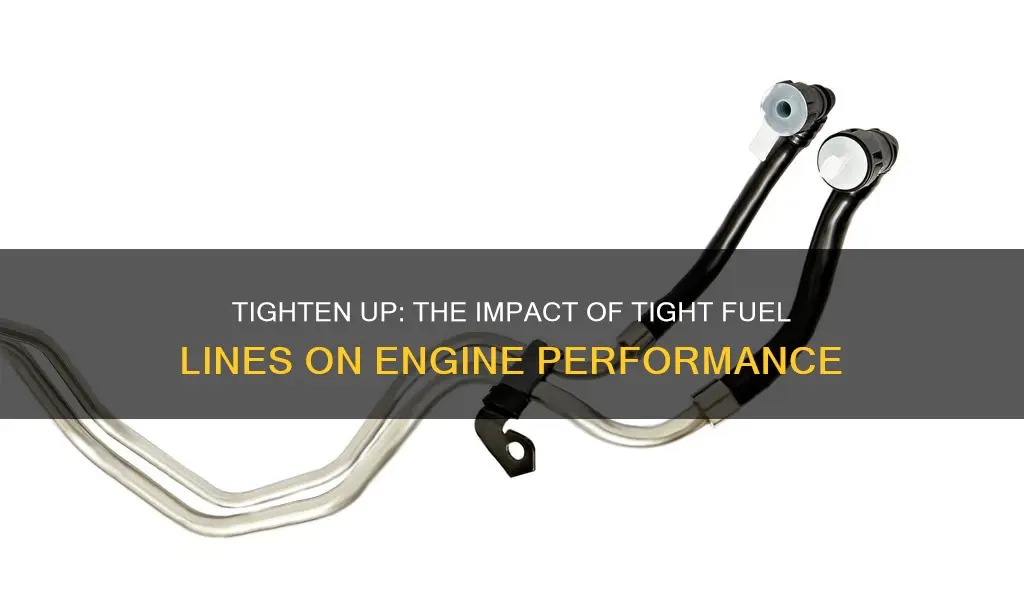
Tight fuel lines are a critical component in the efficient operation of any vehicle's fuel system. When fuel lines are too loose, they can cause fuel leaks, which can lead to dangerous situations such as engine fires or explosions. Conversely, when fuel lines are too tight, they can restrict fuel flow, leading to poor engine performance and potential damage to the fuel system. Understanding how to properly install and maintain fuel lines is essential for ensuring the safety and reliability of any vehicle. This guide will explore the importance of tight fuel lines and provide practical tips for ensuring optimal performance and longevity of the fuel system.
What You'll Learn
- Fuel Line Material: Choose the right material for tight fuel lines, considering flexibility and durability
- Clamping Techniques: Secure fuel lines with appropriate clamps to prevent leaks and ensure a tight fit
- Routing and Bending: Route fuel lines carefully, avoiding sharp bends to prevent damage and maintain tightness
- Pressure Testing: Conduct pressure tests to ensure fuel lines are tight and leak-free
- Maintenance and Inspection: Regularly inspect and maintain fuel lines to prevent leaks and ensure optimal performance
Fuel Line Material: Choose the right material for tight fuel lines, considering flexibility and durability
When dealing with tight fuel lines, the choice of material is critical to ensure optimal performance and longevity. The primary concern with tight fuel lines is the potential for excessive wear and tear, which can lead to leaks and other issues. Therefore, selecting a material that offers both flexibility and durability is essential.
One of the most commonly used materials for fuel lines is rubber. Rubber is known for its flexibility, making it ideal for tight spaces and bends. It can accommodate slight movements and vibrations without compromising the integrity of the fuel line. Additionally, rubber is resistant to most fuels, including gasoline and diesel, ensuring that it can withstand the corrosive effects of these substances. However, it's important to note that rubber fuel lines may not be as durable as other materials, especially in extreme temperature conditions.
For applications requiring higher durability, synthetic materials like polyurethane or EPDM (Ethylene Propylene Diene Monomer) are excellent choices. These materials offer superior resistance to fuel degradation and temperature fluctuations. Polyurethane, in particular, is known for its flexibility and ability to resist abrasion, making it suitable for tight fuel lines that may experience frequent movement. EPDM, on the other hand, is highly resistant to ozone and UV radiation, ensuring that the fuel lines remain intact even in harsh environmental conditions.
Another consideration is the use of metal fuel lines, which are often made from stainless steel. While metal lines offer excellent durability and resistance to corrosion, they are less flexible and can become stiff over time, especially in tight spaces. This can lead to increased stress on the fuel line, potentially causing cracks or leaks. Therefore, metal fuel lines are typically used in applications where flexibility is less critical, such as in high-performance vehicles with ample engine bay space.
In summary, when choosing the right material for tight fuel lines, a balance between flexibility and durability is essential. Rubber provides flexibility but may lack long-term durability, while synthetic materials like polyurethane and EPDM offer superior resistance to fuel and environmental factors. Metal fuel lines are an option for specific applications, but their stiffness should be carefully considered. Understanding the unique requirements of your fuel line setup will help you make an informed decision to ensure reliable performance and longevity.
Cold Weather's Hidden Threat: Fuel Lines at Risk
You may want to see also
Clamping Techniques: Secure fuel lines with appropriate clamps to prevent leaks and ensure a tight fit
When it comes to securing fuel lines, clamping techniques are essential to prevent leaks and ensure a tight, reliable connection. The primary goal is to create a secure bond that can withstand the pressures and vibrations encountered during vehicle operation. Here's an in-depth look at the clamping process:
Choosing the Right Clamp: The first step is to select the appropriate clamp for the specific fuel line. Different fuel lines have varying diameters and materials, so using the right clamp is crucial. Common types include metal or plastic bands, which are often used for smaller lines, and larger, more robust clamps like the 'fuel line clamp' or 'fuel line tie-down' for thicker lines. The clamp should be designed to fit the fuel line snugly without causing damage or distortion.
Application Process: Start by cleaning the fuel line and the clamp to ensure a proper bond. Remove any old clamps or debris. Then, carefully wrap the clamp around the fuel line, ensuring it is centered and aligned with the line's path. The key is to apply the correct amount of pressure; it should be tight enough to secure the line but not so tight that it causes damage or restricts flow. Over-tightening can lead to fuel line damage and potential leaks.
Tightening Techniques: There are various methods to achieve the desired clamping force. One common technique is to use a 'crimping tool' for metal clamps, which applies pressure to the clamp's ends, creating a secure hold. For plastic or rubber bands, a simple hand-tightening method can be effective, but it requires practice to ensure the correct amount of tension. Always refer to the manufacturer's guidelines for specific instructions on tightening procedures.
Multiple Clamps for Complex Routes: In cases where fuel lines have complex routes or multiple bends, additional clamps may be necessary. These secondary clamps provide extra support and prevent the line from shifting or sagging. It's important to space these clamps evenly along the line to maintain a consistent tension and avoid creating pressure points that could cause damage.
Regular Inspection: Even with proper clamping, regular inspections are vital. Over time, clamps can loosen due to vibration or temperature changes. Inspect the fuel lines periodically, especially after major repairs or replacements, to ensure the clamps remain tight and secure. This proactive approach helps prevent fuel leaks, which can be costly and dangerous.
Fuel Line Size for Predator Generators: A Quick Guide
You may want to see also
Routing and Bending: Route fuel lines carefully, avoiding sharp bends to prevent damage and maintain tightness
When working with fuel lines, proper routing and bending techniques are crucial to ensure optimal performance and longevity. One of the most critical aspects is avoiding sharp bends, as these can lead to several issues. Firstly, sharp bends can cause damage to the fuel lines themselves, potentially leading to leaks or even ruptures. This is especially problematic with the high-pressure fuel lines commonly used in modern vehicles. The force exerted by the fuel pressure can cause the line to kink or split at the bend, resulting in costly repairs.
To maintain tightness and prevent these issues, it's essential to follow a few guidelines. Start by planning the route of the fuel line carefully, considering the layout of the engine bay and the positions of other components. Aim for a smooth, gradual curve rather than a sharp angle. A gentle curve will distribute the pressure evenly along the line, reducing the risk of damage. Use a flexible fuel line material that can accommodate some bending without kinking. This flexibility is key to ensuring the line can adjust to the natural contours of the engine bay without forcing sharp angles.
When bending the fuel line, use a fuel line bender or a similar tool designed for this purpose. These tools help create a consistent and controlled bend, ensuring the line remains tight and secure. Avoid using sharp objects or your hands to bend the line, as this can lead to uneven bends and potential damage. Instead, apply gentle, consistent pressure to the bender, following the desired curve.
Additionally, consider the placement of the fuel line's ends. Ensure that the connections are secure and that the line is tightly fastened to the fuel tank and engine. This tightness is essential to prevent fuel leaks and ensure the system operates efficiently. Regularly inspect the fuel lines for any signs of wear or damage, especially at the bends, and replace any lines that show signs of deterioration.
By carefully routing and bending fuel lines, avoiding sharp bends, and maintaining tightness, you can significantly reduce the risk of fuel system issues. This approach ensures the fuel lines remain in optimal condition, providing reliable performance and contributing to the overall longevity of the vehicle's fuel system. Following these practices will help keep your vehicle's fuel system running smoothly and efficiently.
Mastering the Art of Fuel Line Torque: A Comprehensive Guide
You may want to see also
Pressure Testing: Conduct pressure tests to ensure fuel lines are tight and leak-free
Pressure testing is a critical procedure to ensure the integrity and safety of fuel lines in vehicles. This methodical process involves applying controlled pressure to the fuel system to identify any potential leaks or weaknesses in the fuel lines. By simulating real-world conditions, pressure testing provides an effective way to verify the tightness and reliability of these vital components.
When conducting pressure tests, it is essential to use specialized equipment designed for this purpose. A pressure gauge and a compressed air source are typically employed. The gauge measures the pressure within the fuel lines, while the air source provides the necessary force to test for leaks. The process begins by connecting the gauge to the fuel lines and setting the pressure to a predetermined level, often slightly above the system's normal operating pressure.
During the test, the technician carefully monitors the pressure reading. Any drop in pressure indicates a potential leak, which could be caused by a faulty fuel line, a damaged connector, or a loose fitting. It is crucial to identify these issues promptly, as leaks can lead to fuel loss, reduced engine performance, and even potential safety hazards. Technicians should also inspect the fuel lines for any visible signs of damage or wear, as pressure testing alone may not detect all potential problems.
To ensure accuracy, multiple pressure tests should be conducted at different points along the fuel lines. This comprehensive approach helps identify leaks that may occur due to varying line lengths and angles. Additionally, testing at different pressure levels can reveal issues that might only become apparent under specific conditions.
In summary, pressure testing is an indispensable technique for maintaining the health and safety of fuel lines. It provides a proactive approach to identifying potential issues, allowing for timely repairs or replacements. By following this method, technicians can ensure that fuel lines are tight, leak-free, and capable of withstanding the demands of the vehicle's operation. Regular maintenance and pressure testing contribute to the overall reliability and longevity of the fuel system.
Fuel Lines vs. AC Lines: Unraveling the Differences
You may want to see also
Maintenance and Inspection: Regularly inspect and maintain fuel lines to prevent leaks and ensure optimal performance
Fuel lines are a critical component of any vehicle's fuel system, and ensuring they are in good condition is essential for optimal performance and safety. Regular maintenance and inspection of these lines can help prevent leaks, which can cause engine misfires, reduced power, and even potential fires. Here's a detailed guide on how to maintain and inspect fuel lines to keep your vehicle running smoothly.
Visual Inspection: Start by performing a visual inspection of the fuel lines. Look for any signs of damage, such as cracks, brittleness, or corrosion. Check for any visible leaks or drips around the connections and fittings. Over time, fuel lines can degrade due to heat, vibration, and chemical exposure, so it's crucial to identify any issues early on. Inspect the lines for any signs of wear, especially if they are more than a few years old.
Pressure Testing: Conducting a pressure test is an effective way to check the integrity of fuel lines. This test involves attaching a pressure gauge to the fuel line and inflating it to a specified pressure. If the line is intact, it should hold the pressure without any leaks. You can use a portable fuel pressure tester or take your vehicle to a mechanic for professional testing. This method helps identify weak spots or damaged areas that might not be visible during a visual inspection.
Tightening Connections: Fuel lines should be securely attached to the fuel tank and engine. Over time, connections can loosen due to vibration and movement. Regularly check and tighten these connections to ensure a proper seal. Use the appropriate tools to tighten the fittings, and make sure they are tightened to the manufacturer's recommended torque specifications. This simple maintenance task can prevent fuel leaks and potential engine damage.
Replacing Old Lines: If you notice any significant damage or wear during your inspections, it's crucial to replace the affected fuel lines promptly. Old or damaged lines can lead to fuel leaks, which may go unnoticed until it's too late. When replacing lines, ensure you use the correct type and size of fuel lines for your vehicle. Properly route the new lines to avoid any potential damage or interference with other components.
Regular Maintenance Checks: Incorporate fuel line inspections into your regular vehicle maintenance routine. This is especially important if you drive in harsh conditions or have a high-mileage vehicle. By making it a habit to check the fuel lines periodically, you can catch potential issues early and avoid unexpected breakdowns. Consider keeping a record of your inspections and any maintenance work performed to ensure a comprehensive maintenance history.
Remember, proper maintenance and inspection of fuel lines are vital for the overall health and performance of your vehicle. By following these steps, you can help prevent fuel leaks, ensure efficient fuel delivery, and maintain a safe driving experience. Regular attention to this often-overlooked component will contribute to the longevity of your vehicle's fuel system.
Powerful Engine Demands: Choosing the Right Fuel Line for 700 HP
You may want to see also
Frequently asked questions
Fuel lines should be secured tightly to prevent any fuel leaks and ensure optimal performance. The tightness of the fuel lines is crucial to maintain a secure connection and prevent any potential issues.
Yes, fuel lines can be too tight, which may lead to fuel leaks, reduced fuel flow, and potential engine damage. It's important to find the right balance and not overtighten the connections.
Fuel line leaks can occur due to various reasons, including improper installation, damage from sharp edges, corrosion, or simply overtightening. Regular inspection and maintenance can help identify and prevent these leaks.
It is recommended to inspect fuel lines periodically, especially during routine engine maintenance. Look for any signs of damage, corrosion, or leaks. If any issues are found, the fuel lines should be replaced or repaired promptly.
Yes, when tightening fuel lines, it's essential to use the appropriate tools, such as fuel line connectors, crimping tools, or fuel line clamps, to ensure a secure and proper connection without causing damage.