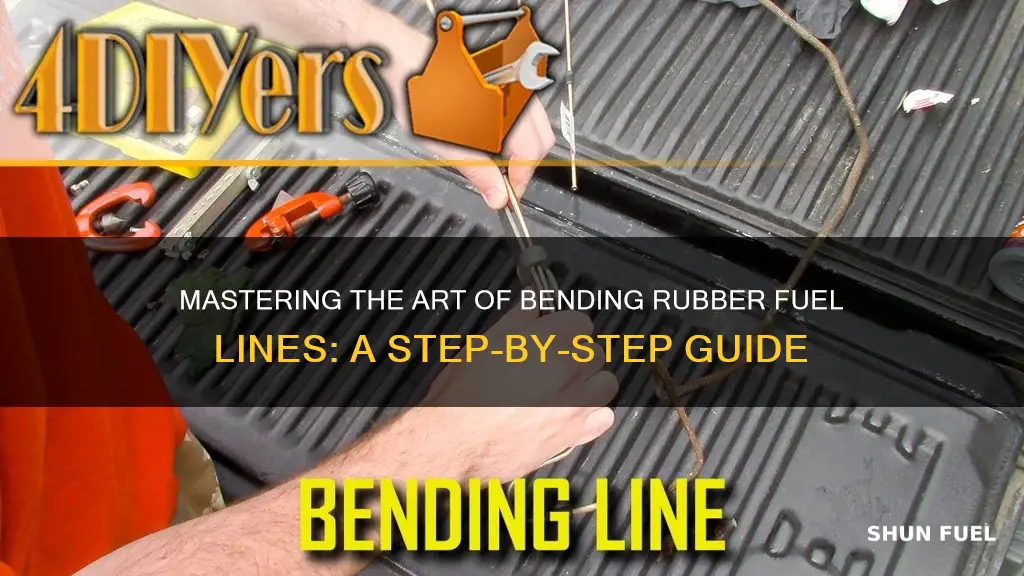
Bending a rubber fuel line is a task that requires careful technique and precision to ensure the line remains intact and functional. This process is often necessary when installing or replacing fuel lines in vehicles, as it allows for the line to be routed around obstacles or to reach specific areas. The key to successfully bending a rubber fuel line is to use the right tools and techniques to avoid damaging the line's integrity. This guide will provide a step-by-step approach to bending a rubber fuel line, ensuring a secure and reliable connection.
What You'll Learn
- Prepare the Line: Ensure the line is straight and free of kinks, using a suitable cleaning agent
- Apply Heat: Use a heat gun or torch to gradually heat the line, avoiding direct flames
- Bend with Care: Bend the line at a controlled angle, using pliers for precision
- Secure Connections: Wrap bent sections with tape to prevent unbending and ensure a tight fit
- Test for Leaks: Inspect the bent line for any cracks or leaks, replacing if necessary
Prepare the Line: Ensure the line is straight and free of kinks, using a suitable cleaning agent
To begin the process of bending a rubber fuel line, it is crucial to start with a well-prepared line. The first step is to ensure that the fuel line is straight and free of any kinks or bends that could compromise its integrity. This initial preparation is essential to avoid any potential issues during the bending process.
Begin by laying the fuel line out on a flat surface, ensuring it is as straight as possible. If the line has any existing bends or kinks, carefully straighten it out. It is important to work with the line in a controlled manner to prevent any sudden movements that could cause further damage. Use your hands or a gentle tool to manipulate the line, being mindful of its flexibility and resilience.
Next, consider using a suitable cleaning agent to remove any dirt, grime, or debris that may be present on the surface of the fuel line. This step is often overlooked but is crucial for a successful bend. Cleaning agents specifically designed for rubber or fuel lines can be used to ensure a thorough clean. These agents help to remove any contaminants that could interfere with the bonding process or affect the line's performance once bent.
When cleaning the line, pay close attention to the areas where you intend to bend it. Ensure that these sections are free from any contaminants that could weaken the material. A clean and smooth surface will allow for a more precise bend and a stronger final product. Take your time with this step, as a thorough cleaning will contribute to the overall success and longevity of the bent fuel line.
After cleaning, inspect the line to ensure it is completely dry before proceeding with the bending process. Moisture can affect the line's flexibility and may lead to issues during the bending. If any moisture is detected, gently wipe it away with a clean cloth or paper towel. This attention to detail will ensure that the line is ready for the next steps in the bending procedure.
Fuel Lines: Your Ultimate Guide to Buying and Installing
You may want to see also
Apply Heat: Use a heat gun or torch to gradually heat the line, avoiding direct flames
When working with rubber fuel lines, applying heat is a crucial step to ensure a successful bend without causing damage. Here's a detailed guide on how to use a heat gun or torch effectively:
Start by identifying the section of the fuel line that needs bending. Ensure you have a clear idea of the desired bend radius and angle. It's important to note that rubber fuel lines can be sensitive to excessive heat, so a controlled and gradual approach is key. Use a heat gun or a small torch, preferably a butane torch designed for soldering, as these tools provide more precise heat control. Set the heat gun or torch to a medium-high setting, allowing for a steady but not overly hot flame.
Now, begin heating the fuel line, moving the heat source along the length of the line you intend to bend. Keep the flame or heat gun in constant motion to ensure even heating. Avoid holding the flame or heat gun in one spot for too long, as this can lead to localized overheating and potential damage. The goal is to gradually increase the temperature of the rubber, making it more pliable and easier to manipulate.
As you heat the line, you'll notice it becoming softer and more flexible. At this point, carefully start to bend the line around the desired shape. Use your hands or a pair of pliers to guide the bend, ensuring it remains consistent and smooth. Remember, the key is to work slowly and methodically, allowing the heat to do its work without causing any sudden or extreme changes in temperature.
Once the line is bent to your satisfaction, allow it to cool down gradually. Rapid cooling can cause the rubber to shrink and become brittle. By taking your time, you'll ensure the bend remains permanent and the fuel line retains its flexibility. This method of applying heat and then carefully bending the line is a safe and effective way to work with rubber fuel lines, allowing you to make adjustments without the risk of melting or damaging the material.
Fuel Line Leaks: A Hidden Hazard or a Minor Issue?
You may want to see also
Bend with Care: Bend the line at a controlled angle, using pliers for precision
Bending a rubber fuel line requires a careful and precise approach to ensure a secure and durable connection. Here's a step-by-step guide to achieving this:
Start by identifying the section of the fuel line that needs bending. It's crucial to understand the line's natural flexibility and any potential constraints. Look for any existing bends or kinks that might affect the bending process. Mark the desired bend point with a pencil or a piece of tape to ensure accuracy.
Now, gather your tools. You'll need a pair of pliers specifically designed for bending, preferably with adjustable jaws to accommodate different materials. Ensure the pliers are clean and free of any debris that might interfere with the bending process.
Gently insert the pliers into the fuel line, positioning the jaws around the bend point. Apply pressure gradually, ensuring the jaws make firm contact with the line. The key is to bend the line at a controlled angle, avoiding sharp or abrupt bends that could compromise the material's integrity. Use your other hand to guide the line and maintain tension, preventing it from kinking or twisting.
As you bend the line, keep a close eye on the angle and pressure applied. A slight bend at a controlled angle is ideal, ensuring the line remains flexible and functional. Avoid excessive force, as it may lead to permanent deformation or even a break in the line. Precision is key here; take your time and make small adjustments until you achieve the desired bend.
Once you've reached the desired angle, release the tension and carefully remove the pliers. Inspect the bend to ensure it is neat and free of any sharp edges that could damage the fuel line or surrounding components. If needed, make small adjustments to refine the bend further. Remember, the goal is to create a smooth, continuous bend that allows the line to function optimally without compromising its flexibility.
Towing's Impact: Uncovering Fuel Line Leaks
You may want to see also
Secure Connections: Wrap bent sections with tape to prevent unbending and ensure a tight fit
When bending a rubber fuel line, it's crucial to secure the bent sections to prevent them from unbending, especially in high-vibration environments. This ensures a tight and reliable connection, minimizing the risk of fuel leaks and potential engine damage. Here's a step-by-step guide on how to achieve this:
Prepare the Materials: You'll need a high-quality electrical or duct tape, preferably made from a durable material like vinyl or rubber. Ensure the tape is wide enough to cover the bent section of the fuel line adequately.
Wrapping Technique: Start by cleaning the surface of the bent section. Remove any dirt or debris to ensure proper adhesion. Then, apply the tape in a series of overlapping layers. Begin with a base layer, wrapping the tape tightly around the bent section, ensuring it adheres well. Overlap the tape slightly, creating a secure bond. Add additional layers, maintaining the overlapping pattern, until you've covered the entire bent area. The key is to apply enough pressure to create a tight seal.
Securing the Tape: After wrapping the tape, secure the ends to prevent them from peeling off. You can use a small piece of tape to create a small 'anchor' at the end of each layer, ensuring the tape stays in place. Alternatively, you can use a small amount of rubber cement or a similar adhesive to bond the tape firmly.
Testing and Inspection: Once the tape is applied, test the bent section by gently flexing it. Ensure it remains securely in place without any movement. Inspect the entire length of the fuel line to identify any potential weak points and reinforce them accordingly.
By following these steps, you can effectively secure the bent sections of a rubber fuel line, ensuring a tight fit and preventing unwanted unbending. This method is particularly useful for fuel lines in vehicles or machinery, where durability and reliability are essential. Remember, proper securing of the fuel line is a critical aspect of maintaining a safe and efficient fuel system.
Fuel Line Routing: A Guide to Running Lines to Your YS 60 Motor
You may want to see also
Test for Leaks: Inspect the bent line for any cracks or leaks, replacing if necessary
Before you begin bending the rubber fuel line, it's crucial to ensure that the process is done correctly and safely. One of the most critical steps in this process is testing for leaks to prevent any potential issues. Here's a detailed guide on how to inspect the bent line for cracks or leaks and take the necessary actions:
Step 1: Visual Inspection
Start by carefully examining the bent rubber fuel line. Look for any visible signs of damage, such as cracks, tears, or bulges. These defects could indicate potential leak points. Pay close attention to the areas where the line has been bent, as these points can be more susceptible to wear and tear. Use a bright flashlight to illuminate the line and inspect it thoroughly, ensuring you don't miss any small cracks or imperfections.
Step 2: Pressure Test
A pressure test is an effective way to identify leaks. You can use a simple setup by attaching a pressure gauge to the fuel line and inflating it to a moderate pressure. Then, observe the line for any signs of leakage. If you notice any fuel escaping, it's a clear indication of a damaged or cracked line. Make sure to release the pressure safely and avoid over-pressurizing the line.
Step 3: Soapy Water Test
For a more comprehensive inspection, use a soapy water solution. Fill a spray bottle with water and add a few drops of dish soap. Spray the soapy water onto the bent fuel line and observe for any bubbles. Bubbles indicate the presence of air or fuel escaping, which could be a sign of a leak. This method is particularly useful for hard-to-reach areas.
Step 4: Replacement
If you find any cracks, tears, or leaks during the inspection, it's essential to replace the damaged fuel line immediately. Rubber fuel lines are designed to be flexible, but they can degrade over time due to various factors like heat, UV exposure, and fuel contamination. If the line is old or shows significant damage, it's best to replace it to avoid potential fuel leaks and ensure the safety of your vehicle.
Remember, regular maintenance and inspection of fuel lines are vital to prevent costly repairs and ensure the efficient operation of your vehicle's fuel system. Always follow safety protocols when working with fuel lines, and if you're unsure, consult a professional mechanic.
Clear Vinyl Tubing: A Fuel Line Alternative?
You may want to see also
Frequently asked questions
Bending a rubber fuel line requires caution and the right tools to avoid damage. Start by identifying the section of the line you need to bend and use a fuel line bender or a pair of pliers designed for this purpose. Apply gentle pressure and work the bender or pliers along the line to create a smooth curve. Avoid sharp bends or kinks, as they can compromise the line's integrity.
While regular pliers can be used in a pinch, it's not the most effective or safe method. Regular pliers may not provide the necessary grip and control, and they can also damage the rubber material. It's best to use specialized tools designed for fuel line bending to ensure a clean and safe bend.
If the fuel line has a small tear or puncture, it's crucial to replace it entirely rather than attempting to bend it. Bending a damaged line can exacerbate the issue and potentially lead to fuel leaks, which pose a fire hazard. Always prioritize safety and consult a professional for proper repairs or replacements.
Yes, it's essential to work slowly and apply consistent pressure when bending the fuel line. Avoid sudden movements or excessive force, as this can cause the line to kink or crack. Take your time and make small adjustments until you achieve the desired bend without compromising the line's integrity.
To ensure the bend stays in place, you can use a small amount of fuel line adhesive or tape at the bend point. This will provide additional support and help maintain the shape. However, be cautious not to over-tighten or apply excessive force, as it might restrict fuel flow. Regularly inspect the bent areas for any signs of wear or damage.