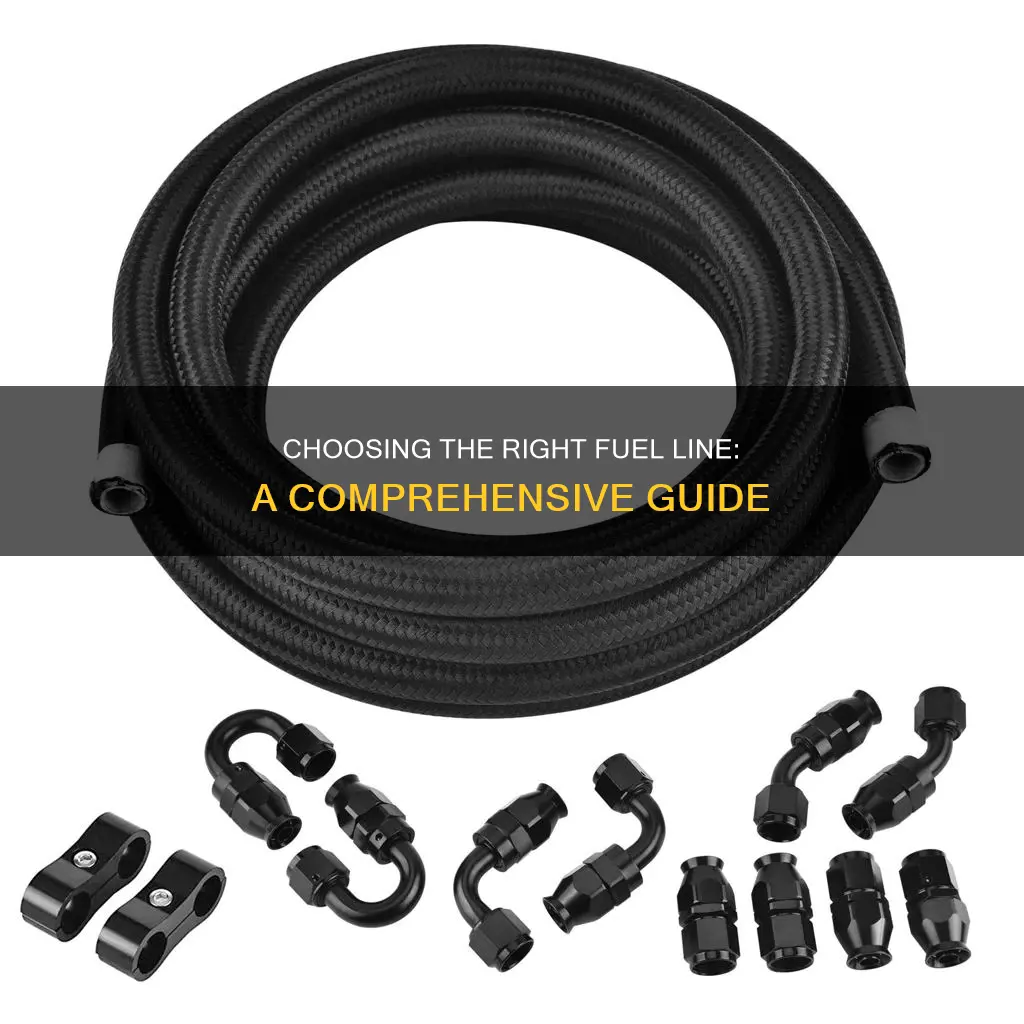
Choosing the best fuel line for your vehicle is crucial for optimal performance and safety. The market offers various options, each with unique characteristics and benefits. Factors such as temperature resistance, flexibility, and compatibility with different fuels play a significant role in determining the ideal fuel line for your specific needs. This introduction aims to explore these considerations and guide you in making an informed decision to ensure your vehicle operates efficiently and reliably.
What You'll Learn
- Fuel Line Material: Choose from rubber, vinyl, or braided steel based on application
- Fuel Line Diameter: Ensure proper flow rate and pressure for engine performance
- Fuel Line Length: Consider length for installation and avoid unnecessary bends
- Fuel Line Compatibility: Match fuel type (gasoline, diesel) and engine requirements
- Fuel Line Routing: Route lines away from heat sources and sharp bends
Fuel Line Material: Choose from rubber, vinyl, or braided steel based on application
When it comes to choosing the right fuel line for your vehicle, the material is a critical factor that can significantly impact performance and longevity. The market offers three primary options: rubber, vinyl, and braided steel, each with unique characteristics suited to different applications. Understanding these differences is essential for making an informed decision.
Rubber Fuel Lines:
Rubber is a traditional and widely used material for fuel lines due to its flexibility and durability. It is an excellent choice for most vehicles, especially those with older engines or those that require a more flexible line. Rubber fuel lines are known for their ability to absorb vibrations and reduce engine noise, providing a smoother driving experience. This material is also resistant to most common fuels, including gasoline and diesel, making it a versatile option. However, rubber can become brittle over time, especially in extreme temperatures, which may lead to cracking and potential fuel leaks. Regular inspections are recommended to ensure the integrity of the fuel lines.
Vinyl Fuel Lines:
Vinyl is another popular choice, offering a balance between flexibility and strength. It is more durable than rubber and can withstand higher temperatures, making it suitable for vehicles with high-performance engines. Vinyl fuel lines are less prone to cracking and are often used in applications where flexibility is crucial, such as in tight spaces or under the vehicle's body. This material is also resistant to fuel degradation, ensuring that the fuel lines remain in good condition over time. However, vinyl may not be as flexible as rubber, which could be a consideration for certain vehicle designs.
Braided Steel Fuel Lines:
Braided steel fuel lines are the stiffest and most rigid option, providing exceptional strength and resistance to fuel degradation. They are ideal for high-performance vehicles or those with modified engines that require a more robust fuel delivery system. Braided steel lines can withstand extreme temperatures and are less susceptible to corrosion, ensuring a long-lasting solution. While they offer superior durability, they may not be as flexible as rubber or vinyl, which could make installation more challenging in certain vehicle designs. Additionally, the rigid nature of braided steel may not be suitable for vehicles with older, more delicate engine components.
The choice between rubber, vinyl, and braided steel fuel lines depends on the specific requirements of your vehicle and the conditions it operates in. For most everyday vehicles, rubber or vinyl lines are sufficient and offer a good balance of performance and cost. However, for high-performance or modified vehicles, braided steel may be the preferred choice to ensure optimal fuel delivery and engine performance. Always consider the manufacturer's recommendations and consult with experts to make the best decision for your specific application.
Unveiling the Secrets: Corvette Fuel Line Sizing, 1969 Edition
You may want to see also
Fuel Line Diameter: Ensure proper flow rate and pressure for engine performance
The diameter of the fuel line is a critical factor in ensuring optimal engine performance and fuel efficiency. When selecting the appropriate fuel line, it is essential to consider the flow rate and pressure requirements for your specific engine setup. The fuel line's diameter directly impacts the volume of fuel that can be delivered to the engine per unit of time, which is crucial for maintaining the desired power output and overall engine health.
A fuel line with an inadequate diameter may result in reduced fuel flow, leading to engine performance issues. Insufficient fuel delivery can cause the engine to run lean, resulting in decreased power, poor fuel economy, and potential misfires. On the other hand, an oversized fuel line with a larger diameter might lead to excessive fuel flow, creating a rich fuel-air mixture. This can cause the engine to run inefficiently, leading to increased emissions and potential engine damage due to the improper air-fuel ratio.
The optimal fuel line diameter is determined by the engine's displacement, power output, and the desired fuel pressure. For high-performance engines, a larger diameter fuel line may be required to accommodate the increased fuel demand and ensure a consistent supply during acceleration or high-load conditions. Conversely, for smaller engines or those with lower power requirements, a smaller diameter fuel line might suffice, providing a balance between flow rate and pressure.
It is recommended to consult the vehicle's manual or seek professional advice to determine the specific fuel line diameter required for your engine. Using the correct diameter ensures that the fuel is delivered efficiently, maintaining the engine's performance and longevity. Additionally, considering the material of the fuel line is essential, as it should be compatible with the fuel type and engine conditions to prevent degradation over time.
In summary, the fuel line diameter plays a vital role in engine performance by regulating the flow rate and pressure of fuel. Selecting the right diameter ensures that the engine receives the appropriate amount of fuel, optimizing power output, fuel efficiency, and overall engine health. Proper fuel line installation and maintenance are essential to guarantee the engine's performance and longevity.
Understanding Rubber Fuel Line Sizes for CJ7s
You may want to see also
Fuel Line Length: Consider length for installation and avoid unnecessary bends
When it comes to choosing the best fuel line for your vehicle, one crucial aspect often overlooked is the length of the fuel line itself. The length of the fuel line is not just a matter of convenience; it significantly impacts the installation process and the overall performance of your fuel system. Here's why considering the length of the fuel line is essential and how it can benefit your vehicle.
Installation Considerations:
The length of the fuel line is a critical factor during the installation process. Longer fuel lines may require more careful routing to avoid unnecessary bends and twists. Bending fuel lines excessively can lead to reduced flexibility, potential damage, and even fuel leaks over time. When installing the fuel line, aim for a straight and smooth path from the fuel tank to the engine. This approach ensures that the fuel line can expand and contract without stress, reducing the risk of cracks or failures. Proper installation also allows for easier maintenance and access to the fuel system, making it a more reliable and long-lasting solution.
Avoiding Unnecessary Bends:
One of the primary goals when selecting fuel line length is to minimize unnecessary bends. Excessive bending can restrict fuel flow, leading to reduced engine performance and potential fuel starvation. To avoid this, plan the route of the fuel line carefully, ensuring it follows a direct path from the tank to the engine. Consider the vehicle's structure and available space to create a smooth and straight line. By reducing bends, you maintain the integrity of the fuel line and ensure optimal fuel delivery to the engine, resulting in improved power and efficiency.
Flexibility and Durability:
Opting for the right fuel line length also contributes to the overall flexibility and durability of the fuel system. Longer lines might require additional support or protective measures to prevent kinking or damage. However, with careful planning, you can achieve a balance between length and flexibility. A well-designed fuel line system should allow for some movement without compromising the structural integrity of the line. This flexibility is crucial, especially in vehicles with limited space, as it ensures the fuel line can adapt to various driving conditions without putting excessive strain on the material.
Performance and Safety:
The length of the fuel line directly impacts the performance and safety of your vehicle. Longer lines might require specialized fittings and connectors to ensure a secure and leak-free connection. Additionally, proper length considerations can help prevent fuel vapor buildup, which can lead to engine misfires and reduced performance. By choosing the appropriate length and ensuring a straight installation, you maintain the fuel system's efficiency and contribute to a safer driving experience.
In summary, when deciding on the best fuel line, remember that the length is not just a matter of convenience but a critical aspect of installation and performance. By considering the length and avoiding unnecessary bends, you ensure a smooth installation process, optimal fuel flow, and improved overall reliability for your vehicle's fuel system.
Understanding Fuel Line Seals: A Comprehensive Guide
You may want to see also
Fuel Line Compatibility: Match fuel type (gasoline, diesel) and engine requirements
When it comes to choosing the best fuel line for your vehicle, compatibility is key. The fuel line is a critical component in the fuel delivery system, responsible for transporting fuel from the tank to the engine. Using the right fuel line ensures optimal performance, safety, and longevity of your engine. Here's a detailed guide on how to match fuel lines to your specific needs:
Gasoline vs. Diesel:
The primary distinction lies in the fuel type. Gasoline engines require a fuel line designed to handle gasoline, while diesel engines need a fuel line compatible with diesel fuel. Gasoline fuel lines are typically made with materials that can withstand the volatility of gasoline, ensuring it doesn't degrade over time. Diesel fuel lines, on the other hand, are engineered to handle the higher pressure and lubricating properties of diesel, which can be more aggressive on fuel system components.
Engine Requirements:
Different engines have unique specifications. For instance, high-performance engines may demand fuel lines with enhanced flexibility and durability to accommodate rapid acceleration and high-stress conditions. Older or classic car engines might require specific fuel line materials to match the era's standards. Always refer to your vehicle's manual or consult a mechanic to understand the engine's unique fuel line requirements.
Material Considerations:
Fuel lines are typically made from rubber, vinyl, or synthetic materials. Rubber and vinyl are cost-effective but may not be as durable or flexible as synthetic options. Synthetic fuel lines offer superior resistance to heat, chemicals, and abrasion, making them ideal for high-performance or older vehicles. The choice of material also depends on the climate; synthetic lines are less prone to cracking in extreme temperatures.
Size and Diameter:
Fuel lines come in various diameters, and the right size is crucial for efficient fuel flow. A larger diameter line can handle higher fuel pressures and volumes, which is beneficial for high-performance engines. However, it's essential to ensure that the fuel line's diameter doesn't restrict flow in other parts of the system. Always match the fuel line's specifications to your engine's requirements.
Installation and Maintenance:
Proper installation is vital to ensure compatibility and performance. When replacing fuel lines, ensure you use the correct fittings and connectors for your specific fuel type and engine. Regular maintenance, including checking for leaks and inspecting the fuel lines for any signs of damage, is essential to prevent fuel-related issues.
By carefully considering fuel type, engine requirements, and material compatibility, you can select the best fuel line for your vehicle, ensuring optimal performance and reliability. Remember, using the wrong fuel line can lead to engine issues, reduced fuel efficiency, and potential safety hazards.
The Strange Sound of Frozen Fuel Lines: A Guide
You may want to see also
Fuel Line Routing: Route lines away from heat sources and sharp bends
When it comes to fuel line routing, one of the most critical considerations is to route the lines away from heat sources and sharp bends. This practice is essential to ensure the longevity and efficient operation of your fuel system. Heat sources, such as exhaust manifolds, engine blocks, or even hot pipes, can cause the fuel lines to expand and contract rapidly, leading to potential damage over time. This is especially true for rubber fuel lines, which are more susceptible to heat-related degradation. By keeping the fuel lines away from these heat sources, you minimize the risk of cracks, leaks, and premature failure.
Additionally, sharp bends in the fuel lines can create stress points, which may lead to the development of cracks or even complete rupture. The sharp turns can cause the fuel lines to wear out faster, especially at the points where the bends occur. To avoid this, it is recommended to use gentle curves and avoid any sharp angles. This practice ensures that the fuel lines have a smoother path, reducing the likelihood of damage and improving overall system reliability.
When routing the fuel lines, it's a good idea to follow a path that is as straight as possible. This helps to minimize the overall length of the lines, reducing the chances of kinks and bends forming. A straight path also makes it easier to identify and address any potential issues during the installation process. Furthermore, keeping the lines as short as practical is beneficial, as longer lines increase the risk of fuel vaporization and potential performance issues.
In areas where sharp bends are unavoidable, consider using flexible fuel line connectors or fittings that can accommodate the necessary angles without causing excessive stress on the line. These connectors can help distribute the force more evenly, reducing the risk of damage. It's also a good practice to use protective sleeves or shields over the fuel lines in areas where they might come into contact with sharp edges or hot surfaces, providing an extra layer of protection.
Remember, proper fuel line routing is a crucial aspect of maintaining a reliable and efficient fuel system. By routing the lines away from heat sources and sharp bends, you can significantly extend the life of your fuel lines and ensure optimal performance. This simple yet effective practice is often overlooked but can make a substantial difference in the overall health and longevity of your vehicle's fuel system.
Unveiling the Mystery: What Exactly is 6AN Fuel Line?
You may want to see also
Frequently asked questions
The optimal fuel line material depends on your vehicle's specific requirements and the type of fuel it uses. For gasoline engines, rubber or synthetic rubber-coated fuel lines are commonly used and offer good flexibility and resistance to fuel evaporation. For diesel engines, fuel lines made of steel or stainless steel are often preferred due to their durability and ability to withstand higher pressure.
The fuel line diameter is crucial for efficient fuel delivery. A larger diameter fuel line allows for higher flow rates, which can improve engine performance, especially in high-demand situations. However, it's essential to consider the vehicle's engine size, fuel pump specifications, and the overall fuel system design. Consulting the vehicle's manual or seeking advice from a mechanic can help determine the appropriate fuel line diameter.
Braided fuel lines are known for their strength and flexibility. They are often made of steel or stainless steel and feature a braided design that provides excellent resistance to fuel contamination and abrasion. Braided fuel lines are commonly used in high-performance vehicles or those with modified fuel systems, ensuring a reliable and efficient fuel supply.
While universal fuel lines are available and can be used in a pinch, it's generally recommended to use fuel lines specifically designed for your vehicle. Universal lines may not have the same level of compatibility and performance as OEM (Original Equipment Manufacturer) parts. Always refer to the vehicle's manual or consult a professional to ensure you choose the correct fuel line for your specific make and model.
Fuel lines should be inspected regularly for any signs of damage, cracks, or leaks. Over time, fuel lines can degrade due to fuel contamination, heat, and vibration. It is generally recommended to replace fuel lines every 5-10 years or whenever there are visible signs of wear and tear. Regular maintenance and timely replacements can help ensure optimal engine performance and prevent potential fuel-related issues.