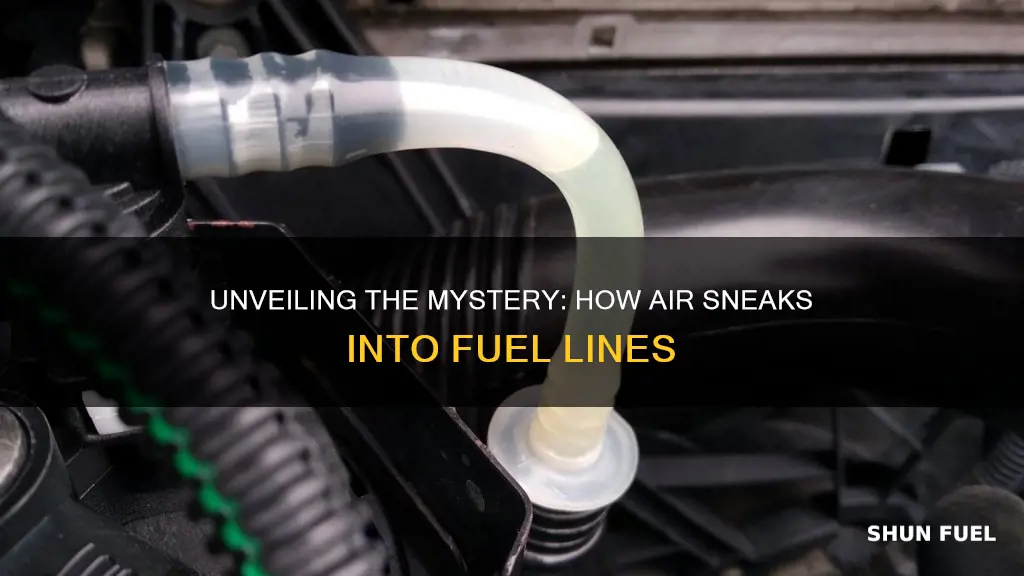
The process of how air gets into fuel lines is an important aspect of engine performance and maintenance. When air enters the fuel line, it can lead to a variety of issues, including reduced engine efficiency, performance problems, and even engine damage. Understanding the causes and effects of air in the fuel line is crucial for mechanics and car owners alike. This paragraph will explore the various factors that contribute to air infiltration, such as fuel pump issues, faulty fuel injectors, and the natural tendency of air to enter any open system. By delving into these factors, we can gain a comprehensive understanding of how air finds its way into fuel lines and the potential consequences.
What You'll Learn
- Fuel Pump Function: The fuel pump delivers fuel from the tank to the engine, creating pressure to draw air into the line
- Air Pressure Differential: Air flows from areas of high pressure (atmosphere) to low pressure (inside the fuel line)
- Fuel Injector Design: Injectors are designed to create a vacuum, drawing air into the fuel-air mixture
- Vacuum System: The engine's vacuum system assists in drawing air into the fuel line during operation
- Fuel Line Material: Special materials allow air to pass through while preventing fuel leakage
Fuel Pump Function: The fuel pump delivers fuel from the tank to the engine, creating pressure to draw air into the line
The fuel pump is a critical component in the fuel system of an engine, responsible for ensuring a steady and efficient supply of fuel to the engine's combustion chambers. Its primary function is to deliver fuel from the fuel tank to the engine, creating the necessary pressure to facilitate the intake of air into the fuel line. This process is essential for the engine's proper operation and performance.
When the engine is running, the fuel pump operates continuously, drawing fuel from the tank and sending it through the fuel line. The pump is typically driven by the engine's timing belt or chain, ensuring that it runs in sync with the engine's cycles. As the pump operates, it generates a controlled amount of pressure, which is crucial for several reasons. Firstly, it ensures that the fuel is delivered at the right pressure to the engine, allowing for efficient atomization and mixing with air in the intake system. This precise pressure control is vital for maintaining optimal engine performance and fuel efficiency.
The pressure created by the fuel pump also plays a significant role in drawing air into the fuel line. As the pump pushes fuel through the line, it creates a partial vacuum, which pulls air into the system. This process is often referred to as 'vacuum-assisted air intake.' The air is drawn into the fuel line, where it mixes with the fuel, creating a combustible mixture. This mixture is then directed to the engine's intake valves, where it is ignited, powering the engine's operation.
In modern vehicles, the fuel pump's function is highly regulated and often integrated with the engine's electronic control unit (ECU). The ECU monitors the fuel pressure and adjusts the pump's operation accordingly. This ensures that the fuel pressure remains within the optimal range, providing the engine with the precise amount of fuel required for efficient combustion. Additionally, the ECU can adjust the pump's performance based on driving conditions, such as speed, load, and temperature, further optimizing the engine's operation.
In summary, the fuel pump's role in delivering fuel and creating pressure is fundamental to the engine's ability to draw air into the fuel line. This process ensures a well-regulated fuel supply, enabling efficient combustion and optimal engine performance. Understanding the fuel pump's function is essential for maintaining and troubleshooting fuel-related issues in vehicles, as it directly impacts the engine's overall health and efficiency.
Auto Body Repair: Can Shops Fix Fuel Lines?
You may want to see also
Air Pressure Differential: Air flows from areas of high pressure (atmosphere) to low pressure (inside the fuel line)
The concept of air pressure differential is fundamental to understanding how air can enter fuel lines. In this scenario, the atmosphere acts as a vast reservoir of air at a higher pressure compared to the pressure inside the fuel line. This pressure difference creates a natural flow of air, similar to how water flows from a higher elevation to a lower one.
When the fuel line is filled with fuel, it creates a low-pressure environment within the line. This low pressure is relative to the surrounding atmosphere, which exerts a higher pressure. As a result, air from the atmosphere, being at a higher pressure, tends to flow into the fuel line to equalize the pressure. This process is driven by the basic principle of pressure equalization, ensuring that the pressure inside the fuel line matches the atmospheric pressure.
The flow of air into the fuel line is a continuous process. As soon as the pressure inside the line becomes lower than the atmospheric pressure, air will continue to enter until equilibrium is reached. This dynamic process ensures that the fuel line maintains a consistent pressure, which is crucial for the proper functioning of the fuel system.
It's important to note that this air-fuel mixture is not ideal for combustion. The presence of air in the fuel line can lead to several issues. Firstly, it can cause the fuel to become less concentrated, affecting the engine's performance. Secondly, air bubbles in the fuel can lead to poor fuel atomization, resulting in incomplete combustion and reduced engine efficiency.
To mitigate these problems, fuel systems often employ various mechanisms. These include fuel pumps that maintain a consistent pressure, ensuring that the fuel line remains at a slightly higher pressure than the atmosphere. Additionally, fuel filters can trap any air bubbles or contaminants that may have entered the system, ensuring a clean and efficient fuel supply.
Barb Connectors: Essential or Redundant? The Fuel Line Debate
You may want to see also
Fuel Injector Design: Injectors are designed to create a vacuum, drawing air into the fuel-air mixture
Fuel injectors are a crucial component in modern vehicle engines, responsible for delivering the precise amount of fuel required for optimal combustion. The design of these injectors is intricate and plays a vital role in ensuring efficient engine performance. One of the key principles behind their operation is the creation of a vacuum, which facilitates the intake of air into the fuel-air mixture.
The process begins with the injector's ability to generate a low-pressure region, or vacuum, within the fuel line. This is achieved through a carefully engineered design that includes a series of precision-made components. At the heart of the injector is a small, high-pressure pump that draws fuel from the fuel tank and injects it into a narrow passageway. As the fuel is injected, it creates a region of low pressure in the line, pulling air from the atmosphere into the system. This air-fuel mixture is then carefully managed to ensure the correct ratio for combustion.
The design of the injector nozzles is critical to this process. These nozzles are shaped and angled to create a specific flow pattern, directing the fuel and air into the engine's combustion chamber. The shape and size of the nozzles influence the speed and direction of the fuel-air stream, ensuring it mixes thoroughly and efficiently. This design also considers the pressure and temperature requirements to atomize the fuel, allowing it to burn completely and cleanly.
Additionally, fuel injectors are designed with a mechanism to control the flow rate of the fuel-air mixture. This is achieved through a series of valves and solenoids that can precisely regulate the amount of fuel injected. By adjusting the fuel flow, the injector can maintain the optimal air-fuel ratio, ensuring the engine operates efficiently and meets emissions standards.
In summary, fuel injectors are engineered to create a vacuum, drawing air into the fuel-air mixture, which is then carefully managed to optimize engine performance. The design involves intricate nozzles and flow control mechanisms, all working together to deliver the precise fuel-air mixture required for efficient combustion in modern vehicle engines. This process highlights the complexity and precision required in fuel injector design.
Fixing a Fuel Line: A Step-by-Step Guide to Repair
You may want to see also
Vacuum System: The engine's vacuum system assists in drawing air into the fuel line during operation
The vacuum system in an engine is a crucial component that plays a vital role in ensuring efficient fuel delivery and combustion. When the engine is running, it creates a low-pressure area or a vacuum within the system, which is a result of the engine's internal combustion process. This vacuum effect is harnessed to draw air into the fuel line, a process that is essential for proper engine operation.
As the engine operates, the vacuum system creates a partial vacuum, which is essentially a region of low pressure. This low pressure is generated by the engine's cylinders during the downstroke of the pistons. When the pistons move downward, they create a space that is devoid of pressure, pulling air from the atmosphere into the engine's intake system. This air is then directed towards the fuel line, where it is mixed with the fuel to create a combustible mixture.
The vacuum system's primary function is to assist in the induction process, ensuring that a steady supply of air is available for the combustion process. When the engine is idling or at low speeds, the vacuum effect becomes even more critical. During these conditions, the engine's ability to draw air into the fuel line is limited due to the reduced airflow. Here, the vacuum system steps in to create the necessary pressure differential, allowing for efficient air intake and fuel injection.
In modern engines, the vacuum system is often integrated with the fuel injection system to optimize performance. The vacuum-assisted fuel injection ensures that the correct air-fuel mixture is delivered to the engine's cylinders. This precision in fuel delivery is crucial for maintaining optimal engine operation, as it directly impacts power output, fuel efficiency, and emissions.
Additionally, the vacuum system's design and functionality can vary between different engine types and models. Some engines may utilize a mechanical vacuum pump to enhance the vacuum effect, especially in high-performance applications where air intake needs to be maximized. This pump creates an even stronger low-pressure area, allowing for improved air induction and fuel efficiency. Understanding the vacuum system's role is essential for engine mechanics and enthusiasts, as it highlights the intricate relationship between air and fuel in the engine's operation.
John Deere LX255 Fuel Line Location: A Comprehensive Guide
You may want to see also
Fuel Line Material: Special materials allow air to pass through while preventing fuel leakage
The fuel lines in a vehicle's engine are crucial components that deliver fuel from the tank to the engine's carburetor or fuel injectors. Over time, these lines can become susceptible to the intrusion of air, which can lead to various performance issues. Understanding how air enters the fuel line is essential for implementing effective solutions to prevent these problems.
One primary method of air infiltration is through small openings or cracks in the fuel line itself. These openings can be a result of wear and tear, corrosion, or damage during installation or repairs. When air seeps into the fuel line, it can cause the fuel to become less dense, leading to a condition known as "airlock." Airlock can result in poor engine performance, as the engine may not receive the correct fuel-air mixture, causing it to run rich (with too much fuel) or lean (with too little fuel).
Another way air can enter the fuel system is through the fuel pump. The pump is designed to draw fuel from the tank and deliver it to the engine. However, if the pump is not functioning correctly, it may create a partial vacuum, allowing air to enter the system. This is particularly common in older vehicles or those with faulty pumps.
To address these issues, engineers have developed specialized materials for fuel lines that incorporate unique properties. These materials are designed to allow air to pass through while simultaneously preventing fuel leakage. One such material is a composite of woven fibers and a flexible, durable outer layer. The fibers create a semi-permeable membrane, allowing air molecules to pass through while retaining the fuel's larger molecules. This ensures that air can enter the system without compromising the integrity of the fuel.
Additionally, some fuel lines are equipped with small, carefully designed perforations or pores along their length. These openings are strategically placed to allow air to enter the line without creating a path for fuel to escape. The material's composition and structure are optimized to ensure that only air molecules can pass through, maintaining the fuel's integrity. This design not only prevents airlock but also ensures a consistent fuel supply, promoting optimal engine performance.
Optimizing Fuel Delivery: Choosing the Right PSI for Your Fuel Line
You may want to see also
Frequently asked questions
Air can enter the fuel line due to a few reasons. One common cause is a faulty fuel pump or pressure regulator, which may allow air to be drawn into the system when the fuel flow is interrupted. Additionally, if the fuel tank is not properly sealed, air can seep in and mix with the fuel.
Air in the fuel line can lead to poor engine performance. When air is introduced, it can cause fuel to become less dense, resulting in a leaner fuel-air mixture. This can lead to reduced power, decreased fuel efficiency, and even engine misfires or stalling.
There are several indicators that air has entered the fuel system. These include a decrease in engine power, rough idling, and increased fuel consumption. You might also notice a change in the engine's sound, becoming more erratic or noisy.
To prevent air intrusion, it's essential to maintain the fuel system's integrity. Regularly inspect and replace old or damaged fuel lines, pumps, and filters. Ensure that the fuel tank is sealed properly and consider using a fuel stabilizer to maintain the fuel's quality.
Yes, you can bleed the air out of the fuel line. This process involves starting the engine and allowing it to run while simultaneously opening and closing the fuel line's bleeder valve. This action forces any trapped air to be expelled from the system. It's recommended to consult the vehicle's manual for specific instructions.