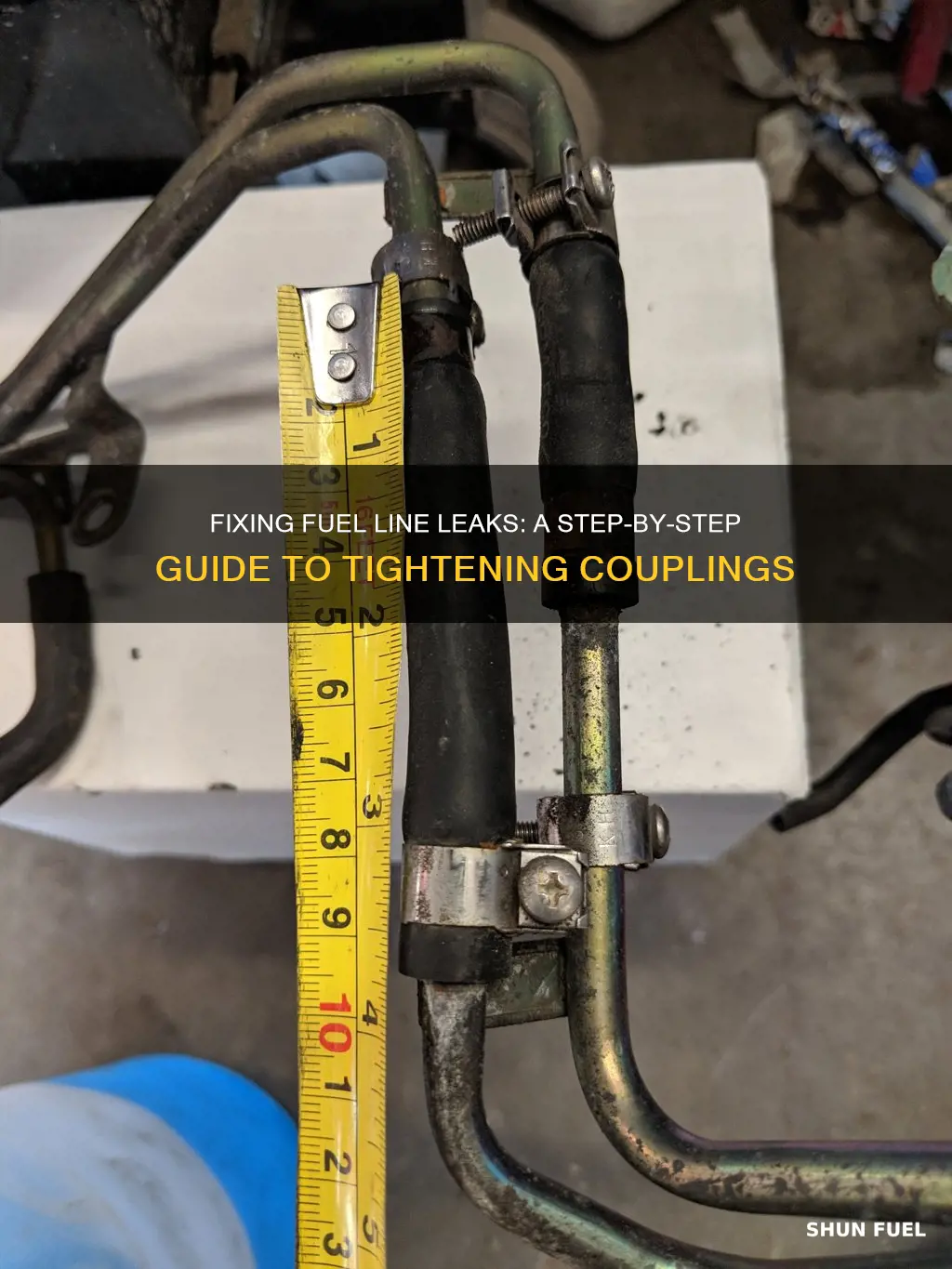
Fixing a leaky fuel line coupling can be a straightforward process if you follow the right steps. Start by identifying the source of the leak, which could be due to worn-out gaskets, damaged fittings, or corrosion. Gather the necessary tools and materials, including a fuel line coupling kit, a wrench, and a cleaning agent. Ensure you shut off the fuel supply and drain any residual fuel from the system before beginning the repair. Carefully remove the old coupling and clean the surfaces, then apply a suitable sealant or adhesive to the new coupling. Reinstall the coupling securely, ensuring all components are properly aligned and tightened. Finally, test the system for leaks and make any necessary adjustments to ensure a tight and reliable connection.
What You'll Learn
- Identify the leak: Inspect the fuel line coupling for damage or corrosion
- Clean and lubricate: Apply a suitable lubricant to the coupling and surrounding areas
- Tighten connections: Secure the coupling with appropriate fasteners to ensure a tight seal
- Replace worn parts: If the coupling is damaged, consider replacing it with a new one
- Test and verify: After repairs, test the fuel system to ensure no further leaks
Identify the leak: Inspect the fuel line coupling for damage or corrosion
When dealing with a leaky fuel line coupling, the first step is to carefully inspect the coupling for any signs of damage or corrosion. This initial assessment is crucial as it helps pinpoint the exact cause of the leak and guides the subsequent repair process. Start by visually examining the coupling for any visible damage. Look for cracks, frayed or exposed wires, or any other physical imperfections. These issues could be the result of age, wear and tear, or previous repair attempts. Pay close attention to the connection points where the fuel line and coupling meet, as these areas are prone to developing leaks over time.
Corrosion is another common culprit for fuel line leaks. Check for any signs of rust or oxidation around the coupling and the fuel line. Corroded surfaces can create a weak bond, leading to leaks. If you notice any corrosion, it's essential to clean and treat the affected areas to ensure a proper repair. Use a wire brush or a specialized corrosion remover to carefully remove the corrosion without damaging the underlying material. Once the inspection is complete, assess the severity of the damage. Minor issues, such as small cracks or minor corrosion, might be repairable with simple fixes. However, if the damage is extensive or the coupling appears severely compromised, it may require replacement.
During this inspection, it's also a good idea to check the surrounding area for any signs of fuel leakage. Even a small leak can indicate a more significant issue. If you detect any fuel residue or notice a strong smell of gasoline, it's crucial to address the problem promptly to prevent potential hazards. Remember, a thorough inspection at this stage can save you from more complex and costly repairs down the line. If you're unsure about the extent of the damage or the best course of action, it's always advisable to consult a professional mechanic who can provide expert guidance and ensure a safe and effective repair.
Understanding the Perfect Fuel Line Size for Snapper Lawb Mowers
You may want to see also
Clean and lubricate: Apply a suitable lubricant to the coupling and surrounding areas
When dealing with a leaky fuel line coupling, one of the most effective and straightforward solutions is to clean and lubricate the affected area. This process involves removing any dirt, debris, or corrosion that might be present and then applying a suitable lubricant to ensure a tight and secure connection. Here's a step-by-step guide to help you through this process:
Step 1: Cleaning the Coupling and Surrounding Areas
Start by disconnecting the fuel line from the coupling. This step is crucial to ensure you can access the coupling without any fuel pressure. Once disconnected, use a clean cloth or a soft-bristled brush to remove any visible dirt or corrosion from the coupling and the surrounding areas. Pay close attention to the threads and any small crevices where debris might have accumulated. It's important to keep the area as clean as possible to ensure the lubricant adheres properly.
Step 2: Choosing the Right Lubricant
Selecting the appropriate lubricant is essential for a successful repair. For fuel line couplings, a silicone-based grease or a fuel-resistant silicone sealant is often recommended. These types of lubricants are designed to withstand the harsh conditions of fuel systems, including high temperatures and the presence of fuel vapor. Ensure you choose a lubricant that is compatible with the materials used in your fuel line coupling.
Step 3: Applying the Lubricant
After cleaning the area, it's time to apply the lubricant. Start by threading the coupling onto the fuel line, ensuring it is aligned correctly. Then, apply a small amount of lubricant to the threads and the inside of the coupling. Use your fingers or a small tool to gently work the lubricant into the threads, ensuring an even coating. Take care not to over-lubricate, as this can lead to excess fuel accumulation and potential engine issues.
Step 4: Reassembly and Testing
Once the lubricant has been applied, carefully reassemble the coupling and secure it in place. Ensure that the coupling is tight and secure, but be careful not to overtighten it, as this can also cause damage. After reassembly, reconnect the fuel line and test the system for leaks. If no leaks are detected, your repair should be successful.
Remember, regular maintenance and cleaning of fuel line couplings can prevent many common issues, including leaks. By following these steps, you can effectively clean and lubricate the coupling, ensuring a reliable and leak-free fuel system.
XT225 Fuel Line: Finding the Perfect Size for Your Engine
You may want to see also
Tighten connections: Secure the coupling with appropriate fasteners to ensure a tight seal
When dealing with a leaky fuel line coupling, one of the most effective solutions is to tighten the connections. This process involves securing the coupling with the right fasteners to ensure a tight and leak-free seal. Here's a step-by-step guide to help you through this repair:
Start by identifying the type of coupling you are working with. Different couplings may require specific fasteners, so it's crucial to have the right tools for the job. Common fasteners used for fuel line couplings include nuts, bolts, and clamps. Ensure you have the appropriate size and type of fasteners to match the coupling's specifications.
Next, locate the coupling and inspect it for any visible damage or wear. Clean the coupling and the surrounding area to remove any dirt or debris that might interfere with the sealing process. This step is essential to ensure a proper bond between the fasteners and the coupling.
Now, apply the fasteners securely. Tighten the nuts or bolts by hand first to get a good initial grip. Then, using a wrench or a suitable tool, apply firm pressure to tighten the fasteners further. The goal is to achieve a snug fit without over-tightening, as this can damage the coupling or fuel line. Refer to the manufacturer's guidelines or a repair manual for specific torque specifications if available.
After tightening the fasteners, check the coupling for any leaks. Turn on the fuel system and observe if the leak has been eliminated. If there are still leaks, carefully inspect the connection and consider tightening the fasteners a bit more or adjusting the positioning of the coupling. Remember, the key is to find the right balance between a secure fit and avoiding excessive force that could cause damage.
In some cases, you might need to adjust the coupling's position or use additional sealing materials to ensure a perfect fit. This could involve slight modifications to the coupling or the fuel line itself. Always exercise caution and refer to expert advice when making such adjustments to avoid any potential hazards.
Mastering Fuel Line Bleeding: A Step-by-Step Guide for Petrol Cars
You may want to see also
Replace worn parts: If the coupling is damaged, consider replacing it with a new one
If you've identified that the issue with your fuel line coupling is due to wear and tear, it's important to take action to prevent further leaks and potential engine damage. Replacing worn parts is a crucial step in addressing this problem. Here's a comprehensive guide on how to replace the coupling:
Start by carefully inspecting the fuel line coupling. Look for any visible signs of damage, such as cracks, corrosion, or excessive wear. If the coupling appears damaged, it's best to replace it to ensure a secure and leak-free connection. Gather the necessary tools and replacement parts before proceeding. You'll typically need a new coupling, fuel line, and possibly some sealing compounds or tape. Ensure you have the correct specifications for your vehicle's fuel line to ensure a proper fit.
Locate the fuel line coupling, which is usually positioned between the fuel tank and the engine. Carefully disconnect the old coupling by loosening any securing clips or fasteners. Be cautious not to force anything to avoid damaging the surrounding components. Once disconnected, remove the old coupling and set it aside. Now, prepare the new coupling by cleaning the ends and ensuring they are free of any debris. Slide the new coupling onto the fuel line, ensuring it is aligned correctly. Use the appropriate sealing compound or tape to secure the coupling and create a tight seal.
Reattach the coupling to the fuel line and the engine, following the manufacturer's instructions for proper installation. Tighten the fasteners securely but be careful not to over-tighten, as it may damage the fuel line. Once installed, check for any leaks by starting the engine and monitoring for any signs of fuel escaping. If no leaks are detected, you've successfully replaced the worn-out coupling. Remember to dispose of the old parts responsibly and consider consulting a professional mechanic if you're unsure about any step during the replacement process.
Ford Fuel Line: Understanding the Connection to the Fuel Rail
You may want to see also
Test and verify: After repairs, test the fuel system to ensure no further leaks
After completing the necessary repairs to address a leaky fuel line coupling, it is crucial to thoroughly test and verify the system to ensure that the issue has been resolved and there are no further leaks. This step is essential to guarantee the safety and efficiency of your vehicle's fuel system. Here's a detailed guide on how to approach this testing process:
Step 1: Visual Inspection
Start by conducting a visual inspection of the fuel line coupling and its surrounding areas. Look for any visible signs of damage, cracks, or corrosion. Check for any debris or contaminants that might have accumulated during the repair process. Ensure that all components are securely connected and free from any visible defects.
Step 2: Pressure Testing
Perform a pressure test on the fuel system to identify any potential leaks. You can use a fuel pressure gauge for this purpose. Start by disconnecting the fuel pump and temporarily blocking the return line to create a closed system. Apply pressure to the system and monitor the gauge for any drops or fluctuations. A steady reading indicates a secure seal, while any deviations suggest a leak. Repeat this process at different operating temperatures to account for environmental factors.
Step 3: Leak Detection
Utilize a leak detection method to identify hidden leaks that might not be visible to the naked eye. One common technique is to use a soapy water solution. Spray the solution onto the fuel line coupling and observe for any bubbles. Bubbles indicate the presence of a leak, allowing you to pinpoint the exact location for further repair. Alternatively, you can use a fuel system dye, which is injected into the system and helps identify leaks through its color change.
Step 4: Engine Operation
Start the engine and listen for any unusual noises, especially hissing or roaring sounds, which could indicate a fuel leak. Pay attention to the fuel gauge and ensure it functions correctly, as any discrepancies may suggest a leak in the fuel tank or lines. Let the engine run for a period, checking for any changes in performance or unusual behavior.
Step 5: Final Verification
After completing the above steps, recheck the fuel line coupling for any signs of damage or wear. Ensure that all repairs have been effectively executed. If no further leaks are detected, you can consider the fuel system to be in good working order. However, if any issues persist, it is advisable to re-evaluate the repair process and address any remaining problems.
Remember, thorough testing is critical to ensuring the longevity and reliability of your vehicle's fuel system. By following these steps, you can effectively verify the success of your repairs and maintain a safe and efficient driving experience.
Fuel Lines vs. AC Lines: Unraveling the Differences
You may want to see also
Frequently asked questions
A fuel line coupling can leak due to several reasons, including age, corrosion, damage from vibrations, or improper installation. Over time, the materials used in the coupling may degrade, leading to cracks or weakened seals.
For a temporary fix, you can use a fuel line clamp or a temporary coupling. These can provide a quick solution to stop the leak, but it's important to note that this is a temporary measure. It's recommended to replace the coupling as soon as possible to ensure a proper and long-lasting repair.
Replacing a fuel line coupling requires a few essential tools. You'll need a fuel line cutter or a pair of sharp scissors to cut the old coupling, a fuel line cleaner to remove any debris, a new coupling with the appropriate size and thread, and a fuel line crimping tool to secure the new coupling.
It is generally not recommended to fix a leaky coupling without removing the fuel line. Accessing the coupling often requires disconnecting the fuel line to ensure a proper repair. Removing the fuel line temporarily will make the process safer and more efficient.
Here are some DIY tips:
- Ensure you have the correct replacement coupling with the right specifications for your vehicle.
- Clean the fuel line and the coupling ends to remove any dirt or corrosion.
- Use a fuel line primer on the new coupling to ensure a secure connection.
- Tighten the coupling securely but avoid over-tightening to prevent damage.
- After installation, check for any leaks and ensure all connections are tight.