair of pliers or a fuel line tool to help guide the line into the connector. It's also a good idea to have a clean workspace to avoid any contamination that could affect the connection's integrity.
Now, let's get started with the process of threading the fuel line into the connector. The key here is to ensure a snug fit, which will help prevent leaks and ensure the fuel line is secure. Start by aligning the fuel line with the connector, ensuring that the line is straight and the connector is in the correct orientation. This step is crucial to ensure a proper connection.
Carefully slide the fuel line into the connector, paying close attention to the direction of the line. It should slide in smoothly, but you might need to apply a bit of force, especially if the line is stiff. If you encounter resistance, stop and check that the line is aligned correctly. You want to avoid forcing the line, as this could damage the connector or the line itself.
As you slide the line in, ensure that it is fully inserted and that there is no gap between the line and the connector. A snug fit is essential to prevent fuel leaks and ensure the system's safety. If the line is not fully inserted, you may need to carefully adjust it to ensure a complete connection.
Finally, once the fuel line is fully inserted, double-check that it is secure and there are no visible gaps. You can use a fuel line tool or a pair of pliers to gently pull on the line to ensure it is tight. This final step is important to guarantee a reliable connection that will withstand the pressures and vibrations of the engine.
Fuel Line Inspection: When to Check for Leaks and Damage
You may want to see also
Secure with Clamps: Tighten the clamps securely to prevent any leaks
When threading a fuel line for a connector, ensuring a secure and leak-free connection is crucial. One essential step in this process is the use of clamps to tighten the connection. Here's a detailed guide on how to secure the fuel line with clamps:
Start by ensuring you have the appropriate clamps for the specific fuel line and connector you are working with. Clamps come in various sizes and designs, so it's important to choose the right one for a snug fit. Look for clamps that are designed for fuel lines, as they will have the necessary sealing properties to prevent leaks.
Position the fuel line and connector so that the line is aligned with the connector's inlet. Carefully slide the clamp over the fuel line, ensuring it covers the thread or connection point. The clamp should be positioned close to the connector, providing a secure base for tightening.
Now, it's time to tighten the clamp. Use a wrench or a suitable tool to apply firm pressure and tighten the clamp securely. The goal is to create a tight seal that prevents any movement or gaps between the fuel line and the connector. Tighten the clamp in a clockwise direction, ensuring you don't overtighten, as this can damage the fuel line or connector.
Check the tightness of the clamp by gently pulling on the fuel line. It should feel firmly attached and not move or wobble. If there is any play or movement, you may need to tighten the clamp further. Remember, a secure clamp is essential to prevent fuel leaks and ensure the system's overall safety.
Finally, inspect the entire setup for any signs of damage or leaks. Tightening the clamp is just one part of the process. Ensure that the fuel line is not pinched or damaged during the tightening process, as this could lead to future issues. By following these steps and paying close attention to the clamp's security, you can effectively thread the fuel line and connector, ensuring a reliable and safe fuel system.
Unclipping the Ford Pink Fuel Line: A Step-by-Step Guide
You may want to see also
Frequently asked questions
Threading a fuel line is a crucial step in ensuring a secure and leak-free connection between the fuel source and the engine. It involves creating a male-female thread on the fuel line to fit into a corresponding female connector, allowing for a tight and reliable seal.
Using the correct thread size is essential to guarantee a proper fit. If the threads are too small or too large, the fuel line may not seal correctly, leading to potential fuel leaks and engine performance issues. Always refer to the vehicle's manual or consult a mechanic to determine the appropriate thread size.
Threading the fuel line requires patience and precision. Start by cleaning the fuel line and connector to ensure a smooth surface. Then, using a thread-seating tool or a pipe wrench, carefully thread the male end of the fuel line onto the female connector. Apply firm pressure and rotate the line clockwise until it is fully seated. Avoid over-tightening to prevent damage to the threads.
Reusing an old fuel line is generally not recommended as it may have deteriorated or damaged threads over time. It's best to use a new fuel line with fresh threads to ensure a secure connection. Old lines might also have accumulated debris or contaminants that could affect the seal.
You will need a few essential tools for this task. A thread-seating tool or a pipe wrench is used to create the threads. Additionally, have a fuel line cleaner, a rag or cloth, and a pair of pliers handy for any necessary adjustments. It's also a good practice to wear gloves and safety goggles to protect your hands and eyes during the process.