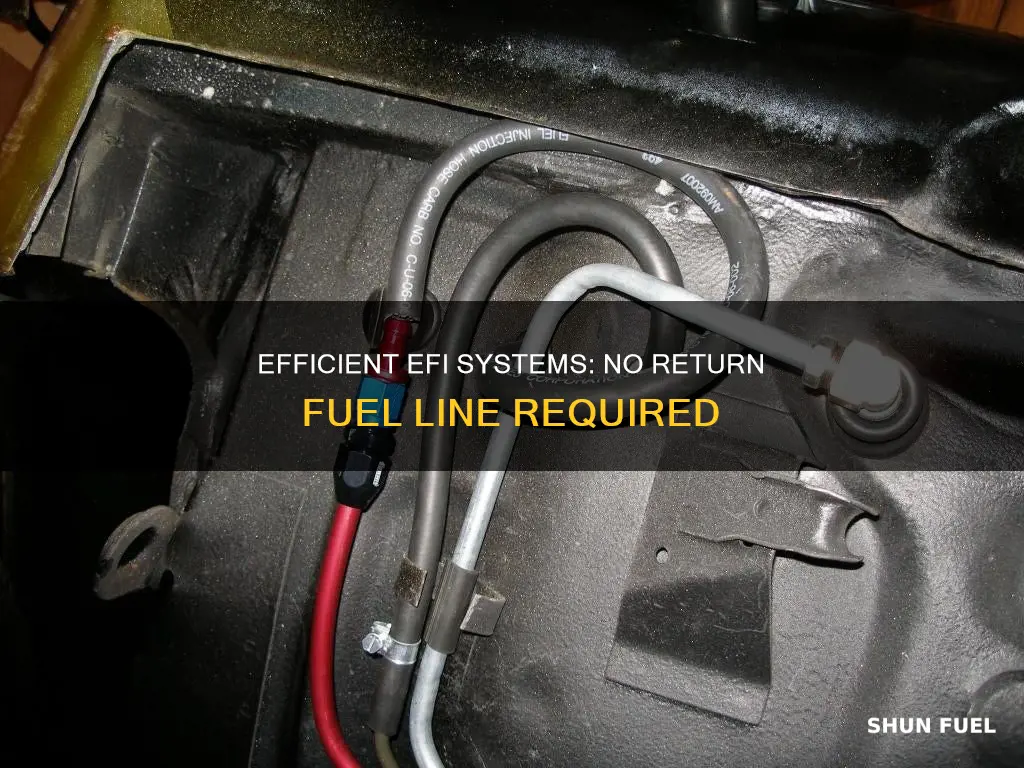
When it comes to EFI (Electronic Fuel Injection) systems, one of the key differences lies in the design of the fuel return line. Some systems, such as those found in many modern vehicles, utilize a return fuel line to recirculate excess fuel back to the fuel tank or tank pressure regulator. However, there is a type of EFI system that stands out for its unique approach: the system that does not require a return fuel line. This design choice is often associated with fuel-injected engines in motorcycles, where the fuel is directly injected into the combustion chamber, eliminating the need for a return line. This feature not only simplifies the engine's design but also contributes to a more efficient fuel delivery process, making it an intriguing aspect of automotive engineering.
What You'll Learn
- Mechanical Injection Systems: These systems use a manual return line, not a fuel return line
- Direct Injection: Fuel is injected directly into the combustion chamber, eliminating the need for a return line
- Common Rail Systems: High-pressure fuel is stored in a common rail, with no return line required
- Port Injection: Fuel is injected into the intake manifold, often without a return line
- Electronic Fuel Injection (EFI) Without Return: Some EFI systems use a closed loop, eliminating the need for a return line
Mechanical Injection Systems: These systems use a manual return line, not a fuel return line
Mechanical injection systems, often referred to as carburetor-like setups, are a classic example of a fuel injection system that does not require a dedicated return fuel line. This is a key distinction that sets it apart from more modern electronic fuel injection (EFI) systems. In mechanical injection, the fuel is delivered to the engine through a series of precise mechanisms, primarily relying on the pressure created by the fuel pump and the engine's vacuum.
The absence of a return fuel line in mechanical injection systems is a result of their design philosophy. Unlike EFI systems, which often use a return line to ensure optimal fuel pressure and flow, mechanical injection systems operate on a simpler principle. They utilize a manual return line, which is essentially a small diameter tube that allows excess fuel to be returned to the fuel tank or reservoir. This manual return line is a crucial component, as it helps maintain the correct fuel level and pressure, ensuring the engine receives the right amount of fuel at all times.
The design of mechanical injection systems is inherently more straightforward. It relies on the engine's natural vacuum and the fuel pump's pressure to deliver fuel. This simplicity means that the system doesn't require the complexity of a return fuel line, which is often used in EFI systems to manage fuel pressure and ensure efficient operation. Instead, the manual return line in mechanical injection systems provides a feedback mechanism, allowing the driver to adjust the fuel mixture manually, often through a carburetor-like setup.
One of the advantages of this design is the reduced complexity and potential for fewer issues related to fuel pressure management. Without the need for a return fuel line, the system is less prone to issues like pressure drops or fuel leaks, which can be common in more complex EFI systems. This simplicity also makes mechanical injection systems more cost-effective and easier to maintain, as they often require fewer sensors and electronic components.
In summary, mechanical injection systems, with their manual return lines, offer a unique approach to fuel delivery. This design choice simplifies the system, reduces potential issues, and provides a cost-effective solution for engines that don't require the advanced fuel management capabilities of modern EFI systems. Understanding these differences is essential for anyone working with or studying various fuel injection technologies.
Understanding Fuel Injector Return Lines: A Comprehensive Guide
You may want to see also
Direct Injection: Fuel is injected directly into the combustion chamber, eliminating the need for a return line
Direct injection is a fuel injection system that has revolutionized engine design and performance. One of its key advantages is the elimination of the need for a return fuel line, which is a significant departure from traditional port fuel injection (PFI) systems. This innovation in engine technology offers a more efficient and effective way of delivering fuel to the engine, resulting in improved performance and reduced emissions.
In a direct injection system, fuel is injected directly into the combustion chamber, which is the space where the air-fuel mixture is ignited to power the engine. This approach differs from PFI, where fuel is injected into the intake manifold, and then the air-fuel mixture is drawn into the combustion chamber. By injecting fuel directly, the system ensures a more precise and controlled fuel-air mixture, leading to better combustion efficiency.
The absence of a return fuel line in direct injection systems is a critical feature. In traditional PFI, a return line is necessary to recirculate excess fuel back to the fuel tank or reservoir. This process can lead to fuel wastage and increased emissions. Direct injection, however, injects fuel directly into the combustion chamber, ensuring that all the fuel is utilized for combustion, thus minimizing fuel consumption and reducing harmful emissions.
The design of direct injection systems also allows for higher fuel pressure, which further enhances the efficiency of the combustion process. Higher fuel pressure enables the system to inject fuel with greater precision, ensuring that the air-fuel mixture is optimally balanced for efficient combustion. This results in improved engine performance, with better throttle response and higher power output.
Furthermore, direct injection systems offer advantages in terms of engine durability and longevity. By eliminating the need for a return fuel line, these systems reduce the risk of fuel-related issues such as fuel pump wear and tear, which can occur due to the constant recirculation of fuel in PFI systems. This makes direct injection engines more reliable and less prone to fuel system-related problems over time.
Submersible Fuel Line Hose: Top Sources for Purchase
You may want to see also
Common Rail Systems: High-pressure fuel is stored in a common rail, with no return line required
The Common Rail system is an advanced fuel injection technology used in modern diesel engines, and it offers several advantages over traditional pump-line-nozzle systems. One of its key features is the absence of a return fuel line, which sets it apart from other Electronic Fuel Injection (EFI) systems. This unique design has significant implications for engine performance and efficiency.
In a Common Rail system, high-pressure fuel is stored in a common rail, a high-pressure reservoir, which is connected to the fuel injectors via individual supply lines. Unlike traditional systems, where fuel returns to a low-pressure reservoir, the Common Rail design eliminates the need for a return fuel line. This simplification is achieved by using a high-pressure pump to supply fuel directly to the injectors, ensuring precise fuel delivery under high pressure.
The absence of a return fuel line in the Common Rail system offers several benefits. Firstly, it reduces the complexity of the fuel system, making it more compact and lightweight. This simplification also contributes to improved fuel efficiency, as there is no energy loss associated with the fuel returning to a reservoir. Additionally, the high-pressure nature of the fuel delivery allows for faster response times, enabling the engine to start quickly and respond promptly to driver inputs.
Another advantage is the enhanced control over fuel injection timing and quantity. The high-pressure fuel in the common rail can be precisely managed, allowing for accurate injection timing and volume. This level of control is crucial for optimizing engine performance, especially during rapid acceleration or when the engine operates under varying loads. The system can quickly adjust fuel delivery to meet the immediate demands of the engine, ensuring smooth and efficient power delivery.
Furthermore, the Common Rail system's design contributes to improved engine emissions. By delivering fuel directly to the injectors, the system minimizes fuel vaporization and ensures complete combustion. This results in reduced exhaust emissions, making it an environmentally friendly choice for diesel engines. The system's ability to maintain high pressure throughout the fuel delivery process also contributes to better fuel atomization, leading to more efficient combustion and reduced smoke and particulate matter.
Powerful Engine Demands: Choosing the Right Fuel Line for 650HP Big Block
You may want to see also
Port Injection: Fuel is injected into the intake manifold, often without a return line
Port injection is a fuel injection system that has been around for many years and is still used in some modern applications. In this system, fuel is directly injected into the intake manifold of the engine, which is located between the air filter and the cylinders. This method of fuel delivery has several advantages and is often associated with not requiring a return fuel line, which is a unique feature compared to other electronic fuel injection (EFI) systems.
The absence of a return fuel line is a significant design choice in port injection systems. Typically, in other EFI systems like multi-point injection or electronic throttle control (ETC), a return line is used to ensure that excess fuel is recycled back to the fuel tank or tank breather, maintaining a precise fuel-air mixture. However, port injection bypasses this need by injecting fuel directly into the intake manifold, allowing for a more straightforward design. This simplicity can make port injection systems easier to manufacture and maintain, especially in high-performance applications where quick fueling adjustments are required.
In port injection, the fuel is injected by a fuel pump, which is often located in the fuel tank or close to it. The fuel is then distributed through a series of fuel rails or individual injectors, each serving one or more cylinders. This direct injection into the intake manifold ensures that the fuel mixes with the incoming air as soon as possible, optimizing the combustion process. The lack of a return line means that the system relies on the engine's natural vacuum to draw the fuel into the cylinders, creating a unique dynamic compared to other EFI systems.
One of the key benefits of port injection is its ability to provide a wide range of fueling options. Since the fuel is injected directly into the intake, it allows for precise control over the fuel-air mixture, enabling tuners and engineers to fine-tune the engine's performance. This level of control is particularly useful in high-performance applications, where optimizing power output and efficiency is crucial. Additionally, port injection can offer better low-end torque and improved throttle response due to the direct fueling strategy.
Despite its advantages, port injection systems have some limitations. They are generally less efficient in terms of fuel consumption compared to more modern EFI systems like direct injection (DI) or gasoline direct injection (GDI). Port injection also may not provide the same level of emissions control as newer technologies, as it lacks the ability to precisely manage the fuel-air mixture in the same way. However, for specific applications, such as classic car restoration or high-performance racing, port injection remains a popular choice due to its simplicity and performance capabilities.
WRX Fuel Line: Discover the Perfect OEM Size
You may want to see also
Electronic Fuel Injection (EFI) Without Return: Some EFI systems use a closed loop, eliminating the need for a return line
The concept of Electronic Fuel Injection (EFI) systems without a return fuel line is an intriguing aspect of modern engine technology. While traditional EFI setups often incorporate a return line to ensure precise fuel management, some innovative designs have evolved to eliminate this component. This approach is particularly notable in certain high-performance and racing applications where weight reduction and streamlined plumbing are advantageous.
In these advanced EFI systems, a closed-loop design is employed, creating a feedback mechanism that continuously monitors and adjusts fuel delivery. This loop typically consists of a fuel pressure sensor, a mass airflow sensor, and an engine control unit (ECU). The ECU receives data from these sensors, calculating the optimal fuel-air mixture and adjusting the fuel pressure accordingly. By doing so, it ensures that the engine receives the precise amount of fuel required for efficient combustion.
The absence of a return fuel line in these systems offers several benefits. Firstly, it simplifies the overall fuel system design, reducing the number of components and potential leak points. This simplicity can contribute to improved reliability and easier maintenance. Additionally, the elimination of the return line can lead to a more compact and lightweight fuel system, which is especially beneficial for high-performance applications where every gram matters.
One of the key advantages of this closed-loop EFI system is its ability to provide highly accurate fuel management. The real-time feedback from the sensors allows for rapid adjustments, ensuring that the engine operates at its optimal performance level. This level of precision is particularly crucial in racing environments, where split-second decisions can make a significant difference in performance.
In summary, the development of EFI systems without return fuel lines represents a significant advancement in engine technology. These systems offer a closed-loop design that provides precise fuel management, eliminating the need for a return line. This innovation not only simplifies the fuel system but also enhances performance and reliability, making it an attractive choice for both high-performance applications and those seeking improved engine efficiency.
Thawing Fuel Lines: Quick Fixes for Frozen Pipes
You may want to see also
Frequently asked questions
EFI stands for Electronic Fuel Injection, which is a system used in modern vehicles to manage the fuel supply to the engine. It ensures precise fuel delivery, optimizing performance, fuel efficiency, and emissions. Understanding the different types of EFI systems can help car owners make informed decisions when modifying or maintaining their vehicles.
The Direct Injection (DI) system is a type of EFI that does not need a return fuel line. In a DI system, fuel is injected directly into the combustion chamber, bypassing the traditional fuel rail and return line. This design simplifies the fuel system and reduces the risk of fuel pressure loss.
The Direct Injection system's design allows for more efficient fuel delivery, as the fuel is injected directly into the engine's cylinders. This results in improved power output, better fuel economy, and reduced emissions. Without the return line, the system maintains optimal fuel pressure, ensuring a consistent and reliable performance.