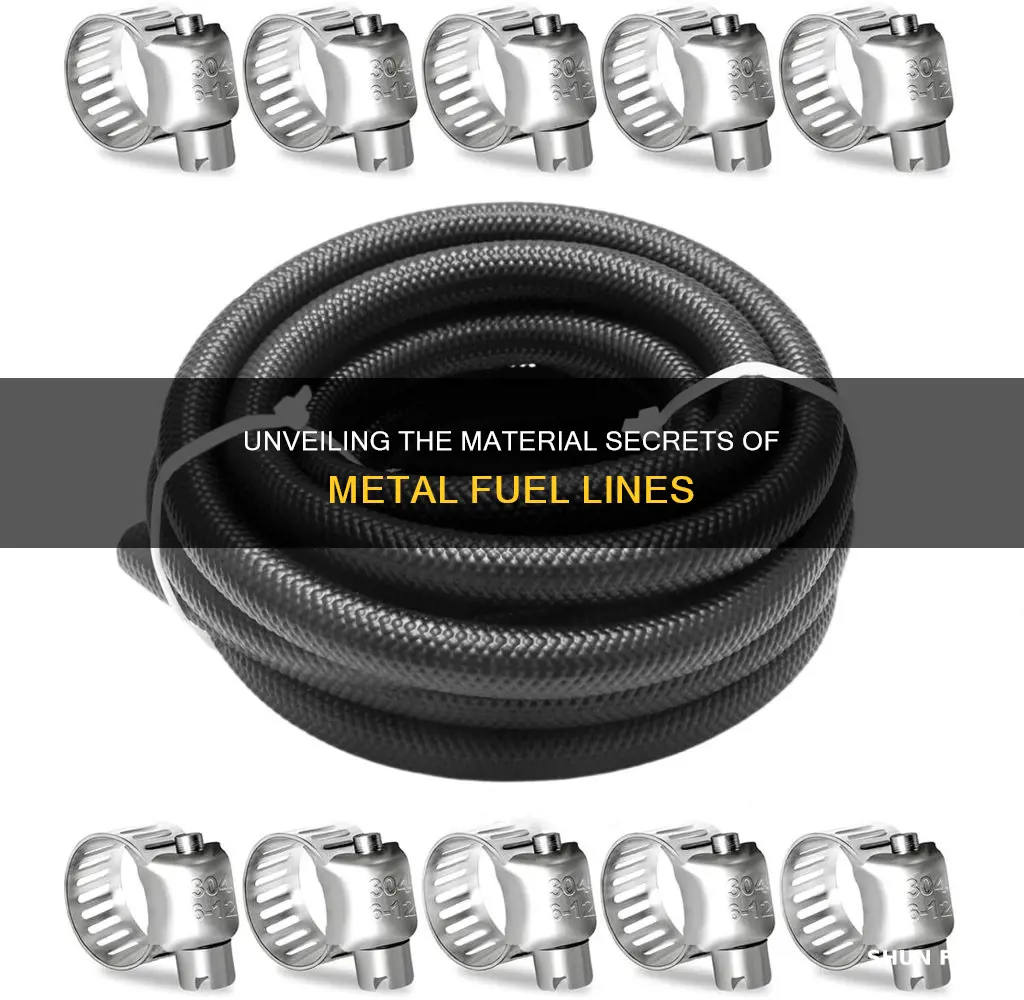
Metal fuel lines are an essential component in the fuel delivery system of vehicles, responsible for transporting fuel from the tank to the engine. These lines are typically constructed from materials that offer durability, strength, and resistance to corrosion, ensuring they can withstand the harsh conditions of the engine bay. The most common materials used for metal fuel lines include stainless steel and aluminum. Stainless steel is highly regarded for its superior corrosion resistance and strength, making it an ideal choice for fuel lines that need to withstand the corrosive effects of fuel and engine heat. Aluminum, on the other hand, is known for its lightweight properties and is often used in applications where weight reduction is crucial. Both materials provide reliable performance and contribute to the overall efficiency and safety of the fuel system.
What You'll Learn
- Material: Metal fuel lines are typically made from steel, aluminum, or copper alloys
- Strength: These materials offer high tensile strength for durability
- Corrosion Resistance: They are designed to resist corrosion from fuel chemicals
- Flexibility: Metal fuel lines are flexible to accommodate engine movement
- Temperature Tolerance: They can withstand extreme temperatures without compromising performance
Material: Metal fuel lines are typically made from steel, aluminum, or copper alloys
Metal fuel lines are an essential component of a vehicle's fuel system, responsible for transporting fuel from the tank to the engine. When it comes to the material used for these lines, engineers and manufacturers have traditionally relied on three primary metals: steel, aluminum, and copper alloys. Each of these materials offers unique advantages and is chosen based on specific requirements and considerations.
Steel: One of the most common materials for metal fuel lines is steel. It is known for its strength, durability, and resistance to corrosion. Steel fuel lines can withstand high pressure and temperature variations, making them ideal for use in automotive applications. The material's inherent strength ensures that the fuel lines can handle the rigors of the road, including vibrations and impacts. Additionally, steel is relatively easy to manufacture and can be produced at a lower cost compared to other metals. This makes it a popular choice for mass-produced vehicles, where cost-effectiveness is a significant factor.
Aluminum: Aluminum is another metal that finds its place in fuel line manufacturing. This material is valued for its lightweight properties, which contribute to improved fuel efficiency in vehicles. Aluminum fuel lines are often used in high-performance or racing applications where weight reduction is crucial. Despite its lightweight nature, aluminum can still provide adequate strength and durability. However, it is generally more susceptible to corrosion compared to steel, so additional protective measures might be required in certain environments.
Copper Alloys: Copper alloys, such as brass and bronze, are less common in fuel line manufacturing but offer unique benefits. Copper is an excellent conductor of heat, which can be advantageous in certain fuel systems. These alloys provide good corrosion resistance and have a relatively low coefficient of expansion, ensuring that the fuel lines maintain their shape and integrity over a wide temperature range. While copper alloys are more expensive than steel and aluminum, their superior corrosion resistance and unique thermal properties make them suitable for specialized applications or in environments with specific requirements.
The choice of material for metal fuel lines depends on various factors, including the vehicle's intended use, environmental conditions, and performance needs. Each metal offers distinct advantages, and manufacturers carefully select the appropriate material to ensure the fuel system's reliability and efficiency. Whether it's the strength of steel, the lightweight nature of aluminum, or the unique properties of copper alloys, these materials play a crucial role in the design and functionality of metal fuel lines.
Aluminum or Steel: Choosing the Right Fuel Line Material
You may want to see also
Strength: These materials offer high tensile strength for durability
Metal fuel lines are an essential component of any vehicle's fuel system, and their construction is a critical aspect of vehicle design. When it comes to strength, metal fuel lines are engineered to withstand the rigors of the road and the demands of fuel transport. The primary materials used for these lines are chosen for their exceptional tensile strength, ensuring that the fuel lines can handle the pressure and stress associated with fuel delivery.
Tensile strength is a measure of a material's ability to resist breaking or permanent deformation when pulled. In the context of fuel lines, this property is crucial because it determines how well the lines can handle the force exerted by the fuel and the engine's operation. High tensile strength materials ensure that the fuel lines remain intact and functional, even under varying temperatures and pressure conditions. This is particularly important in high-performance vehicles or those operating in extreme environments.
One of the key materials utilized in metal fuel lines is steel. Steel alloys, such as stainless steel and carbon steel, are renowned for their exceptional strength and durability. These alloys are carefully selected and treated to enhance their tensile properties, making them ideal for fuel lines. For instance, stainless steel offers excellent resistance to corrosion and oxidation, ensuring that the fuel lines remain strong and reliable over an extended period. Its high tensile strength allows it to withstand the constant flexing and movement associated with vehicle operation.
In addition to steel, aluminum alloys are also employed in certain applications. Aluminum provides a lightweight alternative while still maintaining impressive tensile strength. This is especially beneficial in high-performance vehicles where weight reduction is a priority without compromising structural integrity. The combination of strength and lightweight properties makes aluminum a popular choice for fuel lines in racing or sports cars.
The manufacturing process of these metal fuel lines involves precise engineering and fabrication techniques. The materials are carefully selected and formed to ensure a seamless and robust connection between the fuel lines and other components. This attention to detail is vital to guarantee the overall strength and reliability of the fuel system, contributing to the vehicle's performance and safety.
Unveiling the 1967 Ford LTD's Fuel Line Route
You may want to see also
Corrosion Resistance: They are designed to resist corrosion from fuel chemicals
Metal fuel lines are an essential component in any vehicle's fuel system, responsible for transporting fuel from the tank to the engine. Given the corrosive nature of fuel chemicals, these lines are meticulously designed to withstand the harsh environment. The primary goal is to ensure that the fuel remains uncontaminated and that the metal lines do not degrade over time, which could lead to engine performance issues.
The materials used in manufacturing these lines are carefully selected to offer superior corrosion resistance. One of the most common materials is stainless steel, known for its exceptional ability to resist corrosion. This metal is particularly effective because it forms a protective oxide layer on its surface, which prevents further corrosion. The oxide layer acts as a barrier, safeguarding the underlying metal from the corrosive effects of fuel chemicals.
In addition to stainless steel, some manufacturers also use brass or copper alloys. These materials are chosen for their inherent corrosion resistance properties. Brass, for instance, is a combination of copper and zinc, which creates a durable and non-reactive surface. Copper alloys, on the other hand, offer excellent resistance to corrosion, especially in the presence of fuel chemicals. The use of these alloys ensures that the fuel lines remain intact and functional over the long term.
The design of the fuel lines also plays a crucial role in their corrosion resistance. Manufacturers often incorporate features such as protective coatings or specialized coatings to enhance their ability to resist corrosion. These coatings can be applied to the inner surface of the lines to create a barrier between the metal and the fuel, further preventing any chemical reactions that could lead to degradation.
Furthermore, the manufacturing process itself is optimized to ensure the highest level of corrosion resistance. This includes precise control over the material's purity and the application of specialized treatments to enhance its protective properties. By combining the right materials with innovative design and manufacturing techniques, metal fuel lines are engineered to provide reliable and long-lasting performance, even in the challenging conditions of a vehicle's fuel system.
Nova Fuel Tank Lines: Unlocking Engine Power and Efficiency
You may want to see also
Flexibility: Metal fuel lines are flexible to accommodate engine movement
Metal fuel lines are an essential component in any vehicle's fuel system, responsible for transporting fuel from the tank to the engine. One of the critical aspects of these lines is their flexibility, which is often overlooked. This flexibility is crucial in accommodating the various movements and vibrations experienced by the engine during operation.
The flexibility of metal fuel lines is achieved through the use of specific materials and design techniques. These lines are typically made from high-quality metals such as stainless steel or aluminum, which offer excellent durability and resistance to corrosion. The metal is carefully selected to ensure it can withstand the harsh conditions inside the engine bay, including extreme temperatures and mechanical stress.
The manufacturing process involves forming the metal into a tubular structure, which is then carefully bent and manipulated to create the desired flexibility. This process requires precision and expertise to ensure the lines can move with the engine without compromising their structural integrity. The flexibility is further enhanced by the addition of protective coatings or sleeves, which help to reduce wear and tear from friction against other engine components.
In addition to the material and manufacturing considerations, the design of the fuel lines also plays a significant role in their flexibility. The lines are often designed with a series of small bends and kinks, allowing them to move freely without kinking or becoming rigid. This design feature ensures that the fuel lines can adapt to the engine's movements, even during sharp turns or sudden accelerations.
The flexibility of metal fuel lines is a vital aspect of their performance and longevity. By accommodating engine movement, these lines help to maintain a consistent fuel supply, ensuring optimal engine operation. This flexibility also contributes to the overall reliability of the vehicle, as it reduces the risk of fuel leaks or damage to the fuel system caused by excessive movement or vibration.
Unleash the Power: Breaking Fuel Lines: A Quarry Decision
You may want to see also
Temperature Tolerance: They can withstand extreme temperatures without compromising performance
Metal fuel lines are an essential component in the fuel delivery system of many vehicles, and their design and material composition are crucial for optimal performance and safety. When it comes to temperature tolerance, these lines are engineered to excel, ensuring that fuel delivery remains efficient and reliable even under extreme conditions.
The ability to withstand extreme temperatures is a critical aspect of metal fuel lines' performance. These lines are typically made from materials that offer excellent heat resistance, such as stainless steel or aluminum alloys. Stainless steel, for instance, is renowned for its exceptional temperature tolerance, capable of withstanding temperatures ranging from extremely low sub-zero values to high-heat environments. This material's inherent corrosion resistance and high-temperature stability make it ideal for fuel lines, ensuring that the fuel remains uncontaminated and that the system operates efficiently.
In high-performance vehicles or those operating in challenging environments, metal fuel lines often incorporate specialized coatings or treatments to enhance their temperature resistance further. For example, some lines may be lined with a protective layer of Teflon or a similar material, which reduces friction and heat absorption, ensuring that the fuel lines maintain their structural integrity and performance even when exposed to intense heat.
The temperature tolerance of metal fuel lines is not limited to high-temperature environments alone. These lines are also designed to handle extremely low temperatures, which is particularly important in cold climates or for vehicles used in winter conditions. The materials used, such as low-carbon steel or specific alloys, provide excellent cold weather performance, preventing brittleness and ensuring flexibility even at sub-zero temperatures. This flexibility is crucial to maintaining a consistent fuel flow and preventing damage to the fuel system.
Furthermore, the manufacturing process plays a significant role in achieving optimal temperature tolerance. Advanced techniques, such as precision welding and heat-treating processes, are employed to ensure that the metal fuel lines are robust and can withstand the extreme conditions they will encounter. These processes enhance the material's strength and durability, allowing the fuel lines to perform reliably over a wide temperature range without any degradation in quality.
Unveiling the Mystery: What Material Powers Your Lawn Mower's Fuel Lines?
You may want to see also
Frequently asked questions
Metal fuel lines, typically made of steel or aluminum, are engineered to withstand high-pressure environments and provide a robust fuel delivery system. These materials offer excellent strength and durability, ensuring the lines can handle the demands of fuel transportation in automotive applications.
Metal fuel lines are preferred due to their superior resistance to corrosion and extreme temperatures. Unlike some other materials, metals do not degrade over time when exposed to fuel chemicals, ensuring a longer-lasting and more reliable fuel supply. This makes them ideal for high-performance vehicles and those operating in harsh conditions.
Yes, metal fuel lines are versatile and can be used across various vehicle types, from motorcycles to heavy-duty trucks. Their compatibility with different fuel systems and ability to handle varying temperatures make them a universal choice for fuel delivery, ensuring efficient and safe operation.