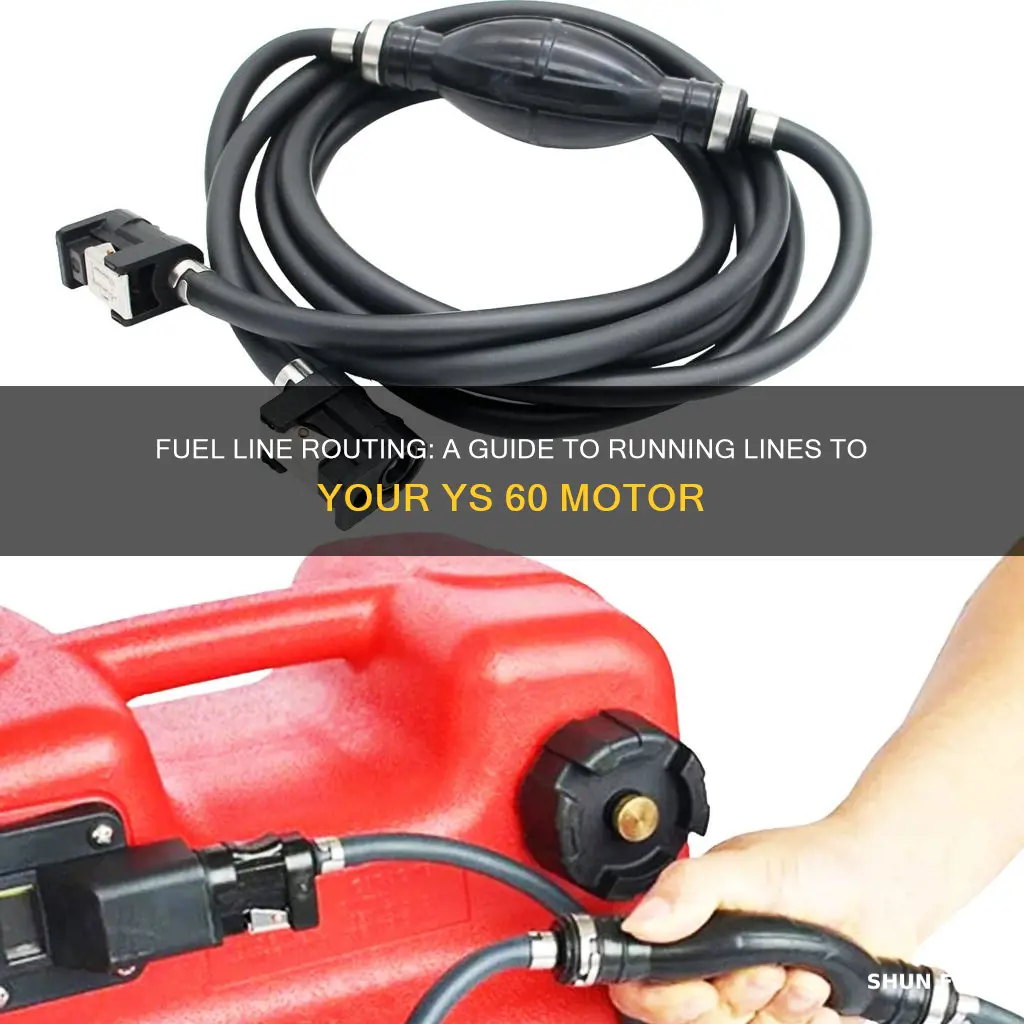
Running fuel lines to a Yamaha 60 motor requires careful planning and execution to ensure optimal performance and safety. This process involves several steps, including selecting the appropriate fuel line material, understanding the motor's fuel requirements, and properly routing the lines to the engine. It's crucial to consider factors such as fuel pressure, temperature, and vibration resistance when choosing the fuel line. Additionally, proper installation techniques, such as using the right fittings and ensuring secure connections, are essential to prevent leaks and maintain the motor's efficiency. This guide will provide a comprehensive overview of the process, offering valuable insights for anyone looking to successfully connect fuel lines to their Yamaha 60 motor.
What You'll Learn
- Location: Identify optimal spots for fuel lines, considering engine size and layout
- Material: Choose appropriate fuel line material for durability and flexibility
- Routing: Plan a safe path for lines, avoiding heat sources and sharp bends
- Fittings: Select compatible fittings for secure connections and leak prevention
- Testing: Inspect fuel lines for leaks and ensure proper fuel flow
Location: Identify optimal spots for fuel lines, considering engine size and layout
When planning the routing of fuel lines for a YS60 motor, it's crucial to consider the engine's size and layout to ensure optimal performance and reliability. The goal is to minimize fuel line length while maintaining a secure and efficient connection to the fuel source. Here's a detailed guide on identifying the best locations for fuel lines:
Engine Compartment Layout: Start by examining the YS60 engine's layout within the vehicle. Note the positions of the fuel tank, fuel pump, and the engine's various components. Typically, the fuel pump is located close to the tank, and the engine's intake manifold or carburetor will be where the fuel needs to reach. Aim to route the fuel lines in a way that minimizes bends and twists, as sharp angles can restrict fuel flow and cause pressure drops.
Fuel Tank Position: The location of the fuel tank is critical. If it's positioned low in the vehicle, you might consider running the fuel line along the frame or under the vehicle to keep it close to the ground, reducing the risk of damage from bumps or vibrations. Alternatively, if the tank is higher, you can route the line vertically, ensuring it's securely fastened to avoid any potential leaks.
Fuel Pump and Line Routing: The fuel pump should be positioned to ensure easy access for maintenance and to allow for sufficient cooling. Route the fuel line from the pump to the engine, keeping it as straight as possible. Avoid crossing over other components or running it along the bottom of the engine bay, as this can restrict access and potentially cause damage during engine operation.
Intake Manifold or Carburetor: When connecting to the engine, ensure the fuel line reaches the intake manifold or carburetor efficiently. If the engine has a carburetor, position the line to allow for easy adjustment and maintenance. For engines with fuel injection, the line should be directed towards the fuel injectors, ensuring a precise and controlled fuel supply.
Security and Flexibility: Consider using fuel line clips or ties to secure the lines, ensuring they don't interfere with other components or moving parts. Allow for some flexibility in the routing to accommodate engine movement during operation. This balance between security and flexibility will help prevent fuel line damage and ensure optimal performance.
Fuel Line Sources for 2000 Mercury Mountaineer: Quick and Easy Access
You may want to see also
Material: Choose appropriate fuel line material for durability and flexibility
When it comes to running fuel lines to a YS60 motor, choosing the right material is crucial for ensuring durability and flexibility. The fuel lines need to withstand the high pressure and temperature of the engine, as well as any vibrations and movements it may experience during operation. Here are some key considerations for selecting the appropriate material:
Durability: The primary requirement for fuel line material is durability. The lines should be able to resist wear and tear, especially in areas where they are exposed to the engine's harsh environment. Look for materials that are resistant to fuel degradation, such as ethanol-resistant rubber or synthetic compounds. These materials will ensure that the fuel lines remain intact and functional over time, even with frequent use.
Flexibility: Flexibility is another essential factor. Fuel lines need to be able to move and bend without kinking or cracking. This is particularly important when the motor is in motion, as the lines will experience various angles and positions. Choose materials that offer a good balance of flexibility and strength. Rubber compounds with a higher durometer (hardness) can provide the necessary rigidity while still allowing for some flexibility. Alternatively, consider using braided fuel lines, which offer excellent flexibility and can withstand tight bends without compromising performance.
Temperature Resistance: The YS60 motor generates significant heat, so the fuel lines must be able to withstand elevated temperatures. Select materials that have a high temperature resistance, typically measured in degrees Celsius or Fahrenheit. This ensures that the lines remain pliable and do not become brittle or crack under the engine's operating conditions.
Compatibility: Ensure that the chosen material is compatible with the fuel type used in your application. Different fuels may have varying chemical properties, and some materials may react or degrade when exposed to certain fuels. Check the manufacturer's guidelines or consult experts to determine the best material for your specific fuel type.
Installation and Maintenance: Consider the ease of installation and maintenance when selecting the material. Some materials may require special tools or techniques for installation, while others may be more susceptible to damage during the setup process. Additionally, materials that are easy to inspect and replace if necessary will contribute to the overall longevity of the fuel line system.
Unraveling the Smelly Mystery: Why Braided Fuel Lines Stink
You may want to see also
Routing: Plan a safe path for lines, avoiding heat sources and sharp bends
When routing fuel lines to your YS60 motor, it's crucial to prioritize safety and efficiency. Begin by studying the engine's layout and identifying the optimal path for the fuel lines. Aim to keep the lines as straight as possible to minimize potential issues. Avoid running the lines alongside hot engine components or exhaust systems, as this can lead to fuel line damage or contamination. Instead, plan a route that provides a safe distance from heat sources.
Consider the engine's mounting points and available space when planning the route. You might need to use brackets or ties to secure the lines in place, ensuring they remain taut and free from any sharp bends or kinks. Aim for a layout that allows for easy access during maintenance and inspection.
The choice of fuel line material is essential. Opt for high-temperature-rated materials to withstand the engine's operating conditions. Flexible fuel lines with a protective outer layer are ideal, ensuring durability and resistance to heat and abrasion.
Pay close attention to the bends in the fuel lines. Avoid sharp bends, as they can restrict fuel flow and potentially cause damage over time. Instead, create gentle curves, allowing for a smooth flow of fuel. Use bends that are gradual and wide enough to prevent stress on the line.
Additionally, consider the use of fuel line protectors or sleeves, especially if the lines will be routed near the exhaust or other hot surfaces. These protectors provide an extra layer of insulation and help prevent heat-related damage. Proper routing and the use of suitable materials will ensure a reliable and long-lasting fuel system for your YS60 motor.
Choosing the Right Fuel Line for Your Lawn Mower: A Guide
You may want to see also
Fittings: Select compatible fittings for secure connections and leak prevention
When it comes to running fuel lines to your YS 60 motor, selecting the right fittings is crucial for ensuring secure connections and preventing leaks. The goal is to create a reliable and efficient fuel delivery system that can withstand the demands of your engine. Here's a detailed guide on choosing the appropriate fittings:
Material Compatibility: Begin by considering the material compatibility between the fuel lines, fittings, and your motor. Different materials have varying levels of resistance to fuel degradation. For instance, natural rubber fuel lines are commonly used due to their flexibility and compatibility with gasoline. However, if you're dealing with diesel or certain types of fuel, you might need to opt for fittings made from materials like nitrile or fluoropolymer, which offer better resistance to fuel-related chemicals.
Fitting Types: There are various types of fittings available, each serving a specific purpose. The most common types include barbed fittings, compression fittings, and quick-connect fittings. Barbed fittings are ideal for creating a temporary connection and are often used for testing or short-term applications. Compression fittings provide a secure, leak-resistant seal by compressing the fuel line against the fitting. Quick-connect fittings offer convenience and ease of use, allowing for rapid assembly and disassembly. Choose the fitting type that best suits your project's requirements and the level of accessibility you need.
Size and Thread Compatibility: Ensure that the fittings you select are compatible with the size and thread of your fuel lines. Fuel lines typically come in standard sizes, such as 3/8" or 1/4" ID (inside diameter). Measure the inside diameter of your fuel lines and choose fittings with matching threads. Using the wrong size can result in a poor connection, leading to fuel leaks or reduced performance.
Leak-Proof Design: Look for fittings that feature a robust, leak-proof design. This is essential to prevent fuel spills and potential hazards. Compression fittings, for example, often include O-rings or sealing washers that create a tight seal around the fuel line. Quick-connect fittings should have secure locking mechanisms to ensure a reliable connection. Inspect the fittings for any signs of damage or wear, as this can compromise their ability to prevent leaks.
Durability and Weather Resistance: Consider the environmental conditions your fuel system will operate in. If your motor is exposed to varying temperatures or harsh weather, opt for fittings made from durable materials that can withstand these conditions. For instance, UV-resistant fittings are ideal for outdoor applications to prevent degradation from sunlight. Additionally, ensure that the fittings can handle the pressure and flow rates expected in your fuel system.
The Fuel Tank's Double Line: A Safety Feature Explained
You may want to see also
Testing: Inspect fuel lines for leaks and ensure proper fuel flow
When setting up fuel lines for a YS60 motor, it's crucial to test the system thoroughly to ensure it's leak-free and functioning correctly. This testing process involves a series of steps to verify the integrity of the fuel lines and the overall fuel delivery system. Here's a detailed guide on how to inspect and test the fuel lines:
Leak Testing: Begin by applying a small amount of diesel fuel or a suitable leak detection fluid to the fuel lines. This can be done by connecting a small syringe or a dropper to the fuel line and carefully injecting the fluid. Pay close attention to all connections, including the fuel pump, fuel filter, and the motor itself. Inspect the lines for any signs of fuel seepage or leaks. Leaks can occur at connections, fittings, or where the lines attach to the motor. Use a rag or paper towel to wipe the lines and connections, and check for any fuel residue. If you notice any leaks, tighten connections or replace damaged parts to ensure a secure and leak-free setup.
Pressure Testing: After ensuring no leaks, it's essential to check the fuel pressure. Use a fuel pressure gauge to measure the pressure at the fuel pump outlet. The pressure should be within the specified range for your YS60 motor. If the pressure is too low, it may indicate a restricted fuel line or a problem with the fuel pump. Adjustments or repairs may be necessary to ensure optimal fuel flow.
Flow Testing: Proper fuel flow is critical for the engine's performance. Set up a fuel flow meter or use a calibrated container to measure the volume of fuel flowing through the lines over a specific time period. Compare the measured flow rate with the expected rate based on the motor's specifications. If the flow rate is inconsistent or too low, it could indicate blockages or issues with the fuel pump or filter. Address these problems to ensure a steady and adequate fuel supply.
Visual Inspection: While testing, also perform a visual inspection of the fuel lines for any signs of damage, cracks, or deterioration. Look for any bends or kinks that might restrict fuel flow. Ensure that the lines are properly routed and not rubbing against any sharp edges or surfaces that could cause damage. A thorough visual check will help identify potential issues before they cause problems during operation.
Start-Up and Monitoring: Once all the testing is complete, start the engine and monitor its performance. Listen for any unusual noises and watch for any warning lights or indicators. Ensure that the engine starts smoothly and runs without any issues. If everything is functioning as expected, your fuel line setup is ready for operation. Regularly monitor the engine's performance and fuel consumption to ensure the system remains reliable over time.
Mastering GM Fuel Pump: Tips for Removing Fuel Line Fittings
You may want to see also
Frequently asked questions
Running fuel lines to a YS60 motor involves a few steps to ensure a proper and safe fuel supply. First, you'll need to determine the fuel requirements of your motor and the appropriate gauge of fuel line. Typically, a YS60 motor will require a fuel line with a diameter of 3/8" or 1/2" to handle the fuel flow efficiently. Start by locating the fuel tank and the motor's fuel inlet. Use a suitable fuel line material, such as vinyl or rubber, that can withstand fuel pressure and temperature. Secure the fuel line with clamps or fittings to ensure a tight connection. It's crucial to route the fuel line away from heat sources and sharp edges to prevent damage. Consider using a fuel filter to ensure clean fuel delivery. Finally, double-check all connections and ensure there are no leaks before starting the engine.
When connecting fuel lines to a YS60 motor, it's recommended to use fuel-rated fittings specifically designed for fuel systems. These fittings are typically made of materials like brass or stainless steel to ensure durability and resistance to corrosion. Look for fittings with a male and female thread that matches the fuel line's internal diameter. Common types include quick-connect fittings, barbed fittings, and compression fittings. Ensure you have the correct size and thread pitch for your fuel lines. Always clean and deburr the threads before assembly to create a tight seal.
Yes, using a fuel pump is a common practice when running fuel lines to a YS60 motor. A fuel pump helps deliver fuel at the required pressure to the engine. You can choose between a mechanical fuel pump, which is driven by the engine's camshaft, or an electric fuel pump, which is powered by a separate battery. When selecting a fuel pump, consider the motor's displacement and the desired fuel flow rate. Ensure the pump's outlet size matches the fuel line's diameter. Properly mount the fuel pump and secure the fuel lines to the pump's output and the motor's inlet.
Preventing fuel leaks is essential for a safe and efficient fuel system. Here are some tips: Always use fuel-resistant clamps or fittings to secure the fuel lines. Ensure a tight connection by tightening the clamps or fittings according to the manufacturer's instructions. Check for any sharp bends or kinks in the fuel lines, as these can cause leaks. Route the fuel lines away from moving parts and heat sources. Use fuel line protectors or sleeves to shield the lines from potential damage. Regularly inspect the fuel lines for any signs of wear, cracks, or damage, and replace them if necessary.
Choosing the right fuel filter is crucial to maintain a clean fuel supply to your YS60 motor. Consider using a high-quality fuel filter designed for high-pressure fuel systems. A 3/8" or 1/2" fuel filter with a mesh or paper element is commonly used for this motor. The filter should have a suitable flow rate to handle the expected fuel volume. Mount the filter inline between the fuel pump and the motor's fuel inlet. Regularly check and replace the fuel filter to ensure optimal performance and prevent engine issues caused by contaminated fuel.