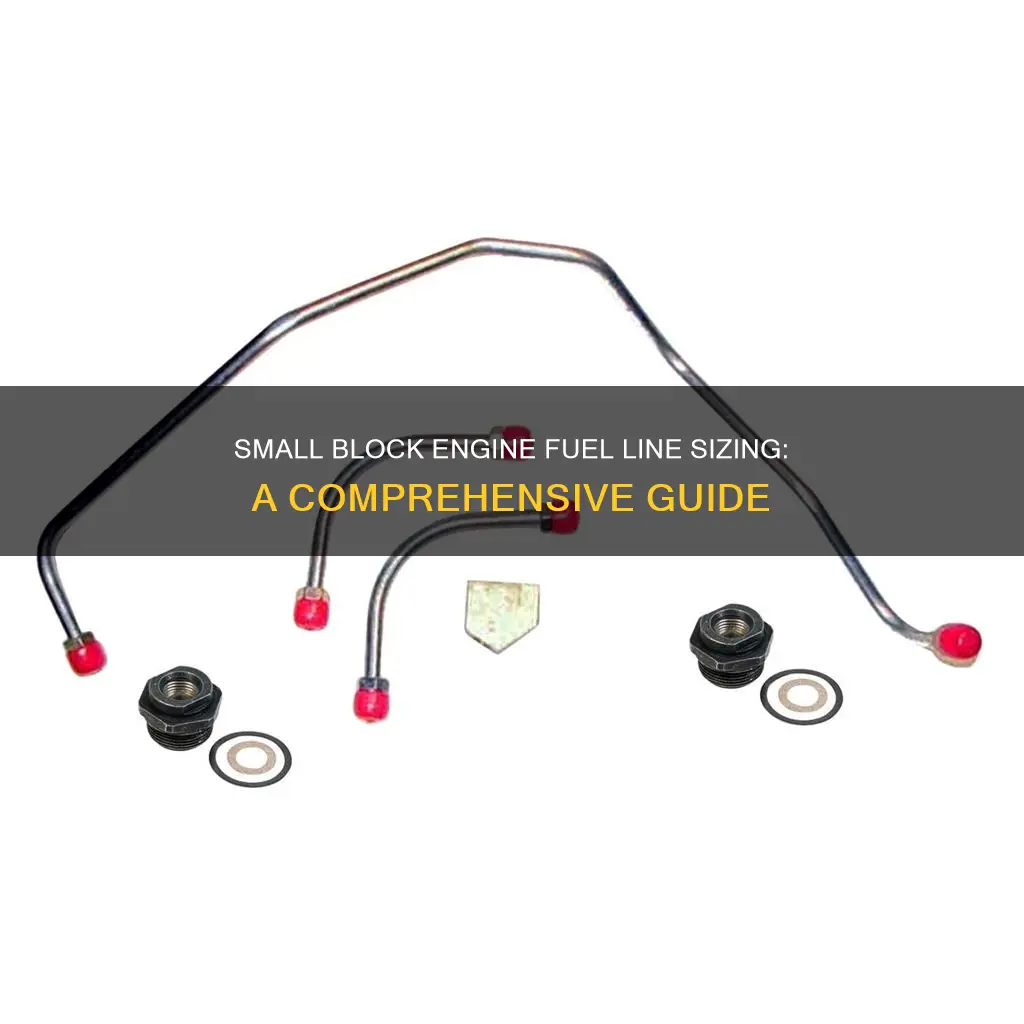
When it comes to small block engines, choosing the right fuel line size is crucial for optimal performance. The fuel line acts as the highway for gasoline, delivering it from the fuel tank to the engine's carburetor or fuel injectors. In this guide, we'll explore the factors that determine the ideal fuel line size for small blocks, ensuring your engine receives the necessary fuel for efficient operation.
Characteristics | Values |
---|---|
Fuel Line Diameter | Typically 3/8" to 1/2" for small-block engines, but can vary based on engine size and performance requirements. |
Material | Common materials include steel, stainless steel, and aluminum. Stainless steel is often preferred for its durability and resistance to corrosion. |
Length | The length of the fuel line should be sufficient to reach from the fuel pump to the carburetor or fuel injectors, considering any bends and turns in the routing. |
Flexibility | Fuel lines should be flexible enough to accommodate engine movement without kinking or restricting fuel flow. |
Pressure Rating | Choose a fuel line with an appropriate pressure rating to handle the fuel pump's output and ensure reliable fuel delivery. |
Compatibility | Ensure the fuel line is compatible with the engine's fuel type (gasoline, ethanol, etc.) and the fuel system design. |
Routing | Proper routing is crucial to avoid interference with engine components and to maintain a straight path from the pump to the carburetor/injectors. |
Clamping | Use appropriate clamps to secure the fuel line to the engine and ensure a tight, leak-free connection. |
Quality | Opt for high-quality fuel lines from reputable manufacturers to ensure reliability and longevity. |
What You'll Learn
- Engine Power: Determine fuel flow rate based on engine power output
- Fuel Pressure: Higher pressure requires larger fuel lines to prevent restriction
- Line Material: Choose fuel-resistant material like stainless steel or EPDM rubber
- Line Diameter: Smaller lines reduce pressure drop, larger lines increase flow
- Routing: Keep fuel lines short and direct to minimize pressure loss
Engine Power: Determine fuel flow rate based on engine power output
When it comes to optimizing the performance of a small-block engine, understanding the relationship between engine power output and fuel flow rate is crucial. Engine power is directly influenced by the amount of fuel delivered to the engine, and thus, determining the appropriate fuel flow rate is essential for achieving optimal performance.
The first step in determining the fuel flow rate is to consider the engine's power output. Engine power is typically measured in horsepower (hp) or kilowatts (kW). Higher power outputs generally require more fuel to sustain the increased performance. As a general rule, for every 1 hp of engine power, you will need approximately 0.1 to 0.2 gallons per minute (gpm) of fuel flow. For example, if your small-block engine produces 200 hp, you would need a fuel flow rate of around 20 to 40 gpm.
However, it's important to note that this is a simplified guideline, and actual fuel flow requirements may vary depending on several factors. Engine efficiency, load conditions, and the specific design of the fuel injection system all play a role in determining the optimal fuel flow rate. For instance, a well-tuned engine with efficient combustion may require less fuel per horsepower compared to a less efficient engine.
To accurately determine the fuel flow rate, it is recommended to use a fuel flow meter or consult the engine manufacturer's specifications. These tools will provide precise measurements of the fuel required for a given power output. Additionally, monitoring the engine's performance and adjusting the fuel flow rate accordingly can help fine-tune the engine's operation and ensure it runs efficiently within the desired power range.
In summary, when dealing with a small-block engine, matching the fuel flow rate to the engine's power output is vital for optimal performance. By understanding the relationship between power and fuel, and considering various influencing factors, you can ensure that your engine receives the right amount of fuel to produce the desired power output while maintaining efficiency and reliability.
Understanding Fuel Lines: A1 vs. B1 Differences Explained
You may want to see also
Fuel Pressure: Higher pressure requires larger fuel lines to prevent restriction
When it comes to fuel systems in small-block engines, fuel pressure is a critical factor that can significantly impact performance. Higher fuel pressure is often desired to ensure efficient atomization and proper combustion, especially in high-performance applications. However, it's essential to understand that increased pressure requires careful consideration of fuel line sizing to avoid unnecessary restrictions.
The relationship between fuel pressure and line size is straightforward: higher pressure demands larger-diameter fuel lines to accommodate the flow without causing bottlenecks. Smaller lines with higher pressure can lead to restrictions, which in turn reduce performance and may even cause engine issues. This is because fuel lines act as a conduit for the fuel, and the size of the line directly influences the flow rate and pressure drop.
To calculate the appropriate fuel line size, you need to consider the fuel pressure and the desired flow rate. A common rule of thumb is to use a fuel line with an inside diameter that is at least 1.5 times the square root of the fuel pressure in psi. For instance, if your small-block engine operates at 10 psi, you should aim for a fuel line with an inside diameter of approximately 2.5 inches (6.35 cm) or more. This ensures that the line can handle the pressure without restricting the fuel flow.
In practice, you might encounter fuel lines with various sizes, typically ranging from 3/8 inch to 1/2 inch in diameter. For higher pressure applications, opting for larger sizes like 5/16 inch or even 3/8 inch can be beneficial. It's crucial to remember that the fuel line's length also plays a role, as longer lines may introduce additional restrictions. Therefore, keeping the fuel line as short as possible is generally recommended to minimize potential pressure drops.
In summary, when dealing with small-block engines and higher fuel pressure, selecting the appropriate fuel line size is vital. Larger lines are necessary to prevent restrictions and ensure optimal performance. By understanding the relationship between pressure and line size, enthusiasts can fine-tune their fuel systems for improved power and efficiency.
Powerful Engine Demands: Choosing the Right Fuel Line for 1000 HP
You may want to see also
Line Material: Choose fuel-resistant material like stainless steel or EPDM rubber
When it comes to selecting the appropriate fuel line for your small-block engine, one of the most critical factors to consider is the material of the fuel line itself. The choice of material is essential to ensure the longevity and reliability of your fuel system, especially in high-performance applications. The primary goal is to choose a material that can withstand the corrosive nature of fuel and the extreme temperatures it may encounter.
Fuel-resistant materials are designed to combat these challenges. Stainless steel is an excellent option for fuel lines due to its inherent corrosion resistance. It is a durable material that can handle the harsh conditions of fuel, including its potential to contain harmful contaminants. Stainless steel fuel lines are known for their strength and flexibility, making them a popular choice for high-performance engines. This material is also highly resistant to oxidation, ensuring that the fuel line remains in optimal condition over an extended period.
Another viable option for fuel-line material is EPDM (Ethylene Propylene Diene Monomer) rubber. EPDM is a synthetic rubber that offers excellent resistance to fuel and temperature variations. It is a cost-effective solution that provides reliable performance without compromising on durability. EPDM fuel lines are flexible and can accommodate slight engine movements, ensuring a secure and tight connection. This material is also known for its ability to resist cracking and aging, making it a long-lasting choice for fuel systems.
The choice between stainless steel and EPDM rubber depends on various factors, including your specific engine requirements, budget, and personal preferences. Stainless steel is often preferred for its superior strength and longevity, especially in racing or high-performance applications where fuel temperatures can soar. On the other hand, EPDM rubber is an excellent choice for street cars or daily drivers, offering a balance between performance and cost.
In summary, when selecting fuel lines for your small-block engine, opt for fuel-resistant materials such as stainless steel or EPDM rubber. These materials ensure that your fuel system remains reliable and efficient, even under demanding conditions. By choosing the right material, you contribute to the overall performance and longevity of your engine, making it a crucial aspect of your vehicle's maintenance.
Optimizing Performance: Choosing the Right Fuel Line for Your 2001 Polaris Indy 500
You may want to see also
Line Diameter: Smaller lines reduce pressure drop, larger lines increase flow
When it comes to fuel lines for a small-block engine, the diameter of the line is a critical factor to consider. The size of the fuel line directly impacts the flow rate and pressure drop within the system. Smaller fuel lines have a reduced diameter, which means they offer less resistance to the flow of fuel. This reduced resistance allows for a more efficient transfer of fuel from the tank to the engine, ensuring that the engine receives the necessary amount of fuel for optimal performance. By using smaller lines, you can minimize pressure drop, which is the reduction in pressure as the fuel travels through the line. A lower pressure drop means that the fuel can maintain its pressure, ensuring a consistent and reliable fuel supply to the engine.
On the other hand, larger fuel lines have a greater diameter, which provides increased flow capacity. When the line diameter is larger, it allows for a higher volume of fuel to pass through per unit of time. This is particularly important in high-performance applications where the engine requires a rapid and efficient fuel supply to meet its power demands. Larger lines can handle higher flow rates, ensuring that the engine receives the required fuel quickly and effectively. However, it's essential to note that larger lines may also increase the overall system cost and complexity, as they require more material and careful routing to avoid interference with other engine components.
The choice between smaller and larger fuel lines depends on the specific requirements of your small-block engine. If you're aiming for maximum performance and need to supply fuel rapidly to the engine, larger lines might be preferable. However, for most everyday driving conditions, smaller lines are often sufficient and provide a cost-effective solution. Smaller lines are easy to install and maintain, making them a popular choice for enthusiasts who want to enhance their engine's performance without adding excessive complexity.
In summary, the line diameter is a crucial consideration when determining the appropriate fuel line size for a small-block engine. Smaller lines reduce pressure drop, ensuring a consistent fuel supply, while larger lines increase flow capacity, catering to high-performance needs. Understanding the impact of line diameter on flow and pressure drop will help you make an informed decision to optimize your engine's performance and fuel delivery system.
Unveiling the Power of 8AN Fuel Lines: A Comprehensive Guide
You may want to see also
Routing: Keep fuel lines short and direct to minimize pressure loss
When it comes to optimizing fuel delivery for a small-block engine, one crucial aspect often overlooked is the routing of the fuel lines. Proper routing is essential to ensure efficient and reliable fuel supply, especially in high-performance applications where every ounce of power matters. The primary goal here is to minimize pressure loss, which can significantly impact engine performance and fuel efficiency.
The key principle in routing fuel lines is simplicity and directness. Fuel lines should be kept as short and direct as possible to reduce the distance fuel has to travel from the fuel pump to the engine. This approach minimizes the potential for pressure drops due to the inherent resistance of fuel lines. Longer lines can lead to increased fuel pressure drop, especially at higher flow rates, which may result in reduced power and even engine misfires.
To achieve this, start by positioning the fuel pump as close to the engine as feasible. This placement ensures that the fuel lines are short and straight, reducing the risk of kinks and bends that can impede fuel flow. From the pump, the lines should be routed directly to the fuel injectors or the carburetor, depending on the engine setup. Avoid any unnecessary bends or turns, as these can create restrictions and increase pressure loss.
In addition to keeping the lines short, consider the use of fuel line protectors or sleeves to minimize friction and potential damage. These protectors can be especially useful when routing lines through engine compartments with sharp edges or protruding components. By using protective sleeves, you not only ensure a longer lifespan for the fuel lines but also maintain optimal fuel flow.
Lastly, proper routing also involves considering the engine's mounting positions and available space. Fuel lines should be routed away from hot surfaces and high-temperature areas to prevent fuel degradation and potential safety hazards. With careful planning and execution, you can ensure that your small-block engine receives the clean, pressurized fuel it needs to perform at its best.
The Ultimate Guide to Choosing the Right Size Clamp for Your 1/4" Fuel Line
You may want to see also
Frequently asked questions
The size of the fuel line depends on various factors, including the engine's power output, fuel pump capacity, and desired flow rate. For a small block engine, a common recommendation is to use a fuel line with an inside diameter (ID) of 3/8 inches. This size provides a good balance between fuel flow and flexibility, ensuring efficient delivery of fuel to the engine while maintaining a reasonable pressure drop.
While using a larger fuel line might seem like an easy way to boost performance, it's not always beneficial. A larger ID fuel line can lead to increased pressure drop, especially at higher engine speeds. This may result in reduced fuel pressure and potential performance losses. It's best to stick with the recommended size or slightly larger, depending on your specific engine requirements.
The length of the fuel line is crucial to ensure optimal fuel delivery. A general guideline is to keep the fuel line as short as possible while still allowing for easy access and routing. For a small block engine, a fuel line length of around 12-18 inches is often sufficient. Properly routing the line away from heat sources and sharp bends can also help maintain fuel pressure and ensure reliable operation.