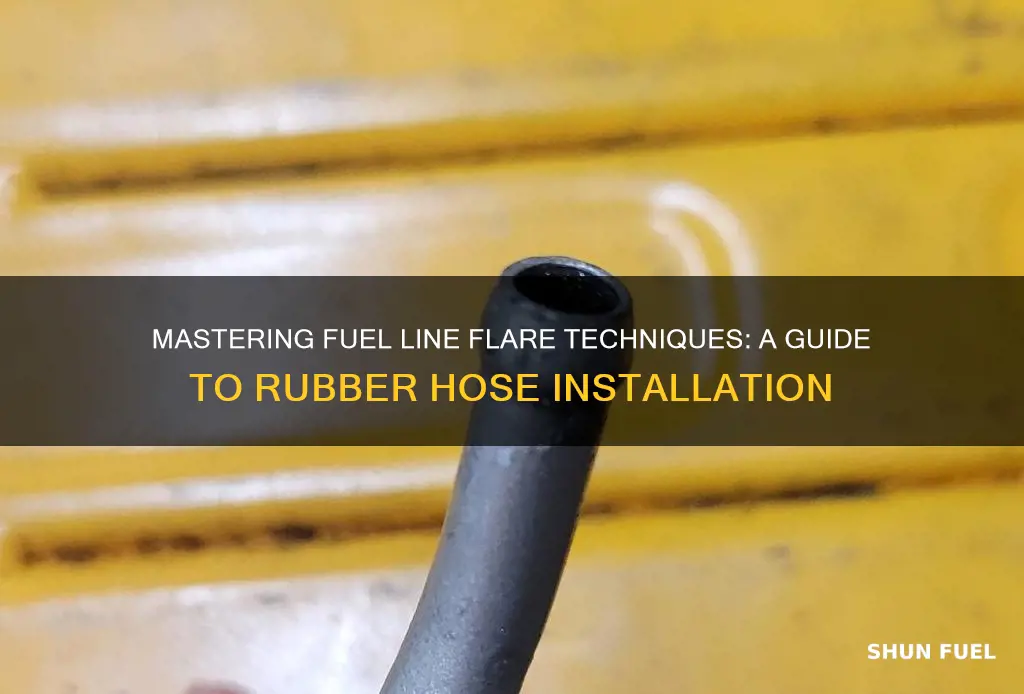
Flaring fuel lines for rubber hoses is a crucial step in ensuring a secure and leak-free connection in automotive or industrial applications. This process involves creating a precise, flared end on the fuel line to fit the rubber hose, which provides a tight seal and prevents fuel leaks. The technique requires careful preparation, the right tools, and a methodical approach to achieve a professional finish. This guide will provide a step-by-step overview of the process, including the necessary equipment, safety precautions, and best practices to ensure a successful flare job.
Characteristics | Values |
---|---|
Material | Rubber |
Application | Fuel Line |
Flaring Technique | Manual or Machine-Assisted |
Tools Required | Flare tool, pipe cutter, sandpaper, fuel line cleaner |
Steps | 1. Cut the fuel line to the desired length. 2. Clean the ends of the fuel line and the flare tool. 3. Insert the fuel line into the flare tool. 4. Apply force to the flare tool to create a flare. 5. Repeat the process for the other end of the fuel line. 6. Test the flare connection for leaks. |
Leak Test | Use a soapy water solution to check for any leaks around the flared connection. |
Safety Precautions | Wear protective gear, ensure proper ventilation, and follow manufacturer guidelines. |
Common Issues | Leaks, improper flare creation, compatibility issues with fuel type. |
Maintenance | Regularly inspect flares for wear and tear, and replace if necessary. |
What You'll Learn
- Preparation: Gather tools and materials, ensuring proper safety gear and a clean workspace
- Hose Inspection: Check for damage, cracks, or leaks, replacing if necessary
- Flaring Tool: Select the appropriate flaring tool for the hose and fuel line size
- Flaring Process: Follow a step-by-step guide, applying pressure and forming a tight seal
- Testing: Verify the flare connection's integrity through pressure testing and visual inspection
Preparation: Gather tools and materials, ensuring proper safety gear and a clean workspace
Before you begin the process of flaring a fuel line to a rubber hose, it's crucial to ensure you have the necessary tools and materials ready. This preparation step is essential to guarantee a smooth and efficient flaring process. Here's a detailed guide on what you need to do:
Gather the Tools and Materials:
- Start by collecting all the required tools and components. You will need a flare tool, which is a specialized device designed for creating flares. Ensure it is compatible with the fuel line and hose sizes you are working with. Additionally, have a variety of flare inserts or sleeves in different sizes to accommodate various fuel line diameters. These inserts are typically made of metal and are used to create the flare.
- Get a high-quality fuel line that matches the specifications of your existing hose. Measure the length required and purchase it accordingly. It's important to have a slightly longer piece to allow for adjustments during the flaring process.
- Don't forget the rubber hose itself, ensuring it is in good condition and free from any damage or cracks.
- Other essential tools include a pair of pliers, a wrench, and a clean cloth or rag. These will be used for holding, tightening, and cleaning during the process.
Safety Gear and Workspace Preparation:
- Safety should always be a top priority. Put on safety goggles to protect your eyes from any potential debris or splashes. Gloves are also recommended to safeguard your hands.
- Choose a well-ventilated workspace, preferably outdoors, to ensure proper ventilation when working with fuel. Ensure the area is clear of any obstacles or tripping hazards.
- Clean your workspace thoroughly. Remove any clutter or debris that might interfere with the flaring process. A clean and organized space will make it easier to work with precision.
- Consider laying down a drop cloth or old newspapers to catch any potential spills or debris, protecting your work area and surrounding surfaces.
By following this preparation step, you'll be well-equipped to tackle the flaring process with confidence, ensuring a successful and safe outcome. Remember, taking the time to gather the right tools and materials, and setting up a safe workspace, is crucial for any successful DIY project.
Understanding the Choke Fuel Line: A Car's Essential Component
You may want to see also
Hose Inspection: Check for damage, cracks, or leaks, replacing if necessary
Hose inspection is a crucial part of vehicle maintenance to ensure the safety and efficiency of your fuel system. Over time, hoses can deteriorate due to various factors, including age, exposure to chemicals, and physical damage. Regular checks can help prevent costly repairs and potential safety hazards. Here's a step-by-step guide to inspecting your fuel hose for any issues:
- Visual Inspection: Start by visually examining the hose for any visible signs of damage. Look for cracks, tears, bulges, or any distortion in its shape. Rubber hoses can degrade due to UV exposure, leading to brittleness and cracking. Inspect the hose for any discoloration or hardening, which may indicate the breakdown of the rubber material. Check for any signs of fuel leakage around the hose connections, as this could be a result of a damaged or worn-out hose.
- Flexibility and Movement: A healthy fuel hose should be flexible and able to move with the engine and vehicle components. Test the hose's flexibility by gently bending it and checking for any stiffness or rigidity. If the hose feels hard or breaks easily, it may be past its prime and could lead to fuel leaks.
- Connection Integrity: Inspect the connections between the hose and the fuel tank, pump, and other components. Ensure that the fittings are secure and tight. Over time, connections can loosen or become corroded, leading to potential fuel leaks. If you notice any corrosion or damage around the connections, it's essential to clean or replace the affected parts.
- Leaks and Moisture: Moisture in the fuel line is a significant concern, as it can lead to corrosion and engine performance issues. Check for any signs of moisture inside the hose, which may be visible as a white or milky appearance. If you find moisture, it could indicate a leak or a compromised seal. In such cases, the hose should be replaced immediately to prevent further damage.
- Replacement and Maintenance: If you identify any damage, cracks, leaks, or signs of deterioration during the inspection, it's best to replace the hose promptly. Regularly scheduled maintenance checks can help identify these issues before they become major problems. Keep a record of the hose's condition and replacement dates to ensure you stay on top of the maintenance.
Remember, a well-maintained fuel hose is essential for optimal engine performance and safety. By following these inspection steps, you can ensure that your vehicle's fuel system remains reliable and efficient.
Unclogging the Jeep Cherokee: A Guide to Removing the Fuel Line
You may want to see also
Flaring Tool: Select the appropriate flaring tool for the hose and fuel line size
When it comes to flaring fuel lines for rubber hoses, selecting the right flaring tool is crucial for a successful and secure connection. The process of flaring involves creating a smooth, rounded bend at the end of the fuel line to ensure a tight seal when connected to another component. Here's a step-by-step guide on choosing the appropriate flaring tool for your specific hose and fuel line size:
Identify the Hose and Fuel Line Size: Before purchasing a flaring tool, you must know the dimensions of your fuel line and hose. Measure the outside diameter of the hose and the fuel line to determine the size of the flare required. Common sizes for fuel lines range from 3/8" to 1-1/2" in diameter, with corresponding flaring tools available for each size.
Choose the Right Tool: Flaring tools come in various types, including hand-held flaring tools, bench-mounted flaring machines, and hydraulic flaring presses. For most automotive applications, a hand-held flaring tool is sufficient. These tools are versatile and can be used for various hose sizes. When selecting a hand-held flaring tool, consider the following:
- Tool Type: Look for tools specifically designed for the size of your fuel line. Manufacturers often provide detailed specifications and compatibility information. For example, a 3/8" fuel line flaring tool will have a specific radius and angle to create the correct flare.
- Material Compatibility: Ensure the flaring tool is compatible with the material of your fuel line and hose. Most rubber hoses and fuel lines are made from materials like natural rubber or synthetic compounds, so choose a tool that can handle these materials without causing damage.
- Ergonomics and Comfort: Consider the tool's design and handle comfort, especially if you plan to use it for extended periods. A well-designed handle with a secure grip can make the flaring process more efficient and less tiring.
Practice and Technique: Flaring is a skill that requires practice to master. Start with smaller hose sizes and work your way up to larger ones. Always follow the manufacturer's instructions for the specific tool you are using. Proper technique involves applying consistent pressure and using the right amount of force to create a clean, rounded flare without distorting the hose.
Remember, using the correct flaring tool for your hose and fuel line size is essential to ensure a reliable and long-lasting connection. It's an investment in the quality of your vehicle's fuel system and overall performance.
Xterra Fuel Line Fitting Location: A Comprehensive Guide
You may want to see also
Flaring Process: Follow a step-by-step guide, applying pressure and forming a tight seal
The flaring process is a crucial technique used to create a secure and leak-proof connection between a fuel line and a rubber hose. It involves shaping the end of the fuel line to match the hose's internal diameter, ensuring a tight seal. Here's a step-by-step guide to mastering this process:
- Preparation: Begin by gathering the necessary tools and materials. You'll need a flaring tool or a specialized flaring machine, which applies pressure to the fuel line. Ensure you have the correct size of fuel line and rubber hose that you want to connect. Clean the fuel line and hose to remove any dirt or debris that might interfere with the sealing process.
- Positioning: Hold the fuel line in one hand and the rubber hose in the other. Position the end of the fuel line so that it is aligned with the opening of the hose. Make sure the fuel line is straight and there are no kinks or bends that could affect the flare.
- Applying Pressure: Using the flaring tool or machine, apply firm and even pressure to the fuel line. The goal is to form a uniform and consistent flare. Start by applying pressure at a 90-degree angle to the fuel line, then gradually move the tool along the length of the line, creating a series of small, controlled bends. This process will cause the material to stretch and form a flare. Take care not to apply excessive force, as it may damage the hose or fuel line.
- Forming the Flare: As you move the tool along the fuel line, you'll notice the material starting to form a rounded shape. Continue applying pressure and moving the tool until the flare reaches the desired length and shape. The flare should be long enough to provide a secure seal but not so long that it becomes cumbersome. A typical flare length is around 1/2 to 3/4 inch.
- Finishing Touches: Once you've formed the flare, inspect it for any sharp edges or uneven areas. Use a file or sandpaper to smooth out any rough spots, ensuring a clean and precise connection. The goal is to create a seamless transition between the fuel line and the hose, allowing for a tight seal.
- Testing the Seal: After flaring, it's essential to test the connection. Connect the flared fuel line to the rubber hose and check for any leaks. If there are no leaks, you've successfully created a secure and reliable seal. If any leaks occur, carefully inspect the flare and make any necessary adjustments to ensure a proper fit.
Mastering the flaring process requires practice and attention to detail. It is a skill that can be honed over time, ensuring professional-quality connections for your fuel lines and rubber hoses. Remember, a well-flared connection not only prevents fuel leaks but also contributes to the overall efficiency and reliability of your fuel system.
Marine Fuel Line: Top Sources for Your Boat
You may want to see also
Testing: Verify the flare connection's integrity through pressure testing and visual inspection
When it comes to ensuring the integrity of flare connections in fuel lines for rubber hoses, testing is an essential step that should not be overlooked. The process begins with a thorough visual inspection, which is a simple yet crucial initial check. This inspection involves carefully examining the flare connections for any visible signs of damage, wear, or improper assembly. Look for any cracks, tears, or deformations in the rubber hose, as well as ensuring that the flare fittings are securely attached and aligned. Any signs of damage or irregularity should be noted and addressed before proceeding with further testing.
Pressure testing is the next critical phase in verifying the flare connections' integrity. This test is designed to simulate real-world conditions and assess the connection's ability to withstand fuel pressure. Here's a step-by-step guide to performing this test: First, ensure that the fuel line is properly connected to the flare fitting and the rubber hose is securely attached. Then, use a calibrated pressure gauge to apply a controlled amount of pressure to the fuel line, gradually increasing it to a level that represents typical operating conditions. Observe the flare connection for any leaks or signs of failure. The pressure should be maintained for a specified duration, usually a few minutes, allowing for a comprehensive evaluation. If no leaks or issues are detected during this test, it indicates that the flare connection is likely secure and functional.
During the pressure test, it's essential to pay attention to any unusual noises or behaviors. If the rubber hose shows signs of distortion or if the flare fitting appears to be leaking, it may indicate a compromised connection. In such cases, further investigation and potential re-flanging or replacement of the affected components might be necessary. Additionally, it is recommended to record the pressure and duration of the test for future reference and to ensure consistency in the testing process.
After the pressure test, a final visual inspection is beneficial to confirm the flare connections' integrity. This inspection should be conducted with a keen eye for detail, checking for any residual signs of damage or wear that might have been missed initially. Look for any changes in the hose's appearance, such as swelling or discoloration, which could indicate internal damage. Also, ensure that all connections remain tight and secure, with no loose fittings that could lead to potential fuel leaks.
By following these testing procedures, you can effectively verify the quality and reliability of flare connections in fuel lines for rubber hoses. This process ensures that the fuel system is safe and functional, providing peace of mind for both DIY enthusiasts and professionals in the automotive or industrial sectors. Remember, proper testing and inspection are fundamental to maintaining the performance and longevity of any fuel-related equipment.
Summer Car Fuel Tank Line: Where It Goes and How to Check
You may want to see also
Frequently asked questions
Flaring a fuel line is a crucial step in ensuring a secure and leak-free connection between the fuel line and the rubber hose. It involves creating a precise, crimped connection that provides a tight seal, preventing fuel leaks and potential hazards.
Flaring can be done using a flaring tool or a hand-held flaring machine. Start by cutting the fuel line to the desired length and inserting the hose into the line. Then, using the flaring tool, apply pressure to the hose and line, creating a series of crimps. Ensure the crimps are uniform and secure, and test the connection for leaks.
Yes, it's important to use the right tools and materials for the job. Ensure the fuel line and hose are clean and free of debris. Apply the correct amount of force when flaring to avoid damaging the materials. Practice and patience are key; take your time to create neat and consistent crimps. Regularly test the connections to ensure they are leak-free before finalizing the installation.