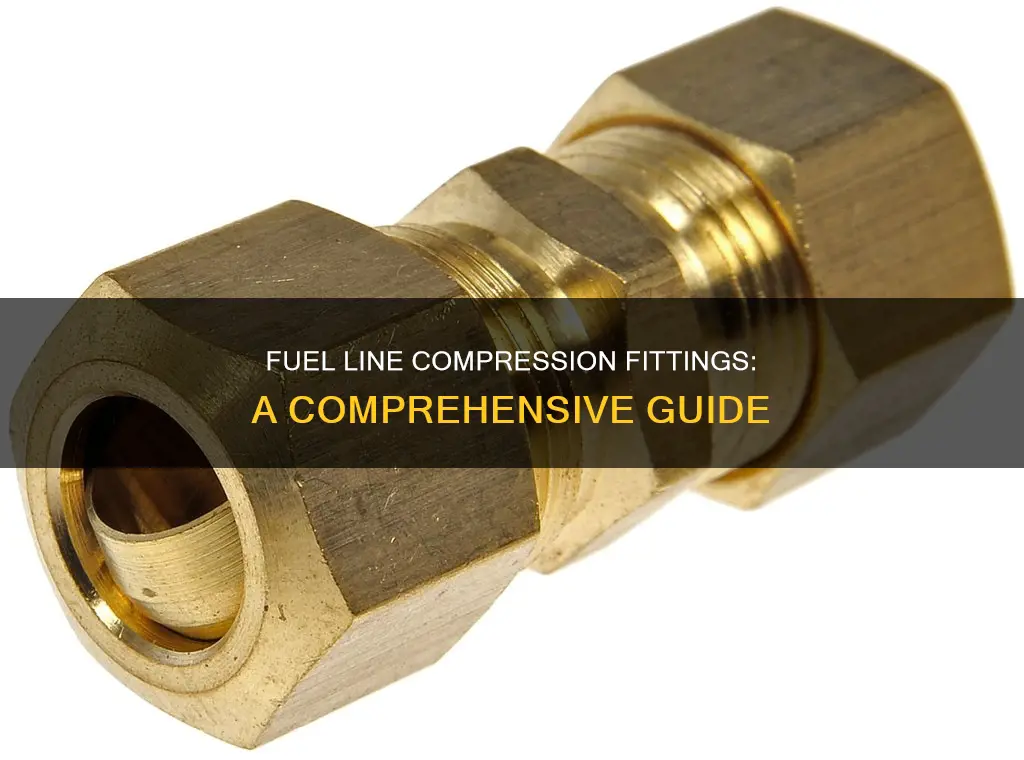
Compression fittings are an essential component in the construction and maintenance of fuel lines, ensuring a secure and leak-free connection. The question of whether compression fittings are available for fuel lines is a relevant one, as fuel systems require specialized components to handle the unique challenges of fuel transport and delivery. This paragraph aims to explore the availability and importance of compression fittings specifically designed for fuel lines, highlighting their role in ensuring the safety and efficiency of fuel systems.
Characteristics | Values |
---|---|
Availability | Yes, compression fittings for fuel lines are available in the market. |
Material | Common materials include stainless steel, brass, and aluminum. |
Compatibility | Designed to fit various fuel line sizes and types. |
Pressure Rating | Depending on the manufacturer, these fittings can handle different pressure levels, typically up to 300 psi. |
Temperature Range | They can withstand a wide temperature range, often from -40°F to 400°F. |
Ease of Installation | Compression fittings are generally easy to install using hand tools. |
Durability | Known for their durability and resistance to corrosion. |
Application | Suitable for fuel systems in vehicles, boats, and aircraft. |
Brand Availability | Brands like Gates, Flex-O-Pipe, and Fuel Line Solutions offer these fittings. |
Customization | Some manufacturers provide custom-made fittings for specific fuel line requirements. |
What You'll Learn
- Material Compatibility: Ensure the material of the compression fitting is compatible with fuel
- Pressure Rating: Check the fitting's pressure rating to handle fuel line pressures
- Size and Fit: Verify the fitting's size and thread compatibility with the fuel line
- Durability: Assess the fitting's durability to withstand fuel line conditions
- Safety Standards: Confirm the fitting meets industry safety standards for fuel systems
Material Compatibility: Ensure the material of the compression fitting is compatible with fuel
When it comes to fuel lines, choosing the right compression fitting is crucial for ensuring a safe and efficient system. One of the most important considerations is material compatibility, especially when dealing with fuel, which can vary in composition and properties. The material of the compression fitting must be carefully selected to withstand the specific challenges posed by the fuel it will be used with.
Fuel lines often carry volatile substances, and the fitting must be able to resist corrosion, oxidation, and other forms of degradation that could compromise its integrity. Common materials used for compression fittings include brass, stainless steel, and various plastics. However, not all materials are suitable for every type of fuel. For instance, some fuels may contain acidic components that can corrode certain metals, while others might have high-temperature requirements that demand specific materials.
To ensure compatibility, it is essential to consider the properties of the fuel in question. For example, if the fuel is a gasoline blend, the compression fitting should be made from a material that can withstand the fuel's volatility and resistance to corrosion. Stainless steel is often a good choice due to its inherent corrosion resistance and ability to handle a wide range of temperatures. On the other hand, if the fuel is a diesel, the fitting might need to be made from a material that can handle higher pressure and temperature, such as a specific grade of stainless steel or a high-performance plastic.
In some cases, the fuel line system may require a combination of materials to ensure optimal performance and longevity. For instance, a brass compression fitting might be used for its cost-effectiveness and ease of installation, while a stainless steel adapter is employed to connect it to a fuel line made of a different material. This approach requires careful consideration of the compatibility between the various materials to avoid any adverse effects on the fuel's properties or the overall system performance.
In summary, when selecting a compression fitting for a fuel line, material compatibility is a critical factor. It is essential to research and choose materials that can withstand the specific challenges posed by the fuel, including its chemical composition, temperature requirements, and pressure levels. By ensuring proper material compatibility, you can guarantee a reliable and safe fuel system.
Where to Find Red Kote Fuel Tank Liners: Your Ultimate Guide
You may want to see also
Pressure Rating: Check the fitting's pressure rating to handle fuel line pressures
When considering fuel line fittings, it's crucial to prioritize safety and performance. One critical aspect to evaluate is the pressure rating of these fittings. Fuel lines can operate under varying pressures, and using fittings with an appropriate pressure rating is essential to ensure the system's integrity and prevent potential failures.
The pressure rating of a fitting indicates the maximum pressure it can withstand without compromising its structural integrity. Fuel lines, especially in high-performance vehicles or those with modified engines, can experience significant pressure. Therefore, it's imperative to select fittings that can handle these pressures to avoid leaks, damage, or even catastrophic failures.
To determine the correct pressure rating, you should consult the manufacturer's specifications or technical data sheets for the fuel line fittings. These resources will provide detailed information about the pressure range each fitting is designed to manage. It's important to match the pressure rating of the fitting to or exceed the expected pressure in your fuel line system. For instance, if your fuel line operates at a pressure of 50 psi, the fittings should have a minimum pressure rating of 50 psi or higher.
Additionally, consider the type of fuel being used. Different fuels may have varying pressure requirements. For example, ethanol-blended fuels might require higher pressure ratings compared to conventional gasoline. Understanding the specific fuel characteristics and their impact on pressure is vital for selecting the right fittings.
In summary, when installing or replacing fuel line fittings, always check and verify the pressure rating. This ensures that the fittings can withstand the pressures generated by your fuel system, promoting safety and optimal performance. It is a simple yet critical step in maintaining a reliable and efficient fuel delivery system.
Fuel Tank Linings: Protecting Your Car's Vital Fluid Storage
You may want to see also
Size and Fit: Verify the fitting's size and thread compatibility with the fuel line
When it comes to fuel lines, ensuring a proper fit is crucial for safe and efficient operation. Compression fittings are indeed available for fuel lines, offering a secure and reliable connection. However, it's essential to pay close attention to the size and thread compatibility to ensure a perfect match.
The first step is to identify the fuel line's internal diameter and the corresponding fitting's outer diameter. Fuel lines typically have a specific diameter, and the compression fitting should match this dimension precisely. For example, if your fuel line has a 0.5-inch inner diameter, you need a compression fitting with an outer diameter of 0.5 inches to ensure a snug fit. Measuring or referring to the manufacturer's specifications is vital here.
Thread compatibility is another critical aspect. Fuel lines often feature either metric or imperial threads, and the compression fitting must match this thread type. Metric threads are commonly used in European vehicles, while imperial threads are standard in North American and some Asian markets. Misaligning the threads can lead to leaks or damage, so double-check the thread pitch and diameter to ensure compatibility.
To verify the size and fit, you can use a thread gauge or a caliper to measure the fuel line and the compression fitting. This process ensures that the fitting's outer diameter matches the line's inner diameter and that the threads are aligned correctly. Additionally, consider the length of the fitting; it should be sufficient to create a secure seal without protruding into the fuel line or causing damage.
In summary, when sourcing compression fittings for fuel lines, meticulous attention to size and thread compatibility is essential. By carefully measuring and comparing the fuel line's specifications to the fitting's dimensions, you can ensure a secure and leak-free connection, promoting the safe and efficient operation of your vehicle's fuel system. Always refer to the manufacturer's guidelines or seek professional advice for specific vehicle requirements.
Finding the Perfect Fuel Line for Your 1993 Toyota 4Runner
You may want to see also
Durability: Assess the fitting's durability to withstand fuel line conditions
When considering the use of compression fittings for fuel lines, it's crucial to evaluate their durability to ensure they can withstand the demanding conditions of fuel systems. Fuel lines operate in environments with varying temperatures, pressure fluctuations, and exposure to corrosive substances, making the choice of fittings critical for long-term reliability.
Compression fittings, designed to secure fuel lines to components like fuel tanks and engines, rely on a tight seal created by compressing the fitting onto the fuel line. While this design provides a secure connection, it also means that the fitting must be robust enough to handle the constant expansion and contraction caused by temperature changes. Over time, weaker fittings may degrade, leading to leaks or even failure, which could result in fuel leaks, engine misfires, or even fire hazards.
To assess durability, look for fittings made from high-quality materials that offer excellent resistance to corrosion and wear. Common materials include brass, stainless steel, and aluminum alloys. These materials are chosen for their ability to maintain structural integrity under the harsh conditions found in fuel systems. For instance, stainless steel is highly resistant to corrosion and can withstand extreme temperatures, making it an ideal choice for fuel line fittings.
Additionally, consider the design of the fitting. Compression fittings with robust, reinforced bodies and secure locking mechanisms are more likely to provide long-lasting performance. These designs ensure that the fitting remains tight and secure, even when subjected to vibrations and temperature changes. It's also important to check for any signs of weakness or brittleness in the material, especially in areas where stress concentrations are high.
In summary, when selecting compression fittings for fuel lines, prioritize those made from durable materials and featuring robust designs. This ensures that the fittings can effectively manage the challenges posed by fuel line conditions, providing a reliable and safe connection throughout the vehicle's lifetime. By carefully considering these factors, you can make an informed decision that contributes to the overall reliability of the fuel system.
Quick Fix: Temporary Solutions for Leaky Fuel Lines
You may want to see also
Safety Standards: Confirm the fitting meets industry safety standards for fuel systems
When it comes to fuel lines, ensuring the safety and reliability of the system is paramount. One crucial aspect of achieving this is the use of appropriate compression fittings. These fittings are designed to securely connect fuel lines, preventing leaks and potential hazards. By understanding and adhering to industry safety standards, you can ensure that your fuel system operates efficiently and safely.
Industry standards for fuel systems are stringent and essential to follow. These standards are in place to minimize the risk of fuel-related accidents and ensure the longevity of the vehicle's fuel system. One of the key considerations is the material and design of the compression fittings. Fittings should be made from high-quality materials that can withstand the corrosive nature of fuel and the pressure it exerts. Common materials used include stainless steel and brass, which offer excellent durability and resistance to corrosion. The design should also incorporate features such as a robust sealing mechanism to ensure a tight and secure connection.
Safety standards often require compression fittings to meet specific performance criteria. These criteria may include pressure ratings, temperature tolerances, and the ability to withstand vibration and movement over time. For instance, the fitting should be able to handle the pressure differentials associated with fuel injection systems without compromising its integrity. Additionally, the fittings should be designed to prevent fuel leakage, as even a small leak can lead to dangerous situations, especially in enclosed spaces.
To confirm compliance with safety standards, it is essential to look for certifications and approvals from recognized testing laboratories. These certifications provide assurance that the compression fittings have undergone rigorous testing and meet the required performance standards. Look for markings or labels indicating industry-recognized standards, such as those set by the Society of Automotive Engineers (SAE) or the International Organization for Standardization (ISO). These certifications will help you verify that the fittings are safe and reliable for your fuel system.
In summary, when dealing with fuel lines, prioritizing safety is non-negotiable. Compression fittings play a critical role in achieving this, and their selection should be guided by industry safety standards. By choosing fittings made from suitable materials, considering their design, and ensuring compliance with performance criteria, you can create a robust and secure fuel system. Always refer to manufacturer guidelines and industry resources to make informed decisions, ensuring the safety and efficiency of your vehicle's fuel system.
Can Fuel Line Returns Use Plastic T-Fittings? Expert Insights Revealed
You may want to see also
Frequently asked questions
Compression fittings are used to securely connect fuel lines to fuel tanks, pumps, and other components in a vehicle's fuel system. They provide a tight seal to prevent fuel leaks and ensure efficient fuel transfer.
Yes, compression fittings are designed to be compatible with various types of fuel lines, including rubber, vinyl, and plastic lines. However, it's important to choose the correct size and type of fitting for the specific fuel line material and diameter.
Installation involves cleaning the fuel line and fitting, inserting the fitting over the fuel line, and then compressing the fitting onto the line using a tool. It's crucial to follow manufacturer instructions and ensure a proper seal to avoid fuel leaks.
Yes, compression fittings are commonly used in high-pressure fuel systems. They are designed to withstand the pressure and provide a reliable seal, ensuring safe and efficient fuel delivery to the engine.
Yes, compression fittings can be reused if they are properly maintained and installed. Regular inspection and tightening can ensure their longevity and prevent fuel leaks over time. Proper care will extend the lifespan of the fittings and the overall fuel system.