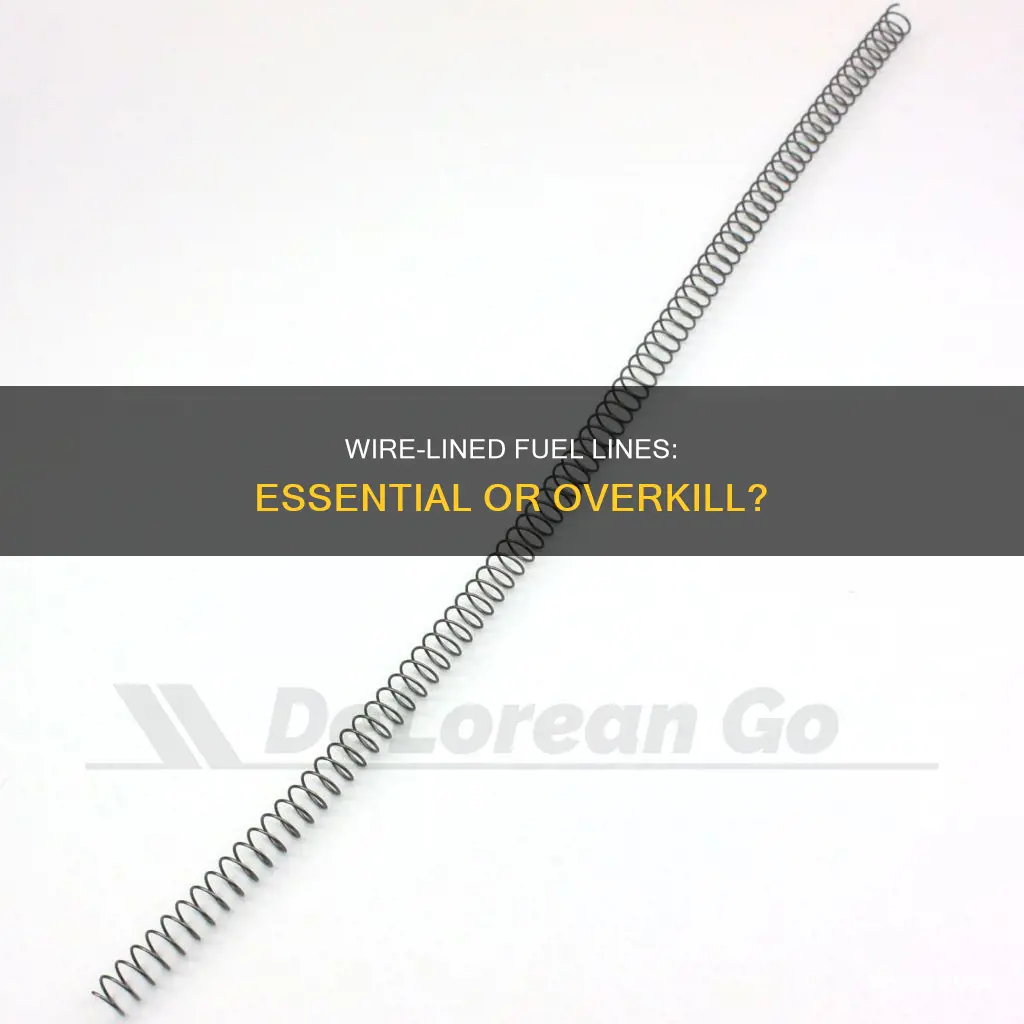
When it comes to fuel lines, many car enthusiasts and DIYers often wonder if wire-lined fuel lines are necessary. These fuel lines are designed with a braided wire layer, which is intended to provide additional protection against damage from road debris and other potential hazards. In this paragraph, we will explore the benefits and considerations of using wire-lined fuel lines, helping you decide if they are a worthwhile investment for your vehicle.
What You'll Learn
- Material Comparison: Compare metal-lined vs. rubber fuel lines for durability
- Performance Considerations: Evaluate fuel line material for engine power and efficiency
- Environmental Factors: Assess fuel line resistance to heat, cold, and chemicals
- Safety Standards: Ensure fuel lines meet industry standards for fuel containment
- Cost-Benefit Analysis: Weigh the cost of wire-lined lines against potential performance gains
Material Comparison: Compare metal-lined vs. rubber fuel lines for durability
When it comes to choosing the right fuel lines for your vehicle, understanding the differences between metal-lined and rubber fuel lines is crucial for ensuring optimal performance and longevity. Both types of fuel lines have their unique advantages and are chosen based on specific requirements and conditions. Let's delve into a material comparison to highlight the durability aspects of these two options.
Metal-Lined Fuel Lines:
Metal-lined fuel lines, often made of steel or aluminum, offer exceptional durability and strength. The metal lining provides excellent resistance to fuel contamination and degradation. Over time, fuel can break down and become more corrosive, especially in older vehicles with less refined fuel systems. Metal-lined lines effectively prevent this by acting as a barrier, ensuring that the fuel remains pure and does not come into contact with the inner walls of the line. This is particularly important in high-performance vehicles or those with modified engines, where fuel quality and stability are critical. The metal construction also makes these lines highly resistant to abrasion and impact, making them ideal for rugged environments or vehicles with rough terrain.
Rubber Fuel Lines:
Rubber fuel lines, on the other hand, are known for their flexibility and ease of installation. They are typically used in situations where a more flexible approach is required, such as in classic cars or vehicles with limited space under the hood. Rubber is naturally resistant to fuel degradation, which is a significant advantage in preventing fuel-related issues. However, rubber's durability can vary depending on the quality of the material and the manufacturing process. Lower-grade rubber may become brittle over time, especially in extreme temperatures, leading to potential cracks and fuel leaks. Despite this, modern rubber fuel lines are often reinforced with materials like steel or braided fibers to enhance their strength and flexibility, making them a reliable choice for many applications.
Durability and Longevity:
The key difference in durability lies in the material's ability to withstand fuel-related challenges. Metal-lined fuel lines excel in this regard due to their inherent resistance to fuel contamination and their robust construction. They are less prone to deterioration and are more likely to maintain their structural integrity over an extended period. Rubber fuel lines, while flexible, may require more frequent replacements, especially in harsh conditions or high-temperature environments. However, with advancements in rubber technology, modern rubber lines can offer improved durability, making them a viable option for various vehicle types.
In summary, the choice between metal-lined and rubber fuel lines depends on the specific needs of your vehicle and the conditions it operates in. Metal-lined lines provide superior durability and fuel protection, making them ideal for high-performance or modified vehicles. Rubber lines, with their flexibility and resistance to fuel degradation, are suitable for classic cars or applications where space is limited. Understanding these material differences will help you make an informed decision to ensure your fuel system remains reliable and efficient.
Can Diesel Fuel Lines Freeze? Winter Fuel Line Tips
You may want to see also
Performance Considerations: Evaluate fuel line material for engine power and efficiency
When it comes to optimizing engine performance and efficiency, the choice of fuel line material is a critical factor that often goes overlooked. The fuel lines in your engine are responsible for transporting fuel from the tank to the injectors or carburetor, and the material they are made of can significantly impact power output and overall engine efficiency. Here's a detailed look at how to evaluate fuel line materials for performance considerations:
Material Properties and Engine Performance:
The performance of your engine is directly related to the quality and properties of the fuel it receives. Fuel lines should be designed to ensure that the fuel is delivered at the right pressure and temperature, and with minimal degradation. Different materials have varying effects on fuel flow characteristics:
- Flexibility and Durability: Fuel lines need to be flexible to accommodate engine movement during operation. Materials like rubber or high-quality synthetic compounds offer excellent flexibility, ensuring that the fuel lines can bend and twist without restricting flow. This flexibility is crucial for maintaining consistent fuel delivery, especially in high-performance engines that experience rapid acceleration and deceleration.
- Heat Resistance: Engine compartments can get extremely hot, and fuel lines should be able to withstand these temperatures without compromising fuel quality. Materials like stainless steel or specialized polymers with heat-resistant properties are ideal for maintaining fuel stability and preventing degradation, which can lead to reduced power and efficiency.
- Chemical Compatibility: The fuel line material must be compatible with the type of fuel it carries. For example, ethanol-blended fuels require materials that can withstand the higher alcohol content without leaching or corrosion. Using the wrong material can result in fuel contamination, leading to engine issues and reduced performance.
Impact on Engine Efficiency:
The choice of fuel line material can have a direct impact on engine efficiency:
- Flow Rate and Pressure: High-performance engines require precise fuel injection to optimize power output. Fuel lines made from materials with low-pressure drop characteristics ensure that fuel is delivered at the required pressure, allowing for efficient combustion. This results in improved power and torque while maintaining better fuel economy.
- Avoiding Fuel Degradation: Certain materials can cause fuel degradation over time, leading to reduced performance. For instance, rubber fuel lines may absorb fuel additives, affecting the fuel's chemical properties. Choosing materials that minimize fuel interaction, such as braided stainless steel or specialized fuel-resistant polymers, ensures that the fuel remains stable, resulting in consistent engine performance.
- Vibration and Noise: Engine vibrations can affect fuel line integrity, especially in high-performance applications. Materials that provide excellent vibration damping, such as those with a flexible core and a protective outer layer, help maintain fuel line integrity, preventing leaks and ensuring a steady fuel supply.
When evaluating fuel line materials, consider the specific requirements of your engine, including its power output, fuel type, and operating conditions. Consulting with engine manufacturers or fuel system experts can provide valuable insights into the best materials for your application. Remember, the right fuel line material choice can contribute to a more responsive, efficient, and powerful engine.
Poulan PP3516AVX Fuel Line Length: Expert Guide
You may want to see also
Environmental Factors: Assess fuel line resistance to heat, cold, and chemicals
When considering the environmental factors that affect fuel lines, it's crucial to evaluate their resistance to heat, cold, and chemicals. These factors can significantly impact the performance and longevity of the fuel lines, especially in various automotive and industrial applications. Here's a detailed breakdown of how to assess these aspects:
Heat Resistance: Fuel lines are often exposed to high temperatures, especially in engines and industrial settings. To assess heat resistance, you should consider the operating temperature range of the fuel lines. Different materials have varying tolerances to heat. For instance, rubber fuel lines might degrade at higher temperatures, leading to cracks or leaks. In contrast, some synthetic materials, like silicone or EPDM (Ethylene Propylene Diene Monomer), offer better heat resistance, making them suitable for high-temperature environments. It's essential to choose fuel lines with a temperature rating that exceeds the expected operating temperature to ensure long-term reliability.
Cold Resistance: Extreme cold temperatures can also pose challenges for fuel lines. When fuel lines are exposed to freezing temperatures, they may become brittle and prone to cracking. Assessing cold resistance involves understanding the material's flexibility and ability to withstand temperature fluctuations. Materials like nylon or braided steel-reinforced rubber offer better cold resistance, ensuring the fuel lines remain flexible and intact even in sub-zero conditions. This is particularly important in regions with harsh winters or for applications where temperature variations are significant.
Chemical Resistance: Fuel lines must be resistant to various chemicals present in fuels, such as ethanol, methanol, and additives. Different materials have varying levels of chemical resistance. For example, natural rubber is susceptible to degradation by certain chemicals, while materials like fluoropolymers (PTFE or FEP) and certain types of rubber compounds offer excellent chemical resistance. Assessing chemical resistance is vital to ensure that the fuel lines do not leach harmful substances into the fuel, potentially causing engine issues or environmental concerns.
In summary, when evaluating fuel lines, it is essential to consider their resistance to heat, cold, and chemicals. By selecting materials that can withstand the specific environmental conditions of your application, you can ensure the longevity and reliability of the fuel lines. This assessment is particularly critical for applications where fuel lines are exposed to extreme temperatures or harsh chemicals, as it directly impacts the overall performance and safety of the system.
Fuel Line Placement: Carb Dirtbike Guide
You may want to see also
Safety Standards: Ensure fuel lines meet industry standards for fuel containment
When it comes to fuel containment and safety, adhering to industry standards is paramount. Fuel lines play a critical role in delivering fuel from the tank to the engine, and their integrity is essential to prevent fuel leaks and potential hazards. Industry standards, such as those set by the Society of Automotive Engineers (SAE) and the American Petroleum Institute (API), provide guidelines for the design, installation, and maintenance of fuel lines to ensure they meet the required safety criteria. These standards are in place to minimize the risk of fuel-related accidents and environmental damage.
One key aspect of meeting these safety standards is the use of appropriate materials for fuel lines. The choice of material is crucial as it directly impacts the line's ability to withstand various environmental factors and potential corrosion. Wire-lined fuel lines, for instance, are designed to reinforce the fuel line's structure and provide additional protection against damage. This reinforcement is particularly important in high-pressure fuel systems, where the fuel lines are more susceptible to wear and tear. By incorporating a wire-lining, manufacturers can ensure that the fuel lines remain intact and functional over the long term, reducing the likelihood of fuel leaks and potential engine failures.
Industry standards also dictate the installation process to ensure fuel lines are secure and properly routed. Proper installation is critical to prevent any compromise in the line's integrity. This includes using the correct fittings, clamps, and fasteners to ensure a tight and leak-free connection. Additionally, the fuel lines should be routed away from heat sources, sharp edges, and potential impact areas to avoid damage. Adhering to these installation guidelines is essential to maintain the safety and reliability of the fuel system.
Regular maintenance and inspections are another vital component of meeting safety standards. Over time, fuel lines can degrade due to factors like fuel quality, temperature fluctuations, and mechanical stress. Regular checks can help identify any signs of wear, corrosion, or damage, allowing for prompt repairs or replacements. This proactive approach ensures that the fuel lines continue to meet the required safety standards and minimize the risk of unexpected failures.
In summary, ensuring fuel lines meet industry standards for fuel containment is a critical aspect of vehicle safety. By using appropriate materials, such as wire-lined fuel lines, and following installation and maintenance guidelines, vehicle owners can significantly reduce the risk of fuel-related accidents and engine damage. Adherence to these standards is essential for maintaining a safe and reliable fuel system, ultimately contributing to the overall safety of the vehicle and its occupants.
Understanding Fuel Line Sizes for Tahoe Ti 9000 Lxu Models
You may want to see also
Cost-Benefit Analysis: Weigh the cost of wire-lined lines against potential performance gains
The decision to install wire-lined fuel lines in your vehicle is a significant one, and it often comes down to a careful cost-benefit analysis. While wire-lined fuel lines have gained popularity for their potential performance enhancements, they come with a price tag that needs to be evaluated against the expected gains. Here's a detailed breakdown to help you make an informed choice:
Performance Benefits:
Wire-lined fuel lines, also known as braided or steel-braided lines, are designed to improve fuel delivery efficiency. The primary advantage is reduced fuel pressure drop, especially at high engine speeds. This can lead to better throttle response, improved power delivery, and potentially higher horsepower output. For enthusiasts seeking maximum performance, this can be a compelling argument. Additionally, the braided design can help prevent fuel leaks and ensure a consistent fuel supply, which is crucial for optimal engine operation.
Cost Considerations:
The initial investment for wire-lined fuel lines can vary depending on the make and model of your vehicle. These lines are often more expensive than traditional rubber or silicone hoses. The cost may range from a few hundred to over a thousand dollars, depending on the complexity of the installation and the brand. Furthermore, the installation process can be more intricate, requiring specialized tools and knowledge, which may add to the overall expense.
Long-Term Value:
When evaluating the cost-benefit ratio, consider the long-term value. Wire-lined fuel lines can potentially increase the longevity of your engine by ensuring a consistent and efficient fuel supply. This can lead to reduced engine wear and tear, resulting in lower maintenance costs over time. Moreover, the performance gains might make your vehicle more responsive and enjoyable to drive, potentially increasing its resale value.
Weighing the Options:
- If you're a performance enthusiast aiming for maximum power and responsiveness, the investment in wire-lined fuel lines could be justified.
- For everyday drivers seeking a subtle improvement in acceleration, the benefits might be less critical, and the cost could be a deterrent.
- Consider your budget, the specific needs of your vehicle, and the potential performance gains to make an informed decision.
In summary, while wire-lined fuel lines offer performance advantages, the decision to install them should be based on a comprehensive cost-benefit analysis, taking into account both the immediate and long-term financial implications.
Vacuum Line Fuel Spill: Causes and Solutions
You may want to see also
Frequently asked questions
Wire-lined fuel lines, also known as braided fuel lines, are designed to provide a more flexible and durable solution for fuel delivery systems. The wire reinforcement helps to prevent fuel leaks, reduce vibration-induced damage, and improve overall fuel system longevity.
The need for wire-lined fuel lines depends on various factors, including your vehicle's age, fuel system design, and operating conditions. For older vehicles or those with high-performance engines, wire-lined fuel lines can be beneficial to ensure reliable fuel delivery and prevent potential issues. However, for newer vehicles with modern fuel systems, standard fuel lines might be sufficient, but it's always a good idea to consult your vehicle's manual or a professional mechanic for specific recommendations.
While it is possible to install wire-lined fuel lines yourself, especially if you have experience with automotive repairs, it is generally recommended to seek professional assistance. Fuel line installation requires precision and knowledge of the vehicle's fuel system to ensure proper connections and avoidance of any potential leaks. A qualified mechanic can also provide guidance on the best type of fuel lines for your specific vehicle, ensuring optimal performance and safety.