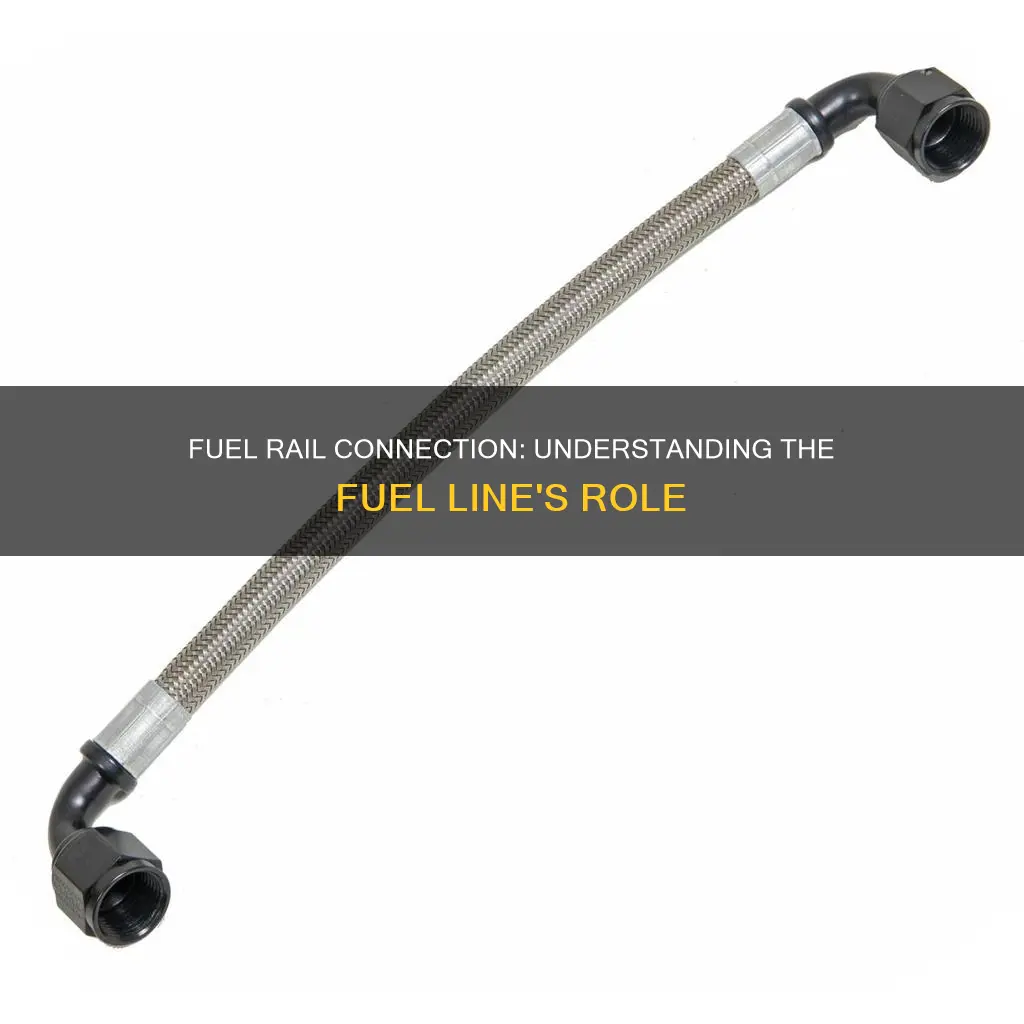
The fuel line plays a crucial role in the fuel system of an engine, connecting the fuel tank to the fuel rail. Understanding the process of how the fuel line connects to the fuel rail is essential for maintaining a vehicle's performance and reliability. This paragraph will explore the various methods and considerations involved in establishing a secure and efficient connection between the fuel line and the fuel rail, ensuring optimal fuel delivery to the engine.
Characteristics | Values |
---|---|
Connection Type | Typically a quick-connect fitting or a high-pressure fuel line with a clamp or ferrule |
Material | High-pressure fuel lines are usually made of steel or stainless steel, while quick-connect fittings may use rubber or plastic |
Pressure Rating | Fuel lines are designed to handle the pressure of the fuel system, often rated for high-pressure applications |
Length | The length of the fuel line can vary depending on the vehicle's design and engine location |
Compatibility | Ensure the fuel line is compatible with the fuel type (gasoline, diesel, etc.) and the vehicle's fuel system |
Flexibility | Fuel lines need to be flexible to accommodate engine movement and vibrations |
Seals | Quick-connect fittings often use O-rings or seals to ensure a tight connection |
Routing | Fuel lines are routed to avoid sharp bends and potential damage, often following the engine's contours |
Maintenance | Regular inspection and replacement of fuel lines are recommended to prevent leaks and ensure optimal performance |
What You'll Learn
- Fuel Rail Design: The fuel rail is designed to hold the fuel at a consistent pressure
- Fuel Pump: The fuel pump is responsible for delivering fuel from the tank to the rail
- Fuel Injectors: Fuel injectors are connected to the fuel rail and spray fuel into the engine
- Fuel Pressure Regulator: This component regulates the pressure of fuel in the system
- Fuel Line Material: The material of the fuel line must be compatible with the fuel type
Fuel Rail Design: The fuel rail is designed to hold the fuel at a consistent pressure
The fuel rail is a critical component in the fuel system of an internal combustion engine, and its design is crucial for efficient and reliable engine operation. One of its primary functions is to maintain a consistent pressure of fuel, ensuring that the engine receives the correct amount of fuel at the right time. This is achieved through a carefully designed structure and connection system.
The fuel rail is typically made of a durable material, such as aluminum or steel, and is engineered to withstand the high pressures involved in fuel delivery. It is designed with a series of fuel passages or channels that run from the fuel pump to the individual fuel injectors. These passages are precisely sized and spaced to allow for an even distribution of fuel pressure across the rail. The key to this design is to ensure that the fuel is not concentrated in one area, which could lead to uneven atomization and potential engine performance issues.
To achieve consistent pressure, the fuel rail incorporates a series of pressure-regulating mechanisms. One common design feature is the use of a pressure-relief valve or a pressure-reducing orifice. These components are strategically placed along the fuel rail to maintain a steady pressure as the fuel flows through the system. The valve or orifice opens or closes based on the pressure, ensuring that the fuel pressure at the injectors remains within the optimal range.
Additionally, the fuel rail's design often includes a fuel filter, which is positioned to filter contaminants from the fuel as it enters the rail. This filter helps prevent any debris or impurities from reaching the injectors, ensuring clean fuel delivery and maintaining engine performance. The filter is typically designed to be easily accessible for replacement, allowing for regular maintenance to keep the fuel system in optimal condition.
In summary, the fuel rail's design is a critical aspect of engine performance, focusing on maintaining consistent fuel pressure. This is achieved through precise engineering, including the use of pressure-regulating components and filters, to ensure that the engine receives the correct amount of fuel at the right pressure, resulting in efficient and reliable operation. Understanding these design principles is essential for anyone working on fuel systems, as it ensures the proper functioning of the entire engine.
Thawing Frozen Fuel Lines: A Guide to Unfreezing
You may want to see also
Fuel Pump: The fuel pump is responsible for delivering fuel from the tank to the rail
The fuel pump plays a critical role in the fuel delivery system of a vehicle, ensuring that the engine receives the necessary fuel for operation. Its primary function is to pump fuel from the fuel tank to the fuel rail, which is a crucial component in the fuel injection process. This process is essential for modern engines, as it ensures precise fuel metering and timing, leading to efficient combustion and optimal performance.
When the engine is started, the fuel pump is activated, and it begins to draw fuel from the tank. The pump is typically located near the tank or integrated into it, and it operates using an electric motor or a mechanical linkage. As the pump activates, it creates a vacuum or pressure, depending on the design, which draws fuel through the fuel lines. These lines are carefully routed to ensure a continuous and efficient flow of fuel.
The fuel lines are designed with specific diameters and materials to handle the pressure and volume of fuel being pumped. They are connected to the fuel pump using fittings or quick-connect couplings, ensuring a secure and leak-free connection. From the pump, the fuel travels through the lines to the fuel rail, which is often located near the engine. The rail is a metal or plastic structure with multiple outlets, each connected to an individual cylinder's fuel injectors.
At the fuel rail, the pressure is typically reduced to match the engine's requirements. This is achieved through a pressure-reducing valve or a series of small orifices in the rail itself. Once the fuel reaches the rail, it is distributed to the injectors, which precisely meter and inject the fuel into the engine's cylinders during the combustion process. This system ensures that the engine receives the correct amount of fuel at the right time, optimizing performance and fuel efficiency.
In summary, the fuel pump is a vital component in the fuel delivery process, transferring fuel from the tank to the fuel rail. Its operation ensures that the engine receives the required amount of fuel for efficient combustion. Understanding the role of the fuel pump and its connection to the fuel rail is essential for maintaining and troubleshooting fuel-related issues in vehicles.
Mastering the Art of Rubber Fuel Line Removal: A Comprehensive Guide
You may want to see also
Fuel Injectors: Fuel injectors are connected to the fuel rail and spray fuel into the engine
Fuel injectors play a crucial role in modern engine systems, ensuring efficient and precise fuel delivery to the engine's combustion chambers. These injectors are strategically connected to the fuel rail, a component that acts as a reservoir for the fuel-air mixture. The connection between the fuel injectors and the fuel rail is a critical aspect of engine performance and reliability.
The fuel rail is typically located near the engine's cylinder head, providing easy access to the injectors. It is designed to hold a specific amount of fuel under pressure, ensuring a steady supply for the engine's operation. Each fuel injector is connected to the fuel rail via a dedicated fuel line, which is carefully routed to maintain optimal pressure and minimize any potential leaks. These fuel lines are usually made of durable materials like steel or aluminum to withstand the high pressure and temperature inside the engine.
When the engine is running, the fuel pump sends pressurized fuel through the fuel rail to the injectors. The injectors are precisely calibrated to spray the fuel in a specific pattern and amount, ensuring complete combustion. This process is highly efficient as it allows for better control over the fuel-air mixture, resulting in improved engine performance, reduced emissions, and better fuel economy.
The connection between the fuel injectors and the fuel rail is designed with precision to accommodate various engine sizes and configurations. Engineers carefully consider factors such as engine displacement, power output, and fuel requirements when designing these connections. This ensures that the fuel injectors receive the correct amount of fuel at the right pressure, optimizing engine performance across different operating conditions.
In summary, the fuel injectors' connection to the fuel rail is a vital component of the engine's fuel delivery system. This setup enables precise fuel injection, contributing to efficient combustion and overall engine performance. Understanding this connection is essential for mechanics and engineers working on fuel injection systems, ensuring proper maintenance and troubleshooting.
Fuel Pressure Regulator: Essential Return Line or Redundant?
You may want to see also
Fuel Pressure Regulator: This component regulates the pressure of fuel in the system
The fuel pressure regulator is a critical component in a vehicle's fuel system, ensuring that the fuel delivered to the engine is at the precise pressure required for optimal performance and efficiency. This small but essential part is often overlooked, yet it plays a vital role in maintaining the health and longevity of the engine.
Its primary function is to maintain a consistent and controlled pressure within the fuel system. When the engine is running, the regulator monitors the fuel pressure and makes adjustments to ensure it stays within a specific range. This is crucial because fuel pressure that is too high can lead to inefficient combustion, while pressure that is too low can result in poor engine performance and potential damage to the fuel injectors.
The regulator achieves this by using a spring-loaded mechanism that opens or closes depending on the pressure it senses. When the pressure is below the desired level, the regulator allows more fuel to enter the system, increasing the pressure. Conversely, if the pressure exceeds the set point, the regulator restricts the fuel flow, reducing the pressure back to the optimal level. This process happens almost instantaneously, ensuring that the engine always receives the correct amount of fuel.
In modern vehicles, the fuel pressure regulator is often integrated into the fuel pump module or the fuel rail itself. This design choice simplifies the system and ensures that the fuel pressure is regulated as close to the engine as possible, minimizing pressure losses in the fuel lines. The regulator's precision is key to the overall performance and reliability of the vehicle, especially in high-performance engines where fuel pressure must be tightly controlled.
Regular maintenance and inspection of the fuel pressure regulator are essential to ensure its longevity and proper functioning. Over time, the regulator can become contaminated or worn, leading to inconsistent fuel pressure. This may result in noticeable performance issues, such as reduced power, poor fuel economy, or even engine misfires. Therefore, keeping this component in good condition is vital for the overall health of the vehicle's engine.
Mastering the Art of Car Fuel Line Splices: A Step-by-Step Guide
You may want to see also
Fuel Line Material: The material of the fuel line must be compatible with the fuel type
The choice of material for the fuel line is a critical aspect of ensuring optimal performance and longevity in a fuel system. When it comes to compatibility, the fuel line material must be carefully selected to match the type of fuel being used. Different fuels have varying chemical compositions and properties, and using the wrong material can lead to issues such as fuel degradation, leaks, and even system failure.
For example, gasoline-powered engines typically use fuel lines made from materials like rubber or synthetic compounds that can withstand the volatility of gasoline. These materials are designed to resist the corrosive effects of gasoline over time, ensuring a reliable fuel supply to the engine. On the other hand, diesel fuel requires a different approach due to its higher boiling point and different chemical properties. Fuel lines for diesel engines often use materials like steel or specialized rubber compounds that can handle the higher pressure and temperature requirements.
In the case of ethanol-blended fuels, such as E85, the fuel line material becomes even more crucial. Ethanol is more corrosive to certain materials, so fuel lines made from compatible materials like high-density polyethylene (HDPE) or specific rubber compounds are recommended to prevent damage to the fuel system. The compatibility ensures that the fuel line can withstand the unique challenges posed by ethanol-based fuels.
Additionally, the material selection should consider the operating conditions and temperature variations the fuel line will encounter. Some materials may become brittle or degrade at high temperatures, while others might not provide sufficient flexibility at low temperatures. Therefore, it is essential to choose a material that can handle the specific environmental conditions of the fuel system.
In summary, the material of the fuel line is a critical factor in maintaining a healthy and efficient fuel system. It must be compatible with the fuel type to prevent degradation, leaks, and other issues. Engineers and mechanics should always refer to the vehicle's specifications and consult experts to select the appropriate fuel line material, ensuring the system's reliability and performance.
Can Regular Fuel Lines Handle Diesel Fuel?
You may want to see also
Frequently asked questions
A fuel rail is a component in an internal combustion engine's fuel injection system. It serves as a central point where the fuel is delivered and distributed to multiple fuel injectors. The fuel rail is designed to store high-pressure fuel, ensuring a consistent and precise fuel supply to the engine's cylinders.
The fuel line is typically connected to the fuel rail via a quick-connect fitting or a specialized coupling. This connection allows for the transfer of fuel from the fuel pump or tank to the fuel rail. The design of the connection ensures a secure and leak-free attachment, maintaining the required pressure and flow rate.
Yes, there are various connection methods, including threaded, clamp-style, and quick-connect fittings. Threaded connections involve screwing the fuel line into the rail, providing a tight seal. Clamp-style connections use a clamp to secure the line, while quick-connect fittings offer a convenient and efficient way to attach and detach the fuel line.
Fuel rails and lines are often made of durable materials like aluminum or steel to withstand high pressure and temperature. The connections may also utilize materials such as brass, stainless steel, or specialized rubber compounds to ensure compatibility and prevent fuel leakage.
Yes, a poorly connected or damaged fuel line can lead to engine problems. Leaks or blockages in the connection can result in inadequate fuel supply, causing the engine to run poorly or even stall. It is essential to ensure proper installation and regular maintenance to prevent such issues.