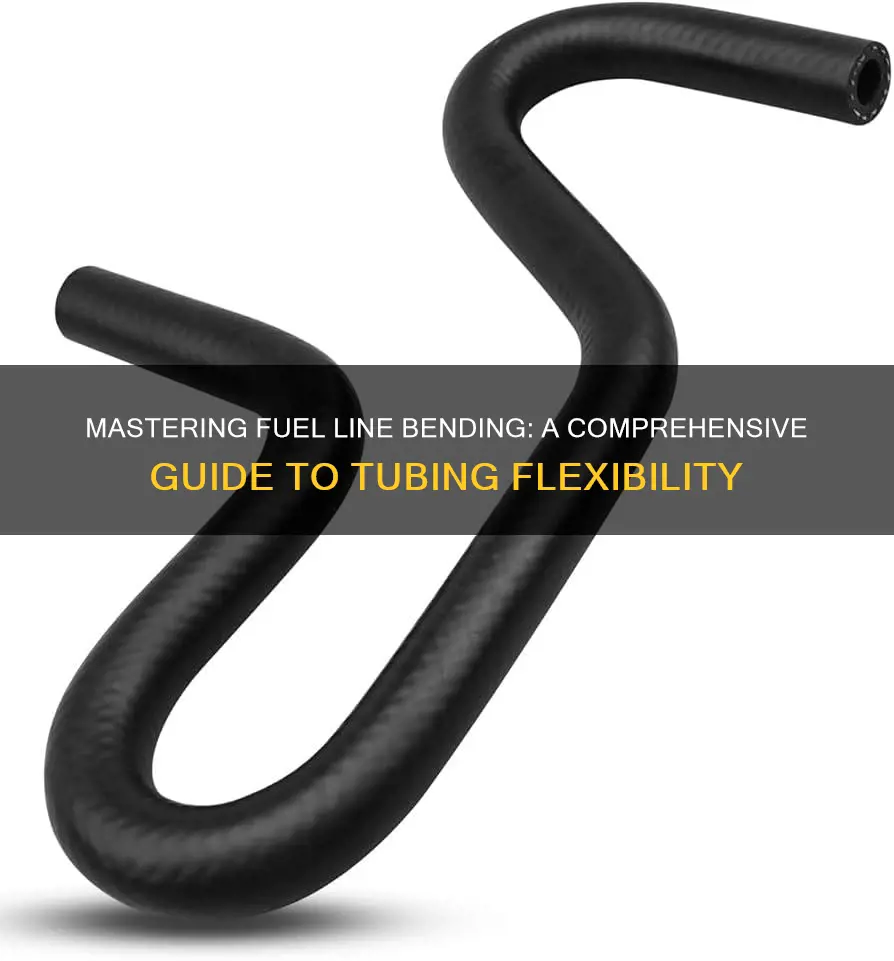
Bending fuel line tubing is a crucial skill for anyone working on fuel systems in vehicles. It requires precision and care to ensure a secure and leak-free connection. This guide will provide a step-by-step process to master the art of bending fuel line tubing, covering essential tools, safety precautions, and techniques to achieve a professional finish.
What You'll Learn
- Prepare the Materials: Gather fuel line tubing, fuel, and tools like a bending machine or a heat gun
- Measure and Mark: Accurately measure and mark the tubing length, ensuring precise bends at desired angles
- Heat and Bend: Apply heat to the tubing, then carefully bend it using a tool or a mandrel
- Trim and Connect: Trim excess tubing and connect it to fuel sources using appropriate fittings
- Test for Leaks: Inspect the bent tubing for any leaks, ensuring a secure and leak-free fuel line
Prepare the Materials: Gather fuel line tubing, fuel, and tools like a bending machine or a heat gun
To begin bending fuel line tubing, you'll need to gather the necessary materials and tools. Firstly, ensure you have the correct type of fuel line tubing suitable for your specific application. Different fuels may require different tubing materials, so check the specifications for your fuel type. Gather a length of tubing that is slightly longer than the desired final length to allow for any adjustments.
Next, collect the appropriate tools. A bending machine is ideal for precise and consistent bends, especially for larger tubing diameters. These machines can be adjusted to create various bend radii and angles. Alternatively, a heat gun can be used for smaller tubing or when a more flexible approach is required. The heat gun applies heat to the tubing, making it pliable and allowing for manual bending.
In addition to the tubing and tools, you'll need a source of fuel. This is essential for testing the bent tubing's functionality. Ensure you have a small amount of fuel ready, as you may need to make adjustments and repeat the bending process. It's a good practice to have a fuel pump or a small fuel container to facilitate the testing process.
When preparing your workspace, ensure it is well-ventilated and free from any potential hazards. Fuel line tubing should be handled with care to avoid any damage or contamination. Consider wearing protective gear, such as gloves and safety goggles, to ensure a safe working environment.
By gathering these materials and tools, you'll be well-prepared to start the process of bending fuel line tubing. Remember to follow safety guidelines and take your time to achieve the desired bends without causing any damage to the tubing or compromising its functionality.
Hydraulic Hose for Diesel Fuel: A Practical Guide
You may want to see also
Measure and Mark: Accurately measure and mark the tubing length, ensuring precise bends at desired angles
When it comes to bending fuel line tubing, accurate measurement and marking are crucial steps to ensure a successful and precise bend. This process requires careful attention to detail and a systematic approach to achieve the desired angles and curvature. Here's a step-by-step guide to help you master this technique:
Step 1: Measuring and Determining the Length: Begin by carefully measuring the length of the tubing that needs to be bent. Use a flexible measuring tape or a ruler to get an accurate reading. It's essential to measure twice to ensure precision, especially if you're working with a long piece of tubing. Mark the starting point of your bend, indicating the zero-degree bend, and then measure and mark the desired bend angle along the tubing's length. For example, if you need a 90-degree bend, measure and mark 90 degrees from the starting point.
Step 2: Marking the Bending Points: Once you have the measurements, it's time to mark the tubing. Use a permanent marker or a piece of chalk to create clear and visible marks. Ensure that the marks are aligned with the desired bend angles. For instance, if you're aiming for a series of small bends, mark multiple points along the tubing's length, ensuring they are evenly spaced and follow the intended curve. This step is critical as it provides a visual guide for the bending process.
Step 3: Precision and Angle Accuracy: When marking, pay close attention to the angle measurements. For sharp bends, you might need to make multiple small marks to guide the bending process. For larger angles, a single mark might suffice, but ensure it is precise. Consider using a protractor or a angle-measuring tool to verify the accuracy of your marks, especially for complex bends. The goal is to create a clear path for the tubing to follow during the bending process.
Step 4: Safety and Preparation: Before you start bending, ensure you have a well-ventilated workspace and wear appropriate safety gear, such as gloves and safety goggles. Fuel line tubing may contain hazardous substances, so proper protection is essential. Additionally, have the necessary tools ready, such as a tubing bender or a pair of pliers, depending on the bending technique you plan to use.
By following these steps, you can achieve precise bends in fuel line tubing, ensuring a professional and safe installation. Remember, accurate measurement and marking are fundamental to the success of any bending project, and this technique can be adapted for various tubing materials and applications.
Thawing Fuel Lines: Quick Fixes for Frozen Fuel Lines
You may want to see also
Heat and Bend: Apply heat to the tubing, then carefully bend it using a tool or a mandrel
To bend fuel line tubing, you'll need to apply heat to the material to make it more pliable. This process is crucial for achieving the desired shape without causing damage to the tubing. Start by heating the tubing using a heat gun or a torch. Hold the heat source a few inches away from the tubing and move it slowly along the length, ensuring an even distribution of heat. The goal is to raise the temperature of the tubing to a point where it becomes soft and pliable but not so hot that it becomes dangerous to handle. Allow the tubing to cool slightly after heating to prevent it from becoming too hot to touch.
Once the tubing is heated, it's time to bend it. You have two main options: using a tool or a mandrel. For the tool method, select a suitable bending tool, such as a tube bender or a pair of pliers with a curved jaw. Position the tubing at the desired bend point and apply gentle pressure with the tool, working the tubing around the curve. Take your time and apply consistent force to avoid kinking or damaging the tubing. For a more precise bend, especially for tight or complex curves, a mandrel can be used. A mandrel is a cylindrical tool that you insert into the tubing and then rotate while applying pressure. This method provides better control over the bend radius and ensures a more accurate and consistent bend.
When bending, always work with the tubing at a moderate temperature to maintain its flexibility. Avoid over-bending, as it can lead to permanent deformation or cracking. If you need to make multiple bends, repeat the heating and bending process for each bend point. Remember to cool the tubing slightly between bends to prevent overheating and maintain its structural integrity.
Practice and patience are key when learning to bend fuel line tubing. It may take a few attempts to get the hang of it, but with time, you'll develop the skill to create smooth and precise bends. Always prioritize safety by wearing protective gear, such as heat-resistant gloves, and ensure you are working in a well-ventilated area when using heat sources.
2010 Accord's Return Fuel Line: What You Need to Know
You may want to see also
Trim and Connect: Trim excess tubing and connect it to fuel sources using appropriate fittings
When working with fuel line tubing, it's essential to ensure a precise and secure connection to the fuel sources in your vehicle. The process of trimming and connecting the tubing involves several steps to guarantee a reliable and safe setup. Here's a detailed guide on how to achieve this:
Trimming the Tubing: Begin by carefully measuring the length of fuel line tubing required for your specific application. It's crucial to trim the tubing to the exact length needed to avoid any excess material that could cause unnecessary strain or interference. Use a sharp, clean pair of tubing cutters or a dedicated tubing trimmer to make a precise cut. Ensure that the cut ends are smooth and free of any burrs, as these can lead to leaks or damage during the connection process.
Preparing the Fittings: Select the appropriate fittings for your fuel line tubing, considering factors such as the type of fuel, pressure, and compatibility with your vehicle's system. Common fittings include compression fittings, quick-connect fittings, or barbed fittings, each with its own advantages. Clean the fittings thoroughly to remove any debris or contaminants. This step is vital to ensure a tight and leak-free connection.
Connecting the Tubing: Now, you can start the process of connecting the trimmed tubing to the fuel sources. If using compression fittings, insert the tubing into the fitting and tighten the nut securely, ensuring a firm grip. For quick-connect fittings, simply push the tubing onto the fitting until it clicks into place, forming a secure connection. When using barbed fittings, slide the tubing over the barbed end and secure it with a ferrule or clamp. Always follow the manufacturer's instructions for the specific fitting type you are using.
Testing for Leaks: After connecting the tubing to the fuel sources, it is crucial to test for any leaks. Turn on the fuel supply and inspect all connections for any signs of fuel escaping. Use a soapy water solution or a specialized leak detection kit to make this process easier. If any leaks are detected, tighten the fittings or re-seat the tubing to resolve the issue.
Final Adjustments: Once you've confirmed that all connections are leak-free, make any necessary adjustments to ensure a smooth and efficient flow of fuel. Check for any kinks or bends in the tubing that might restrict fuel flow and adjust accordingly. Properly securing the tubing with clamps or brackets can also prevent movement and potential disconnections.
Air in Fuel Line: Symptoms and Solutions
You may want to see also
Test for Leaks: Inspect the bent tubing for any leaks, ensuring a secure and leak-free fuel line
When bending fuel line tubing, it's crucial to ensure a secure and leak-free connection to prevent fuel leaks, which can be dangerous and costly. After bending the tubing, the next critical step is to thoroughly inspect it for any potential leaks. This process involves a systematic approach to guarantee the integrity of the fuel line.
Start by cleaning the tubing and the surrounding areas. Any dirt or debris can interfere with the inspection process and make it harder to identify leaks. Use a mild detergent and water solution to clean the tubing, ensuring you remove any contaminants. Rinse thoroughly to eliminate any soap residue.
Next, apply a small amount of diesel fuel or a suitable fuel line sealer to the bent tubing. This step is essential as it allows you to visually identify any leaks. The fuel will make any cracks or small holes visible, making it easier to pinpoint the issue. Ensure you apply the fuel evenly along the length of the tubing, covering all bends and connections.
Now, carefully inspect the tubing for any signs of leakage. Look for any discolored areas or small droplets of fuel around the bends and connections. Even a small leak can be a significant issue, so pay close attention to detail. If you notice any fuel accumulation, it indicates a potential leak, and you should investigate further.
In addition to visual inspection, you can use a fuel leak detector or a soapy water test to enhance your detection capabilities. Spray the tubing with the fuel leak detector or mix a solution of soap and water and apply it to the bent areas. Any bubbles or soapy residue will indicate a leak. This method can help you identify issues that might not be visible to the naked eye.
By following these steps, you can ensure that the bent fuel line tubing is secure and leak-free, minimizing the risk of fuel-related problems in your vehicle. It is a critical process that requires attention to detail and the right tools to guarantee a safe and efficient fuel system.
El Camino Fuel Line: Size Matters for Optimal Performance
You may want to see also
Frequently asked questions
When bending fuel line tubing, it's crucial to use a gentle and controlled approach. Start by securing the tubing in a vice or clamp to hold it firmly. Then, use a pair of pliers or a bending tool to apply pressure and create the desired bend. Take small, gradual steps to avoid putting excessive force, which can lead to cracking or damage.
While regular pliers can be used, it's not the most ideal tool for the job. Regular pliers may not provide the necessary grip and control required for bending fuel line tubing, especially if it's made of a flexible material. Consider using a pair of fuel line bending pliers or a specialized bending tool designed for this purpose.
To prevent kinks and sharp bends, it's essential to plan your bending process. Measure and mark the tubing at the desired bend points, ensuring the bends are smooth and gradual. Take your time and apply consistent pressure to create the bends. Avoid forcing the tubing, as it can lead to permanent deformation.
If you accidentally create a sharp bend, do not try to straighten it by force. Instead, carefully cut off the damaged section and replace it with a new piece of tubing. It's important to maintain the integrity of the fuel line to prevent leaks and ensure proper fuel flow.
Yes, the technique may vary depending on the angle you need to achieve. For small angles, you can use a combination of gentle pressure and rotation. For larger angles, consider using a bending tool with adjustable jaws to control the bend radius. Always work slowly and carefully to get the desired angle without distorting the tubing.