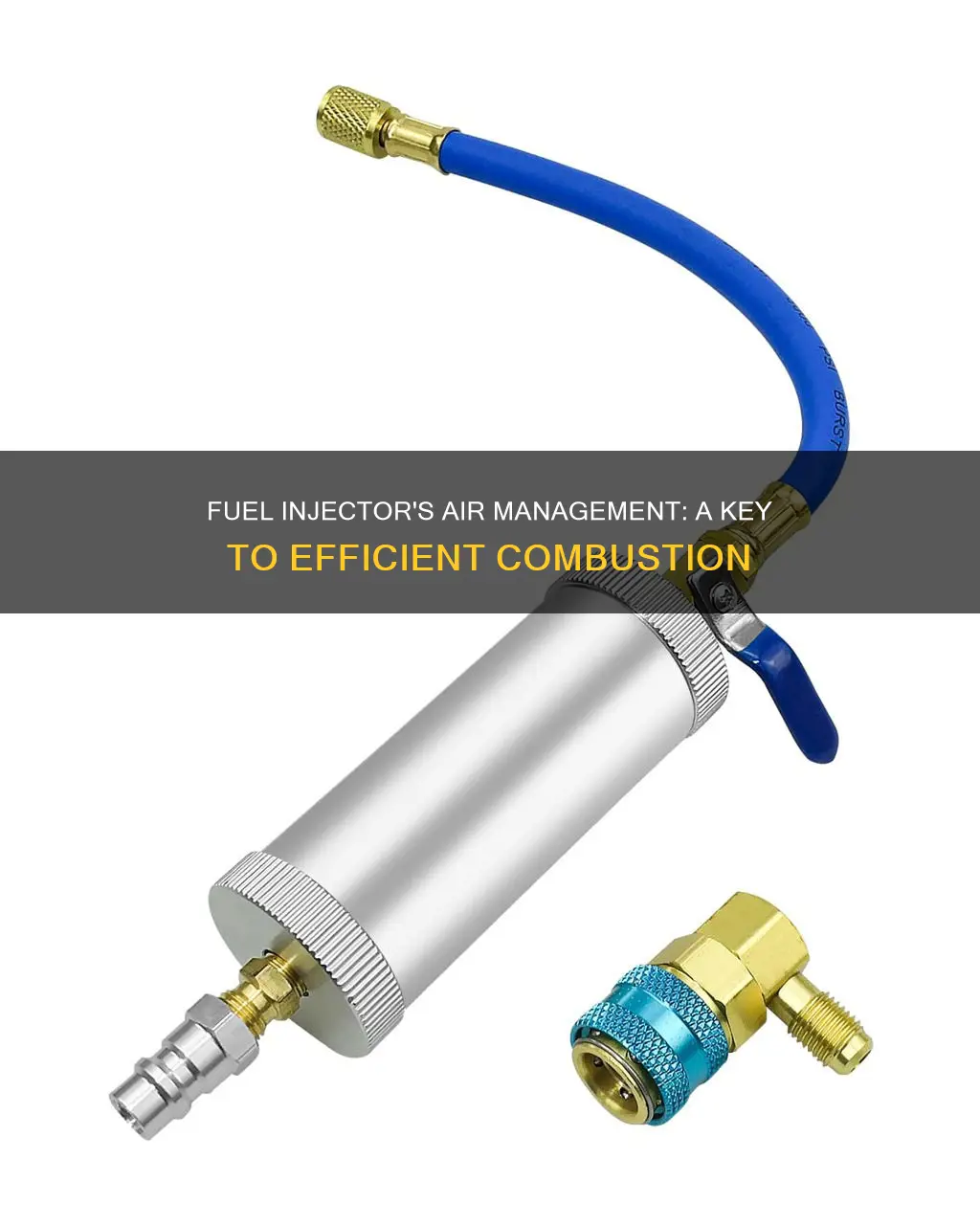
Fuel injectors play a crucial role in modern vehicle engines by precisely managing the fuel-air mixture. They ensure optimal combustion by introducing fuel into the engine's intake system, where it mixes with air. This process requires careful consideration of the air-fuel ratio to achieve efficient performance and minimize emissions. The fuel injector's design and operation are tailored to handle the complexities of air in the fuel line, ensuring a balanced mixture that meets the engine's requirements. Understanding how fuel injectors manage air in the fuel line is essential for optimizing engine performance and maintaining vehicle efficiency.
What You'll Learn
- Air-Fuel Ratio Control: Fuel injectors precisely manage the air-fuel mixture for optimal combustion
- Air Pressure Regulation: Injectors ensure consistent air pressure to maintain fuel atomization
- Air Intake System: The design of the air intake influences fuel efficiency and performance
- Air Flow Meter: This sensor measures air intake to adjust fuel injection accordingly
- Air-Fuel Balance: Injectors optimize the air-fuel ratio for efficient combustion and reduced emissions
Air-Fuel Ratio Control: Fuel injectors precisely manage the air-fuel mixture for optimal combustion
Fuel injectors play a crucial role in modern vehicle engines by precisely managing the air-fuel mixture, ensuring optimal combustion and efficient performance. This process is known as air-fuel ratio control, and it involves a complex interplay of sensors, actuators, and electronic controls. The primary goal is to maintain the ideal air-fuel ratio, which is typically around 14.7:1 (air to fuel by weight) for gasoline engines. This ratio is essential for complete combustion, maximizing power output, and minimizing harmful emissions.
At the heart of this system are the fuel injectors, which are responsible for delivering the precise amount of fuel required for each cylinder. These injectors are highly accurate and can adjust the fuel flow rate based on real-time engine conditions. When the engine is idling or operating at high speeds, the fuel injectors make rapid adjustments to maintain the optimal air-fuel ratio. This dynamic control is made possible by advanced electronic controls that continuously monitor various engine parameters.
The air-fuel ratio control system employs a network of sensors to gather critical data. These include mass airflow (MAF) sensors, which measure the amount of air entering the engine, and oxygen (O2) sensors, which monitor the oxygen content in the exhaust stream. By analyzing these sensor inputs, the engine control unit (ECU) can make informed decisions about fuel injection timing and quantity. For instance, if the O2 sensor detects a lean mixture (too much air and not enough fuel), the ECU will instruct the fuel injectors to deliver more fuel to achieve the desired ratio.
In addition to the sensors, the fuel injectors themselves are designed to handle the dynamic nature of air-fuel ratio control. They use a solenoid-operated valve to regulate fuel pressure and flow. When the ECU commands a change in fuel delivery, the solenoid activates, allowing the precise amount of fuel to be injected into the intake manifold or directly into the cylinders. This process is rapid and responsive, ensuring that the engine always operates at the optimal air-fuel ratio.
The benefits of precise air-fuel ratio control are significant. It results in improved engine performance, with better throttle response and power output. Additionally, it contributes to reduced emissions, as the optimal ratio promotes complete combustion, minimizing the production of harmful pollutants. Modern fuel injection systems, combined with sophisticated electronic controls, have revolutionized engine technology, offering a seamless driving experience while adhering to stringent environmental regulations.
Replacing the Fuel Line: A Step-by-Step Guide for the FS55R
You may want to see also
Air Pressure Regulation: Injectors ensure consistent air pressure to maintain fuel atomization
The fuel injection system plays a crucial role in modern engines by precisely managing the fuel-air mixture, and one of its key functions is air pressure regulation. This process ensures that the engine receives the optimal amount of air, which is essential for efficient combustion. Air pressure regulation is vital because it directly impacts the atomization of fuel, the process of breaking down fuel into tiny droplets. Proper atomization allows for better mixing of fuel and air, resulting in more complete combustion and improved engine performance.
Fuel injectors are designed to maintain a consistent air pressure within the fuel line, which is critical for several reasons. Firstly, it ensures that the fuel is atomized effectively. When the air pressure is regulated, the fuel injectors can spray the fuel as fine droplets, creating a mist-like consistency. This fine atomization is necessary for efficient fuel-air mixture formation, as it increases the surface area of the fuel, allowing it to mix more readily with the incoming air.
In engines, the air-fuel mixture's quality is directly related to the engine's performance and efficiency. With consistent air pressure, the fuel injectors can deliver the correct amount of fuel at the right time, ensuring that the engine operates optimally. This precision in fuel delivery contributes to better power output, improved fuel economy, and reduced emissions.
The air pressure regulation process involves several components working together. The fuel injectors are connected to a high-pressure fuel pump, which supplies fuel at a precise pressure. This pressure is carefully controlled by an electronic control unit (ECU), which monitors engine conditions and adjusts the fuel pressure accordingly. The ECU ensures that the air pressure in the fuel line remains within a specific range, optimizing the fuel atomization process.
Additionally, some fuel injection systems incorporate an air pressure sensor to provide real-time feedback. This sensor measures the air pressure and sends data to the ECU, allowing for immediate adjustments to maintain the desired pressure. By continuously monitoring and regulating air pressure, the fuel injectors can adapt to various driving conditions, ensuring consistent performance regardless of external factors.
Datsun 1600 Roadster Fuel Line Sizing Guide: Carburetor Edition
You may want to see also
Air Intake System: The design of the air intake influences fuel efficiency and performance
The air intake system plays a crucial role in optimizing the performance and efficiency of an engine, especially when it comes to fuel injectors. When designing an air intake system, engineers aim to ensure that the engine receives the right amount of air at the correct pressure and temperature to facilitate efficient combustion. This is particularly important as the fuel injector's primary function is to spray fuel into the engine's cylinders, and the quality of the air-fuel mixture directly impacts the engine's performance.
One key aspect of the air intake system is its ability to manage air flow. The design should allow for a smooth and controlled airflow into the engine. This involves the use of various components such as air filters, which are essential to remove contaminants and ensure clean air intake. A well-designed air filter can significantly improve engine performance by providing a consistent and high-quality air supply. Additionally, the intake system may include a throttle body or a throttle plate, which regulates the airflow by adjusting the size of the opening, thus controlling the amount of air entering the engine.
The design of the air intake also considers the engine's requirements for optimal performance. Engineers must take into account the engine's displacement, power output, and fuel injection system type. For instance, high-performance engines often require a more aggressive air intake design to provide the necessary air volume and pressure for efficient combustion. This might involve using larger air filters, intake pipes with increased cross-sectional areas, or even superchargers or turbochargers to boost the air pressure and density.
Furthermore, the air intake system's design can impact fuel efficiency. A well-designed intake system minimizes air resistance and ensures a steady airflow, allowing the engine to operate at its most efficient state. This can lead to improved fuel economy and reduced emissions. Engineers often employ techniques like using smooth, straight intake pipes, optimizing the shape and size of the air filter, and implementing advanced materials to reduce weight and improve airflow.
In summary, the air intake system's design is a critical factor in the overall performance and efficiency of an engine, especially when working in conjunction with fuel injectors. By carefully considering the airflow, using appropriate components, and tailoring the design to the engine's specifications, engineers can ensure that the engine receives the ideal air-fuel mixture, resulting in improved performance, fuel efficiency, and a more responsive driving experience.
Oil Line to Fuel Pump: A DIY Guide
You may want to see also
Air Flow Meter: This sensor measures air intake to adjust fuel injection accordingly
The air flow meter is a crucial component in modern fuel injection systems, playing a vital role in optimizing engine performance and fuel efficiency. This sensor is designed to measure the volume of air entering the engine, which is a critical factor in the fuel injection process. By accurately determining the amount of air, the engine can precisely calculate the required fuel to achieve optimal combustion.
When the engine is running, the air flow meter constantly monitors the air intake. It does this by measuring the pressure difference between the intake manifold and the atmosphere. This pressure difference is directly related to the volume of air flowing into the engine. The sensor then converts this pressure data into a measurable signal, typically an electrical voltage, which represents the air intake.
The primary function of the air flow meter is to provide real-time feedback to the engine's electronic control unit (ECU). The ECU uses this information to adjust the fuel injection process accordingly. If the air intake is higher than expected, the ECU will increase the fuel injection to maintain the desired air-fuel mixture. Conversely, if the air intake is lower, the ECU will reduce the fuel to prevent over-fuelling and potential engine damage. This dynamic adjustment ensures that the engine operates efficiently and produces optimal power output.
In addition to its role in fuel injection, the air flow meter also contributes to the overall engine management system. It helps in monitoring the engine's performance and diagnosing potential issues. For instance, if the air flow meter readings deviate significantly from the expected values, it could indicate a problem with the air filter, intake manifold, or even the sensor itself. This information is valuable for technicians and engineers in troubleshooting and maintaining the engine's health.
Modern vehicles often incorporate advanced technologies, such as mass airflow sensors, to enhance the accuracy of air intake measurements. These sensors provide more precise data, allowing for even finer control over the fuel injection process. By combining the air flow meter's measurements with other engine sensors, the ECU can make informed decisions to optimize power, fuel economy, and emissions simultaneously. This sophisticated approach ensures that the engine operates at its peak performance while adhering to environmental regulations.
Optimal Diameter for Steel Fuel Lines: A Comprehensive Guide
You may want to see also
Air-Fuel Balance: Injectors optimize the air-fuel ratio for efficient combustion and reduced emissions
The air-fuel balance is a critical aspect of engine performance and emissions control, and fuel injectors play a pivotal role in achieving this delicate equilibrium. When dealing with the air in the fuel line, injectors must precisely manage the ratio of air to fuel to ensure optimal combustion. This process is a complex dance of precision and timing, where the fuel injector acts as the conductor, orchestrating the perfect blend of elements for efficient power generation and minimal environmental impact.
In the context of internal combustion engines, the air-fuel ratio is a critical parameter. It represents the mass ratio of air to fuel, and an ideal ratio is crucial for complete combustion. Too much fuel without sufficient air can lead to inefficient burning, resulting in wasted fuel and increased emissions of harmful pollutants. Conversely, an excess of air without enough fuel can cause incomplete combustion, leading to a lack of power and the release of nitrogen oxides, another harmful emission.
Fuel injectors are designed to precisely control the fuel flow into the engine's combustion chamber. They do this by metering and delivering the exact amount of fuel required to achieve the optimal air-fuel ratio. This ratio is typically around 14.7:1, meaning 14.7 parts of air to one part of fuel by weight. Achieving this ratio is essential for efficient combustion, as it ensures that the fuel burns completely, producing the maximum amount of energy with minimal byproducts.
Modern fuel injectors use advanced technology to maintain this balance. They are equipped with pressure regulators that control the fuel pressure, ensuring it is within the optimal range for the engine's operating conditions. Additionally, some injectors have flow rate controllers that precisely manage the volume of fuel delivered, allowing for fine-tuning of the air-fuel ratio. This level of control is vital, especially in high-performance engines or those with strict emissions standards.
The optimization of the air-fuel ratio by fuel injectors has a direct impact on engine performance and environmental friendliness. Efficient combustion results in better fuel economy, reduced exhaust emissions, and improved engine power. By ensuring that the fuel burns completely, the injector minimizes the release of harmful pollutants, contributing to cleaner air and a more sustainable environment. This intricate process showcases the sophistication of fuel injection technology and its role in maintaining the delicate balance between power and environmental responsibility.
F150 Fuel Line: Understanding Proper Ratings and Safety
You may want to see also
Frequently asked questions
Fuel injectors are designed to precisely control the ratio of fuel and air in the combustion chamber. They achieve this by atomizing the fuel into a fine spray and mixing it with the incoming air. This process ensures that the air-fuel mixture is optimal for efficient combustion, providing the right balance of power and fuel economy.
Air pressure is crucial in fuel injectors as it helps to create a consistent and controlled flow of air into the engine. The injector regulates the air pressure to match the fuel pressure, ensuring a precise mixture. This regulation is vital for maintaining the correct air-fuel ratio and overall engine performance.
Fuel injectors are equipped with sensors that monitor the air density. These sensors provide real-time data, allowing the injector to adjust the fuel injection timing and quantity accordingly. By compensating for changes in air density, the system ensures that the engine receives the correct amount of fuel, regardless of the environmental conditions.
The air flow meter measures the volume of air entering the engine and provides this information to the fuel injector. This data is essential for calculating the required fuel amount. By accurately assessing the air intake, the fuel injector can deliver the precise fuel dosage needed for optimal combustion.
Air temperature affects the density of the air, which in turn influences the fuel-air mixture. Fuel injectors are calibrated to account for these temperature variations. By adjusting the fuel injection parameters, the system maintains the desired air-fuel ratio, ensuring stable engine operation across different ambient temperatures.