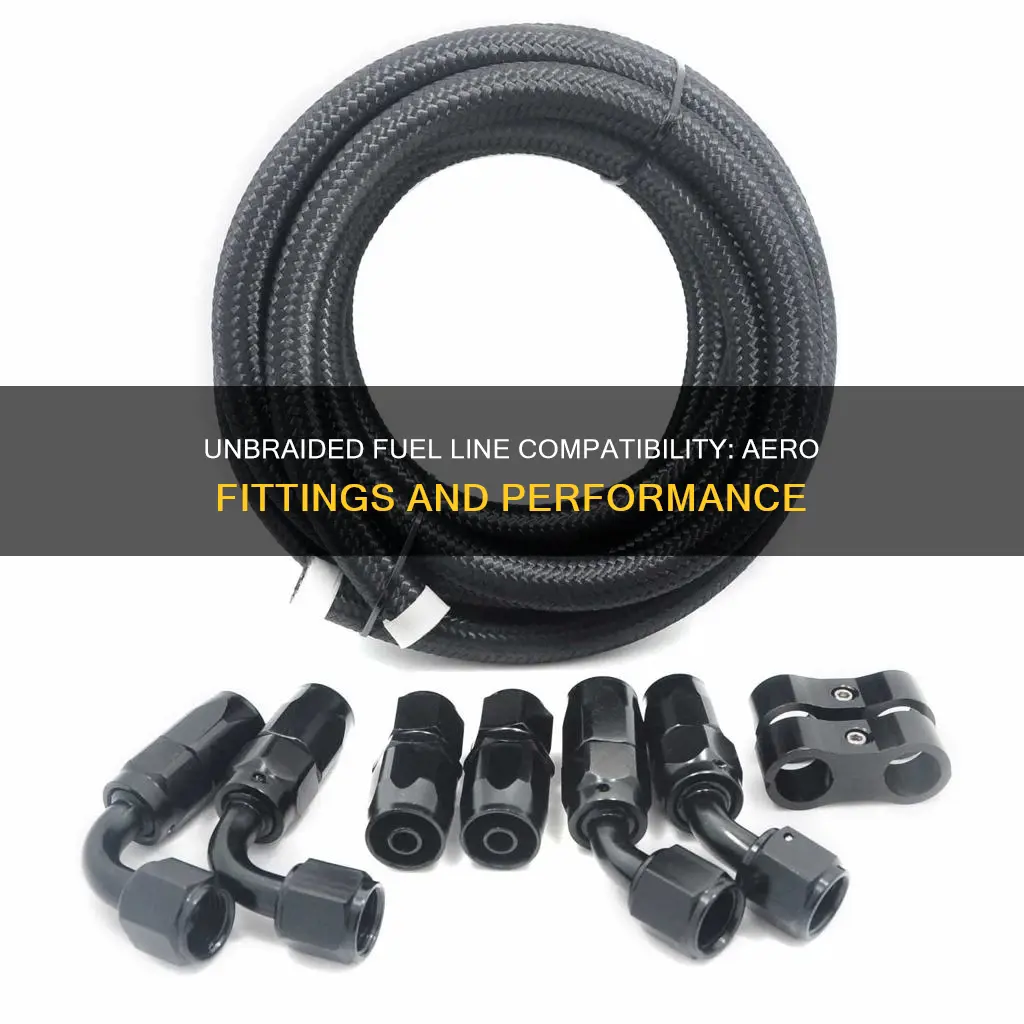
When it comes to modifying your vehicle's fuel system, one of the key considerations is the compatibility of different components. Specifically, many enthusiasts and DIYers wonder if unbraided fuel lines can be used with aero fittings. This question is particularly relevant for those looking to enhance their vehicle's performance and aesthetics. Unbraided fuel lines, known for their flexibility and durability, are often preferred for their ability to withstand high pressure and temperature changes. On the other hand, aero fittings, designed for their sleek and lightweight construction, offer improved airflow and reduced drag. By exploring the compatibility of these two components, we can provide valuable insights into how to optimize your fuel system for both performance and style.
Characteristics | Values |
---|---|
Compatibility | Unbraided fuel lines are generally compatible with aero fittings, but it's important to check specific models and sizes. |
Flexibility | Unbraided fuel lines offer excellent flexibility, allowing for easier installation and routing compared to braided lines. |
Durability | These lines are known for their durability and resistance to heat, making them suitable for high-performance applications. |
Material | Typically made from materials like silicone or rubber, ensuring flexibility and heat resistance. |
Installation | Easier to install due to their flexibility, but proper crimping or clamping techniques are still necessary. |
Cost | Often more affordable than braided lines, especially for longer lengths. |
Appearance | Unbraided lines have a more casual, unreinforced look, which might be preferred for certain vehicle aesthetics. |
Maintenance | Low maintenance required, as they are less prone to kinking or damage from sharp edges. |
Performance | Can handle high-pressure fuel systems and provide consistent performance. |
Availability | Widely available in various lengths and diameters. |
What You'll Learn
- Compatibility: Unbraided lines may not fit Aero fittings due to different diameters and materials
- Pressure Rating: Check if unbraided lines can handle Aero fitting pressure requirements
- Flexibility: Unbraided lines offer more flexibility, which can be beneficial for Aero installations
- Durability: Aero fittings require durable lines to withstand high temperatures and vibrations
- Installation: Proper installation techniques are crucial for both unbraided lines and Aero fittings
Compatibility: Unbraided lines may not fit Aero fittings due to different diameters and materials
When considering the compatibility of unbraided fuel lines with Aero fittings, it's important to understand the potential challenges that may arise. One of the primary concerns is the difference in diameters and materials between these two types of fuel lines. Unbraided lines, often made from materials like rubber or silicone, have a specific diameter that is designed to fit certain fittings. Aero fittings, on the other hand, may have unique dimensions and require a precise match to ensure a secure and leak-free connection.
The diameter of unbraided fuel lines is crucial as it directly impacts the flow rate of fuel. These lines are typically designed with a specific inner diameter to allow for optimal fuel delivery while maintaining flexibility. Aero fittings, however, might have different requirements, and using a line with a mismatch in diameter can lead to issues. For instance, a line that is too small may restrict fuel flow, causing performance problems, while a larger diameter line might not fit the fitting's internal dimensions, resulting in a loose connection.
Additionally, the materials used in unbraided fuel lines and Aero fittings play a significant role in compatibility. Different materials have varying levels of flexibility, temperature resistance, and chemical compatibility. Unbraided lines often rely on the flexibility of rubber or silicone to conform to different shapes and sizes. In contrast, Aero fittings may be constructed from materials that are more rigid or have specific properties required for their function. Using a line made from a material that doesn't match the fitting's requirements can lead to premature wear, leaks, or even damage to the fuel system.
To ensure a proper fit, it is recommended to consult the manufacturer's guidelines or seek expert advice when combining unbraided fuel lines with Aero fittings. Understanding the specific requirements of both components is essential to avoid potential issues. By carefully considering the diameters and materials, you can make an informed decision and ensure the compatibility and longevity of your fuel system.
Copper Fuel Lines: Safe for Your Boat's Engine?
You may want to see also
Pressure Rating: Check if unbraided lines can handle Aero fitting pressure requirements
When considering the use of unbraided fuel lines with Aero fittings, one of the critical factors to evaluate is the pressure rating of the unbraided lines. Aero fittings are designed to handle specific pressure requirements, and it's essential to ensure that the fuel lines used can withstand these pressures to maintain optimal performance and safety.
Unbraided fuel lines, as the name suggests, are constructed without a braided layer, typically made of rubber or synthetic materials. While they offer flexibility and ease of installation, their pressure-handling capabilities may vary. Aero fittings often require fuel lines with a higher pressure rating to ensure a secure and reliable connection. The pressure requirements for Aero fittings can range from 150 to 300 psi, depending on the specific application and engine configuration.
To determine if unbraided lines can handle the pressure requirements of Aero fittings, it is crucial to check the manufacturer's specifications. Most fuel line manufacturers provide detailed information about their products, including pressure ratings. Look for data sheets or product descriptions that specify the minimum and maximum pressure the unbraided line can withstand. This information will help you make an informed decision and ensure compatibility with the Aero fittings.
Additionally, consider the potential risks of using unbraided lines with lower pressure ratings. Insufficient pressure rating can lead to fuel leaks, reduced performance, and even potential damage to the engine over time. It is essential to prioritize safety and choose fuel lines that can handle the expected pressure levels to ensure the longevity and reliability of your vehicle's fuel system.
In summary, when using unbraided fuel lines with Aero fittings, carefully assess the pressure rating to ensure compatibility. Checking manufacturer specifications and understanding the pressure requirements of Aero fittings will help you make the right choice, ensuring a secure and efficient fuel delivery system. Always prioritize safety and consult experts if needed to guarantee the best performance.
Optimizing Performance: Choosing the Right Fuel Line for Your SBC 350
You may want to see also
Flexibility: Unbraided lines offer more flexibility, which can be beneficial for Aero installations
When considering the use of unbraided fuel lines with aero fittings, one of the key advantages is the flexibility that unbraided lines provide. This characteristic becomes especially important in aero installations, where the fuel lines need to navigate through tight spaces and follow the contours of the vehicle's body.
Unbraided fuel lines are constructed without any reinforcing braids or layers, allowing them to conform to the shape of the installation area more easily. This flexibility is crucial in aero applications, where the fuel lines might need to bend around sharp corners, follow the curve of the hood, or accommodate the movement of various vehicle components during acceleration and deceleration. The lack of braids means that the line can move more freely, reducing the risk of damage and ensuring a more secure installation.
In aero installations, the goal is often to create a sleek and low-profile appearance, which can be challenging when using rigid braided lines. Braided lines, while strong and durable, have limited flexibility and can make it difficult to achieve the desired aesthetic. Unbraided lines, on the other hand, can be manipulated to fit the unique contours of the aero setup, allowing for a more seamless and integrated look.
Furthermore, the flexibility of unbraided lines can contribute to a more secure and reliable fuel system. By allowing the lines to move and adjust, you reduce the chances of damage from sharp bends or excessive tension. This is particularly important in high-performance vehicles where the fuel system needs to handle rapid changes in load and stress. The flexibility of unbraided lines can help absorb these changes, ensuring a consistent and reliable fuel supply to the engine.
In summary, the flexibility of unbraided fuel lines is a significant advantage when used with aero fittings. It allows for a more customized and secure installation, accommodating the unique challenges of aero-style fuel systems. This flexibility ensures that the fuel lines can follow the vehicle's contours, maintain a sleek appearance, and provide a reliable fuel supply, all while withstanding the rigors of everyday driving.
Upgrading Your CB350's Fuel Line: 5mm or Not?
You may want to see also
Durability: Aero fittings require durable lines to withstand high temperatures and vibrations
When considering the use of unbraided fuel lines with aero fittings, it's crucial to prioritize durability, especially in high-performance automotive applications. Aero fittings, known for their sleek and lightweight design, often require fuel lines that can withstand the rigors of racing and high-performance driving. The durability of these fuel lines is essential to ensure reliable fuel delivery and prevent potential leaks or failures under extreme conditions.
One of the primary factors affecting durability is the ability of the fuel line to resist high temperatures. Aero fittings, often made from lightweight materials, may generate more heat during operation compared to standard fittings. Unbraided fuel lines, typically constructed from materials like stainless steel braids or high-temperature-resistant polymers, offer superior heat resistance. These materials can withstand the elevated temperatures associated with high-performance engines, ensuring that the fuel lines remain flexible and intact even when exposed to intense heat.
Vibrations and mechanical stress are another consideration for durability. Racing environments and high-performance driving involve rapid acceleration, sharp turns, and varying road conditions, all of which can exert significant stress on fuel lines. Unbraided fuel lines, with their flexible and robust construction, are designed to accommodate these vibrations and movements without compromising integrity. The lack of a braided layer allows for more natural flexibility, reducing the risk of damage or cracking over time.
To ensure optimal durability, it is recommended to choose unbraided fuel lines specifically engineered for high-temperature and vibration-resistant applications. These lines should be constructed with materials that can handle the unique challenges of aero fittings, such as lightweight yet sturdy polymers or carefully selected braids of stainless steel. Proper installation and regular inspections are also vital to maintaining the integrity of the fuel lines and ensuring they can withstand the demands of high-performance driving.
In summary, when using aero fittings, selecting unbraided fuel lines with excellent durability is essential. These lines should be capable of withstanding high temperatures and vibrations, ensuring reliable fuel delivery and contributing to the overall performance and safety of the vehicle. By considering the specific requirements of aero fittings, enthusiasts and professionals can make informed choices to optimize their high-performance automotive setups.
Clean Fuel: Tips for Removing Excess Carbon from Your Lines
You may want to see also
Installation: Proper installation techniques are crucial for both unbraided lines and Aero fittings
When it comes to connecting unbraided fuel lines with Aero fittings, proper installation is essential to ensure optimal performance and safety. These components are designed to work together seamlessly, and any mistakes during the installation process can lead to issues down the line. Here's a step-by-step guide to help you get it right:
Preparation: Before you begin, ensure you have the necessary tools and materials, including the unbraided fuel line, Aero fittings, fuel line connectors, and any required tools for cutting and bending the line. Check the fuel line for any defects or damage, especially if it's a replacement. Unbraided lines are known for their flexibility, but they can still be susceptible to punctures or tears if not handled carefully.
Cutting and Preparation: Measure and cut the unbraided fuel line to the desired length, ensuring you have enough excess to work with. Smooth any sharp edges with a file or sandpaper to prevent damage to the fittings. Clean the interior and exterior of the Aero fittings to remove any debris or contaminants that could interfere with the connection.
Assembly: Start by inserting the fuel line into the Aero fitting, ensuring it is aligned correctly. Use the provided fuel line connectors to secure the line to the fitting. Tighten the connectors securely, but be careful not to overtighten, as this can damage the line or fitting. The key here is to create a tight, leak-free seal without applying excessive force.
Bending and Routing: After the initial connection, you'll need to bend and route the unbraided line to its desired position. Aero fittings often require specific angles and orientations to fit the vehicle's design. Use a pair of pliers or a fuel line bender to make precise bends, ensuring the line is not kinked or damaged. Route the line away from high-heat areas and sharp edges to prevent melting or puncturing.
Testing and Final Adjustments: Once the installation is complete, start the vehicle's engine and check for any leaks at the connections. If no leaks are found, you've successfully installed the unbraided fuel line with Aero fittings. However, if any issues arise, carefully inspect the connections and make adjustments as necessary. Remember, proper installation is critical to maintaining the integrity of your fuel system and overall vehicle performance.
Automotive Fuel Line: A Viable Option for Outboard Motor?
You may want to see also
Frequently asked questions
Yes, you can use unbraided fuel line with Aero fittings, but it's important to consider a few factors. Aero fittings are designed for high-pressure applications and require a specific type of fuel line to ensure a secure and reliable connection. Unbraided fuel lines are typically made of synthetic materials like silicone or rubber and are flexible, which can be beneficial for accommodating vibrations and movement in the engine bay. However, they might not provide the same level of rigidity and pressure resistance as braided fuel lines. It's recommended to use a fuel line that matches the pressure rating and material requirements of the Aero fittings to ensure optimal performance and safety.
Unbraided fuel lines offer several advantages when used with Aero fittings. Firstly, their flexibility allows for easier installation and routing around the engine bay, making the process more manageable. This flexibility can also help reduce stress on the fuel line, preventing potential damage from engine movement. Additionally, unbraided lines are often more resistant to temperature changes, which is crucial for maintaining fuel stability and performance in varying environmental conditions.
When installing unbraided fuel lines with Aero fittings, it's essential to ensure a tight and secure connection. Start by cleaning the fittings and fuel line to remove any contaminants. Then, apply a suitable fuel line adhesive or tape to the fuel line and fitting threads to create a reliable bond. Make sure the fuel line is properly lubricated and routed correctly, allowing for some slack to account for engine movement. Regularly inspect the connections for any signs of leakage or damage, and consider using a fuel line protector to safeguard against potential impacts or vibrations.