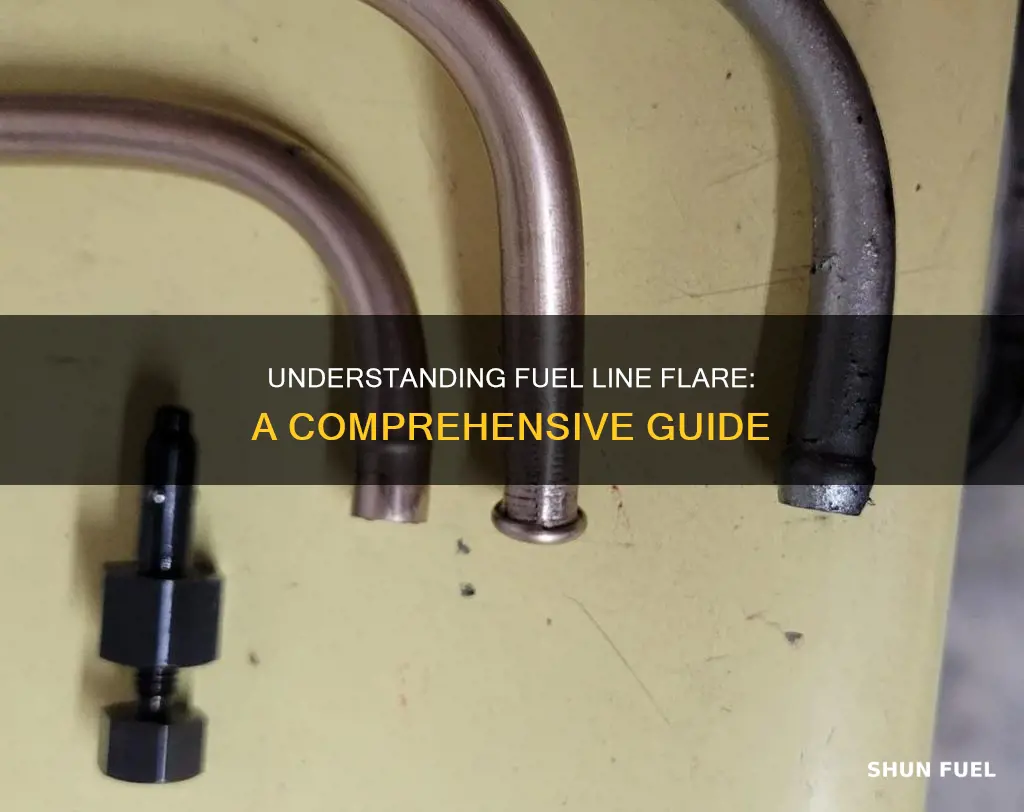
When it comes to choosing the right flare for your fuel line, it's important to consider the specific requirements of your vehicle and the type of fuel it uses. Different types of fuel lines may require different types of flares to ensure a secure and reliable connection. Understanding the compatibility and specifications of the flare is crucial to avoid any potential issues with fuel delivery and engine performance. Whether you're working on a classic car or a modern vehicle, selecting the appropriate flare for your fuel line is essential for a successful and safe installation.
What You'll Learn
- Fuel Line Material: Choose the right material for your fuel line, considering factors like temperature resistance and flexibility
- Flaring Techniques: Master various flaring techniques to ensure a secure and leak-free fuel line connection
- Flaring Tools: Familiarize yourself with the necessary tools for flaring, including flares, dies, and mandrels
- Fuel Line Sizing: Determine the appropriate size of the fuel line based on flow rate and pressure requirements
- Safety Precautions: Implement safety measures during flaring, such as using protective gear and working in a well-ventilated area
Fuel Line Material: Choose the right material for your fuel line, considering factors like temperature resistance and flexibility
When it comes to choosing the right material for your fuel line, several factors come into play, especially when considering the harsh conditions that fuel lines often face. Temperature resistance and flexibility are two critical aspects that should guide your decision. The material you select must be able to withstand the extreme temperatures that can vary widely, from the cold of winter to the heat of summer, without compromising its structural integrity.
For instance, rubber is a popular choice for fuel lines due to its inherent flexibility and resilience. It can absorb vibrations and flex with the movement of the vehicle, ensuring a secure and reliable connection. Natural rubber is known for its excellent temperature resistance, able to handle both hot and cold conditions without becoming brittle or soft. However, it's important to note that rubber may not be the best choice for high-pressure applications, as it can become susceptible to cracking over time.
Another option is synthetic rubber, which offers improved resistance to heat and chemicals compared to natural rubber. This type of rubber is often used in high-performance vehicles or in applications where the fuel line is exposed to more aggressive environments. Synthetic rubber can maintain its flexibility and temperature resistance even under extreme conditions, making it a reliable choice for fuel lines.
For those seeking an even more robust solution, polyurethane (PU) is an excellent alternative. PU fuel lines offer superior temperature resistance, often handling temperatures that natural or synthetic rubber cannot. They are also highly flexible, providing a secure connection without compromising the vehicle's performance. Additionally, polyurethane is resistant to abrasion and chemicals, making it an ideal choice for both on-road and off-road vehicles, as well as for applications where the fuel line is exposed to harsh chemicals or environmental factors.
In summary, when selecting the material for your fuel line, it is crucial to consider the specific requirements of your vehicle and the environment in which it operates. Temperature resistance and flexibility are key factors that will determine the longevity and reliability of your fuel line. By choosing the right material, you can ensure a safe and efficient fuel delivery system, providing peace of mind and optimal vehicle performance.
Essential Fittings for High-Pressure Fuel Lines: 60 PSI Requirements
You may want to see also
Flaring Techniques: Master various flaring techniques to ensure a secure and leak-free fuel line connection
Flaring is a critical process in creating a secure and leak-free connection for fuel lines, ensuring the safety and efficiency of any fuel-powered system. This technique involves shaping and bending the ends of fuel lines to create a tight seal, preventing any potential leaks and ensuring a reliable fuel supply. Here's an in-depth guide to mastering various flaring techniques:
Understanding the Basics:
Before diving into specific techniques, it's essential to understand the fundamental principles of flaring. Flaring requires precise control over heat, pressure, and the physical manipulation of the fuel line material. The goal is to create a smooth, continuous bend at the end of the line, forming a tight seal when connected to another component. This process should be done with care to avoid damaging the fuel line or creating weak points.
Gathering the Right Tools:
To master flaring, you'll need a set of specialized tools. This includes a flaring tool kit, which typically consists of a mandrel (a cylindrical tool), a die (a shaped tool), and a heat source. The mandrel is used to guide the bending process, ensuring a consistent curve. The die applies the necessary force to shape the material, and the heat source is crucial for softening the metal, making it more pliable during the flaring process.
Step-by-Step Flaring Process:
- Preparation: Start by cleaning the fuel line end and removing any debris or contaminants. Ensure the surface is smooth and free of any obstacles that might interfere with the flaring process.
- Heating: Apply heat to the fuel line end using a torch or a heat gun. The heat softens the metal, making it easier to shape. Be cautious not to overheat, as it may damage the material.
- Bending: Using the mandrel, guide the heated fuel line end and apply pressure to create a continuous curve. The die can be used to shape the bend and ensure a consistent radius. The goal is to form a smooth, uniform flare without any sharp bends or kinks.
- Cooling and Inspection: Allow the flared section to cool slightly, then inspect it for quality. The flare should be free of any cracks, sharp edges, or uneven bends. Ensure the flare is long enough to provide a secure connection.
Mastering Different Flaring Techniques:
- Single-Bender Flaring: This technique is suitable for smaller fuel lines and involves a single bend. It requires precision and control over the heating and bending process.
- Double-Bender Flaring: For larger fuel lines, a double-bender flare is often used, creating two bends. This technique provides a stronger connection but demands more skill to avoid creating weak points.
- V-Bending: In this method, the fuel line end is bent into a V-shape, offering a unique connection style. It is useful in specific applications where a standard flare might not fit.
Practice and Safety:
Flaring is a skill that improves with practice. Take the time to experiment with different materials and techniques to find what works best for your specific fuel line connections. Always prioritize safety by wearing protective gear and ensuring proper ventilation when working with heat sources. Regularly inspect your flaring tools for wear and tear, replacing them if necessary to maintain precision.
Mastering flaring techniques is an essential skill for anyone working with fuel lines, ensuring a professional and reliable connection. With practice and attention to detail, you can create secure, leak-free joints, contributing to the overall safety and performance of fuel-powered systems.
C1500 Fuel Lines: A Comprehensive Guide to Identification
You may want to see also
Flaring Tools: Familiarize yourself with the necessary tools for flaring, including flares, dies, and mandrels
When it comes to working with fuel lines, understanding the proper flaring tools and techniques is essential for a successful and safe installation. Flaring is a process that involves shaping and bending the end of a fuel line to create a sealed connection, ensuring a tight and leak-free fit. Here's an overview of the key tools you should be familiar with:
Flares: These are the primary components used in flaring. Flares come in various shapes and sizes, and the choice depends on the specific application and the type of fuel line being used. Common flare types include the 90-degree flare, which is a right-angle bend, and the 45-degree flare, which provides a more gradual curve. The flare angle and radius are critical factors, as they determine the strength and durability of the connection. For instance, a 90-degree flare is ideal for tight spaces, while a 45-degree flare offers better flexibility and is suitable for longer runs.
Dies: Dies are essential tools for shaping and forming the fuel line to match the flare. They come in different sizes and designs, allowing for precise control over the flare's dimensions. When using a die, you apply force to the fuel line, forcing it to conform to the shape of the die. This process ensures that the flare is uniform and consistent, creating a reliable seal. It's crucial to select the appropriate die size that matches the flare type to achieve the correct flare dimensions.
Mandrels: Mandrels are cylindrical tools that provide support and guidance during the flaring process. They are inserted into the fuel line and help maintain the desired shape and angle of the flare. Mandrels are particularly useful for creating consistent flares, especially in high-volume production environments. By using a mandrel, you can ensure that each flare is identical, reducing the risk of errors and improving overall quality. Different mandrel sizes and designs are available to accommodate various flare types and fuel line diameters.
Familiarizing yourself with these flaring tools is crucial for any professional working in the fuel line installation or repair field. Understanding the different flare types, dies, and mandrels allows for the selection of the appropriate tools for each specific job, ensuring a secure and reliable connection. Additionally, practicing with these tools and mastering the flaring technique will contribute to efficient and accurate work, ultimately leading to a safer and more reliable fuel system.
Choosing the Right Fuel Line: A Comprehensive Guide for Car Owners
You may want to see also
Fuel Line Sizing: Determine the appropriate size of the fuel line based on flow rate and pressure requirements
When determining the appropriate size of a fuel line, it is crucial to consider the flow rate and pressure requirements to ensure optimal performance and safety. The size of the fuel line directly impacts the efficiency of the fuel delivery system, especially in high-performance applications where precise fuel management is essential. Here's a detailed guide on how to approach fuel line sizing:
Understanding Flow Rate: The flow rate, typically measured in gallons per minute (GPM) or liters per minute (LPM), represents the volume of fuel that needs to be delivered through the line. It is a critical factor in sizing the fuel line. Higher flow rates require larger-diameter lines to accommodate the increased volume of fuel without causing excessive pressure drops. For instance, a fuel pump capable of delivering 100 GPM will necessitate a larger fuel line compared to one with a 50 GPM capacity. Calculating the required flow rate involves considering the engine's fuel requirements, the desired performance, and any potential future upgrades.
Pressure Considerations: Fuel lines must also be sized to handle the pressure requirements of the fuel system. Pressure can vary depending on the fuel source, pump specifications, and system design. High-pressure fuel systems, often found in racing applications or high-performance vehicles, demand fuel lines with larger diameters to prevent excessive pressure drops and ensure efficient fuel delivery. It is essential to consult the manufacturer's specifications for the maximum pressure the fuel line can withstand without compromising safety.
Using Flow Rate and Pressure Data: Engineers and technicians can use flow rate and pressure data sheets to select the appropriate fuel line size. These data sheets provide information on the relationship between flow rate, pressure, and line diameter. By plotting the desired flow rate and pressure against the available data, one can identify the suitable fuel line diameter. For instance, a data sheet might indicate that a 0.75-inch fuel line can handle a flow rate of 80 GPM at a pressure of 50 psi.
Material Selection: The choice of material for the fuel line is another critical aspect. Common materials include steel, aluminum, and various types of rubber or synthetic compounds. Each material has its advantages and limitations regarding flexibility, durability, and pressure resistance. For high-pressure applications, steel or aluminum lines might be preferred, while rubber or synthetic lines are suitable for flexible connections.
Safety and Performance: Proper fuel line sizing is essential for both safety and performance. Insufficient line size can lead to reduced fuel flow, engine misfires, or even fuel starvation during high-load conditions. Conversely, oversized lines may result in unnecessary pressure drops, reduced system efficiency, and potential fuel vaporization. Therefore, it is crucial to strike a balance between flow rate, pressure, and line diameter to optimize the fuel delivery system's performance.
Understanding Low Permeation Fuel Lines: A Comprehensive Guide
You may want to see also
Safety Precautions: Implement safety measures during flaring, such as using protective gear and working in a well-ventilated area
When engaging in flaring operations, it is crucial to prioritize safety to prevent accidents and ensure the well-being of personnel. One essential safety precaution is to utilize appropriate protective gear. This includes wearing heat-resistant gloves, flame-resistant clothing, and safety goggles to shield against potential burns, sparks, and flying debris. Additionally, consider donning a respirator or a face mask to protect against inhaling harmful fumes or gases that may be released during the flaring process. These protective measures act as a barrier between the worker and potential hazards, reducing the risk of injury.
Another critical aspect of safety during flaring is to work in a well-ventilated area. Proper ventilation is essential to disperse any flammable gases or vapors that might accumulate in the vicinity. Ensure that the work area has adequate airflow to prevent the buildup of explosive mixtures. If working outdoors, consider the wind direction and take measures to avoid directing the flare's flames towards personnel or nearby structures. Adequate ventilation can be achieved by opening windows, using fans, or setting up temporary ventilation systems, especially in enclosed spaces.
It is imperative to establish clear communication protocols during flaring operations. Assign specific roles and responsibilities to team members, ensuring everyone understands their tasks and potential hazards. Implement a system for signaling and warning others of any potential dangers, such as using hand gestures, whistles, or designated warning devices. Effective communication can prevent accidents and enable swift responses to emergencies.
Furthermore, regular safety training and drills should be conducted to familiarize personnel with flaring procedures and potential risks. This training should cover emergency response plans, including evacuation routes and the use of fire extinguishers or other firefighting equipment. By educating workers about the specific hazards associated with flaring, you empower them to take proactive safety measures.
Lastly, ensure that all equipment and tools used during flaring are in good working condition and properly maintained. Inspect and test the functionality of flares, nozzles, and associated machinery to guarantee their reliability. Regular maintenance not only enhances safety but also extends the lifespan of the equipment, reducing the likelihood of malfunctions.
Unveiling the Car Fuel Line: Visual Guide
You may want to see also
Frequently asked questions
For fuel lines, it is recommended to use a flare that is specifically designed for fuel applications. These flares are typically made from brass or stainless steel and are engineered to withstand the corrosive nature of fuels. Look for flares with a smooth, non-threaded end to ensure a secure and leak-free connection.
The size of the flare should match the diameter of your fuel line. Measure the inside diameter of the fuel line and select a flare with a corresponding diameter. Common sizes include 1/8", 1/4", 3/8", and 1/2" for fuel lines. It's important to get the right size to ensure a proper fit and avoid any potential leaks.
Yes, flare tools are essential for creating secure fuel line connections. These tools help to crimp the flare onto the fuel line, ensuring a tight and reliable seal. There are different types of flare tools available, such as manual or hydraulic, depending on your preference and the size of the flares you need to create.
Flaring a fuel line involves several steps. First, cut the fuel line to the desired length and deburr the ends. Then, use a flare tool to create the flare by bending the end of the line at a specific angle and radius. Ensure the flare is smooth and free of any sharp edges. Finally, inspect the connection for leaks and make any necessary adjustments.