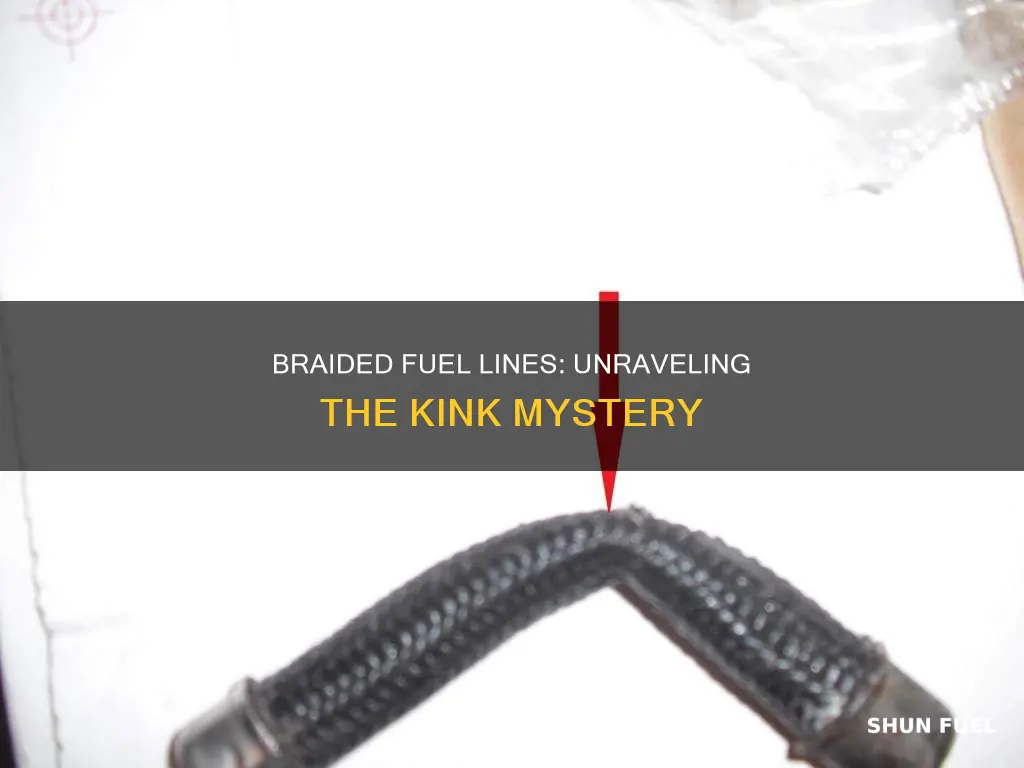
When it comes to fuel lines, durability and reliability are crucial, especially in high-performance vehicles. One popular choice for fuel lines is steel braided fuel lines, known for their strength and flexibility. However, a common concern among car enthusiasts and mechanics is whether these lines can kink or become damaged over time. This introduction aims to explore the potential issues related to kinking in steel braided fuel lines, considering factors such as material quality, installation, and maintenance practices. By understanding these aspects, we can ensure that fuel lines remain in optimal condition, providing a safe and efficient fuel supply to the engine.
Characteristics | Values |
---|---|
Durability | Steel braided fuel lines are highly durable and resistant to kinking, making them a reliable choice for fuel delivery systems. |
Flexibility | Despite their strength, these lines offer flexibility, allowing for easy installation and routing around engine components. |
Temperature Resistance | They can withstand a wide range of temperatures, ensuring performance in various environmental conditions. |
Corrosion Resistance | The braided design and material composition provide excellent resistance to corrosion, preventing degradation over time. |
Fuel Compatibility | These lines are compatible with most fuels, including gasoline, diesel, and ethanol blends. |
Kink Resistance | The braided construction significantly reduces the likelihood of kinking, ensuring a consistent fuel flow. |
Longevity | With proper care, steel braided fuel lines can last much longer than traditional rubber lines, providing long-term reliability. |
Visual Appeal | The braided pattern adds a unique aesthetic to the fuel system, appealing to enthusiasts who value customization. |
Maintenance | Low maintenance is required, as these lines are less prone to leaks and require minimal attention. |
What You'll Learn
- Braided Fuel Line Flexibility: Can steel braided lines bend without kinking
- Fuel Line Pressure: How does pressure affect kinking
- Temperature Effects: Does heat or cold cause kinking
- Line Length: Are longer lines more prone to kinking
- Installation Practices: Proper techniques to prevent kinking during installation
Braided Fuel Line Flexibility: Can steel braided lines bend without kinking?
The debate around the flexibility of steel braided fuel lines has been a topic of interest for many vehicle enthusiasts and mechanics. When it comes to the question of whether steel braided fuel lines can bend without kinking, the answer is a bit more complex than a simple yes or no. These fuel lines are known for their durability and resistance to kinking, which is a common issue with rubber fuel lines. However, their flexibility is not as straightforward.
Steel braided fuel lines are designed with a braided steel wire core, which provides excellent strength and flexibility. The braiding technique allows the line to bend and twist without compromising its structural integrity. This is particularly important in automotive applications where fuel lines need to navigate through tight spaces and make sharp turns. The braided design enables the line to conform to these shapes without kinking or bending out of shape.
One of the key advantages of steel braided fuel lines is their ability to withstand extreme temperatures and pressure fluctuations. The braided construction ensures that the line remains flexible even in harsh conditions. This flexibility is crucial for maintaining a consistent fuel supply to the engine, especially during acceleration and deceleration. Unlike rubber lines, which can become stiff and prone to kinking, steel braided lines can adapt to the vehicle's movements without affecting performance.
However, it's important to note that while steel braided fuel lines offer superior flexibility, there are still factors to consider. The flexibility of the line can vary depending on the thickness and quality of the braided wire. Thinner wires might offer more flexibility but could be more susceptible to damage. Additionally, the overall length of the fuel line and the specific design of the vehicle's fuel system can influence how the line bends and twists.
In summary, steel braided fuel lines are designed to be flexible and resistant to kinking, making them an excellent choice for vehicle fuel systems. Their braided construction allows them to bend and adapt to various shapes and movements without compromising performance. While there are considerations to be made regarding wire thickness and overall design, the flexibility of these fuel lines is generally a reliable feature for ensuring a consistent fuel supply to the engine.
Mastering the Arnold Fuel Line Tool: A Comprehensive Guide
You may want to see also
Fuel Line Pressure: How does pressure affect kinking?
The concept of fuel line pressure and its impact on kinking is an important consideration when dealing with fuel systems, especially in high-performance vehicles or those with modified engines. When discussing the kinking of steel-braided fuel lines, pressure plays a critical role in determining the likelihood and severity of this issue.
In the context of fuel lines, pressure refers to the force exerted by the fuel as it flows through the line. High-pressure fuel systems are common in modern vehicles, particularly in diesel engines, where fuel is delivered at pressures ranging from 200 to 300 psi (pounds per square inch) or even higher. While this pressure is necessary to ensure efficient fuel atomization and combustion, it also has a direct influence on the flexibility and kinking propensity of the fuel line.
When fuel lines are subjected to high pressure, the force exerted on the inner walls of the line can cause it to become more rigid. This increased rigidity makes the fuel line less flexible, especially in the case of steel-braided lines. Steel braiding provides strength and durability but can also make the line more susceptible to kinking, especially at sharp bends or tight turns. Kinking occurs when the fuel line is forced into a tight radius, causing the line to bend excessively and potentially leading to a restriction or blockage in the fuel flow.
The relationship between pressure and kinking is a delicate balance. On one hand, moderate pressure ensures proper fuel delivery and atomization, while on the other, excessive pressure can make the fuel line more prone to kinking. Manufacturers often design fuel systems with specific pressure requirements to optimize performance while minimizing the risk of kinking. For instance, some fuel lines may be designed with a slight bend or radius to reduce the likelihood of kinking, especially in areas where the line might encounter obstacles or vibrations.
To mitigate the risk of kinking due to pressure, several strategies can be employed. One approach is to use fuel lines with a higher flexibility rating, which can better withstand the forces exerted by high-pressure fuel. Additionally, proper routing and installation techniques are crucial. Ensuring that the fuel lines are not subjected to sharp bends or tight turns can significantly reduce the chances of kinking. Regular maintenance and inspections can also help identify any potential issues, allowing for timely adjustments or replacements to prevent kinking-related problems.
Mercury Outboard Fuel Filter Clogging: Causes and Solutions
You may want to see also
Temperature Effects: Does heat or cold cause kinking?
The performance and longevity of fuel lines, especially those made from steel braided materials, can be significantly influenced by temperature variations. When considering the potential for kinking, it's important to understand the role of heat and cold.
Heat can cause the fuel line to expand, leading to increased flexibility and reduced risk of kinking. This is particularly beneficial in high-temperature environments or for applications where the fuel line may be exposed to direct sunlight. The expansion of the steel braided material allows it to bend more easily without putting excessive pressure on the fuel line's inner components. However, it's crucial to note that excessive heat can also lead to material degradation over time, so maintaining a balance is essential.
On the other hand, cold temperatures can present a different challenge. As temperatures drop, the fuel line contracts, which may result in increased rigidity and a higher likelihood of kinking. This is especially true for steel braided fuel lines, as the braiding process can make the material more susceptible to cold-induced stiffness. In extremely cold conditions, the fuel line might not be able to accommodate the movement of the engine or other vehicle components, leading to potential kinks and fuel supply issues.
To mitigate these temperature-related kinking concerns, manufacturers often recommend using fuel lines with specific temperature ratings. These ratings indicate the minimum and maximum temperatures at which the fuel line can operate without compromising its structural integrity. Operating the vehicle within these temperature limits ensures that the fuel line remains flexible and resistant to kinking.
Additionally, proper insulation and protective measures can be employed to shield the fuel line from extreme temperature fluctuations. This may include using heat shields or cold weather kits, especially for applications in diverse climate conditions. By understanding the temperature effects and implementing appropriate measures, vehicle owners can ensure the reliability and longevity of their steel braided fuel lines.
Optimal Diameter for Steel Fuel Lines: A Comprehensive Guide
You may want to see also
Line Length: Are longer lines more prone to kinking?
The length of a fuel line can indeed play a role in its propensity to kink, and this is an important consideration for vehicle owners and mechanics alike. When it comes to steel braided fuel lines, the general consensus is that longer lines are more susceptible to kinking. This is primarily due to the inherent flexibility and rigidity of the material. Steel braided fuel lines are known for their durability and resistance to heat and pressure, but their very design can also make them prone to kinking, especially over longer distances.
The kinking issue arises because longer lines have more material that can potentially twist and bend, especially when the vehicle is in motion or when the fuel tank is not full. As the vehicle accelerates or decelerates, the fuel line may stretch and contract, causing it to twist and form kinks. These kinks can restrict fuel flow, leading to potential engine performance issues, such as reduced power, stalling, or even engine damage over time.
One way to mitigate this problem is to ensure that the fuel lines are properly routed and secured. This includes using appropriate clamps and brackets to keep the lines in place and preventing them from moving or twisting unnecessarily. Additionally, maintaining a consistent fuel level in the tank can help reduce the stress on the fuel lines, as an empty tank can cause the lines to sag and potentially kink.
For those who have experienced kinking in steel braided fuel lines, there are solutions available. One common approach is to use a fuel line protector, which is a flexible sleeve or cover that slides over the fuel line. This protector helps to absorb the impact of road vibrations and reduces the likelihood of kinking. Regular inspections and maintenance can also help identify and address any potential issues before they become major problems.
In summary, while steel braided fuel lines are known for their durability, their length can contribute to the risk of kinking. Proper installation, routing, and maintenance are essential to minimize this risk and ensure optimal engine performance. By understanding the relationship between line length and kinking, vehicle owners can take proactive measures to protect their fuel systems and maintain reliable operation.
Mastering the Art of Aircraft Fuel Cell Line Knots
You may want to see also
Installation Practices: Proper techniques to prevent kinking during installation
When installing steel braided fuel lines, it is crucial to employ proper techniques to prevent kinking, as this can lead to reduced fuel flow, potential engine damage, and performance issues. Here are some detailed installation practices to ensure a smooth and efficient setup:
- Route Planning: Before beginning the installation, carefully plan the route of the fuel line. Consider the engine's layout, available space, and any potential obstacles. Avoid sharp bends or tight turns that could cause the braided steel to kink. Opt for a more flexible path, allowing the line to move freely without restrictions.
- Use of Support: Steel braided fuel lines require proper support to maintain their shape and prevent kinking. Utilize fuel line supports or brackets at regular intervals along the route. These supports should be securely mounted and capable of withstanding the line's tension. Proper support ensures that the line remains in a straight or slightly curved path, reducing the likelihood of kinking.
- Bending and Handling: When bending the steel braided fuel line, exercise caution. Avoid sharp bends, as this can create stress points and potential kinks. Instead, opt for gradual bends and use your hands or tools to apply pressure evenly. Handle the line with care, as excessive force or rough handling can also lead to kinking. It is recommended to wear gloves to protect the line's surface and ensure a smooth bend.
- Connection Techniques: Proper connection methods are essential to prevent kinking at the fuel line's ends. When connecting the line to the fuel pump, engine, or other components, ensure a secure and tight fit. Use fuel line connectors that provide a reliable seal and allow for slight flexibility. Avoid overtightening, as this can restrict movement and cause kinking. Additionally, ensure that all connections are free from sharp edges or protruding components that might catch and kink the line.
- Testing and Inspection: After the installation, thoroughly test the system to identify any potential issues. Start the engine and monitor the fuel flow, ensuring it meets the required specifications. Inspect the fuel lines for any visible kinks or bends that might have occurred during the installation process. Address any concerns promptly to guarantee optimal performance and prevent long-term damage.
By following these installation practices, you can minimize the risk of kinking in steel braided fuel lines, ensuring a reliable and efficient fuel delivery system for your vehicle. Proper planning, support, and handling techniques are key to achieving a smooth and kink-free installation.
Silverado 1998 Fuel Line Removal: A Step-by-Step Guide
You may want to see also
Frequently asked questions
No, steel braided fuel lines are designed to be flexible and resistant to kinking. The braided steel construction allows for a high degree of flexibility, making it less prone to kinking compared to other types of fuel lines. This flexibility is especially beneficial in high-vibration environments, where traditional fuel lines might be more susceptible to damage and kinking.
Yes, steel braided fuel lines can be bent and twisted without permanent damage. The braided design provides a certain degree of give, allowing for adjustments without compromising the integrity of the line. However, it's important to avoid excessive bending or twisting, as it may lead to wear and tear over time. Always ensure that the fuel lines are routed according to the manufacturer's guidelines to maintain optimal performance and longevity.
Steel braided fuel lines can withstand moderate temperatures, but prolonged exposure to high heat can cause degradation. The steel braiding provides some protection against heat, but it's essential to ensure that the fuel lines are not subjected to excessive temperatures, especially in close proximity to hot engine components. Using heat shields or insulation can help prevent damage and maintain the integrity of the fuel lines.