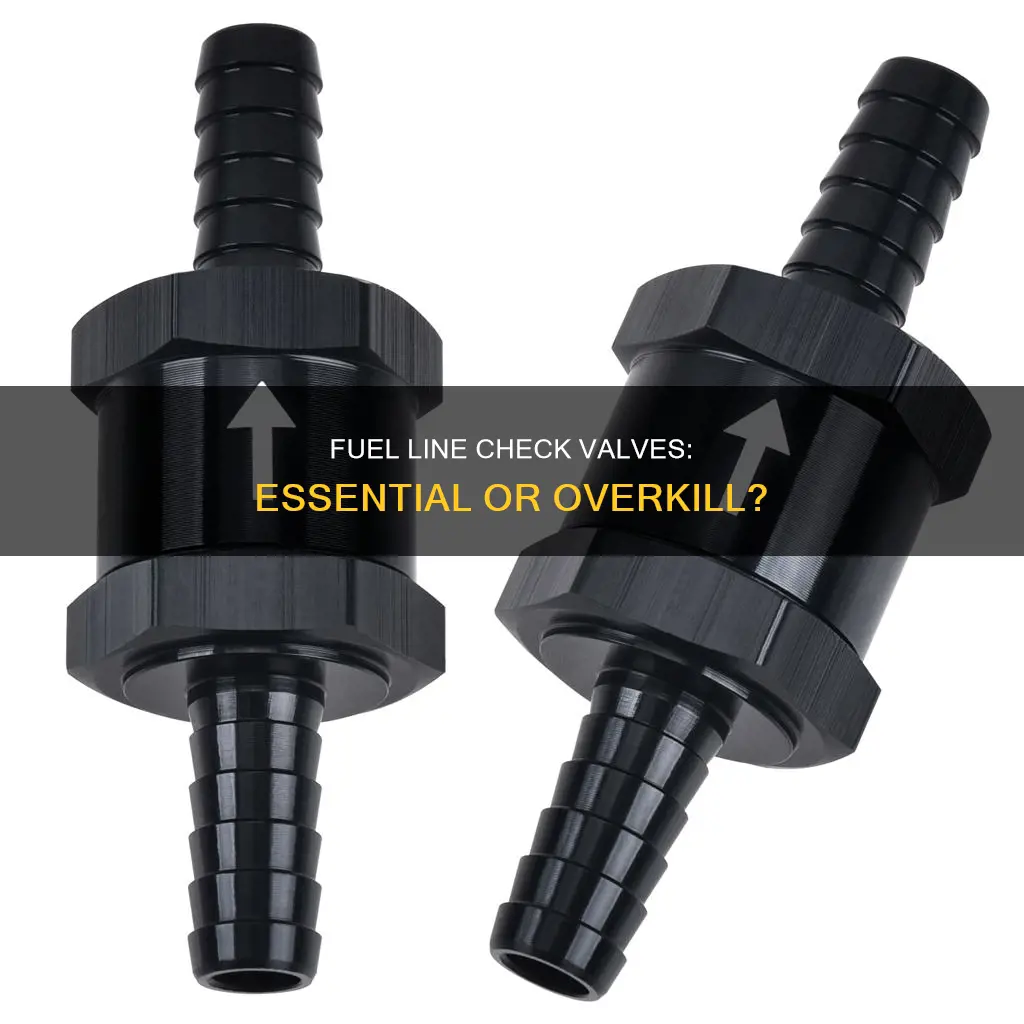
When it comes to vehicle maintenance, ensuring the proper functioning of fuel lines is crucial for safety and performance. One essential component that often raises questions is the check valve within the fuel line. This paragraph aims to explore the necessity of check valves in fuel lines, addressing the common query: Does a fuel line need a check valve? It will delve into the role of check valves in preventing fuel leaks, maintaining pressure, and safeguarding against contamination, ultimately highlighting their importance in vehicle operation and longevity.
Characteristics | Values |
---|---|
Purpose | Prevent fuel from flowing back into the tank when the engine is off |
Location | Typically installed between the fuel pump and the engine |
Material | Rubber, metal, or a combination of both |
Functionality | Allows fuel to flow in one direction only |
Common Issues | Can become clogged, cracked, or damaged over time |
Maintenance | Regular inspection and replacement when necessary |
Compatibility | Varies depending on the vehicle make and model |
Cost | Relatively affordable, but can vary based on the brand and quality |
Installation | May require professional assistance for proper fitting |
What You'll Learn
- Fuel Line Design: Check valves are often integrated into fuel lines to prevent backflow
- Fuel Pressure Regulation: Check valves help maintain optimal fuel pressure in the system
- Engine Performance: Properly functioning check valves ensure efficient engine operation and fuel delivery
- Safety Mechanisms: Check valves act as safety devices to prevent fuel leaks and potential hazards
- Maintenance and Inspection: Regular inspection of check valves is crucial for fuel system longevity
Fuel Line Design: Check valves are often integrated into fuel lines to prevent backflow
Fuel lines are an essential component of any vehicle's fuel system, responsible for transporting fuel from the tank to the engine. While they are designed to be robust and reliable, they can be susceptible to issues such as backflow, which occurs when fuel flows in the opposite direction, potentially causing damage to the engine or leading to performance problems. To mitigate this risk, check valves are often integrated into the fuel line design.
Check valves are an integral part of fluid systems, including fuel lines, as they provide a one-way barrier that allows fluid to flow in one direction while preventing backflow. In the context of fuel lines, these valves are strategically placed to ensure that fuel flows from the tank to the engine, preventing any potential contamination or damage caused by reverse flow. This is particularly important in high-pressure fuel systems, where the risk of backflow is higher due to the force of the fuel flow.
The design and placement of check valves in fuel lines are critical to their effectiveness. Typically, these valves are positioned near the engine, closer to the fuel pump, as this is where the pressure is highest. By locating the check valve in this area, it can effectively prevent backflow when the engine is running, ensuring that fuel is delivered efficiently and safely. Additionally, the valve's design should allow for easy maintenance and replacement, as fuel lines may require periodic inspection and service.
Incorporating check valves into fuel line design offers several advantages. Firstly, it enhances the overall reliability of the fuel system by reducing the likelihood of backflow-related issues. This is crucial for maintaining optimal engine performance and longevity. Secondly, it provides a layer of protection against potential contaminants that may be present in the fuel, especially in systems where fuel is stored for extended periods. Finally, the use of check valves can help prevent engine damage caused by fuel-related issues, such as pump failure or fuel system contamination.
In summary, check valves are a vital component in the design of fuel lines, serving as a critical safety measure to prevent backflow. Their strategic placement and design considerations ensure that fuel flows in the intended direction, protecting the engine and maintaining optimal performance. By integrating these valves into fuel line systems, engineers can enhance the reliability and longevity of the vehicle's fuel system, contributing to a safer and more efficient driving experience.
Unraveling the Mystery: Understanding Fuel Line Retaining Clips
You may want to see also
Fuel Pressure Regulation: Check valves help maintain optimal fuel pressure in the system
The role of a check valve in a fuel system is to ensure that fuel flows in the correct direction and prevents backflow, which is crucial for maintaining optimal fuel pressure. Fuel pressure is a critical factor in engine performance, and any disruption to this pressure can lead to reduced power, poor fuel efficiency, and even engine damage. Check valves are an essential component in the fuel line, especially in systems where fuel is under pressure.
In a fuel injection system, the fuel pump creates pressure to deliver fuel to the injectors. This pressure needs to be regulated to ensure it remains within a specific range for optimal engine operation. Check valves are strategically placed in the fuel lines to control the direction of fuel flow and prevent air from entering the system, a process known as 'vapor lock'. When the engine is running, the check valve opens to allow fuel to flow from the tank to the pump and then to the injectors. As the engine idles or stops, the check valve closes, preventing the fuel from flowing back into the tank and maintaining the required pressure.
These valves are typically made of durable materials like brass or stainless steel to withstand the corrosive nature of fuel and the pressure it exerts. They are designed with a spring-loaded mechanism that keeps the valve closed when the pressure is low, such as during engine start-up or when the vehicle is stationary. When the engine is running and the pressure increases, the spring is overcome, allowing the valve to open. This simple yet effective design ensures that the fuel system operates efficiently and safely.
The presence of check valves in the fuel line is vital for several reasons. Firstly, it prevents air from entering the fuel, which can lead to engine misfires and reduced performance. Secondly, it ensures that the fuel pump operates within its optimal pressure range, extending its lifespan. Additionally, check valves help maintain a consistent fuel pressure throughout the system, which is essential for precise fuel injection and combustion.
In summary, check valves play a critical role in fuel pressure regulation by controlling the direction of fuel flow and preventing backflow. They are designed to open and close based on the pressure in the system, ensuring that the fuel line operates efficiently and safely. Properly functioning check valves are essential for maintaining optimal engine performance and longevity.
Where to Find the Best Deals on Diesel Fuel Lines
You may want to see also
Engine Performance: Properly functioning check valves ensure efficient engine operation and fuel delivery
The concept of check valves in fuel lines is an essential aspect of engine performance and fuel delivery systems. These valves are designed to allow fuel to flow in one direction while preventing it from flowing back, ensuring a controlled and efficient process. When it comes to engine operation, the proper functioning of check valves plays a critical role in maintaining optimal performance.
In the context of fuel delivery, check valves are typically installed in the fuel lines to regulate the flow of fuel from the tank to the engine. The primary purpose is to prevent fuel from returning to the tank, especially when the engine is not running or during deceleration. This is crucial because fuel that flows backward can lead to several performance issues. For instance, it can cause fuel to accumulate in the lines, leading to potential blockages and reduced fuel pressure, which directly impacts the engine's ability to start and run efficiently.
When a check valve is functioning correctly, it ensures that the fuel flows in a single direction, from the fuel pump to the engine, and not the other way around. This unidirectional flow is vital for maintaining the required fuel pressure and ensuring that the engine receives the precise amount of fuel needed for efficient combustion. As a result, the engine operates optimally, delivering the desired power output and fuel economy.
Moreover, the presence of check valves in fuel lines contributes to the overall reliability and longevity of the engine. By preventing backflow, these valves minimize the risk of fuel degradation, which can occur when fuel is exposed to air for extended periods. This degradation can lead to reduced engine performance and potential damage over time. Therefore, ensuring that check valves are in good working condition is a simple yet effective way to maintain the health and efficiency of the engine.
In summary, check valves in fuel lines are not just a component but a critical element in the engine's performance and fuel delivery system. Their proper functioning ensures that fuel flows efficiently, preventing backflow and maintaining the required pressure for optimal engine operation. Regular inspection and maintenance of these valves can contribute to the overall reliability and longevity of the engine, making it a vital consideration for vehicle owners and mechanics alike.
Air in Fuel Line: Causes, Effects, and Solutions
You may want to see also
Safety Mechanisms: Check valves act as safety devices to prevent fuel leaks and potential hazards
Check valves are an essential component in fuel line systems, serving as a critical safety mechanism to prevent fuel leaks and potential hazards. These valves are designed to allow fuel to flow in one direction only, ensuring that it moves from the fuel tank to the engine and nowhere else. This unidirectional flow is crucial because it prevents fuel from flowing back into the tank, which could lead to dangerous situations.
The primary purpose of a check valve in a fuel line is to provide a fail-safe mechanism. In the event of a malfunction or damage to the fuel pump or engine, the check valve will close automatically, blocking the reverse flow of fuel. This immediate response helps to mitigate the risk of fuel spilling or leaking, which could ignite and cause a fire or explosion. For instance, if a fuel pump fails and starts to pump air instead of fuel, the check valve will close, preventing the air from entering the engine and causing potential damage.
In addition to preventing fuel leaks, check valves also contribute to the overall safety of the vehicle by ensuring that the fuel system operates efficiently. By allowing fuel to flow in one direction, these valves help maintain the necessary pressure and flow rate, ensuring that the engine receives the correct amount of fuel for optimal performance. This is particularly important in high-performance vehicles or those with advanced fuel injection systems, where precise fuel management is critical.
Furthermore, the use of check valves in fuel lines is a preventative measure that can save lives and property. Fuel is a highly flammable substance, and any leak or spillage can have severe consequences. Check valves provide an extra layer of protection, especially in older vehicles or those with known fuel system issues, where the risk of leaks is higher. They are a simple yet effective way to enhance the safety of a vehicle's fuel system.
In summary, check valves are a vital safety feature in fuel lines, designed to prevent fuel leaks and potential hazards. By ensuring unidirectional flow, these valves act as a fail-safe mechanism, protecting against fuel system malfunctions and potential disasters. Their presence is a critical aspect of vehicle safety, contributing to the overall reliability and performance of the fuel system.
Understanding the Cause: Why Tractors Experience Air in Fuel Lines
You may want to see also
Maintenance and Inspection: Regular inspection of check valves is crucial for fuel system longevity
The importance of regular maintenance and inspection of check valves in fuel systems cannot be overstated. These valves are critical components designed to prevent backflow and ensure the unidirectional flow of fuel, which is essential for optimal engine performance and longevity. Over time, check valves can experience wear and degradation, leading to potential issues that may go unnoticed until it's too late.
One of the primary reasons for regular inspection is to identify any signs of damage or malfunction early on. Check valves are susceptible to sediment buildup, corrosion, and mechanical wear. Sediment and debris can accumulate in the valve's housing, especially in systems with long fuel lines or those exposed to dirty fuel. This buildup can restrict the valve's movement, causing it to fail to close properly, which may result in fuel leakage and potential engine damage. Regular cleaning and inspection can help prevent such issues.
During an inspection, it's essential to check for any visible signs of damage, such as cracks, corrosion, or warping. These issues can compromise the valve's functionality and lead to fuel leaks, which are highly dangerous. Additionally, inspect the surrounding areas for any signs of fuel leakage, as even a small leak can have significant consequences over time. It is also recommended to check the valve's seat and disc for wear. The seat, which is the stationary part of the valve, should be smooth and free of any damage. If the seat is worn or damaged, it may not provide an effective seal, allowing fuel to flow in the wrong direction.
Another critical aspect of maintenance is ensuring that the check valve is properly lubricated. Adequate lubrication reduces friction and wear, ensuring smooth operation. Insufficient lubrication can lead to increased wear and potential failure. It is recommended to use the manufacturer's specified lubricant and reapply it as per the maintenance schedule.
In summary, regular inspection and maintenance of check valves are vital for the long-term health of fuel systems. By identifying and addressing potential issues early, such as sediment buildup, corrosion, or mechanical wear, you can prevent costly repairs and ensure the safe and efficient operation of your engine. It is a simple yet essential task that every vehicle owner should prioritize to maintain their fuel system's integrity.
Fixing a Broken Fuel Line: Lawn Mower Repair Tips
You may want to see also
Frequently asked questions
A check valve is an essential component in a fuel line system, designed to prevent fuel from flowing in the reverse direction. It ensures that fuel flows only in one direction, from the fuel tank to the engine, and not back towards the tank or any other part of the system.
The primary reason is to maintain the integrity of the fuel system. Without a check valve, fuel could potentially flow back into the tank when the engine is not running, leading to issues like fuel degradation, contamination, and even engine misfires.
Yes, check valves are commonly used in both gasoline and diesel fuel lines. They are typically installed in the line between the fuel pump and the engine, ensuring that the pump's operation is not hindered by back pressure and that fuel is delivered efficiently.
When the engine is running and fuel is being pumped, the check valve opens, allowing fuel to pass through. However, when the engine is turned off, the check valve closes due to a spring mechanism, preventing fuel from flowing back into the tank. This ensures that the fuel system remains pressurized and ready for the next engine start.
Yes, if you notice any of the following, it could indicate a faulty check valve: engine stalling or hesitation during operation, fuel odor in the cabin, reduced fuel efficiency, or visible signs of fuel leakage around the valve. Regular maintenance and inspections can help identify such issues early on.