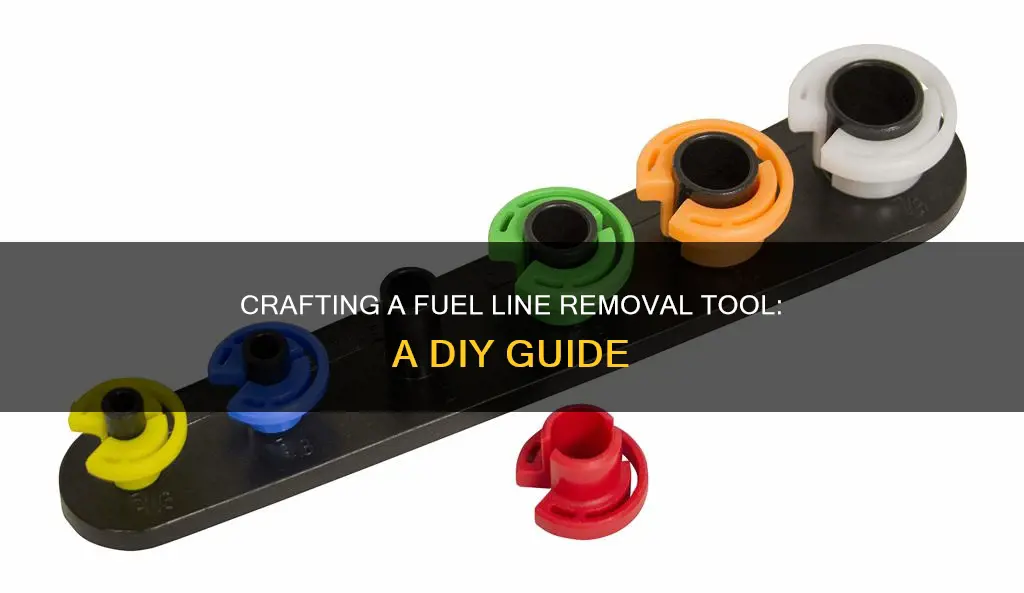
Creating a fuel line removal tool can be a useful project for mechanics and DIY enthusiasts alike. This tool is designed to make the process of disconnecting fuel lines from an engine or fuel tank easier and safer. The tool typically consists of a set of specialized pliers or a pair of adjustable spanners with a unique design that allows for a secure grip on the fuel line without damaging it. In this guide, we will explore the materials and steps required to build this handy tool, ensuring you have the knowledge to efficiently remove fuel lines for maintenance or repairs.
What You'll Learn
- Material Selection: Choose durable, flexible materials like rubber or metal
- Design Considerations: Ensure compatibility with fuel line sizes and vehicle types
- Manufacturing Process: Utilize injection molding or machining for precise tool creation
- Safety Features: Incorporate guards to prevent fuel spillage during removal
- Ergonomic Handle: Design a comfortable, non-slip handle for easy manipulation
Material Selection: Choose durable, flexible materials like rubber or metal
When designing a fuel line removal tool, material selection is a critical aspect that ensures the tool's durability, flexibility, and overall effectiveness. The primary goal is to create a tool that can withstand the challenges of removing fuel lines without causing damage or breaking under pressure. Here's a detailed guide on why and how to choose the right materials:
Durability and Strength: Fuel lines are often made of various materials, including rubber, plastic, and metal. When designing the removal tool, you need a material that can match or exceed the strength of these lines. Rubber, for instance, is a popular choice for fuel lines due to its flexibility and durability. When selecting rubber, opt for high-quality, reinforced varieties that can handle the pressure and temperature variations associated with fuel systems. Metal, such as steel or aluminum, is another excellent option for the tool's construction. These metals provide exceptional strength and can withstand the rigors of fuel line removal, ensuring a long-lasting tool.
Flexibility: Flexibility is key to a successful removal process. The tool should be able to conform to the shape of the fuel line and navigate through tight spaces without kinking or breaking. Rubber, being naturally flexible, is an ideal choice for this purpose. You can also consider using flexible metal alloys, such as bronze or brass, which offer a good balance between strength and flexibility. This flexibility will allow the tool to reach around corners and access hard-to-reach areas without causing damage to the fuel line.
Heat Resistance: Fuel systems often operate under high temperatures, so the chosen material should be able to withstand these conditions. Rubber compounds that include heat-resistant additives can be an excellent choice, ensuring the tool remains flexible and functional even in hot environments. For metal components, select materials with good heat resistance, such as stainless steel or heat-treated aluminum, to prevent melting or degradation.
Corrosion Resistance: Fuel lines are often exposed to corrosive substances, so the tool should be designed with materials that resist corrosion. Stainless steel, for example, is highly resistant to corrosion and can handle the harsh conditions of a fuel system. Rubber seals and gaskets should also be made from corrosion-resistant materials to ensure a long-lasting seal.
In summary, the material selection for a fuel line removal tool should prioritize durability, flexibility, heat resistance, and corrosion resistance. By choosing the right combination of rubber and metal, you can create a tool that effectively and safely removes fuel lines, ensuring a smooth and efficient process. This approach will also contribute to the overall longevity of the tool and its ability to handle various fuel line removal tasks.
Grand Prix: A Guide to Disconnecting Fuel Lines on a 99 Grand Prix
You may want to see also
Design Considerations: Ensure compatibility with fuel line sizes and vehicle types
When designing a fuel line removal tool, ensuring compatibility with various fuel line sizes and vehicle types is crucial for its effectiveness and versatility. This consideration is essential to accommodate the diverse range of fuel systems found in different vehicles, from compact cars to heavy-duty trucks. The tool should be designed with adjustable features or interchangeable components to cater to these variations.
One approach is to create a modular design, allowing users to customize the tool's dimensions and shape. This could involve incorporating adjustable sleeves or clamps that can be tailored to fit different fuel line diameters. By offering a range of interchangeable parts, the tool can be adapted to suit various fuel line sizes, ensuring a secure and efficient removal process. For instance, a set of different-sized sleeves could be provided, allowing users to select the appropriate one for their specific fuel line.
Additionally, considering the vehicle's make and model is vital. Different vehicle manufacturers may use distinct fuel system designs, requiring unique tool approaches. Researching and understanding the specific fuel line configurations of various vehicle types is essential. This knowledge will enable the design of specialized components that align with the vehicle's architecture, ensuring a precise fit and efficient removal process.
The tool's design should also account for the varying lengths and positions of fuel lines. Some vehicles may have longer fuel lines that require a more extended tool, while others might have fuel lines in tight or hard-to-reach areas. Creating a tool with adjustable length or flexible joints can accommodate these differences, providing users with the flexibility to navigate different vehicle fuel systems.
Furthermore, the material and construction of the tool play a significant role in its compatibility. Using durable and flexible materials that can withstand the pressure and heat associated with fuel systems is essential. The tool should be designed to prevent damage to the fuel lines during removal, ensuring a safe and efficient process.
Mastering the Art of Painting Rubber Fuel Line Hose
You may want to see also
Manufacturing Process: Utilize injection molding or machining for precise tool creation
The manufacturing process of a fuel line removal tool can be efficiently achieved through two primary methods: injection molding and machining. Each technique offers unique advantages and is chosen based on the specific requirements of the tool's design and production volume.
Injection Molding: This process is ideal for creating tools with intricate designs and precise dimensions. It involves injecting molten plastic into a mold, which then takes the shape of the tool. For a fuel line removal tool, injection molding can be advantageous as it allows for the production of complex shapes, including ergonomic handles and specialized gripping mechanisms. The tool's design can be optimized for comfort and efficiency, ensuring a secure grip on the fuel line without causing damage. The process begins with designing the mold, which requires detailed engineering to ensure the tool's functionality and durability. Once the mold is prepared, the plastic material is heated and injected, then cooled to solidify, resulting in a robust and accurate tool. This method is particularly useful for high-volume production, as it enables rapid manufacturing with consistent quality.
Machining: Machining is a more traditional approach, often employed when working with metal materials. It involves removing material from a solid block to create the desired tool shape. For a fuel line removal tool, machining can be utilized to craft a sturdy and durable instrument. The process typically starts with selecting an appropriate metal, such as steel or aluminum, and then using precision cutting tools to shape the material. Machining allows for tight tolerances and fine detailing, ensuring the tool fits the fuel line perfectly. This method is advantageous for tools requiring high strength and precision, as it provides excellent control over the final product's dimensions. However, machining may be more time-consuming and costly compared to injection molding, especially for large production runs.
The choice between injection molding and machining depends on various factors, including the tool's complexity, required production volume, and material preferences. Injection molding excels in rapid production and intricate designs, while machining offers precision and strength, making it suitable for specialized tools. Both methods can be employed individually or in combination to create a high-quality fuel line removal tool, catering to different industrial needs.
Torquing Stages: Mini Cooper Fuel Line Secrets Unveiled
You may want to see also
Safety Features: Incorporate guards to prevent fuel spillage during removal
When designing a fuel line removal tool, safety should be a top priority, especially when dealing with potentially hazardous fuel systems. One critical aspect to consider is implementing safety features to prevent fuel spillage during the removal process. Here's how you can achieve this:
Guard Design: Incorporate a protective guard around the fuel line connection points. This guard should be carefully crafted to fit the specific fuel line and engine configuration. The primary purpose is to create a barrier that prevents accidental contact with the fuel line during removal. Design the guard with a slight overhang to ensure it covers the entire connection area, including any threads or fittings. This simple yet effective measure can significantly reduce the risk of fuel leakage.
Sealed Connections: To further enhance safety, consider using sealed connections or quick-release mechanisms. These features allow for a secure attachment of the fuel line to the tool, minimizing the chances of fuel escaping during removal. Sealed connections can be achieved by using specialized fittings or adapters that create an airtight seal. Quick-release mechanisms, such as clips or latches, enable a swift and controlled detachment, reducing the time the fuel line is exposed and potentially vulnerable to spills.
Material Selection: Choose materials for your tool that are compatible with fuel and resistant to corrosion. This ensures that the tool itself doesn't contribute to fuel leakage or contamination. Common materials for such applications include stainless steel, aluminum alloys, or specialized plastics designed for fuel-handling. The tool's construction should also consider the fuel's temperature and pressure requirements to maintain integrity.
Visual Indicators: Implement visual cues or indicators to alert users to potential hazards. For instance, a color-coded system can be used to indicate different fuel line connections, making it easier to identify the correct attachment points. Additionally, consider adding a clear, visible warning label or sticker near the fuel line connection, reminding users of the potential for fuel spillage and the importance of handling the tool with care.
By incorporating these safety features, you create a robust and secure fuel line removal tool that prioritizes user safety and minimizes the risk of fuel-related incidents during maintenance or repair tasks. It is crucial to test and refine these designs to ensure they meet the required safety standards and provide a reliable solution for professionals working with fuel systems.
Perfect Fuel Line Size for 7kW Onan Generator
You may want to see also
Ergonomic Handle: Design a comfortable, non-slip handle for easy manipulation
The design of an ergonomic handle is crucial for the functionality and user-friendliness of a fuel line removal tool. This component directly impacts the user's experience and the tool's overall performance. Here's a detailed guide on creating a comfortable and non-slip handle:
Material Selection: Start by choosing a material that offers both comfort and durability. Opt for a high-quality rubber or a specialized grip compound. These materials provide a soft, tactile surface, reducing fatigue during prolonged use. Additionally, ensure the material has excellent grip properties to prevent slipping, especially when hands are wet or covered in grease. Consider materials like silicone or a rubber compound with a textured surface for enhanced grip.
Handle Shape and Size: The handle should be contoured to fit the user's hand naturally. Aim for a shape that mimics the hand's natural grip, allowing for a secure hold. A slightly curved or oval-shaped handle can provide a comfortable grip. The size should be proportional, ensuring it doesn't feel too bulky or too small in the user's hand. A balanced handle size promotes control and reduces strain on the hand and wrist.
Non-Slip Texture: To enhance grip further, incorporate a textured surface on the handle. This can be achieved through various methods such as molding, printing, or adding a layer of textured grip tape. The texture should be subtle enough to provide grip without being too aggressive, which might hinder the user's ability to manipulate the tool precisely. A smooth, slightly textured surface can offer the best of both worlds, ensuring comfort and control.
Ergonomic Considerations: Focus on the overall ergonomics of the handle. Ensure it aligns with the user's hand position and movement when using the tool. The handle should guide the user's hand in a natural, fluid motion, reducing the risk of strain or injury. Consider the angle and orientation of the handle relative to the tool's body to ensure a comfortable and efficient workflow.
Testing and Refinement: Once the handle design is finalized, conduct thorough user testing. Gather feedback on comfort, grip, and overall usability. This feedback will help identify any potential issues and allow for necessary adjustments. Refining the handle design based on user input ensures the tool meets the needs of the intended users, providing a comfortable and efficient experience.
Duramax Fuel Line Pressure: Testing and Troubleshooting Guide
You may want to see also
Frequently asked questions
The tool can be crafted from various materials, including steel, aluminum, or even specialized plastics designed for fuel line applications. The choice of material depends on factors like durability, flexibility, and the specific requirements of the fuel line system.
To achieve a firm grip, consider using a tool with textured surfaces or coatings. Some tools might feature rubberized handles or ergonomic designs that enhance traction. Additionally, applying slight pressure while turning the tool can help create friction and improve grip.
Yes, it's crucial to exercise caution. Use smooth, controlled movements when turning the tool to avoid excessive force. Some tools might have adjustable features or different attachment points to accommodate various fuel line sizes and shapes, reducing the risk of damage.