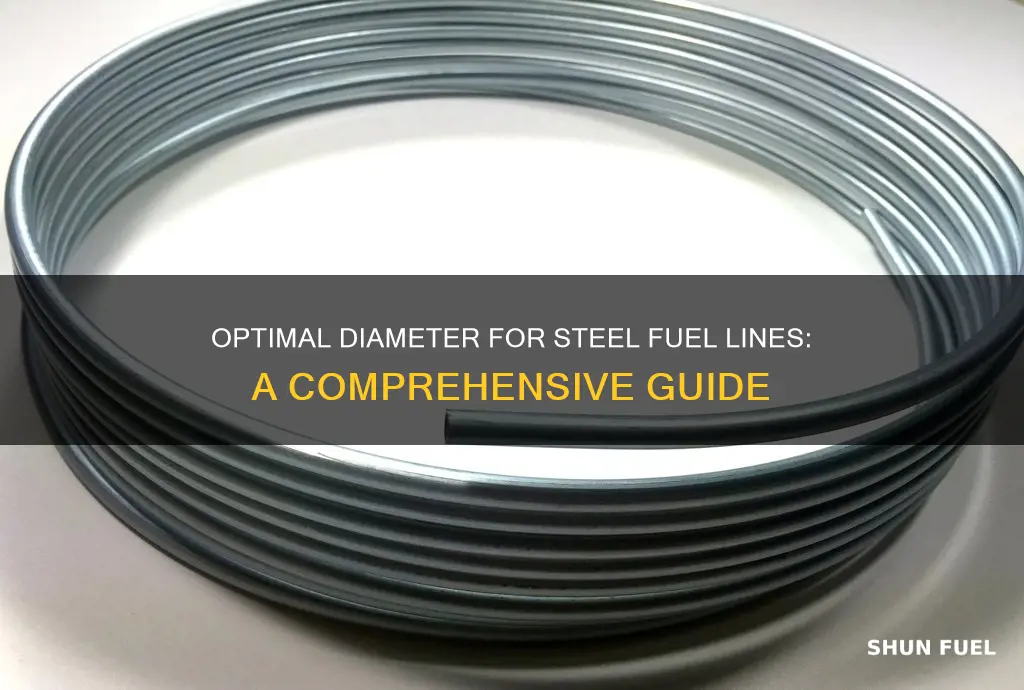
When it comes to steel fuel lines, determining the most appropriate size is crucial for optimal performance and safety. The size of the fuel line directly impacts the flow rate and pressure, which are essential for efficient fuel delivery to the engine. In this discussion, we will explore the various factors that influence the choice of steel fuel line size, including engine requirements, fuel pressure, and environmental conditions. Understanding these considerations will help enthusiasts and professionals alike make informed decisions to ensure reliable and powerful engine operation.
Characteristics | Values |
---|---|
Common Diameter | 3/8" to 1/2" |
Working Pressure | Up to 250 psi |
Material | Steel (usually carbon steel or stainless steel) |
Temperature Range | -40°F to 250°F (-40°C to 121°C) |
Applications | Fuel injection systems, racing cars, aircraft, and industrial machinery |
Advantages | High strength, durability, and resistance to corrosion |
Disadvantages | Can be heavy and more expensive than other materials |
Flexibility | Moderate flexibility, but can be bent to some extent |
Compatibility | Suitable for gasoline and diesel fuel |
Standard Length | Varies, often sold in meters or feet |
Color | Often black or blue, but can be customized |
What You'll Learn
- Material Thickness: Thickness of steel fuel lines varies based on pressure and temperature
- Diameter Range: Steel fuel lines typically range from 1/4 to 1/2 in diameter
- Length Considerations: Line length impacts size choice; longer lines may require larger diameters
- Pressure Rating: Higher pressure requires thicker, larger diameter steel fuel lines
- Temperature Tolerance: Steel lines must withstand temperature fluctuations, affecting size and material choice
Material Thickness: Thickness of steel fuel lines varies based on pressure and temperature
The thickness of steel fuel lines is a critical factor in determining their suitability for specific applications, especially in high-pressure and high-temperature environments. The material thickness directly influences the line's ability to withstand these conditions without compromising performance and safety.
In general, steel fuel lines are designed with a specific thickness to ensure they can handle the expected pressures and temperatures in the system. Thicker walls provide better protection against pressure and temperature extremes, making them ideal for high-performance engines or applications with varying environmental conditions. For instance, in racing cars, where fuel lines are exposed to rapid acceleration and deceleration, thicker steel lines are often preferred to prevent leaks and ensure efficient fuel delivery.
The relationship between material thickness and pressure is particularly important. Thicker steel can withstand higher pressure without deforming or leaking. This is crucial in fuel systems where pressure can fluctuate rapidly, especially during engine operation. Engineers must carefully select the thickness to balance strength and flexibility, ensuring the lines can accommodate pressure changes without failing.
Temperature also plays a significant role in determining the appropriate thickness. Steel fuel lines used in high-temperature environments, such as those found in industrial settings or certain automotive applications, require thicker walls to maintain structural integrity. Thicker lines can better resist thermal expansion and contraction, reducing the risk of cracks or leaks over time.
In summary, the material thickness of steel fuel lines is a critical design consideration. It directly impacts the line's ability to handle pressure and temperature variations, ensuring optimal performance and safety. Engineers and designers must carefully select the thickness based on the specific requirements of the application to ensure the fuel lines meet the necessary standards and provide reliable operation.
Understanding Snowmobile Fuel Lines: Inside the Gas Tank
You may want to see also
Diameter Range: Steel fuel lines typically range from 1/4 to 1/2 in diameter
When it comes to choosing the right size for steel fuel lines, it's important to understand the typical diameter range to ensure optimal performance and safety. Steel fuel lines are an essential component in vehicle fuel systems, responsible for transporting fuel from the tank to the engine. The diameter of these lines plays a crucial role in determining the flow rate and pressure, which directly impacts the engine's performance and efficiency.
The diameter range for steel fuel lines is generally between 1/4 inch and 1/2 inch. This range is carefully selected to balance the need for efficient fuel delivery with the structural integrity required to withstand pressure and potential vibrations during vehicle operation. Smaller diameters, such as 1/4 inch, are often used for high-pressure applications and can provide a more direct and efficient fuel supply to the engine. These smaller lines are commonly found in high-performance vehicles or those with advanced fuel injection systems.
On the other hand, larger diameters, typically around 1/2 inch, are favored for their ability to handle higher fuel flow rates. This is particularly important in applications where the engine requires a substantial amount of fuel, such as in larger vehicles or those with powerful engines. The increased diameter allows for a smoother and more consistent fuel supply, ensuring that the engine receives the necessary amount of fuel for optimal performance.
It's worth noting that the choice of diameter also depends on the specific requirements of the vehicle's fuel system design. Factors such as engine displacement, fuel consumption, and the presence of any fuel pressure regulators or pumps can influence the diameter selection. For instance, a high-performance engine might benefit from smaller diameter lines to maintain precise fuel control, while a larger vehicle with a high fuel demand may opt for larger lines to accommodate the increased flow rate.
In summary, the diameter range of steel fuel lines is a critical consideration when upgrading or replacing fuel lines. Understanding this range allows enthusiasts and professionals to make informed decisions, ensuring that the fuel lines meet the performance demands of the vehicle while also providing the necessary structural support. Always consult the vehicle's manual or seek expert advice to determine the most suitable diameter for a specific application.
Miata Fuel Line Sizes: A Comprehensive Guide
You may want to see also
Length Considerations: Line length impacts size choice; longer lines may require larger diameters
When it comes to selecting the appropriate size of steel fuel line, one crucial factor to consider is the length of the line itself. The length of the fuel line plays a significant role in determining the necessary diameter to ensure optimal performance and safety. Longer fuel lines present unique challenges that require careful consideration.
As the length of the fuel line increases, the pressure drop across the line also increases. This is primarily due to the friction and resistance encountered by the fuel as it travels through the longer path. To mitigate this issue, it is essential to choose a larger diameter for the fuel line. A larger diameter allows for a smoother flow of fuel, reducing the pressure drop and ensuring a consistent supply to the engine. This is particularly important in high-performance applications where fuel efficiency and power delivery are critical.
The impact of line length on size choice becomes even more apparent in long-distance fuel delivery systems or those with complex routing. In such cases, the fuel line may need to navigate around obstacles, making it longer and more challenging to manage. By selecting a larger diameter, you can accommodate the increased pressure drop and maintain a reliable fuel supply even over extended distances. This is especially crucial in racing or high-performance vehicles where every second counts.
Additionally, longer fuel lines may also require more frequent bends and turns, which can further contribute to pressure drops. The larger diameter fuel line provides the necessary flexibility to navigate these bends without compromising the flow rate. It ensures that the fuel reaches the engine efficiently, even when the line is bent or routed in a specific manner.
In summary, when dealing with longer fuel lines, it is imperative to choose a larger diameter to compensate for the increased pressure drop and ensure a consistent fuel supply. This consideration is vital for maintaining optimal engine performance and safety, especially in demanding applications. By understanding the relationship between line length and size, engineers and enthusiasts can make informed decisions when selecting steel fuel lines for their vehicles.
Choosing the Right Tubing for Your Fuel Line: A Comprehensive Guide
You may want to see also
Pressure Rating: Higher pressure requires thicker, larger diameter steel fuel lines
When it comes to steel fuel lines, the pressure rating is a critical factor that determines the size and thickness of the line required. Higher pressure applications demand thicker and larger diameter steel fuel lines to ensure safe and efficient operation. This is because increased pressure can lead to several issues if not properly managed. Firstly, it can cause the fuel line to become more susceptible to damage from external factors such as road debris or accidental impacts. Thicker steel provides additional protection against punctures and tears, ensuring the integrity of the fuel system.
The larger diameter of the fuel line is essential to accommodate the higher pressure and maintain a consistent fuel flow. A smaller diameter line would restrict the flow, leading to potential performance issues and reduced engine power. With a larger diameter, the fuel can travel through the line with minimal resistance, ensuring optimal engine performance. This is particularly important in high-performance vehicles or applications where fuel efficiency and power output are crucial.
In addition to the physical attributes, the pressure rating also influences the material properties of the steel. Higher pressure requires steel with enhanced mechanical properties, such as increased tensile strength and hardness. This ensures that the fuel line can withstand the forces exerted by the pressure without compromising its structural integrity. The steel must be able to resist deformation and maintain its shape, even under extreme conditions.
It is worth noting that the pressure rating of the fuel line should be carefully matched to the specific application. Different engines and fuel systems have varying pressure requirements, and using the correct size and thickness is essential for safety and performance. Engineers and designers must consider the operating conditions, fuel type, and system design to determine the appropriate pressure rating and, consequently, the size of the steel fuel line.
In summary, when dealing with higher pressure fuel systems, thicker and larger diameter steel fuel lines are necessary. This ensures the line can withstand the increased pressure, maintain fuel flow, and provide the required protection against potential damage. Understanding the relationship between pressure rating and steel fuel line size is crucial for anyone involved in the design, installation, or maintenance of fuel systems, especially in high-performance or critical applications.
Unveiling the Mystery: Why Air Intrudes in Fuel Lines
You may want to see also
Temperature Tolerance: Steel lines must withstand temperature fluctuations, affecting size and material choice
When it comes to fuel lines, especially those made of steel, temperature tolerance is a critical factor that cannot be overlooked. Steel fuel lines are designed to transmit fuel from the tank to the engine, and they must be able to withstand the extreme temperature variations that occur in different environments. This is particularly important in automotive applications, where fuel lines are exposed to the harsh conditions of the engine bay.
The size of a steel fuel line is directly related to its temperature tolerance. As temperatures drop, the fuel line's flexibility and ability to withstand contraction become crucial. Thicker walls and a larger diameter are often required to ensure the line can handle the reduced volume of fuel without compromising its structural integrity. This is why it's essential to choose the appropriate size based on the operating temperature range. For instance, in cold climates, a larger-sized fuel line might be necessary to prevent freezing and ensure a consistent fuel supply.
The material choice is another critical aspect of temperature tolerance. Different types of steel offer varying levels of resistance to temperature changes. For high-temperature applications, such as racing or high-performance vehicles, stainless steel is often preferred due to its excellent heat resistance and corrosion-resistant properties. On the other hand, for standard automotive use, carbon steel or galvanized steel might be suitable, depending on the specific temperature range and environmental conditions.
In colder climates, the fuel line's material must be able to withstand freezing temperatures without becoming brittle. This often requires the use of materials with lower carbon content or the addition of plasticizers to enhance flexibility. In contrast, for high-temperature environments, materials like stainless steel or alloys with higher chromium content are chosen to resist oxidation and maintain their structural integrity.
In summary, temperature tolerance is a key consideration when selecting the size and material for steel fuel lines. Engineers and designers must carefully evaluate the operating conditions to choose the appropriate size and material combination, ensuring the fuel lines can handle the temperature fluctuations without compromising performance or safety. This attention to detail is vital in the automotive industry to guarantee reliable fuel delivery systems.
Fuel Line Sizing for the Jeep TJ: A Guide
You may want to see also
Frequently asked questions
The most common size for steel fuel lines is 3/8 inch in diameter. This size is widely used in automotive applications due to its balance between flow rate and flexibility.
While using a larger diameter steel fuel line can improve flow rate and potentially enhance performance, it is important to consider the limitations of the vehicle's fuel system. Larger lines may require modifications to the fuel pump and injectors to handle the increased volume, and they might also be less flexible, making installation more challenging.
The length of the steel fuel line can vary depending on the vehicle's design and the desired installation. Typically, fuel lines are designed to be long enough to reach from the fuel tank to the engine, allowing for some flexibility during engine movement. However, it is crucial to ensure that the lines are not too long, as this can lead to unnecessary pressure drops and potential fuel vaporization.
To determine the correct size, you should consult your vehicle's manual or seek advice from a professional mechanic. They can provide specific recommendations based on your car's make, model, and engine type. Additionally, considering the fuel system's requirements, such as flow rate and pressure, will help you choose the most suitable size.