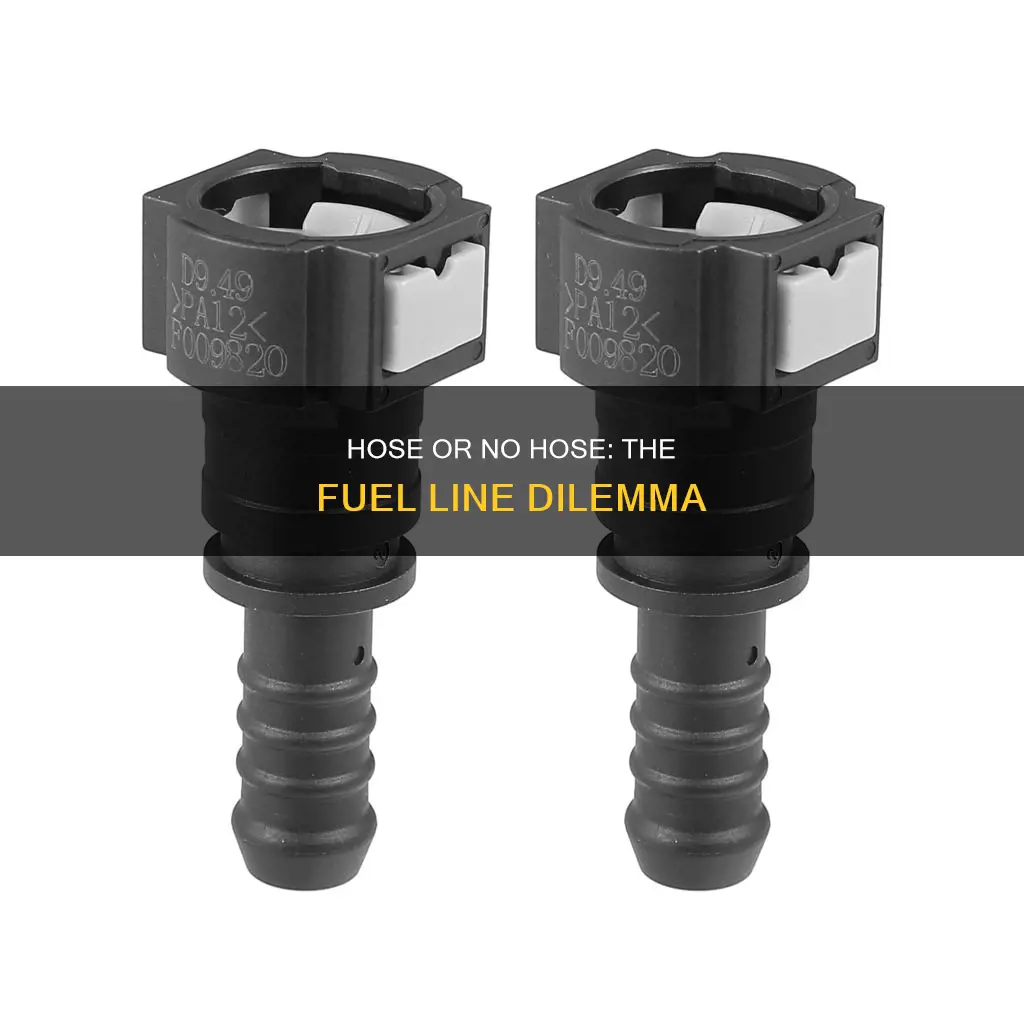
Can you use a hose on your fuel line? It's a common question for vehicle owners and mechanics alike. While it might seem like a straightforward answer, the safety and functionality of your vehicle depend on the right choice. Using a hose on a fuel line can be risky, as it may not be designed to withstand the pressure and temperature changes that fuel lines experience. Additionally, hoses can degrade over time, leading to potential leaks and engine performance issues. This introduction sets the stage for a discussion on the proper methods and considerations when dealing with fuel lines.
What You'll Learn
- Hose Compatibility: Check if the hose is compatible with the fuel type and pressure
- Hose Material: Ensure the hose material is suitable for fuel and temperature
- Hose Length: Measure and adjust hose length for optimal fuel delivery
- Hose Connections: Securely attach hoses to fuel lines with proper fittings
- Hose Inspection: Regularly inspect hoses for cracks, leaks, and wear
Hose Compatibility: Check if the hose is compatible with the fuel type and pressure
When considering using a hose on your fuel line, it's crucial to prioritize safety and ensure compatibility. One of the primary factors to check is the hose's compatibility with the fuel type. Different fuels have varying properties and requirements, and using an incompatible hose can lead to potential issues. For instance, gasoline hoses are designed to withstand the volatility and pressure of gasoline, while diesel hoses are built to handle the higher pressure and lubricating properties of diesel fuel. Using the wrong type of hose can result in fuel leaks, engine damage, or even a fire hazard. Always refer to the vehicle's manual or consult with a professional to determine the appropriate hose type for your specific fuel.
The pressure rating of the hose is another critical aspect to consider. Fuel lines operate under specific pressure conditions, and using a hose with an inadequate pressure rating can compromise safety. Hoses are typically rated for different pressure ranges, such as low, medium, or high pressure. It's essential to select a hose that meets or exceeds the fuel line's pressure requirements. Insufficient pressure rating may lead to hose failure, causing fuel leaks or reduced engine performance. Check the hose's pressure rating and ensure it aligns with the expected fuel line pressure to ensure a secure and reliable connection.
Additionally, the material of the hose is a significant factor in compatibility. Hoses are made from various materials, such as rubber, vinyl, or synthetic compounds, each with its own set of advantages and limitations. For fuel lines, hoses made from compatible materials like fuel-resistant rubber or synthetic compounds are ideal. These materials ensure the hose can withstand the corrosive nature of fuel and maintain its integrity over time. Incompatible materials may degrade or become brittle, leading to potential failures. Always choose hoses specifically designed for fuel applications to guarantee compatibility and longevity.
To ensure proper hose compatibility, it's recommended to consult the vehicle's manufacturer or refer to the fuel system's technical specifications. These sources will provide detailed information on the required hose types, pressure ratings, and materials. By following these guidelines, you can ensure that the hose used on your fuel line is compatible, safe, and reliable, minimizing the risk of fuel-related issues and maintaining optimal engine performance. Remember, when it comes to fuel lines, compatibility is key to a secure and efficient system.
Mastering the Art of Tractor Fuel Line Shutdown: A Step-by-Step Guide
You may want to see also
Hose Material: Ensure the hose material is suitable for fuel and temperature
When considering using a hose on your fuel line, it is crucial to prioritize the material of the hose to ensure safety and efficiency. The primary concern is the compatibility of the hose material with the fuel type and the operating temperature range. Different fuels, such as gasoline, diesel, or aviation fuel, have varying chemical compositions and properties that can affect the hose's performance and longevity.
For instance, gasoline is a volatile fuel that can dissolve certain hose materials over time, leading to potential leaks and engine issues. Common materials like rubber or natural latex hoses may not be suitable for gasoline applications due to their tendency to break down. Instead, hoses made from more resistant materials such as synthetic rubber compounds, such as neoprene or butyl rubber, are preferred. These materials offer better resistance to fuel dissolution and can withstand the corrosive effects of gasoline.
On the other hand, diesel fuel, being less volatile, may not cause the same level of material degradation. However, it still requires careful consideration. Hoses used for diesel fuel should be made from materials that can handle the higher temperatures associated with diesel engines. Common choices include hoses with a higher temperature rating, such as those made from silicone or fluoropolymer compounds. These materials provide excellent resistance to heat and chemical corrosion, ensuring the hose's integrity under demanding conditions.
Temperature considerations are especially important when dealing with aviation fuels, which often have specific temperature requirements. Hoses used in aviation applications must be designed to withstand extreme temperature fluctuations, from cold weather conditions that can cause fuel thickening to hot environments that may lead to fuel evaporation. Materials like fluoropolymer hoses or those with a reinforced construction are often employed to meet these demanding standards.
In summary, selecting the appropriate hose material is critical when using hoses on fuel lines. It involves understanding the properties of the fuel and the temperature range it will encounter. By choosing materials that are resistant to fuel dissolution, chemical corrosion, and temperature extremes, you can ensure the safety and reliability of your fuel system. Always refer to manufacturer guidelines and consult experts when in doubt to make the right choice for your specific application.
Fuel Line Fabrication: Cost Breakdown for Custom Solutions
You may want to see also
Hose Length: Measure and adjust hose length for optimal fuel delivery
When considering the use of hoses for fuel lines, one crucial aspect is the length of the hose. Proper hose length is essential to ensure efficient and safe fuel delivery. Here's a detailed guide on how to measure and adjust hose length for optimal performance:
Measuring Hose Length: Begin by carefully inspecting the fuel line and identifying the points where the hose connects to the fuel tank and the engine. Measure the distance between these connection points. It's important to consider the natural curvature and bends of the fuel line, as these can affect the hose's length. Use a flexible measuring tape or a ruler to get an accurate measurement. Take note of any existing hoses or fuel lines to ensure the new hose can fit without interference.
Optimizing Hose Length: The goal is to achieve a hose length that provides a smooth and direct path from the fuel tank to the engine. A well-fitted hose should allow for easy movement and flexibility without being overly long or short. If the measured length is too long, consider adjusting the hose by carefully trimming it to the desired length. Ensure that you cut the hose at a slight angle to create a clean and precise connection. For shorter lengths, you might need to add extensions or adaptors to maintain the required distance.
Consideration of Flexibility: Flexibility is key when working with hoses. The hose should be able to move with the engine and fuel tank without restricting fuel flow. If the hose is too rigid, it may cause issues during engine operation. Look for hoses with a suitable durometer (hardness) that offers flexibility without compromising strength. This balance ensures the hose can adjust to different engine positions without kinking or bending excessively.
Testing and Adjustments: After adjusting the hose length, it's crucial to test the setup. Start the engine and monitor for any unusual noises or vibrations. Check for leaks at the hose connections to ensure a secure fit. If issues arise, make small adjustments and retest until optimal performance is achieved. This iterative process ensures that the hose length is just right, providing efficient fuel delivery without compromising safety.
Remember, proper hose length is a critical factor in maintaining a reliable fuel system. By carefully measuring, adjusting, and testing, you can ensure that the hose is tailored to your specific fuel line setup, offering optimal performance and longevity.
Hose Clamps for 5/16 Fuel Lines: Size Matters
You may want to see also
Hose Connections: Securely attach hoses to fuel lines with proper fittings
When it comes to working with fuel lines, it's crucial to understand the proper use of hoses and fittings to ensure a safe and efficient system. While it is generally not recommended to use standard hoses directly on fuel lines, there are specific hose connections and fittings designed for this purpose. These connections are engineered to withstand the unique challenges of fuel systems, including high-pressure fuel, temperature variations, and the need for flexibility.
The key to a secure and reliable hose connection is the use of appropriate fittings. These fittings are typically made of durable materials such as brass, stainless steel, or engineered plastics, ensuring they can handle the corrosive nature of fuel. The most common type of fitting used for fuel lines is the quick-connect fitting, which allows for a rapid and secure attachment of the hose. These fittings often feature a male and female end, with a locking mechanism to ensure a tight seal. It is essential to choose fittings that match the diameter and thread size of your fuel line to ensure a proper fit.
To begin the connection process, locate the fuel line where you intend to attach the hose. Clean the area to remove any dirt or debris, ensuring a smooth surface for the fitting. Slide the hose onto the fitting, ensuring it is aligned correctly. The hose should be slightly longer than the fitting to allow for some flexibility during installation. Once aligned, push the fitting onto the fuel line until it is fully seated. Use a wrench or spanner to tighten the fitting securely, but be careful not to overtighten, as this can damage the fuel line.
After the initial connection, it is crucial to test the system for any leaks. Turn on the fuel supply and check for any signs of fuel escaping at the connection point. If a leak is detected, tighten the fitting further or consider using a sealing compound to ensure a tight seal. Always ensure that the hose and fittings are compatible with the type of fuel being used to prevent any potential issues.
In summary, while standard hoses are not typically used on fuel lines, specific hose connections and fittings are designed for this purpose. These connections provide a secure and reliable way to attach hoses to fuel lines, ensuring the system can withstand the demands of fuel delivery. By using the right fittings and following proper installation procedures, you can create a safe and efficient fuel system. Remember to always refer to manufacturer guidelines and consult experts when working with fuel lines to ensure compliance with safety standards.
Understanding Fuel Pump Lines: Why Three is Optimal
You may want to see also
Hose Inspection: Regularly inspect hoses for cracks, leaks, and wear
Regular hose inspections are a critical aspect of vehicle maintenance, especially for those who use hoses in fuel lines. Over time, hoses can deteriorate due to various factors, including age, exposure to heat and cold, and the presence of contaminants. Neglecting to inspect hoses can lead to serious issues, such as fuel leaks, engine damage, and even safety hazards. Therefore, it is essential to establish a routine inspection process to ensure the longevity and reliability of your vehicle's fuel system.
During the inspection, pay close attention to the hoses' condition. Look for any visible signs of damage, such as cracks, splits, or bulges. Cracks can be a result of age or excessive heat/cold exposure, while splits may indicate a more severe issue. Bulges could be a sign of internal damage or a weakened hose structure. Inspect the hoses for any leaks, especially around the connections and fittings. Even a small leak can lead to significant fuel loss over time, impacting engine performance and fuel efficiency.
Wear and tear are common issues with hoses, especially those exposed to the elements. Inspect the hoses for any signs of deterioration, such as hardening, softening, or brittleness. Worn-out hoses may not function properly and could fail under pressure, leading to potential engine damage. It is also important to check the hose's flexibility. Hoses should be able to bend and move without excessive strain, so look for any areas where the hose becomes stiff or rigid.
When inspecting the fuel line hoses, ensure that you cover all relevant areas. Check the hoses that run from the fuel tank to the engine, as well as any additional hoses connected to fuel injectors or other fuel-related components. Pay attention to the connections and fittings, as these are common points of failure. Over time, corrosion or improper installation can lead to leaks or disconnections.
In addition to visual inspections, it is beneficial to develop a routine maintenance schedule. Create a checklist to ensure you don't miss any critical areas. Consider using a flashlight to inspect hard-to-reach places and a magnifying glass to examine small cracks or wear. Regular hose inspections are a simple yet effective way to maintain your vehicle's performance and safety, ensuring that your fuel system operates efficiently and reliably.
Finding the Perfect Fit: Where to Buy Molded Fuel Line for Kx65
You may want to see also
Frequently asked questions
No, it is not safe to use a garden hose on a fuel line. Garden hoses are not designed for fuel and can cause significant damage to the fuel system. The pressure and chemicals in the hose can lead to fuel leaks, contamination, and potential fire hazards.
Using a hose on a fuel line can result in several issues. Firstly, the hose may not be compatible with the fuel type, leading to potential corrosion or fuel degradation. Secondly, hoses can develop cracks or leaks over time, causing fuel to spill and potentially ignite. This can be extremely dangerous and may require professional repair or replacement.
It is not recommended to use a hose for temporary fuel filling. While it might seem convenient, it is a risky practice. The hose may not have the necessary precision and control to ensure an accurate and safe transfer of fuel. Additionally, using a hose can lead to overfilling, which can damage the fuel pump and other fuel system components.
Yes, there are safer alternatives for fuel transfer. Dedicated fuel transfer pumps and containers designed for fuel are recommended. These tools provide a controlled and precise way to move fuel without the risks associated with hoses. It is always best to follow manufacturer guidelines and consult professionals for any fuel-related tasks to ensure safety and prevent potential damage.