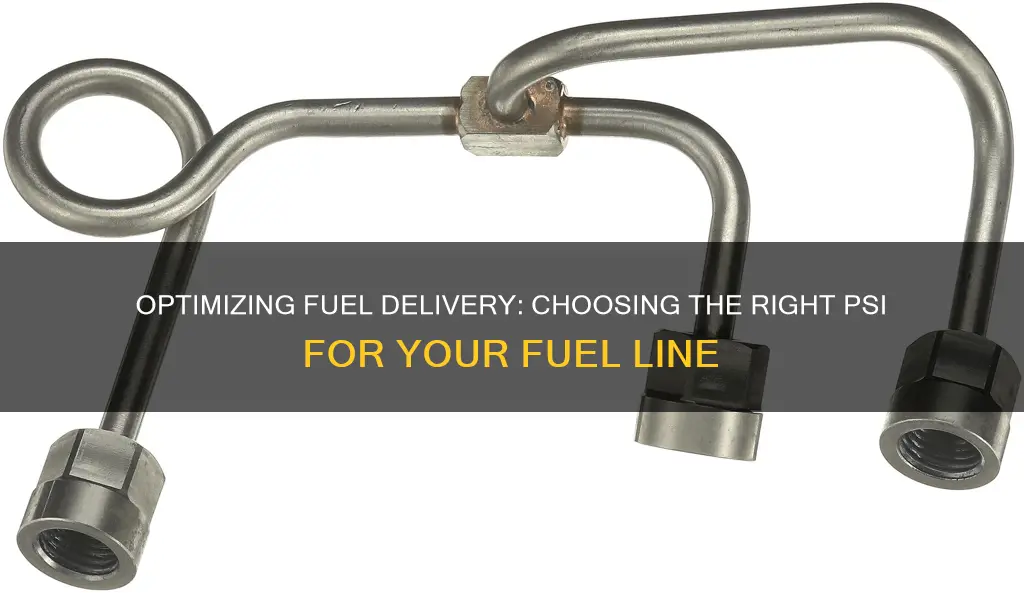
When it comes to fuel lines, understanding the correct psi (pounds per square inch) is crucial for optimal performance and safety. The psi rating determines the pressure a fuel line can withstand, ensuring it can handle the fuel's flow rate and prevent leaks or damage. This is especially important in high-performance vehicles or applications where fuel pressure might vary significantly. Knowing the right psi for your fuel line is essential to ensure your engine runs efficiently and reliably, preventing potential issues caused by incorrect pressure.
What You'll Learn
- Fuel Line Material: Consider psi requirements for different materials like rubber, plastic, or metal
- Fuel Pressure Regulation: psi specifications for fuel pressure regulators and their impact on engine performance
- Fuel Line Diameter: psi recommendations based on fuel line diameter and flow rate
- Fuel System Design: psi considerations for fuel system design, including pumps and injectors
- Fuel Line Length: psi adjustments for fuel lines of varying lengths and potential pressure drops
Fuel Line Material: Consider psi requirements for different materials like rubber, plastic, or metal
When it comes to choosing the right material for your fuel line, understanding the pressure requirements, or psi (pounds per square inch), is crucial. Different materials have varying psi ratings, which determine their ability to withstand fuel pressure and prevent leaks. Here's a breakdown of the psi considerations for common fuel line materials:
Rubber Fuel Lines: Rubber is a popular choice for fuel lines due to its flexibility and durability. The psi requirements for rubber fuel lines typically range from 100 to 200 psi. This range ensures that the rubber material can handle the pressure of fuel without compromising its structural integrity. Higher-quality rubber compounds may offer even greater psi ratings, making them suitable for more demanding applications. It's important to select a rubber fuel line with a psi rating that matches or exceeds the expected fuel pressure in your vehicle to ensure long-lasting performance.
Plastic Fuel Lines: Plastic fuel lines are often lighter and more flexible than rubber alternatives, making them a popular choice for modern vehicles. The psi requirements for plastic fuel lines can vary depending on the specific type of plastic used. Some common plastics used in fuel lines include polyether block amide (PEBA) and polyolefin. PEBA, for instance, often has a psi rating of around 150-200 psi, while polyolefin may offer slightly lower psi ratings of approximately 100-150 psi. These psi ranges provide a good balance between flexibility and pressure resistance, ensuring a reliable fuel supply.
Metal Fuel Lines: Metal fuel lines, typically made from materials like steel or aluminum, are known for their exceptional strength and durability. These lines are often used in high-performance vehicles or applications where extreme conditions are expected. Metal fuel lines can withstand extremely high psi ratings, often exceeding 300 psi. This makes them ideal for racing cars or aircraft, where fuel pressure can be significantly higher. However, metal lines may be less flexible than rubber or plastic, so careful installation is required to avoid damage.
When selecting a fuel line material, it's essential to consider the specific psi requirements of your vehicle's fuel system. Consulting the vehicle's manual or seeking advice from automotive experts can provide valuable insights into the recommended psi range for your particular make and model. Additionally, ensuring that the chosen material meets or exceeds the psi requirements will contribute to a reliable and safe fuel delivery system.
Unraveling the Mystery: Why Fuel Lines Bubble
You may want to see also
Fuel Pressure Regulation: psi specifications for fuel pressure regulators and their impact on engine performance
Fuel pressure regulation is a critical aspect of engine performance, especially in modern vehicles with fuel injection systems. The pressure at which fuel is delivered to the engine's injectors is directly linked to the engine's efficiency, power output, and overall reliability. This is where fuel pressure regulators come into play, acting as the gatekeepers of fuel pressure within the system. These regulators ensure that the fuel pressure is precisely controlled, optimizing the combustion process and maximizing engine performance.
The 'psi' (pounds per square inch) specifications for fuel pressure regulators are a crucial factor in this process. The psi rating indicates the maximum pressure the regulator can withstand and maintain. For instance, a common specification for a fuel pressure regulator might be 60 psi. This means that the regulator is designed to maintain a consistent fuel pressure of up to 60 psi within the fuel system. It's important to note that this pressure is measured at the fuel pump outlet, where the fuel enters the fuel lines.
The impact of these psi specifications on engine performance is significant. Firstly, the correct psi ensures that the fuel is delivered at the right pressure to the injectors. This is vital because fuel injectors are designed to operate within a specific pressure range. If the pressure is too low, the engine may not receive enough fuel, leading to poor performance, reduced power, and potential engine misfires. Conversely, if the pressure is too high, it can lead to excessive fuel atomization, which may result in inefficient combustion and increased emissions.
Moreover, the psi specifications also influence the engine's overall efficiency and longevity. A well-regulated fuel pressure ensures that the engine operates at its optimal combustion temperature and air-fuel ratio. This results in improved fuel economy, reduced engine wear, and a longer lifespan for the engine components, especially the fuel injectors and engine valves.
In summary, understanding and adhering to the psi specifications for fuel pressure regulators is essential for maintaining optimal engine performance. It ensures that the engine receives the correct amount of fuel at the right pressure, leading to improved power, efficiency, and longevity. Regular checks and adjustments of the fuel pressure regulator's psi setting can help keep the engine in top condition and prevent potential issues related to fuel pressure.
Unleash Your Charm: Understanding the Art of Fuel Pick-Up Lines
You may want to see also
Fuel Line Diameter: psi recommendations based on fuel line diameter and flow rate
When it comes to fuel lines, the pressure required (psi) is a critical factor in ensuring efficient and safe fuel delivery to an engine. The pressure in a fuel line is directly related to the diameter of the line and the flow rate of the fuel. Here's a detailed look at how these factors influence psi recommendations:
Fuel Line Diameter: The diameter of the fuel line is a key determinant of the pressure it can withstand and the flow rate it can handle. Generally, larger diameter fuel lines can accommodate higher flow rates and, consequently, higher psi. For example, a 1/4-inch fuel line is typically used for low-pressure applications and may only require a psi of 50-70. In contrast, a 3/8-inch line, which is more common in high-performance applications, can handle a psi of up to 100-120. The increased diameter allows for a larger cross-sectional area, enabling more fuel to flow through the line at a given pressure.
Flow Rate: The flow rate of fuel, measured in gallons per minute (gpm), is another critical factor. Higher flow rates require more psi to ensure the fuel reaches the engine at the desired pressure. For instance, a fuel pump with a flow rate of 5 gpm might operate efficiently at a psi of 60-80, while a pump with a higher flow rate of 10 gpm could require a psi of 100-120. The relationship between flow rate and psi is linear; as the flow rate increases, so does the recommended psi.
Calculating psi: To determine the appropriate psi for a specific fuel line, you can use the following guidelines: Start by identifying the flow rate of your fuel pump and the desired pressure at the engine. Then, consider the diameter of the fuel line. For each inch of fuel line diameter, you can typically increase the psi by 10-15 psi, up to a maximum of 100-120 psi for most common fuel lines. However, it's essential to consult the manufacturer's specifications for your specific fuel system, as these recommendations may vary.
Safety Considerations: It's crucial to remember that exceeding the recommended psi can lead to fuel line failure, which can result in engine damage or even a dangerous fuel leak. On the other hand, insufficient psi may result in poor engine performance, such as reduced power and fuel efficiency. Therefore, it's essential to strike a balance between the flow rate, line diameter, and psi to ensure optimal engine operation.
In summary, the psi required for a fuel line is closely tied to the diameter of the line and the flow rate of the fuel. Larger diameter lines and higher flow rates generally allow for higher psi. By understanding these relationships and consulting manufacturer guidelines, you can ensure that your fuel system operates efficiently and safely.
Camaro Fuel Line Placement: Above or Below Battery Cables?
You may want to see also
Fuel System Design: psi considerations for fuel system design, including pumps and injectors
When designing a fuel system, understanding the pressure requirements is crucial to ensure optimal performance and reliability. The pressure in a fuel system, often referred to as psi (pounds per square inch), plays a significant role in the efficiency and functionality of the entire setup. This is particularly important when considering the components such as fuel pumps and injectors, which are integral to the fuel delivery process.
The psi rating for fuel lines and components is a critical specification that determines the system's ability to deliver fuel efficiently. For instance, fuel pumps are designed to operate within a specific psi range to ensure they can deliver the required volume of fuel at the right pressure. If the pump operates at too low a pressure, it may struggle to meet the demands of the engine, leading to reduced performance. Conversely, excessive pressure can cause fuel to vaporize, leading to potential issues with atomization and combustion.
In the context of fuel injectors, psi considerations are equally vital. Injectors are responsible for precisely metering and injecting fuel into the engine's cylinders. The psi rating of the fuel system must be matched to the injector's specifications to ensure accurate fuel delivery. If the pressure is too low, the injector may not be able to create a fine mist of fuel, leading to incomplete combustion and reduced engine performance. On the other hand, excessive pressure can cause fuel to be injected with too much force, potentially leading to engine misfires or other mechanical issues.
Designing a fuel system requires careful consideration of the engine's requirements and the characteristics of the fuel being used. Factors such as fuel type, engine size, and operating conditions influence the optimal psi range. For example, high-performance engines may require higher psi to ensure efficient fuel delivery, while smaller, more efficient engines might operate within a lower psi range.
In summary, psi considerations are fundamental in fuel system design, impacting the performance and longevity of fuel pumps and injectors. Engineers must carefully select psi ratings that align with the engine's needs, ensuring efficient fuel delivery while avoiding potential issues related to pressure extremes. This meticulous approach to design ensures that the fuel system operates optimally, contributing to the overall performance and reliability of the vehicle.
Unraveling the Mystery: Lines Attached to the Fuel Pump
You may want to see also
Fuel Line Length: psi adjustments for fuel lines of varying lengths and potential pressure drops
When it comes to fuel lines, the length of the line and the potential pressure drops along the way are crucial factors to consider. Longer fuel lines can lead to pressure losses, which may affect the performance of your vehicle. The pressure required in the fuel line is often measured in pounds per square inch (psi), and it's essential to understand how length and pressure drops impact this measurement.
As a general rule, the longer the fuel line, the higher the pressure drop can be expected. This is because the fuel has to travel a greater distance, and as it moves through the line, some pressure is lost due to friction and other factors. For instance, a fuel line that is 10 feet long might experience a pressure drop of 5-10 psi, while a much longer line of 50 feet could result in a pressure loss of 20-30 psi or more. This pressure drop can be critical, especially for high-performance vehicles that require precise fuel delivery.
To mitigate these pressure drops, it's common to use pressure regulators or boosters in the fuel line. These devices can maintain a consistent pressure throughout the line, ensuring that the engine receives the required amount of fuel at the correct pressure. For shorter fuel lines, a simple pressure regulator might suffice, but for longer lines, a more robust system may be necessary.
Adjusting the psi for longer fuel lines involves considering the engine's requirements and the potential pressure losses. You can use pressure gauges to measure the pressure at different points along the line and identify areas where adjustments are needed. By carefully selecting the right pressure regulator or booster and ensuring proper installation, you can optimize the fuel delivery system and maintain optimal engine performance.
In summary, when dealing with fuel lines of varying lengths, it's crucial to account for potential pressure drops. Longer lines require careful consideration of psi adjustments to ensure efficient fuel delivery. Understanding these factors and implementing the necessary adjustments will contribute to a well-functioning fuel system in your vehicle.
Polaris Ranger 570 Fuel Line Fittings: A Comprehensive Guide
You may want to see also
Frequently asked questions
The recommended psi for a fuel line can vary depending on the specific application and vehicle. As a general guideline, most fuel lines are designed to operate within a range of 50 to 100 psi. However, it's crucial to consult the vehicle's manual or manufacturer's specifications to determine the exact psi requirement for your particular make and model.
To find the appropriate psi, start by checking the vehicle's owner's manual, which often includes detailed information about the fuel system. If the manual doesn't provide specific psi values, you can contact the vehicle manufacturer's customer support or consult a professional mechanic who can advise based on your car's specifications.
Using a higher psi fuel line than specified can lead to potential issues. Exceeding the recommended psi may cause excessive pressure, which can result in fuel line damage, leaks, or even fuel system failure. It's essential to adhere to the manufacturer's guidelines to ensure optimal performance and safety.