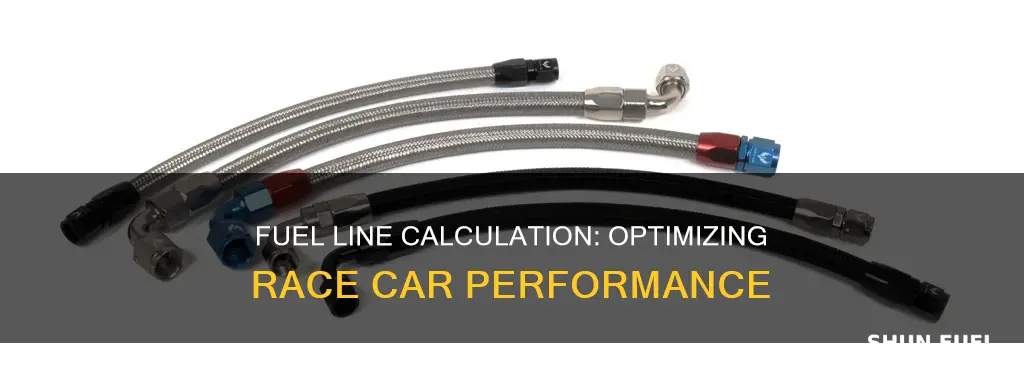
When it comes to racing, every detail matters, and fuel lines are no exception. In this paragraph, we'll explore the crucial aspect of determining the appropriate fuel line length for a race car. From understanding the factors that influence fuel line length to ensuring optimal performance and safety, we'll delve into the considerations that go into selecting the right fuel lines for your high-performance vehicle.
What You'll Learn
- Engine Power: Calculate fuel line requirements based on engine power output
- Flow Rate: Determine the flow rate of fuel needed for optimal performance
- Line Diameter: Choose the appropriate diameter for fuel lines to handle pressure
- Routing: Plan fuel line routing to avoid interference with other components
- Material: Select the right material for fuel lines to withstand high temperatures
Engine Power: Calculate fuel line requirements based on engine power output
When it comes to plumbing a race car, one of the critical aspects is ensuring that the fuel lines are properly sized and installed to handle the power output of the engine. The engine power output directly influences the fuel flow rate required, which in turn determines the diameter and length of the fuel lines. Here's a detailed guide on how to calculate the fuel line requirements based on engine power:
Understanding Engine Power:
Engine power is typically measured in horsepower (hp) or kilowatts (kW). For race cars, the power output can vary significantly, ranging from a few hundred horsepower to over 1000 hp. It's essential to know the exact power rating of your engine to make accurate calculations. This information is usually provided by the manufacturer or can be determined through testing.
Fuel Flow Rate Calculation:
The fuel flow rate is the volume of fuel delivered to the engine per unit of time. It is directly proportional to the engine's power output. A higher-powered engine will require more fuel to sustain its performance. The formula to calculate the fuel flow rate (Q) is:
Q = (Engine Power x Efficiency) / (Fuel Density x Flow Rate Constant)
Where:
- Engine Power is the power output in horsepower or kilowatts.
- Efficiency is the engine's fuel efficiency, often expressed as miles per gallon (mpg) or liters per 100 kilometers (l/100 km).
- Fuel Density is the density of the fuel, typically measured in pounds per cubic foot (lb/ft³) or kilograms per liter (kg/L).
- Flow Rate Constant is a value specific to the fuel system design and can be determined through testing or manufacturer's data.
Determining Fuel Line Diameter:
The fuel flow rate calculation will give you the volume of fuel needed per second. This value can then be used to determine the required fuel line diameter. Fuel lines are typically measured in inches or millimeters. The general rule is that the fuel line diameter should be proportional to the square root of the fuel flow rate. For example, if your calculated fuel flow rate is 100 gallons per minute (gpm), you might need a fuel line with a diameter of approximately 0.5 inches (12.7 mm) to handle this flow efficiently.
Considering Length and Pressure Drop:
The length of the fuel lines and the pressure drop across the lines also play a role in sizing the lines. Longer lines or those with multiple bends may require larger diameters to minimize pressure losses. It's crucial to account for these factors when designing the fuel plumbing system.
Testing and Adjustments:
In practice, fuel line requirements are often determined through testing and adjustments. Race car engineers may use flow benches or vehicle dynos to measure the actual fuel flow rates under different conditions. This data helps fine-tune the fuel line sizes and ensures optimal performance.
Shell Station Fuel Reward Line: Location and Access
You may want to see also
Flow Rate: Determine the flow rate of fuel needed for optimal performance
To ensure optimal performance in a race car, it's crucial to understand the flow rate of fuel, which directly impacts engine power and efficiency. The flow rate refers to the volume of fuel passing through the fuel lines per unit of time. This parameter is critical as it influences the engine's ability to produce power and maintain performance under various conditions.
Calculating the required flow rate involves several factors. Firstly, consider the engine's power output and the desired fuel-air mixture ratio. Modern race cars often utilize advanced fuel injection systems that precisely manage the fuel-air ratio for optimal combustion. The flow rate should be calculated to provide the engine with the exact amount of fuel required for efficient operation. For instance, a high-performance engine might need a higher flow rate to meet its power demands while maintaining a leaner mixture for better fuel economy.
Another critical aspect is the engine's operating conditions. During acceleration, the engine requires more fuel to meet the increased power demands. Similarly, at high speeds or during overtaking maneuvers, the engine's fuel needs surge. The flow rate must be designed to handle these peaks in fuel demand without compromising performance or causing fuel starvation.
To determine the flow rate, engineers often use flow benches or dynamometers, which simulate race car conditions. These tools allow for precise measurement and adjustment of fuel pressure and flow. By testing different fuel line sizes and configurations, engineers can identify the optimal setup that delivers the required flow rate while minimizing pressure drop, ensuring a consistent fuel supply to the engine.
In summary, achieving the right flow rate is essential for maximizing a race car's performance. It involves a detailed understanding of the engine's requirements, operating conditions, and the use of specialized testing equipment. By optimizing the fuel flow, engineers can fine-tune the engine's performance, ensuring it delivers power consistently and efficiently, even under the most demanding racing circumstances.
Fox Fuel Lines: Compatibility with Ford SN95 Models
You may want to see also
Line Diameter: Choose the appropriate diameter for fuel lines to handle pressure
When it comes to plumbing a race car, selecting the right fuel lines is crucial for optimal performance and safety. The diameter of the fuel lines plays a significant role in determining their ability to handle the pressure and flow requirements of the high-performance engine. Here's a detailed guide on how to choose the appropriate line diameter:
Understanding Pressure and Flow: In a race car, fuel lines must withstand high-pressure conditions to ensure efficient fuel delivery to the engine. The pressure can vary depending on the engine's design and operating conditions. Generally, race cars require fuel lines that can handle pressures ranging from 100 to 300 psi (pounds per square inch) or even higher in some cases. Additionally, the fuel lines need to facilitate a rapid and consistent flow of fuel to meet the engine's demanding power requirements.
Line Diameter Selection: The diameter of the fuel line is a critical factor in managing pressure and flow. A larger diameter allows for increased fuel flow rate, which is essential for high-performance applications. As a rule of thumb, the fuel line diameter should be chosen based on the engine's power output and the desired fuel flow rate. For high-performance race cars, a larger diameter is often preferred to ensure that the fuel can reach the engine quickly and efficiently, even under extreme conditions.
Common Diameter Sizes: Fuel lines for race cars typically come in various diameters, ranging from 3/8 inch to 1/2 inch or even larger for extreme high-performance applications. For most race cars, a 3/8-inch or 1/4-inch diameter line is commonly used, providing a good balance between pressure handling and flexibility. However, for engines with higher power outputs, a 1/2-inch or even 5/8-inch diameter line might be necessary to accommodate the increased fuel flow and pressure.
Material Considerations: Along with diameter, the material of the fuel line is also essential. High-quality fuel lines for racing often use materials like stainless steel or braided steel, which offer excellent flexibility, durability, and pressure resistance. These materials can withstand the harsh conditions of racing and ensure a long-lasting performance.
Testing and Simulation: To ensure the chosen fuel line diameter is suitable, it's recommended to conduct pressure testing and flow simulations. This process involves using specialized equipment to measure the line's performance under different pressure and flow conditions. By doing so, you can verify that the selected diameter meets the specific requirements of your race car's engine.
Unveiling the Material Secrets of Metal Fuel Lines
You may want to see also
Routing: Plan fuel line routing to avoid interference with other components
When plumbing a race car, careful planning of fuel line routing is essential to ensure optimal performance and safety. The primary goal is to route the fuel lines in a way that minimizes interference with other critical components, as any disruption can lead to performance issues or even dangerous situations. Here's a detailed guide on how to approach this task:
- Understand the Layout: Begin by thoroughly inspecting the race car's engine bay and interior. Familiarize yourself with the layout of various components, including the engine, transmission, chassis, and any other parts that might be in the vicinity. Identify potential obstacles and areas where the fuel lines could interfere with moving parts or other systems. This initial assessment is crucial for making informed decisions during the routing process.
- Prioritize Safety: Safety should always be the top priority when routing fuel lines. Avoid areas where the lines could come into contact with hot surfaces, sharp edges, or high-pressure components. For instance, keep the fuel lines away from exhaust manifolds, headers, and any parts that generate significant heat during operation. Additionally, ensure that the lines are not routed near moving parts like gears or belts to prevent potential damage or malfunction.
- Optimize Route Selection: Choose the most efficient and interference-free routes for the fuel lines. Typically, the lines should run along the top or sides of the engine bay, utilizing the available space without obstructing other components. Consider the length of the fuel lines and ensure they are not excessively long, as longer lines can lead to fuel pressure issues and reduced performance. Aim for a direct path from the fuel tank to the engine, minimizing the number of bends and turns.
- Use Protective Sleeving: To further protect the fuel lines, consider using protective sleeving or tubing. This adds an extra layer of insulation and safeguards the lines from potential impacts or abrasion. Sleeving can be especially useful in areas where the lines might come into contact with other components or where there is a risk of vibration-induced damage. Ensure that the sleeving material is compatible with the fuel type and does not interfere with the flow.
- Consider Flexibility and Accessibility: While maintaining a secure and interference-free route, also focus on flexibility and accessibility. Allow the fuel lines to bend and adjust to the car's contours without excessive strain. This flexibility ensures that the lines can accommodate the car's movement during acceleration, deceleration, and cornering. Additionally, easily accessible fuel lines facilitate maintenance and inspections, allowing technicians to work on the lines without extensive disassembly.
By carefully planning the fuel line routing, you can ensure that the race car's performance is not compromised and that the fuel system operates efficiently and safely. This attention to detail is a critical aspect of race car plumbing, contributing to the overall success and reliability of the vehicle.
Optimizing Performance: Choosing the Right Fuel Line for Your Waverunner
You may want to see also
Material: Select the right material for fuel lines to withstand high temperatures
When it comes to plumbing a race car, the choice of fuel lines is critical, especially considering the extreme conditions these vehicles operate in. High-performance engines generate immense heat, and the fuel lines must be able to withstand these temperatures without compromising performance or safety. The material of the fuel lines is a key factor in ensuring they can handle the intense heat and pressure associated with racing.
One of the primary considerations is the temperature resistance of the material. Fuel lines should be made from a material that can maintain its structural integrity and flexibility even when exposed to extremely high temperatures. This is crucial to prevent damage to the fuel lines, which could lead to fuel leaks or system failures during the race. Materials like stainless steel, aluminum, and specialized synthetic composites are often used for this purpose. Stainless steel, for instance, offers excellent heat resistance and durability, making it a popular choice for racing applications. It can withstand temperatures up to 1600°F (871°C), which is well beyond what most race cars experience.
Another important aspect is the flexibility of the material. Fuel lines need to be flexible to accommodate the constant vibrations and movements of the vehicle, especially during high-speed cornering and acceleration. Materials like rubber or synthetic compounds with high flexibility and resilience are ideal. These materials can bend and twist without kinking or breaking, ensuring a consistent and reliable fuel supply to the engine.
Additionally, the material should be resistant to fuel degradation. Race car fuels often contain additives that can break down certain materials over time. For example, ethanol-blended fuels can be particularly harsh on certain plastics and rubbers. Therefore, fuel lines should be made from materials that are resistant to fuel degradation, such as high-temperature-resistant synthetic rubbers or fluoropolymers.
In summary, selecting the right material for fuel lines in a race car is essential for performance and safety. The material must be able to withstand high temperatures, maintain flexibility, and resist fuel degradation. By choosing materials like stainless steel, specialized synthetic composites, or high-performance rubbers, race car engineers can ensure that the fuel system operates reliably and efficiently, even under the most demanding conditions. This attention to detail in material selection is a testament to the precision and engineering excellence required in the world of motorsports.
Etec 200 Fuel Line Size: Expert Guide for 2007 Model
You may want to see also
Frequently asked questions
The fuel line size required for your race car depends on several factors, including the engine's power output, the fuel pump's capacity, and the desired fuel flow rate. As a general rule, the fuel line should be able to handle at least 1.5 times the fuel flow rate of your engine. For high-performance engines, a larger fuel line might be necessary to ensure optimal fuel delivery. It's recommended to consult the manufacturer's guidelines or seek advice from experienced mechanics to determine the appropriate size.
The length of the fuel line can vary depending on the car's layout and design. As a starting point, a fuel line length of around 2-4 feet is common for most race cars. However, this can vary based on factors such as the engine's location, the fuel tank's position, and the desired routing. Longer fuel lines might be required for cars with more complex engine bay layouts or those with fuel tanks located far from the engine. It's essential to consider the specific requirements of your vehicle and ensure the fuel line is long enough to reach the engine without excessive bends or strain.
Reusing fuel lines from a previous car is possible, but it should be done with caution and careful consideration. Ensure that the old fuel lines are in good condition and have not been damaged or exposed to extreme temperatures. Check for any signs of wear, cracks, or leaks before reusing them. It's recommended to inspect the fuel lines thoroughly and possibly replace them with new ones to ensure optimal performance and safety. Consulting with a professional mechanic can provide valuable guidance on the suitability of reusing fuel lines in your specific race car setup.